Information hydraulic governor
BOSCH
F 019 Z2E 491
f019z2e491
ZEXEL
105866-7050
1058667050
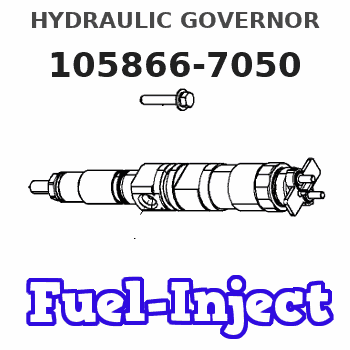
Rating:
Components :
0. | INJECTION-PUMP ASSEMBLY | 105866-7050 |
1. | _ | |
2. | FUEL INJECTION PUMP | |
3. | NUMBER PLATE | |
4. | _ | |
5. | CAPSULE | |
6. | ADJUSTING DEVICE | |
7. | NOZZLE AND HOLDER ASSY | |
8. | Nozzle and Holder | |
9. | Open Pre:MPa(Kqf/cm2) | |
10. | NOZZLE-HOLDER | |
11. | NOZZLE |
Scheme ###:
1. | [1] | 158502-0420 | BASE |
2. | [1] | 029811-8000 | BEARING PLATE |
3. | [1] | 158528-0900 | PACKING RING |
7. | [1] | 158131-0100 | GEAR SHAFT |
10. | [1] | 158028-0000 | O-RING |
11. | [1] | 158507-1920 | DIAPHRAGM HOUSING |
13. | [1] | 158621-0800 | SLEEVE |
18. | [1] | 158699-0621 | COMPENSATOR ASSY |
18/1. | [1] | 158610-1101 | POWER PISTON |
18/3. | [1] | 158654-0800 | COILED SPRING |
18/4. | [1] | 158614-0700 | STOP PIN |
18/5. | [1] | 158612-0500 | PLAIN WASHER |
18/6. | [1] | 158654-0900 | COILED SPRING |
18/7. | [1] | 016110-1220 | LOCKING WASHER |
18/8. | [1] | 158612-0401 | BUSHING |
18/9. | [2] | 016550-2310 | O-RING |
18/10. | [1] | 158615-0500 | PUMP PLUNGER |
18/11. | [1] | 025620-1410 | SPRING PIN |
35. | [3] | 029330-6070 | GASKET |
36. | [3] | 010206-2520 | HEX-SOCKET-HEAD CAP SCREW |
50. | [1] | 158600-1020 | FLYWEIGHT ASSEMBLY |
51. | [1] | 158106-0100 | PLAIN WASHER |
52. | [1] | 029811-0000 | BEARING PLATE |
53. | [1] | 158620-1220 | PILOT VALVE |
60. | [2] | 158220-0000 | GUIDE LEVER |
61. | [2] | 158736-0200 | BEARING PIN |
62. | [4] | 025520-1510 | SPLIT PIN |
70. | [1] | 158730-0220 | TERMINAL ARM |
70/1. | [1] | 158230-0020 | TERMINAL ARM |
70/2. | [1] | 158315-0200 | TERMINAL SHAFT |
70/3. | [1] | 158315-0200 | TERMINAL SHAFT |
70/4. | [2] | 158736-0100 | TAPER PIN |
70/5. | [2] | 011006-0620 | SET OF NUTS |
70/6. | [1] | 158214-0020 | SPEED DROOP ADJUSTER |
70/7. | [1] | 014020-5120 | PLAIN WASHER |
70/8. | [1] | 029320-5030 | TAB WASHER |
70/9. | [1] | 010535-1220 | FLAT-HEAD SCREW |
85. | [1] | 158814-1200 | SPEED CONTROL SHAFT |
86. | [1] | 158823-0300 | BUSHING |
87. | [1] | 158322-0200 | COILED SPRING |
88. | [1] | 158710-0400 | STRAP |
89. | [1] | 029404-5010 | BEARING PIN |
91. | [1] | 158712-2000 | CONTROL LEVER |
93. | [1] | 029010-5210 | BLEEDER SCREW |
95. | [1] | 158211-0100 | STRAP |
96. | [2] | 158653-0100 | WIRE |
104. | [1] | 158017-0900 | GASKET |
105. | [1] | 158962-5620 | GOVERNOR MOTOR ASSY |
105/1. | [1] | 158962-5210 | CASE |
105/2. | [1] | 158903-0200 | HOLDER |
105/3. | [1] | 158903-0300 | HOLDER |
105/4. | [1] | 158903-0400 | FLAT-HEAD SCREW |
105/5. | [1] | 158903-1720 | ADJUSTER |
105/6. | [2] | 158903-0800 | PLATE |
105/7. | [4] | 029010-6330 | BLEEDER SCREW M6P1.0L13 |
105/8. | [1] | 014020-8140 | PLAIN WASHER D16&8.5T1.2 |
105/9. | [1] | 158904-0500 | TOOTHED GEAR |
105/10. | [1] | 158590-0000 | BEARING PIN |
105/11. | [2] | 020106-1640 | BLEEDER SCREW M6P1.0L14 |
105/14. | [1] | 158904-0300 | LEVER SHAFT |
105/15. | [1] | 158904-0200 | LEVER SHAFT |
105/16. | [3] | 014020-8140 | PLAIN WASHER D16&8.5T1.2 |
105/16. | [3] | 014020-8140 | PLAIN WASHER D16&8.5T1.2 |
105/16. | [3] | 014020-8140 | PLAIN WASHER D16&8.5T1.2 |
105/17. | [3] | 015320-1540 | SPLIT PIN |
105/18. | [2] | 158904-0400 | TOOTHED GEAR |
105/18. | [2] | 158904-0400 | TOOTHED GEAR |
105/19. | [3] | 011005-0820 | SET OF NUTS |
105/19. | [3] | 011005-0820 | SET OF NUTS |
105/20. | [1] | 158904-1920 | ROUND NUT |
105/21. | [1] | 158916-0000 | SET OF NUTS |
105/24. | [1] | 158908-3900 | CONDENSER |
105/25. | [2] | 014110-3440 | LOCKING WASHER |
105/26. | [2] | 012153-0840 | FLAT-HEAD SCREW M3P0.5L8 |
105/27. | [1] | 158906-0700 | TERMINAL BOARD |
105/28. | [2] | 014020-4140 | PLAIN WASHER D8&4.5T0.5 |
105/29. | [2] | 014110-4440 | LOCKING WASHER |
105/30. | [2] | 012154-1640 | FLAT-HEAD SCREW |
105/31. | [1] | 158902-0300 | JOINT CONNECTION |
105/32. | [1] | 158902-0020 | FRICTION COUPLING |
105/34. | [1] | 158908-2900 | GEAR HEAD |
105/35. | [1] | 158908-4200 | MOTOR |
105/36. | [4] | 014020-4140 | PLAIN WASHER D8&4.5T0.5 |
105/37. | [4] | 158901-8100 | FLAT-HEAD SCREW |
105/38. | [1] | 158901-2200 | HOSE |
105/39. | [1] | 158901-8300 | COVER |
105/40. | [1] | 158900-0300 | BRACKET |
105/41. | [3] | 158900-0200 | BUSHING |
105/42. | [3] | 029010-6350 | BLEEDER SCREW M6P1.0L22 |
105/43. | [1] | 158907-1820 | LIMIT SWITCH |
105/44. | [1] | 158907-1720 | LIMIT SWITCH |
105/46. | [4] | 020144-1240 | BLEEDER SCREW |
105/47. | [1] | 158906-0801 | TERMINAL |
105/48. | [1] | 158562-2600 | COVER |
105/49. | [4] | 014020-6140 | PLAIN WASHER |
105/50. | [4] | 014110-6440 | LOCKING WASHER |
105/51. | [4] | 158909-0100 | BLEEDER SCREW |
105/53. | [2] | 158901-2700 | PLAIN WASHER |
105/54. | [1] | 158901-2800 | PACKING |
105/55. | [1] | 158901-2600 | GROUND |
112. | [1] | 026512-1640 | GASKET D15.9&12.2T1 |
113. | [1] | 155406-0220 | AIR FILTER |
118. | [1] | 158527-0200 | NEEDLE VALVE |
119. | [1] | 016500-0710 | O-RING |
123. | [2] | 026512-1640 | GASKET D15.9&12.2T1 |
124. | [2] | 029111-2070 | CAPSULE M12P1.5L10 |
130. | [1] | 029331-8040 | GASKET |
131. | [1] | 158660-0320 | CONTROL VALVE |
135. | [1] | 158515-0900 | INDICATOR PLATE |
137. | [1] | 158515-1000 | INDICATOR PLATE |
140. | [2] | 158820-0620 | POINTER |
140. | [2] | 158820-0620 | POINTER |
142. | [2] | 158820-0620 | POINTER |
142. | [2] | 158820-0620 | POINTER |
163. | [1] | 010210-1420 | HEX-SOCKET-HEAD CAP SCREW |
164. | [1] | 026510-1340 | GASKET D13.4&10.2T1 |
190. | [1] | 158017-1000 | GASKET |
200. | [1] | 158599-7220 | SPARE PART |
Include in #2:
105866-7050
as INJECTION-PUMP ASSEMBLY
Cross reference number
Zexel num
Bosch num
Firm num
Name
Information:
Torque for Standard Bolts, Nuts and Taperlock Studs
The following charts give general torques for bolts, nuts and taperlock studs of SAE Grade 5 or better quality.
Torques for Bolts and Nuts With Standard Threads
Torques for Taperlock Studs
Use these standard torque values for all fasteners unless otherwise specified in this publication or in the Service Manual.Torque for Metric Fasteners
This product uses 10.9 Grade metric fasteners.
Be very careful never to mix metric with customary (standard) fasteners. Mismatched or incorrect fasteners will cause engine damage or malfunction and may even result in personal injury.Original fasteners removed from the engine should be saved for reassembly whenever possible. If new fasteners are needed, they must be of the same size and grade as the ones that are being replaced.The material strength identification is usually shown on the bolt head by numbers (8.8, 10.9, etc.). Use these standard torque values unless otherwise specified in this publication or the Service Manual.The following charts give general torques for bolts and nuts with Metric Threads of SAE Grade 8.8 or better quality.
Torques for Bolts and Nuts with Metric Threads
Torque for Standard Hose Clamps-Worm Drive Band Type
The following chart gives the torques for initial installation of hose clamps on new hose and for reassembly or tightening of hose clamps on existing hose.
Torque for Constant Torque Hose Clamps
A constant torque hose clamp can be used in place of any standard hose clamp. Make sure the constant torque hose clamp is the same size as the standard clamp. Due to extreme temperature changes, hose will heat set. Heat setting causes hose clamps to loosen. Loose hose clamps can result in leaks. There have been reports of component failures caused by hose clamps loosening. The new, constant torque hose clamp will help prevent these failures.Each installation application can be different depending on the type of hose, fitting material and anticipated expansion or contraction of the hose and fittings. A torque wrench should be used for proper installation of the new, constant torque hose clamps. Constant torque hose clamps should be installed as follows:* To allow for maximum expansion, install clamps at 50 lb in (5.7 N m).* To allow for equal expansion and contraction, install clamps at 90 lb in (10.2 N m).* To allow for maximum contraction, install clamps at 125 lb in (14.1
The following charts give general torques for bolts, nuts and taperlock studs of SAE Grade 5 or better quality.
Torques for Bolts and Nuts With Standard Threads
Torques for Taperlock Studs
Use these standard torque values for all fasteners unless otherwise specified in this publication or in the Service Manual.Torque for Metric Fasteners
This product uses 10.9 Grade metric fasteners.
Be very careful never to mix metric with customary (standard) fasteners. Mismatched or incorrect fasteners will cause engine damage or malfunction and may even result in personal injury.Original fasteners removed from the engine should be saved for reassembly whenever possible. If new fasteners are needed, they must be of the same size and grade as the ones that are being replaced.The material strength identification is usually shown on the bolt head by numbers (8.8, 10.9, etc.). Use these standard torque values unless otherwise specified in this publication or the Service Manual.The following charts give general torques for bolts and nuts with Metric Threads of SAE Grade 8.8 or better quality.
Torques for Bolts and Nuts with Metric Threads
Torque for Standard Hose Clamps-Worm Drive Band Type
The following chart gives the torques for initial installation of hose clamps on new hose and for reassembly or tightening of hose clamps on existing hose.
Torque for Constant Torque Hose Clamps
A constant torque hose clamp can be used in place of any standard hose clamp. Make sure the constant torque hose clamp is the same size as the standard clamp. Due to extreme temperature changes, hose will heat set. Heat setting causes hose clamps to loosen. Loose hose clamps can result in leaks. There have been reports of component failures caused by hose clamps loosening. The new, constant torque hose clamp will help prevent these failures.Each installation application can be different depending on the type of hose, fitting material and anticipated expansion or contraction of the hose and fittings. A torque wrench should be used for proper installation of the new, constant torque hose clamps. Constant torque hose clamps should be installed as follows:* To allow for maximum expansion, install clamps at 50 lb in (5.7 N m).* To allow for equal expansion and contraction, install clamps at 90 lb in (10.2 N m).* To allow for maximum contraction, install clamps at 125 lb in (14.1