Information injection-pump assembly
BOSCH
9 400 613 411
9400613411
ZEXEL
101400-9071
1014009071
YANMAR
12991651060
12991651060
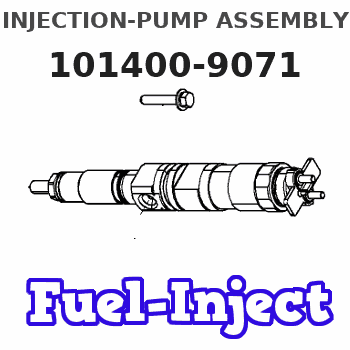
Rating:
Service parts 101400-9071 INJECTION-PUMP ASSEMBLY:
1.
_
4.
SUPPLY PUMP
5.
AUTOM. ADVANCE MECHANIS
6.
COUPLING PLATE
7.
COUPLING PLATE
8.
_
9.
_
10.
NOZZLE AND HOLDER ASSY
11.
Nozzle and Holder
12.
Open Pre:MPa(Kqf/cm2)
13.
NOZZLE-HOLDER
14.
NOZZLE
15.
NOZZLE SET
Cross reference number
BOSCH
9 400 613 411
9400613411
ZEXEL
101400-9071
1014009071
YANMAR
12991651060
12991651060
Zexel num
Bosch num
Firm num
Name
Calibration Data:
Adjustment conditions
Test oil
1404 Test oil ISO4113 or {SAEJ967d}
1404 Test oil ISO4113 or {SAEJ967d}
Test oil temperature
degC
40
40
45
Nozzle and nozzle holder
105780-8140
Bosch type code
EF8511/9A
Nozzle
105780-0000
Bosch type code
DN12SD12T
Nozzle holder
105780-2080
Bosch type code
EF8511/9
Opening pressure
MPa
17.2
Opening pressure
kgf/cm2
175
Injection pipe
Outer diameter - inner diameter - length (mm) mm 6-2-600
Outer diameter - inner diameter - length (mm) mm 6-2-600
Overflow valve
131424-1520
Overflow valve opening pressure
kPa
157
123
191
Overflow valve opening pressure
kgf/cm2
1.6
1.25
1.95
Tester oil delivery pressure
kPa
157
157
157
Tester oil delivery pressure
kgf/cm2
1.6
1.6
1.6
Direction of rotation (viewed from drive side)
Right R
Right R
Injection timing adjustment
Direction of rotation (viewed from drive side)
Right R
Right R
Injection order
1-3-4-2
Pre-stroke
mm
3.6
3.55
3.65
Beginning of injection position
Drive side NO.1
Drive side NO.1
Difference between angles 1
Cal 1-3 deg. 90 89.5 90.5
Cal 1-3 deg. 90 89.5 90.5
Difference between angles 2
Cal 1-4 deg. 180 179.5 180.5
Cal 1-4 deg. 180 179.5 180.5
Difference between angles 3
Cyl.1-2 deg. 270 269.5 270.5
Cyl.1-2 deg. 270 269.5 270.5
Injection quantity adjustment
Adjusting point
A
Rack position
8.9
Pump speed
r/min
1250
1250
1250
Average injection quantity
mm3/st.
48.3
47.3
49.3
Max. variation between cylinders
%
0
-2.5
2.5
Basic
*
Fixing the lever
*
Injection quantity adjustment_02
Adjusting point
C
Rack position
7+-0.5
Pump speed
r/min
400
400
400
Average injection quantity
mm3/st.
13
12
14
Max. variation between cylinders
%
0
-15
15
Fixing the rack
*
Injection quantity adjustment_03
Adjusting point
D
Rack position
9.4++
Pump speed
r/min
100
100
100
Average injection quantity
mm3/st.
65
60
70
Fixing the lever
*
Rack limit
*
Test data Ex:
Governor adjustment
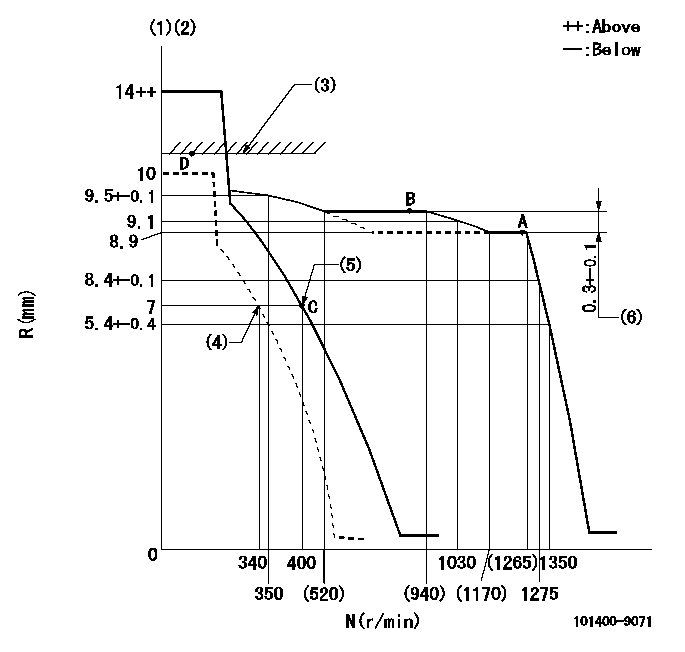
N:Pump speed
R:Rack position (mm)
(1)Target notch: K
(2)Tolerance for racks not indicated: +-0.05mm.
(3)RACK LIMIT
(4)Set idle sub-spring
(5)Main spring setting
(6)Rack difference between N = N1 and N = N2
----------
K=8 N1=1250r/min N2=800r/min
----------
----------
K=8 N1=1250r/min N2=800r/min
----------
Speed control lever angle

F:Full speed
I:Idle
(1)Stopper bolt setting
----------
----------
a=7deg+-5deg b=26deg+-5deg
----------
----------
a=7deg+-5deg b=26deg+-5deg
Stop lever angle
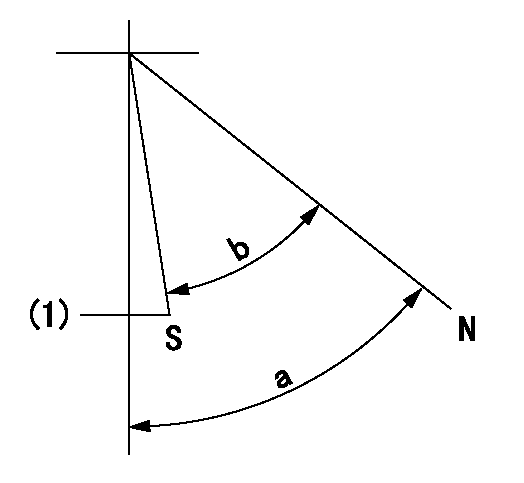
N:Pump normal
S:Stop the pump.
(1)Normal stop
----------
----------
a=58deg+-5deg b=53deg+-5deg
----------
----------
a=58deg+-5deg b=53deg+-5deg
Timing setting
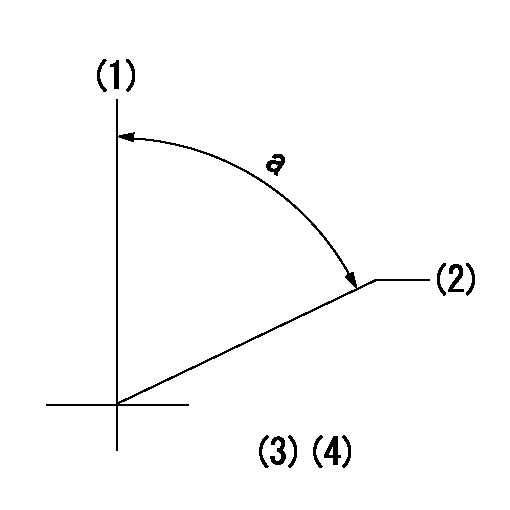
(1)Pump vertical direction
(2)Position of camshaft's key groove at No 1 cylinder's beginning of injection
(3)-
(4)-
----------
----------
a=(60deg)
----------
----------
a=(60deg)
Information:
(b) 4.248 Engines (4 Ring)
**Spring Loaded Conformable Scraper - above gudgeon pin.Internally Stepped Compression - third groove.*Internally Stepped Compression - second groove.Chrome Insert Barrel Faced Compression - top groove.When fitting sealed power rings, ensure that the ends of the spring loaded segment butt together and do not overlap.**Some earlier A4.248 engines had a sealed power scraper ring fitted in the 4th groove. *On some earlier A4.248 engines rated up to 2,000 rev/min, the second compression ring is plain cast iron.Some later engines, rated up to 2,000 rev/min, have internally stepped chrome faced rings in both 2nd and 3rd grooves.When fitting internally stepped compression rings, ensure that the step is towards the piston crown.When fitting the spring loaded conformable scraper ring, ensure that the latch pin enters both ends of the spring. With the ring gap diametrically opposite to the latch pin, position the oil control ring over spring correctly located in annular groove of ring, i.e., between the oil control ring and the bottom of the ring groove in the piston.(c) 4.248 Engines (3 Ring)
Chrome Faced Spring Loaded ConformableScraper - above gudgeon pin.Internally Stepped Taper Faced Compression - second groove.Molybdenum Faced Internally Stepped Barrel Faced Compression - top groove.When fitting the spring loaded conformable scraper ring, ensure that the latch pin enters both ends of the spring. With the ring gap diametrically opposite to the latch pin, position the oil control ring over the spring correctly located in the annular groove of ring, i.e., between the oil control ring and the bottom of the ring groove in the piston.When fitting the internally stepped compression rings in the second and top grooves, ensure that the "step" is towards the piston crown.(d) T4.236 Engines (see Fig. F.6)
F6Chrome Faced Spring Loaded Conformable Scraper - above gudgeon pin.Cast Iron Taper Faced Compression - second groove.Molybdenum Faced Wedge Compression - top groove.When fitting the spring loaded conformable scraper ring, ensure that the latch pin enters both ends of the spring. With the ring gap diametrically opposite to the latch pin, position the oil control ring over spring correctly located in annular groove, i.e., between the oil control ring and the bottom of the ring groove in the piston.When fitting the compression rings, ensure that the manufacturers mark is towards the piston crown.(e) 4.236 Engines fitted with cast iron liners
Slotted Scraper - below gudgeon pin.Slotted Scraper - above gudgeon pin.Internally Stepped Compression - third groove.Internally Stepped Compression - second groove.*Chrome Faced Compression - top groove*With later combine engines, a plain cast iron ring is fitted in the top groove. This plain ring is completely interchangeable with the earlier chrome faced ring. When overhauling combine engines, the later plain ring should always be fitted (in engine sets). From Engine No. 236U68569 fitted to combine applications, some piston ring packs have been altered from five to four rings. The two slotted scraper rings fitted in the forth and fifth grooves have been replaced by one conformable chrome faced ring in the fourth groove only, leaving the
**Spring Loaded Conformable Scraper - above gudgeon pin.Internally Stepped Compression - third groove.*Internally Stepped Compression - second groove.Chrome Insert Barrel Faced Compression - top groove.When fitting sealed power rings, ensure that the ends of the spring loaded segment butt together and do not overlap.**Some earlier A4.248 engines had a sealed power scraper ring fitted in the 4th groove. *On some earlier A4.248 engines rated up to 2,000 rev/min, the second compression ring is plain cast iron.Some later engines, rated up to 2,000 rev/min, have internally stepped chrome faced rings in both 2nd and 3rd grooves.When fitting internally stepped compression rings, ensure that the step is towards the piston crown.When fitting the spring loaded conformable scraper ring, ensure that the latch pin enters both ends of the spring. With the ring gap diametrically opposite to the latch pin, position the oil control ring over spring correctly located in annular groove of ring, i.e., between the oil control ring and the bottom of the ring groove in the piston.(c) 4.248 Engines (3 Ring)
Chrome Faced Spring Loaded ConformableScraper - above gudgeon pin.Internally Stepped Taper Faced Compression - second groove.Molybdenum Faced Internally Stepped Barrel Faced Compression - top groove.When fitting the spring loaded conformable scraper ring, ensure that the latch pin enters both ends of the spring. With the ring gap diametrically opposite to the latch pin, position the oil control ring over the spring correctly located in the annular groove of ring, i.e., between the oil control ring and the bottom of the ring groove in the piston.When fitting the internally stepped compression rings in the second and top grooves, ensure that the "step" is towards the piston crown.(d) T4.236 Engines (see Fig. F.6)
F6Chrome Faced Spring Loaded Conformable Scraper - above gudgeon pin.Cast Iron Taper Faced Compression - second groove.Molybdenum Faced Wedge Compression - top groove.When fitting the spring loaded conformable scraper ring, ensure that the latch pin enters both ends of the spring. With the ring gap diametrically opposite to the latch pin, position the oil control ring over spring correctly located in annular groove, i.e., between the oil control ring and the bottom of the ring groove in the piston.When fitting the compression rings, ensure that the manufacturers mark is towards the piston crown.(e) 4.236 Engines fitted with cast iron liners
Slotted Scraper - below gudgeon pin.Slotted Scraper - above gudgeon pin.Internally Stepped Compression - third groove.Internally Stepped Compression - second groove.*Chrome Faced Compression - top groove*With later combine engines, a plain cast iron ring is fitted in the top groove. This plain ring is completely interchangeable with the earlier chrome faced ring. When overhauling combine engines, the later plain ring should always be fitted (in engine sets). From Engine No. 236U68569 fitted to combine applications, some piston ring packs have been altered from five to four rings. The two slotted scraper rings fitted in the forth and fifth grooves have been replaced by one conformable chrome faced ring in the fourth groove only, leaving the