Information governor
BOSCH
F 019 Z1E 518
f019z1e518
ZEXEL
105933-0442
1059330442
MITSUBISHI
ME740868
me740868
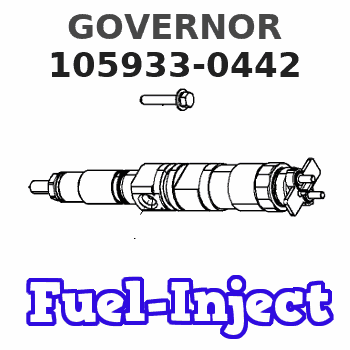
Rating:
Scheme ###:
1. | [1] | 159360-0620 | GOVERNOR HOUSING |
4. | [1] | 159362-5120 | PLATE |
5. | [10] | 139006-6100 | BLEEDER SCREW |
5. | [10] | 139006-6100 | BLEEDER SCREW |
7. | [1] | 139709-0100 | O-RING |
8. | [1] | 159364-4820 | LEVER SHAFT |
9. | [1] | 159362-6520 | CONTROL LEVER |
10. | [1] | 016010-0740 | LOCKING WASHER |
11/1. | [0] | 029311-0220 | SHIM D18&10.3T0.2 |
11/1. | [0] | 029311-0230 | SHIM D18&10.3T0.5 |
11/1. | [0] | 029311-0430 | SHIM D18&10.3T0.30 |
11/1. | [0] | 029311-0440 | SHIM D18&10.3T0.40 |
11/1. | [0] | 029311-0450 | SHIM D18&10.3T0.25 |
11/1. | [0] | 029311-0460 | SHIM D18&10.3T0.35 |
11/1. | [0] | 139410-3300 | SHIM D18&10.3T0.6 |
11/1. | [0] | 139410-3400 | SHIM D18&10.3T0.8 |
11/1. | [0] | 139410-3500 | SHIM D18&10.3T0.9 |
12. | [1] | 159368-7900 | COILED SPRING |
13. | [1] | 159362-5300 | CONTROL LEVER |
15. | [1] | 013020-8040 | UNION NUT M8P1.25H7 |
16. | [1] | 159364-5000 | CAPSULE |
17. | [1] | 159362-5420 | CONTROL LEVER |
18. | [1] | 159215-0300 | COILED SPRING |
20. | [1] | 159364-9800 | LEVER SHAFT |
21. | [2] | 020104-1240 | BLEEDER SCREW |
22. | [1] | 159362-0600 | CONTROL LEVER |
23. | [2] | 139608-0600 | PACKING RING |
23. | [2] | 139608-0600 | PACKING RING |
24. | [1] | 159362-0700 | PLAIN WASHER |
24B/1. | [0] | 139408-1000 | SHIM D16&8T0.5 |
24B/1. | [0] | 139408-1300 | SHIM D16&8T0.2 |
24C. | [1] | 159362-0700 | PLAIN WASHER |
24D. | [1] | 139308-2100 | PLAIN WASHER |
25. | [1] | 159238-4200 | LOCKING WASHER |
25B. | [1] | 159238-4200 | LOCKING WASHER |
26. | [1] | 159390-5300 | CONTROL LEVER |
27. | [1] | 159368-6100 | COILED SPRING |
28. | [1] | 159364-6000 | BUSHING |
29. | [1] | 014110-8440 | LOCKING WASHER |
30. | [1] | 013020-8040 | UNION NUT M8P1.25H7 |
31. | [1] | 155644-1301 | BLEEDER SCREW |
32. | [1] | 013030-6040 | UNION NUT M6P1H3.6 |
35. | [1] | 159361-1120 | GOVERNOR COVER |
43. | [1] | 159364-0700 | LEVER SHAFT |
44. | [1] | 159364-0800 | BEARING PIN |
45. | [2] | 016010-0640 | LOCKING WASHER |
46. | [1] | 159362-8620 | TENSIONING LEVER |
46/1. | [1] | 159362-8521 | TENSIONING LEVER |
46/2. | [1] | 159362-8721 | GUIDE LEVER |
46/3. | [1] | 159364-4201 | BEARING PIN |
46/4. | [1] | 159368-7700 | COILED SPRING |
46/5. | [1] | 016010-0540 | LOCKING WASHER |
46/6. | [1] | 016010-0440 | LOCKING WASHER |
46/7. | [1] | 159364-4121 | RACK |
46/8. | [1] | 159364-4300 | UNION NUT |
46/9. | [1] | 159364-4400 | FLAT-HEAD SCREW |
46/10. | [1] | 159368-6900 | COILED SPRING |
46/11. | [1] | 159368-7000 | COILED SPRING |
46/13. | [1] | 016010-0540 | LOCKING WASHER |
46/14. | [1] | 159364-1900 | FLAT-HEAD SCREW |
46/15. | [1] | 159364-1800 | UNION NUT |
46/16. | [1] | 159368-9500 | COILED SPRING |
47. | [2] | 016110-1020 | LOCKING WASHER |
48. | [2] | 159237-0200 | CAPSULE |
51. | [9] | 020106-3840 | BLEEDER SCREW |
65. | [1] | 154611-3020 | RACK SENSOR ASSY |
65/1. | [1] | 479775-0820 | RACK SENSOR |
65/2. | [1] | 154614-2500 | JOINT CONNECTION |
65/3. | [1] | 154614-5300 | BLOCK |
65/4. | [1] | 010234-1040 | HEX-SOCKET-HEAD CAP SCREW |
65/5. | [1] | 014110-4440 | LOCKING WASHER |
65/6. | [1] | 026524-3040 | GASKET |
65/7A. | [0] | 029310-6220 | SHIM D11.5&6.5T0.10 |
65/7B. | [0] | 029310-6230 | SHIM D11.5&6.5T0.20 |
65/7C. | [0] | 029310-6240 | SHIM D11.5&6.5T0.25 |
65/7D. | [0] | 029310-6260 | SHIM D11.5&6.4T1.00 |
65/7E. | [0] | 029310-6270 | SHIM D11.5&6.4T1.20 |
65/7F. | [0] | 029310-6280 | SHIM D11.5&6.4T1.50 |
65/8. | [1] | 154614-1900 | UNION NUT |
65/9. | [1] | 154614-3300 | BEARING PIN |
97. | [1] | 159364-2000 | CAPSULE |
100. | [1] | 154101-0920 | FLYWEIGHT ASSEMBLY |
101. | [1] | 025803-1310 | WOODRUFF KEY |
102. | [1] | 029321-2020 | LOCKING WASHER |
103. | [1] | 029231-2030 | UNION NUT |
110. | [1] | 154123-2320 | SLIDING PIECE |
111/1. | [0] | 029311-0010 | SHIM D14&10.1T0.2 |
111/1. | [0] | 029311-0180 | SHIM D14&10.1T0.3 |
111/1. | [0] | 029311-0190 | SHIM D14&10.1T0.40 |
111/1. | [0] | 029311-0210 | SHIM D14&10.1T1 |
111/1. | [0] | 139410-0000 | SHIM D14.0&10.1T0.5 |
111/1. | [0] | 139410-0100 | SHIM D14.0&10.1T1.5 |
111/1. | [0] | 139410-3000 | SHIM D14&10.1T2.0 |
111/1. | [0] | 139410-3100 | SHIM D14&10.1T3.0 |
111/1. | [0] | 139410-3200 | SHIM D14&10.1T4.0 |
112. | [1] | 159364-2100 | TERMINAL STUD |
130. | [1] | 159367-1400 | GOVERNOR SPRING |
131. | [1] | 159367-6400 | GOVERNOR SPRING |
132. | [1] | 159368-6500 | COILED SPRING |
133. | [1] | 159368-3620 | SPRING PACK |
133/1. | [1] | 159364-2200 | GUIDE SLEEVE |
133/2. | [1] | 159368-0200 | COILED SPRING |
133/3. | [1] | 159368-0300 | COILED SPRING |
133/4/1. | [0] | 029311-0010 | SHIM D14&10.1T0.2 |
133/4/1. | [0] | 029311-0180 | SHIM D14&10.1T0.3 |
133/4/1. | [0] | 029311-0190 | SHIM D14&10.1T0.40 |
133/4/1. | [0] | 029311-0210 | SHIM D14&10.1T1 |
133/4/1. | [0] | 139410-0000 | SHIM D14.0&10.1T0.5 |
133/4/1. | [0] | 139410-0100 | SHIM D14.0&10.1T1.5 |
133/4/1. | [0] | 139410-3000 | SHIM D14&10.1T2.0 |
133/4/1. | [0] | 139410-3100 | SHIM D14&10.1T3.0 |
133/4/1. | [0] | 139410-3200 | SHIM D14&10.1T4.0 |
135. | [1] | 159364-2300 | FLAT-HEAD SCREW |
137. | [1] | 159364-2000 | CAPSULE |
140. | [1] | 159364-2500 | LEVER SHAFT |
145. | [1] | 159233-5700 | UNION NUT |
149. | [1] | 159237-5400 | CAPSULE |
150. | [1] | 159364-2600 | SLOTTED WASHER |
151. | [1] | 159364-2700 | SLOTTED WASHER |
155. | [1] | 159363-3620 | STRAP |
156. | [1] | 010235-1020 | HEX-SOCKET-HEAD CAP SCREW |
160. | [1] | 159362-7620 | LEVER GROUP |
160/1. | [1] | 159364-9420 | LEVER SHAFT |
160/2. | [1] | 159362-1020 | CONTROL LEVER |
160/3. | [1] | 159362-2000 | CONTROL LEVER |
160/4. | [2] | 159362-1300 | SHIM |
160/4. | [2] | 159362-1300 | SHIM |
160/5. | [2] | 016010-0840 | LOCKING WASHER |
160/5. | [2] | 016010-0840 | LOCKING WASHER |
160/6. | [1] | 159368-7400 | COILED SPRING |
162. | [1] | 139411-0600 | SHIM |
163. | [1] | 159238-3000 | LOCKING WASHER |
164. | [1] | 139610-0800 | PACKING RING |
168. | [1] | 159381-7900 | CONTROL LEVER |
169. | [1] | 159233-7900 | LEVER SHAFT |
170. | [1] | 159381-8022 | CONTROL LEVER |
172. | [3] | 020106-1240 | BLEEDER SCREW M6P1.0L12 |
173. | [1] | 154013-1700 | BLEEDER SCREW |
173B. | [1] | 154013-1800 | BLEEDER SCREW |
173C. | [1] | 154013-1900 | BLEEDER SCREW |
174. | [1] | 154013-2000 | BLEEDER SCREW |
175. | [1] | 154013-2100 | FLAT-HEAD SCREW |
176. | [1] | 154011-4000 | UNION NUT |
177. | [1] | 154011-4100 | UNION NUT |
178. | [1] | 013131-0040 | UNION NUT M10P1.25H6 |
180. | [2] | 139310-0500 | PLAIN WASHER |
181. | [1] | 159381-8120 | CONTROL LEVER |
182. | [0] | 029311-0010 | SHIM D14&10.1T0.2 |
183. | [1] | 014010-6140 | PLAIN WASHER D13&6.5T1 |
183B. | [1] | 159235-7100 | CAP |
184. | [1] | 020006-1270 | BLEEDER SCREW M6P1L12 7T |
185. | [2] | 154339-1200 | COILED SPRING |
186. | [2] | 154156-0900 | TUBE |
187. | [1] | 159230-7700 | BUSHING |
188. | [1] | 159369-1200 | COILED SPRING |
236. | [1] | 154390-4200 | GASKET |
237. | [1] | 154390-2500 | GASKET |
250. | [1] | 159397-6920 | BRACKET |
251. | [2] | 154338-6400 | COILED SPRING |
252. | [1] | 010110-1640 | BLEEDER SCREW M101.25L16 |
252B. | [2] | 020106-1240 | BLEEDER SCREW M6P1.0L12 |
257. | [2] | 154156-0600 | TUBE |
270. | [1] | 159362-7320 | GUIDE PLATE |
271. | [2] | 020106-1640 | BLEEDER SCREW M6P1.0L14 |
300. | [1] | 159373-5400 | CAM PLATE |
301. | [1] | 016010-0840 | LOCKING WASHER |
303. | [1] | 016010-0540 | LOCKING WASHER |
311. | [2] | 159237-5400 | CAPSULE |
355. | [1] | 159397-7220 | BRACKET |
356. | [3] | 020106-1240 | BLEEDER SCREW M6P1.0L12 |
356. | [3] | 020106-1240 | BLEEDER SCREW M6P1.0L12 |
360. | [1] | 159397-9920 | BRACKET |
361. | [2] | 010138-1440 | BLEEDER SCREW M8P1.25L14 |
550. | [1] | 153146-5420 | MICROSWITCH |
551. | [1] | 154614-4120 | CLAMPING BAND |
552. | [1] | 020106-1040 | BLEEDER SCREW M6P1L12 |
835S. | [2] | 154062-1700 | CAP D20L32 |
835S. | [2] | 154062-1700 | CAP D20L32 |
Include in #1:
107691-2373
as GOVERNOR
Cross reference number
Zexel num
Bosch num
Firm num
Name
Information:
COMPRESSION PRESSURE MEASUREMENT
1. Inspection Check to make sure -(1) The crankcase oil level is correct, and the air cleaner, starter and battery are all in normal condition.(2) The engine is at the normal operating temperature.2. Measurement (1) Move the control lever to a position for shutting off fuel supply.(2) Remove all glow plugs from the engine. Install the compression gauge and adapter (ST332270) combination to a cylinder on which the compression pressure is to be measured.
Compression gauge and adaptor
Measuring compression pressure(3) Turn the engine with the starter and read the gauge pressure at the instant the gauge pointer comes to stop.(4) If the gauge reading is below the limit, overhaul the engine.
a) Be sure to measure the compression pressure on all cylinders.b) The compression pressure varies with change of engine rpm. This makes it necessary to check engine rpm at the time of measuring the compression pressure.
a) It is important to measure the compression pressure at regular intervals to obtain the data on the gradual change of the compression pressure.b) The compression pressure would be slightly higher than the standard in a new or overhauled engine owing to break-in of the piston rings, valve seats, etc. It drops as the engine components wear down.
TROUBLESHOOTING
1. GeneralThe diagnosis of troubles, especially those caused by a faulty fuel injection pump or injection nozzles, or low compression pressure, can be difficult. It requires a careful inspection to determine not which item is the cause, but how many causes are contributing to the cause. Several causes may be contributing to a single trouble.On the following pages, there are troubleshooting charts on which engine troubles can be traced to their causes. Each chart has items to be verified ahead and suggested inspection procedure.Diesel engines exhibit some marked characteristics during operation. Knowing these characteristics will help minimize time lost in tracing engine troubles to their source. Following are the characteristics of diesel engines you should know about for diagnosis:* Combustion know (diesel knock)* Some black exhaust smoke (when the engine picks up load)* Vibration (due to high compression pressure and high torque)* Hunting (when the engine speed is quickly decreased)* Some white exhaust smoke (when the engine is cold, or shortly after the engine has been started) 2. Engine troubleshooting Problem 1: Hard starting(1) Items to be checked for ahead* Clogged air cleaner* Wrong oil grade for weather conditions * Poor quality fuel* Low cranking speed(2) Inspection procedure Problem 2: Fuel knockMore or less fuel knock occurs in diesel engines. This may be caused either by an excessively large delay period or by a too fast rate of fuel injection.(1) Items to be checked for ahead* Clogged air cleaner* Poor quality fuel(2) Inspection procedure Problem 3: Overheating(1) Items to be checked for aheadOverheating might also be caused by abnormal operating conditions. If the engine is overheating but its cooling system is not contributing to this trouble, it is necessary to check the difference between the ambient temperature and coolant temperature when the engine is in
1. Inspection Check to make sure -(1) The crankcase oil level is correct, and the air cleaner, starter and battery are all in normal condition.(2) The engine is at the normal operating temperature.2. Measurement (1) Move the control lever to a position for shutting off fuel supply.(2) Remove all glow plugs from the engine. Install the compression gauge and adapter (ST332270) combination to a cylinder on which the compression pressure is to be measured.
Compression gauge and adaptor
Measuring compression pressure(3) Turn the engine with the starter and read the gauge pressure at the instant the gauge pointer comes to stop.(4) If the gauge reading is below the limit, overhaul the engine.
a) Be sure to measure the compression pressure on all cylinders.b) The compression pressure varies with change of engine rpm. This makes it necessary to check engine rpm at the time of measuring the compression pressure.
a) It is important to measure the compression pressure at regular intervals to obtain the data on the gradual change of the compression pressure.b) The compression pressure would be slightly higher than the standard in a new or overhauled engine owing to break-in of the piston rings, valve seats, etc. It drops as the engine components wear down.
TROUBLESHOOTING
1. GeneralThe diagnosis of troubles, especially those caused by a faulty fuel injection pump or injection nozzles, or low compression pressure, can be difficult. It requires a careful inspection to determine not which item is the cause, but how many causes are contributing to the cause. Several causes may be contributing to a single trouble.On the following pages, there are troubleshooting charts on which engine troubles can be traced to their causes. Each chart has items to be verified ahead and suggested inspection procedure.Diesel engines exhibit some marked characteristics during operation. Knowing these characteristics will help minimize time lost in tracing engine troubles to their source. Following are the characteristics of diesel engines you should know about for diagnosis:* Combustion know (diesel knock)* Some black exhaust smoke (when the engine picks up load)* Vibration (due to high compression pressure and high torque)* Hunting (when the engine speed is quickly decreased)* Some white exhaust smoke (when the engine is cold, or shortly after the engine has been started) 2. Engine troubleshooting Problem 1: Hard starting(1) Items to be checked for ahead* Clogged air cleaner* Wrong oil grade for weather conditions * Poor quality fuel* Low cranking speed(2) Inspection procedure Problem 2: Fuel knockMore or less fuel knock occurs in diesel engines. This may be caused either by an excessively large delay period or by a too fast rate of fuel injection.(1) Items to be checked for ahead* Clogged air cleaner* Poor quality fuel(2) Inspection procedure Problem 3: Overheating(1) Items to be checked for aheadOverheating might also be caused by abnormal operating conditions. If the engine is overheating but its cooling system is not contributing to this trouble, it is necessary to check the difference between the ambient temperature and coolant temperature when the engine is in