Information hydraulic governor
BOSCH
F 019 Z2E 259
f019z2e259
ZEXEL
105856-4320
1058564320
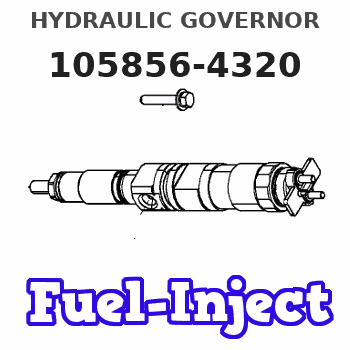
Rating:
Components :
0. | INJECTION-PUMP ASSEMBLY | 105856-4320 |
1. | _ | |
2. | FUEL INJECTION PUMP | |
3. | NUMBER PLATE | |
4. | _ | |
5. | CAPSULE | |
6. | ADJUSTING DEVICE | |
7. | NOZZLE AND HOLDER ASSY | |
8. | Nozzle and Holder | |
9. | Open Pre:MPa(Kqf/cm2) | |
10. | NOZZLE-HOLDER | |
11. | NOZZLE |
Scheme ###:
1. | [1] | 158502-0420 | BASE |
2. | [1] | 029811-8000 | BEARING PLATE |
3. | [1] | 158528-0900 | PACKING RING |
7. | [1] | 158131-0100 | GEAR SHAFT |
10. | [1] | 158028-0000 | O-RING |
11. | [1] | 158507-1820 | DIAPHRAGM HOUSING |
13. | [1] | 158621-0800 | SLEEVE |
18. | [1] | 158699-0521 | COMPENSATOR ASSY |
18/1. | [1] | 158610-0901 | POWER PISTON |
18/3. | [1] | 158654-1000 | COILED SPRING |
18/4. | [1] | 158614-0300 | STOP PIN |
18/5. | [1] | 158612-0500 | PLAIN WASHER |
18/6. | [1] | 158654-1100 | COILED SPRING |
18/7. | [1] | 016110-1220 | LOCKING WASHER |
18/8. | [1] | 158612-0001 | BUSHING |
18/9. | [2] | 158528-1300 | O-RING |
18/10. | [1] | 158615-0400 | PUMP PLUNGER |
18/11. | [1] | 025620-1410 | SPRING PIN |
35. | [3] | 029330-6070 | GASKET |
36. | [3] | 010206-2520 | HEX-SOCKET-HEAD CAP SCREW |
50. | [1] | 158600-0720 | FLYWEIGHT ASSEMBLY |
51. | [1] | 158106-0100 | PLAIN WASHER |
52. | [1] | 029811-0000 | BEARING PLATE |
53. | [1] | 158620-1220 | PILOT VALVE |
60. | [2] | 158220-0000 | GUIDE LEVER |
61. | [2] | 158736-0200 | BEARING PIN |
62. | [4] | 025520-1510 | SPLIT PIN |
70. | [1] | 158730-0220 | TERMINAL ARM |
70/1. | [1] | 158230-0020 | TERMINAL ARM |
70/2. | [1] | 158315-0200 | TERMINAL SHAFT |
70/3. | [1] | 158315-0200 | TERMINAL SHAFT |
70/4. | [2] | 158736-0100 | TAPER PIN |
70/5. | [2] | 011006-0620 | SET OF NUTS |
70/6. | [1] | 158214-0020 | SPEED DROOP ADJUSTER |
70/7. | [1] | 014020-5120 | PLAIN WASHER |
70/8. | [1] | 029320-5030 | TAB WASHER |
70/9. | [1] | 010535-1220 | FLAT-HEAD SCREW |
85. | [1] | 158814-0900 | SPEED CONTROL SHAFT |
86. | [2] | 158823-0300 | BUSHING |
86. | [2] | 158823-0300 | BUSHING |
87. | [1] | 158322-0200 | COILED SPRING |
88. | [1] | 158710-0400 | STRAP |
89. | [1] | 029404-5010 | BEARING PIN |
95. | [1] | 158211-0100 | STRAP |
96. | [2] | 158653-0100 | WIRE |
104. | [1] | 158017-0900 | GASKET |
105. | [1] | 158963-5720 | PNEUMATIC CONTROLLER |
105/1. | [1] | 158562-4600 | COVER |
105/2. | [1] | 158910-0200 | CYLINDER |
105/3. | [3] | 029050-6090 | FLAT-HEAD SCREW |
105/4. | [1] | 014110-6440 | LOCKING WASHER |
105/5. | [1] | 158416-0000 | FLAT-HEAD SCREW |
105/6. | [1] | 158915-0700 | UNION NUT |
105/7. | [1] | 158918-0000 | PLAIN WASHER D30&10.8T1.00 |
105/8. | [1] | 158412-0100 | COILED SPRING K1.0 |
105/9. | [1] | 158912-0600 | COILED SPRING K5.1 |
105/9B. | [1] | 158912-0500 | COILED SPRING K4.9 |
105/9C. | [1] | 158912-0700 | COILED SPRING K5.2 |
105/9D. | [1] | 158912-1100 | COILED SPRING K4.8 |
105/9E. | [1] | 158912-1200 | COILED SPRING K5.4 |
105/10. | [1] | 158918-0000 | PLAIN WASHER D30&10.8T1.00 |
105/11. | [1] | 158413-0001 | STOP PIN |
105/12. | [1] | 158414-0000 | PUMP PLUNGER |
105/13. | [1] | 158414-0100 | DIAPHRAGM |
105/14. | [1] | 158414-0200 | PLATE |
105/15. | [1] | 013020-6040 | UNION NUT M6P1H5 |
105/16. | [1] | 158910-0300 | CAP |
105/17. | [1] | 158915-1000 | FLAT-HEAD SCREW |
105/18. | [1] | 029630-9050 | O-RING |
105/19. | [1] | 158567-1500 | WING NUT |
105/21. | [1] | 158904-2020 | ROUND NUT |
105/22. | [1] | 158916-0000 | SET OF NUTS |
105/23. | [2] | 029050-6220 | FLAT-HEAD SCREW |
105/24. | [2] | 029320-6010 | LOCKING WASHER |
105/25. | [2] | 158909-0200 | BLEEDER SCREW |
105/26. | [1] | 027114-1040 | INLET UNION |
105/27. | [2] | 029331-4120 | GASKET D18&14.2T1.5 |
105/28. | [1] | 027414-2640 | EYE BOLT |
105/30. | [1] | 013020-6040 | UNION NUT M6P1H5 |
105/31. | [1] | 158567-1200 | SET OF NUTS |
105/35. | [1] | 026512-1640 | GASKET D15.9&12.2T1 |
105/36. | [1] | 158066-0000 | BLEEDER SCREW |
106. | [4] | 029010-6350 | BLEEDER SCREW M6P1.0L22 |
118. | [1] | 158527-0200 | NEEDLE VALVE |
119. | [1] | 016500-0710 | O-RING |
123. | [2] | 026512-1640 | GASKET D15.9&12.2T1 |
124. | [2] | 029111-2070 | CAPSULE M12P1.5L10 |
130. | [1] | 029331-8040 | GASKET |
131. | [1] | 158660-0320 | CONTROL VALVE |
135. | [1] | 158515-0700 | INDICATOR PLATE |
137. | [1] | 158515-0800 | INDICATOR PLATE |
140. | [1] | 158820-0620 | POINTER |
142. | [1] | 158820-0620 | POINTER |
158. | [1] | 015040-0880 | BEARING PIN |
190. | [1] | 158017-1000 | GASKET |
200. | [1] | 158599-6920 | SPARE PART |
Include in #2:
105856-4320
as INJECTION-PUMP ASSEMBLY
Cross reference number
Zexel num
Bosch num
Firm num
Name
Information:
Lubrication For A Rebuilt Engine
It is very important for a rebuilt engine to have "adequate" (needed) lubrication during the first seconds of operation. A "dry start" (without needed lubrication) on a rebuilt engine can cause bearing damage.When an engine is rebuilt with new parts, oil is put on each part as it is installed. This is generally enough lubrication for engine start-up. However, this lubrication may not be enough or may be lost if the rebuilt engine is placed in storage for any length of time.When a factory assembled short block assembly is installed, the oil used at the factory has to give this needed lubrication. However, the factory oil application can flow off the parts in a short block during storage or shipment. As a result, the parts in a rebuilt engine will not have "adequate" lubrication at start-up.To prevent the possibility of a "dry start" and bearing damage during the first seconds of running, use the 1P540 Flow Checking Tool Group, and shop air pressure to pressure lubricate (fill the main oil passage with oil under pressure) all rebuilt engines.Procedure for Pressure Lubrication
1. Clean the tank of the 1P540 Flow Checking Tool Group thoroughly, and set the pressure regulator to 35 5 psi (240 35 kPa).
Air pressure should not be more than 50 psi (345 kPa) at any time.
2. Put approximately one gallon of engine oil in the tank.
PRESSURE LUBRICATION (Using the 1P540 Flow Checking Tool Group)3. Connect the tooling to the engine as shown. The tap shown is connected to the main oil passage.4. Add air pressure to the tank, with the regulator set at 35 5 psi (240 35 kPa). Although the tank does have a hand pump, it is difficult to get enough air pressure to do the job with the hand pump. Therefore, use of shop air is recommended.5. Let the one gallon of engine oil flow into the oil passage under pressure.When filling the crankcase, put in one gallon of oil less than the recommendation in the Lubrication and Maintenance Guides, if engine has received this pressure lubrication application. Also, if the engine is not going to be used for a long time, do the above procedure again before the first starting.If shop air is not available for charging the tank, the hand pump may be used to get the minimum required pressure.
Do not use the same 1P540 Flow Checking Tool Group for both "pressure lubrication application" and for checking fuel flow. Incorrect cleaning is probable if the tool is used for both fuel and lube oil. Even a minute amount of dirt in the fuel system can cause fuel nozzle failure.
Dynamometer Test Precaution
To avoid possible engine damage while testing on a dynamometer, the thermostats must be installed and the shunt line connected as shown.
SHUNT LINE CONNECTED TO ENGINEInitial Operation After Engine Reconditioning
The quality of oil control components used in Caterpillar engines is such that, following engine reconditioning (with Caterpillar Service Parts), only an initial operational check
It is very important for a rebuilt engine to have "adequate" (needed) lubrication during the first seconds of operation. A "dry start" (without needed lubrication) on a rebuilt engine can cause bearing damage.When an engine is rebuilt with new parts, oil is put on each part as it is installed. This is generally enough lubrication for engine start-up. However, this lubrication may not be enough or may be lost if the rebuilt engine is placed in storage for any length of time.When a factory assembled short block assembly is installed, the oil used at the factory has to give this needed lubrication. However, the factory oil application can flow off the parts in a short block during storage or shipment. As a result, the parts in a rebuilt engine will not have "adequate" lubrication at start-up.To prevent the possibility of a "dry start" and bearing damage during the first seconds of running, use the 1P540 Flow Checking Tool Group, and shop air pressure to pressure lubricate (fill the main oil passage with oil under pressure) all rebuilt engines.Procedure for Pressure Lubrication
1. Clean the tank of the 1P540 Flow Checking Tool Group thoroughly, and set the pressure regulator to 35 5 psi (240 35 kPa).
Air pressure should not be more than 50 psi (345 kPa) at any time.
2. Put approximately one gallon of engine oil in the tank.
PRESSURE LUBRICATION (Using the 1P540 Flow Checking Tool Group)3. Connect the tooling to the engine as shown. The tap shown is connected to the main oil passage.4. Add air pressure to the tank, with the regulator set at 35 5 psi (240 35 kPa). Although the tank does have a hand pump, it is difficult to get enough air pressure to do the job with the hand pump. Therefore, use of shop air is recommended.5. Let the one gallon of engine oil flow into the oil passage under pressure.When filling the crankcase, put in one gallon of oil less than the recommendation in the Lubrication and Maintenance Guides, if engine has received this pressure lubrication application. Also, if the engine is not going to be used for a long time, do the above procedure again before the first starting.If shop air is not available for charging the tank, the hand pump may be used to get the minimum required pressure.
Do not use the same 1P540 Flow Checking Tool Group for both "pressure lubrication application" and for checking fuel flow. Incorrect cleaning is probable if the tool is used for both fuel and lube oil. Even a minute amount of dirt in the fuel system can cause fuel nozzle failure.
Dynamometer Test Precaution
To avoid possible engine damage while testing on a dynamometer, the thermostats must be installed and the shunt line connected as shown.
SHUNT LINE CONNECTED TO ENGINEInitial Operation After Engine Reconditioning
The quality of oil control components used in Caterpillar engines is such that, following engine reconditioning (with Caterpillar Service Parts), only an initial operational check