Information hydraulic head
BOSCH
9 461 629 124
9461629124
ZEXEL
149200-0722
1492000722
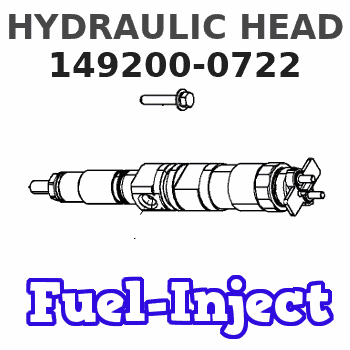
Rating:
Include in ###:
Cross reference number
Zexel num
Bosch num
Firm num
Name
Information:
Removing delivery valve and spring(2) Inspection(a) Open the cock on the fuel filter. If the system has an electromagnetic pump, turn the key to the ON position. Fuel will flow out of the injection pipe. Make ready a container to catch it. If the system has an electromagnetic pump, caution is required since fuel will emerge with great force.(b) Slowly turn the crankshaft clockwise. The injection timing is reached when fuel stops flowing out. When fuel has stopped flowing out, turn the crankshaft slightly in the reverse direction such that fuel flows out. Then, slowly turn the crankshaft clockwise again to more accurately verify the point at which stops flowing out.
Fuel flow
End of fuel flow(c) If the IT mark on the crankshaft pulley and the mark on the gear case are aligned when fuel stops flowing out, the injection timing is normal.
Timing marks(3) Adjustment(a) If the injection timing is out of specification, make adjustments by increasing or decreasing the thickness of the injection pump's mounting shim. A change of 0.1 mm in the shim thickness yields a change of approximately 1° in the injection timing.(b) Increasing the shim thickness retards the injection timing, and decreasing the shim thickness advances it. Shims are available in thicknesses of 0.2 mm (0.008 in.), 0.3 mm (0.012 in.), 0.4 mm (0.016 in.), and 0.8 mm (0.031 in.). The thicknesses are not indicated on the shims, so any shim should be measured with a vernier caliper before being used.
Before using any shim, apply sealant to both sides to prevent oil leakage.
(c) After making adjustments, check that the injection timing is correct.(d) Close the cock on the fuel filter, then fit the delivery valve spring and injection pipe in their original positions.
Injection timing adjustment shim
Adjusting injection timing1.4 Adjusting Idle Speed(1) Preparation for Adjustment(a) Warm up the engine until the coolant reaches a temperature of 60°C (140°F) or higher.(b) Make sure the valve clearances, injection timing, and injectors are normal.(2) Adjusting Low-Idle SpeedLoosen the lock nut on the idling set bolt, turn the bolt to achieve the specified low-idle speed (1,000 25 min-1), then tighten the lock nut to hold the bolt in that position.(3) Adjusting No-Load Maximum SpeedLoosen the lock nut on the high-speed set bolt, turn the bolt to achieve the specified no-load maximum speed (2870+30-10 min-1), then tighten the lock nut to hold the bolt in that position.
Adjusting idle speed1.5 Adjusting Fan Belt Tension(1) Press the fan belt with the specified force mid-way between the alternator pulley and crankshaft pulley, and observe the extent of deflection. (2) If the extent of deflection is out of specification, loosen the adjusting bolt and adjust the fan belt tension by moving the alternator. Retighten the adjusting bolt securely.
Adjusting fan belt tension2. Running in the Engine
After an overhaul, the engine should be tested and inspected on a dynamometer. This operation serves to run in the engine's major moving parts.2.1 Starting the Engine(1) Before starting the engine, check the coolant, engine oil, and fuel levels and