Information hydraulic governor
BOSCH
F 019 Z2E 423
f019z2e423
ZEXEL
105866-4000
1058664000
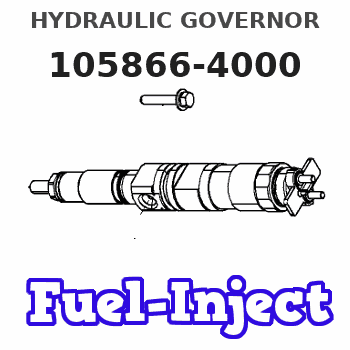
Rating:
Components :
0. | INJECTION-PUMP ASSEMBLY | 105866-4000 |
1. | _ | |
2. | FUEL INJECTION PUMP | |
3. | NUMBER PLATE | |
4. | _ | |
5. | CAPSULE | |
6. | ADJUSTING DEVICE | |
7. | NOZZLE AND HOLDER ASSY | |
8. | Nozzle and Holder | |
9. | Open Pre:MPa(Kqf/cm2) | |
10. | NOZZLE-HOLDER | |
11. | NOZZLE |
Scheme ###:
1. | [1] | 158502-0420 | BASE |
2. | [1] | 029811-8000 | BEARING PLATE |
3. | [1] | 158528-0900 | PACKING RING |
7. | [1] | 158131-0100 | GEAR SHAFT |
10. | [1] | 158028-0000 | O-RING |
11. | [1] | 158507-1920 | DIAPHRAGM HOUSING |
13. | [1] | 158621-0600 | SLIDING PIECE |
18. | [1] | 158699-0621 | COMPENSATOR ASSY |
18/1. | [1] | 158610-1101 | POWER PISTON |
18/3. | [1] | 158654-0800 | COILED SPRING |
18/4. | [1] | 158614-0700 | STOP PIN |
18/5. | [1] | 158612-0500 | PLAIN WASHER |
18/6. | [1] | 158654-0900 | COILED SPRING |
18/7. | [1] | 016110-1220 | LOCKING WASHER |
18/8. | [1] | 158612-0401 | BUSHING |
18/9. | [2] | 016550-2310 | O-RING |
18/10. | [1] | 158615-0500 | PUMP PLUNGER |
18/11. | [1] | 025620-1410 | SPRING PIN |
35. | [3] | 029330-6070 | GASKET |
36. | [3] | 010206-2520 | HEX-SOCKET-HEAD CAP SCREW |
50. | [1] | 158600-1020 | FLYWEIGHT ASSEMBLY |
51. | [1] | 158106-0100 | PLAIN WASHER |
52. | [1] | 029811-0000 | BEARING PLATE |
53. | [1] | 158620-1220 | PILOT VALVE |
60. | [2] | 158220-0000 | GUIDE LEVER |
61. | [2] | 158736-0200 | BEARING PIN |
62. | [4] | 025520-1510 | SPLIT PIN |
70. | [1] | 158730-0220 | TERMINAL ARM |
70/1. | [1] | 158230-0020 | TERMINAL ARM |
70/2. | [1] | 158315-0200 | TERMINAL SHAFT |
70/3. | [1] | 158315-0200 | TERMINAL SHAFT |
70/4. | [2] | 158736-0100 | TAPER PIN |
70/5. | [2] | 011006-0620 | SET OF NUTS |
70/6. | [1] | 158214-0020 | SPEED DROOP ADJUSTER |
70/7. | [1] | 014020-5120 | PLAIN WASHER |
70/8. | [1] | 029320-5030 | TAB WASHER |
70/9. | [1] | 010535-1220 | FLAT-HEAD SCREW |
85. | [1] | 158814-0900 | SPEED CONTROL SHAFT |
86. | [2] | 158823-0300 | BUSHING |
86. | [2] | 158823-0300 | BUSHING |
87. | [1] | 158322-0200 | COILED SPRING |
88. | [1] | 158710-0400 | STRAP |
89. | [1] | 029404-5010 | BEARING PIN |
95. | [1] | 158211-0100 | STRAP |
96. | [2] | 158653-0100 | WIRE |
104. | [1] | 158017-0900 | GASKET |
105. | [1] | 158963-4420 | PNEUMATIC CONTROLLER |
105/1. | [1] | 158562-4600 | COVER |
105/2. | [1] | 158910-0200 | CYLINDER |
105/3. | [3] | 029050-6090 | FLAT-HEAD SCREW |
105/4. | [1] | 014110-6440 | LOCKING WASHER |
105/5. | [1] | 158416-0000 | FLAT-HEAD SCREW |
105/6. | [1] | 158915-0700 | UNION NUT |
105/7. | [1] | 158918-0000 | PLAIN WASHER D30&10.8T1.00 |
105/8. | [1] | 158412-0100 | COILED SPRING K1.0 |
105/9. | [1] | 158912-0600 | COILED SPRING K5.1 |
105/9A. | [1] | 158912-1200 | COILED SPRING K5.4 |
105/9B. | [1] | 158912-0600 | COILED SPRING K5.1 |
105/10. | [1] | 158918-0000 | PLAIN WASHER D30&10.8T1.00 |
105/11. | [1] | 158413-0001 | STOP PIN |
105/12. | [1] | 158414-0000 | PUMP PLUNGER |
105/13. | [1] | 158414-0100 | DIAPHRAGM |
105/14. | [1] | 158414-0200 | PLATE |
105/15. | [1] | 013020-6040 | UNION NUT M6P1H5 |
105/16. | [1] | 158910-0300 | CAP |
105/17. | [1] | 158915-1000 | FLAT-HEAD SCREW |
105/18. | [1] | 029630-9050 | O-RING |
105/19. | [1] | 158567-1500 | WING NUT |
105/21. | [1] | 158904-2020 | ROUND NUT |
105/22. | [1] | 158916-0000 | SET OF NUTS |
105/23. | [2] | 029050-6220 | FLAT-HEAD SCREW |
105/24. | [2] | 029320-6010 | LOCKING WASHER |
105/25. | [2] | 158909-0200 | BLEEDER SCREW |
105/26. | [1] | 027114-1040 | INLET UNION |
105/27. | [2] | 029331-4120 | GASKET D18&14.2T1.5 |
105/28. | [1] | 027414-2640 | EYE BOLT |
105/30. | [1] | 013020-6040 | UNION NUT M6P1H5 |
105/31. | [1] | 158567-1200 | SET OF NUTS |
105/35. | [1] | 026512-1640 | GASKET D15.9&12.2T1 |
105/36. | [1] | 158066-0000 | BLEEDER SCREW |
106. | [4] | 029010-6350 | BLEEDER SCREW M6P1.0L22 |
118. | [1] | 158527-0200 | NEEDLE VALVE |
119. | [1] | 016500-0710 | O-RING |
123. | [2] | 026512-1640 | GASKET D15.9&12.2T1 |
124. | [2] | 029111-2070 | CAPSULE M12P1.5L10 |
130. | [1] | 029331-8040 | GASKET |
131. | [1] | 158660-0320 | CONTROL VALVE |
135. | [1] | 158515-0900 | INDICATOR PLATE |
137. | [1] | 158515-1000 | INDICATOR PLATE |
140. | [1] | 158820-0620 | POINTER |
142. | [1] | 158820-0620 | POINTER |
158. | [1] | 015040-0880 | BEARING PIN |
163. | [1] | 010210-1420 | HEX-SOCKET-HEAD CAP SCREW |
164. | [1] | 026510-1340 | GASKET D13.4&10.2T1 |
190. | [1] | 158017-1000 | GASKET |
200. | [1] | 158599-7320 | SPARE PART |
Include in #2:
105866-4000
as INJECTION-PUMP ASSEMBLY
Cross reference number
Zexel num
Bosch num
Firm num
Name
105866-4000
HYDRAULIC GOVERNOR
K 35CA HYDRAULIC GOVERNOR Hydraulic RHD10 Others
K 35CA HYDRAULIC GOVERNOR Hydraulic RHD10 Others
Information:
Caterpillar's Scheduled Oil Sampling (S O S) is the best indicator for determining what is happening inside your engine.S O S is a diagnostic tool used to determine oil performance and component wear rates with a series of tests designed to identify and measure contamination such as soot, sulfur, etc. and degradation such as the presence of fuel, water and antifreeze in a sample of oil.The tests also determine the amount of wear metals present in the oil sample, which is compared to established Caterpillar norms to determine acceptability. To be effective as an indicator, S O S must be performed on a continuing basis. Intermittent sampling will not allow wear rate trend lines to be established. Obtain at PM Level 1
Obtain S O S samples at regularly scheduled intervals to monitor the condition and maintenance requirements of your engine. Each oil sample should be taken when the oil is warm and well mixed to ensure that the sample is representative of the oil in the engine crankcase.Consult your Caterpillar dealer for complete information and assistance in establishing an S O S program for your engine(s).S O S Analysis
S O S is composed of three basic tests:* Wear Analysis* Chemical and Physical Tests* Oil Condition Analysis Wear analysis is performed with an atomic absorption spectrophotometer to monitor component wear by identifying and measuring concentrations, in parts per million, of wear elements present in the oil. Based on known normal concentration data, maximum limits ofwear elements are established. Impending failures can be identified when test results deviate from concentration levels established as acceptable, based on normal wear. Chemical and physical tests detect the presence of water, fuel and glycol (antifreeze) in the oil and determine whether or not their concentrations exceed established maximum limits. Oil condition is evaluated with infrared analysis. This test determines the presence and measures the amount of contaminants such as soot, sulfur products, oxidation, and nitration products in the oil. Infrared analysis can also assist in customizing (reducing maintaining or extending) oil change intervals for particular conditions and applications.Infrared analysis should always be accompanied by wear element analysis and chemical and physical tests to assure accurate diagnosis. Infrared analysis must be used to determine oil change intervals. S O S must include Infrared (IR) in the analysis.The test results of the oil samples will then be used as a basis for determining the oil change interval for your engine, giving you the ultimate time between oil changes without the risk of engine damage.Refer to Caterpillar pamphlet Scheduled Oil Sampling, form PEDP7105 for information and benefits of S O S.
Obtain S O S samples at regularly scheduled intervals to monitor the condition and maintenance requirements of your engine. Each oil sample should be taken when the oil is warm and well mixed to ensure that the sample is representative of the oil in the engine crankcase.Consult your Caterpillar dealer for complete information and assistance in establishing an S O S program for your engine(s).S O S Analysis
S O S is composed of three basic tests:* Wear Analysis* Chemical and Physical Tests* Oil Condition Analysis Wear analysis is performed with an atomic absorption spectrophotometer to monitor component wear by identifying and measuring concentrations, in parts per million, of wear elements present in the oil. Based on known normal concentration data, maximum limits ofwear elements are established. Impending failures can be identified when test results deviate from concentration levels established as acceptable, based on normal wear. Chemical and physical tests detect the presence of water, fuel and glycol (antifreeze) in the oil and determine whether or not their concentrations exceed established maximum limits. Oil condition is evaluated with infrared analysis. This test determines the presence and measures the amount of contaminants such as soot, sulfur products, oxidation, and nitration products in the oil. Infrared analysis can also assist in customizing (reducing maintaining or extending) oil change intervals for particular conditions and applications.Infrared analysis should always be accompanied by wear element analysis and chemical and physical tests to assure accurate diagnosis. Infrared analysis must be used to determine oil change intervals. S O S must include Infrared (IR) in the analysis.The test results of the oil samples will then be used as a basis for determining the oil change interval for your engine, giving you the ultimate time between oil changes without the risk of engine damage.Refer to Caterpillar pamphlet Scheduled Oil Sampling, form PEDP7105 for information and benefits of S O S.