Information governor
BOSCH
9 420 610 440
9420610440
ZEXEL
105923-1420
1059231420
MITSUBISHI
ME740034
me740034
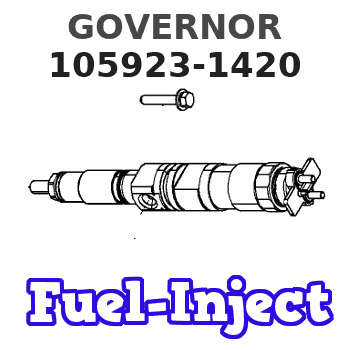
Rating:
Scheme ###:
1. | [1] | 159360-0820 | GOVERNOR HOUSING |
4. | [1] | 159362-5520 | PLATE |
5. | [8] | 139006-6100 | BLEEDER SCREW |
5. | [8] | 139006-6100 | BLEEDER SCREW |
7. | [1] | 139709-0100 | O-RING |
8. | [1] | 159364-3720 | LEVER SHAFT |
9. | [1] | 159362-5620 | CONTROL LEVER |
10. | [1] | 016010-0740 | LOCKING WASHER |
11/1. | [0] | 029311-0220 | SHIM D18&10.3T0.2 |
11/1. | [0] | 029311-0230 | SHIM D18&10.3T0.5 |
11/1. | [0] | 029311-0430 | SHIM D18&10.3T0.30 |
11/1. | [0] | 029311-0440 | SHIM D18&10.3T0.40 |
11/1. | [0] | 029311-0450 | SHIM D18&10.3T0.25 |
11/1. | [0] | 029311-0460 | SHIM D18&10.3T0.35 |
11/1. | [0] | 139410-3300 | SHIM D18&10.3T0.6 |
11/1. | [0] | 139410-3400 | SHIM D18&10.3T0.8 |
11/1. | [0] | 139410-3500 | SHIM D18&10.3T0.9 |
12. | [1] | 159368-8000 | COILED SPRING |
13. | [1] | 159362-4100 | CONTROL LEVER |
15. | [1] | 013020-8040 | UNION NUT M8P1.25H7 |
16. | [1] | 159364-5100 | CAPSULE |
17. | [1] | 159362-1821 | CONTROL LEVER |
18. | [1] | 159368-6800 | COILED SPRING |
20. | [1] | 159364-3800 | LEVER SHAFT |
21. | [2] | 020104-1240 | BLEEDER SCREW |
22. | [1] | 159362-0600 | CONTROL LEVER |
23. | [2] | 139608-0600 | PACKING RING |
23. | [2] | 139608-0600 | PACKING RING |
24. | [1] | 159362-0700 | PLAIN WASHER |
24B/1. | [0] | 139408-1000 | SHIM D16&8T0.5 |
24B/1. | [0] | 139408-1300 | SHIM D16&8T0.2 |
24C. | [1] | 159362-0700 | PLAIN WASHER |
24D. | [1] | 139308-2100 | PLAIN WASHER |
25. | [1] | 159238-4200 | LOCKING WASHER |
25B. | [1] | 159238-4200 | LOCKING WASHER |
26. | [1] | 159390-3320 | CONTROL LEVER |
27. | [1] | 159368-7300 | COILED SPRING |
28. | [1] | 159364-6000 | BUSHING |
29. | [1] | 014110-8440 | LOCKING WASHER |
30. | [1] | 013020-8040 | UNION NUT M8P1.25H7 |
31. | [1] | 155644-1301 | BLEEDER SCREW |
32. | [1] | 013030-6040 | UNION NUT M6P1H3.6 |
35. | [1] | 159361-0520 | GOVERNOR COVER |
43. | [1] | 159364-0700 | LEVER SHAFT |
44. | [1] | 159364-0800 | BEARING PIN |
45. | [2] | 016010-0640 | LOCKING WASHER |
46. | [1] | 159362-8420 | TENSIONING LEVER |
46/1. | [1] | 159362-8320 | TENSIONING LEVER |
46/2. | [1] | 159362-8221 | GUIDE LEVER |
46/3. | [1] | 159364-4201 | BEARING PIN |
46/4. | [1] | 159368-6201 | COILED SPRING |
46/5. | [1] | 016010-0540 | LOCKING WASHER |
46/6. | [1] | 016010-0440 | LOCKING WASHER |
46/7. | [1] | 159364-4121 | RACK |
46/8. | [1] | 159364-4300 | UNION NUT |
46/9. | [1] | 159364-4400 | FLAT-HEAD SCREW |
46/10. | [1] | 159368-6900 | COILED SPRING |
46/11. | [1] | 159368-7000 | COILED SPRING |
46/13. | [1] | 016010-0540 | LOCKING WASHER |
46/14. | [1] | 159364-1900 | FLAT-HEAD SCREW |
46/15. | [1] | 159364-1800 | UNION NUT |
46/16. | [1] | 159368-9500 | COILED SPRING |
47. | [2] | 016110-1020 | LOCKING WASHER |
48. | [2] | 159237-0200 | CAPSULE |
51. | [9] | 020106-3840 | BLEEDER SCREW |
65. | [1] | 155404-3400 | CAP |
66. | [1] | 026524-3040 | GASKET |
97. | [1] | 159364-2000 | CAPSULE |
100. | [1] | 154100-9220 | FLYWEIGHT ASSEMBLY |
101. | [1] | 025803-1310 | WOODRUFF KEY |
102. | [1] | 029321-2020 | LOCKING WASHER |
103. | [1] | 029231-2030 | UNION NUT |
110. | [1] | 154123-2320 | SLIDING PIECE |
111/1. | [0] | 029311-0010 | SHIM D14&10.1T0.2 |
111/1. | [0] | 029311-0180 | SHIM D14&10.1T0.3 |
111/1. | [0] | 029311-0190 | SHIM D14&10.1T0.40 |
111/1. | [0] | 029311-0210 | SHIM D14&10.1T1 |
111/1. | [0] | 139410-0000 | SHIM D14.0&10.1T0.5 |
111/1. | [0] | 139410-0100 | SHIM D14.0&10.1T1.5 |
111/1. | [0] | 139410-3000 | SHIM D14&10.1T2.0 |
111/1. | [0] | 139410-3100 | SHIM D14&10.1T3.0 |
111/1. | [0] | 139410-3200 | SHIM D14&10.1T4.0 |
112. | [1] | 159364-5200 | TERMINAL STUD |
130. | [1] | 159367-1400 | GOVERNOR SPRING |
131. | [1] | 159367-6300 | GOVERNOR SPRING |
132. | [1] | 159368-6500 | COILED SPRING |
133. | [1] | 159368-3720 | SPRING PACK |
133/1. | [1] | 159364-2200 | GUIDE SLEEVE |
133/2. | [1] | 159368-0000 | COILED SPRING |
133/3. | [1] | 159368-0600 | COILED SPRING |
133/4/1. | [0] | 029311-0010 | SHIM D14&10.1T0.2 |
133/4/1. | [0] | 029311-0180 | SHIM D14&10.1T0.3 |
133/4/1. | [0] | 029311-0190 | SHIM D14&10.1T0.40 |
133/4/1. | [0] | 029311-0210 | SHIM D14&10.1T1 |
133/4/1. | [0] | 029311-0210 | SHIM D14&10.1T1 |
133/4/1. | [0] | 139410-0000 | SHIM D14.0&10.1T0.5 |
133/4/1. | [0] | 139410-0100 | SHIM D14.0&10.1T1.5 |
133/4/1. | [0] | 139410-3000 | SHIM D14&10.1T2.0 |
133/4/1. | [0] | 139410-3100 | SHIM D14&10.1T3.0 |
133/4/1. | [0] | 139410-3200 | SHIM D14&10.1T4.0 |
135. | [1] | 159364-2300 | FLAT-HEAD SCREW |
137. | [1] | 159364-2000 | CAPSULE |
140. | [1] | 159364-2500 | LEVER SHAFT |
145. | [1] | 159233-5700 | UNION NUT |
149. | [1] | 159237-5400 | CAPSULE |
150. | [1] | 159364-2600 | SLOTTED WASHER |
151. | [1] | 159364-2700 | SLOTTED WASHER |
155. | [1] | 159363-2620 | STRAP |
156. | [1] | 010235-1020 | HEX-SOCKET-HEAD CAP SCREW |
160. | [1] | 159362-2020 | LEVER GROUP |
160/1. | [1] | 159364-3220 | LEVER SHAFT |
160/2. | [1] | 159362-1020 | CONTROL LEVER |
160/3. | [1] | 159362-2000 | CONTROL LEVER |
160/4. | [2] | 159362-1300 | SHIM |
160/4. | [2] | 159362-1300 | SHIM |
160/5. | [2] | 016010-0840 | LOCKING WASHER |
160/5. | [2] | 016010-0840 | LOCKING WASHER |
160/6. | [1] | 159368-6600 | COILED SPRING |
162. | [1] | 139411-0600 | SHIM |
163. | [1] | 159238-3000 | LOCKING WASHER |
164. | [1] | 139610-0800 | PACKING RING |
168. | [1] | 159380-0300 | CONTROL LEVER |
169. | [1] | 013020-8040 | UNION NUT M8P1.25H7 |
170. | [1] | 159380-5120 | CONTROL LEVER |
172. | [4] | 020106-1240 | BLEEDER SCREW M6P1.0L12 |
172. | [4] | 020106-1240 | BLEEDER SCREW M6P1.0L12 |
173. | [1] | 154013-1700 | BLEEDER SCREW |
173B. | [1] | 154013-1800 | BLEEDER SCREW |
173C. | [1] | 154013-1900 | BLEEDER SCREW |
174. | [1] | 154013-2000 | BLEEDER SCREW |
175. | [1] | 154013-2100 | FLAT-HEAD SCREW |
176. | [1] | 154011-4000 | UNION NUT |
177. | [1] | 154011-4100 | UNION NUT |
178. | [1] | 013131-0040 | UNION NUT M10P1.25H6 |
181. | [1] | 159380-2420 | CONTROL LEVER |
220. | [1] | 159368-8420 | HEADLESS SCREW |
221. | [1] | 154011-4300 | UNION NUT |
222. | [2] | 026512-1540 | GASKET D15.4&12.2T1.50 |
223. | [1] | 154159-2100 | CAP NUT |
225. | [2] | 029310-8050 | SHIM D13.5&8T0.5 |
226. | [1] | 159368-9101 | COILED SPRING |
227. | [1] | 159362-6720 | CONTROL LEVER |
236. | [1] | 154390-4100 | GASKET |
237. | [1] | 154390-2500 | GASKET |
250. | [1] | 159395-1120 | BRACKET |
251. | [2] | 154338-5100 | COILED SPRING |
252. | [3] | 020106-1240 | BLEEDER SCREW M6P1.0L12 |
257. | [2] | 154156-2500 | TUBE |
270. | [1] | 159362-7020 | GUIDE PLATE |
271. | [2] | 020106-1640 | BLEEDER SCREW M6P1.0L14 |
300. | [1] | 159372-6500 | CAM PLATE |
301. | [1] | 016010-0840 | LOCKING WASHER |
303. | [1] | 016010-0540 | LOCKING WASHER |
311. | [2] | 159237-5400 | CAPSULE |
350. | [2] | 139512-0000 | GASKET D17.2&12.2T1.0 |
351. | [1] | 139812-0100 | EYE BOLT |
355. | [1] | 159396-7420 | BRACKET |
356. | [1] | 010110-1640 | BLEEDER SCREW M101.25L16 |
357. | [3] | 020106-1440 | BLEEDER SCREW M6P1.0L14 |
357. | [3] | 020106-1440 | BLEEDER SCREW M6P1.0L14 |
550. | [1] | 153146-2520 | MICROSWITCH |
Include in #1:
106873-7252
as GOVERNOR
Cross reference number
Zexel num
Bosch num
Firm num
Name
Information:
Engine Lifting
When it is necessary to remove a component on an angle, remember that the capacity of an eyebolt is less as the angle between the supporting members and the object becomes less than 90 degrees. Eye Bolts and brackets should never be bent, and should only be loaded under tension.
Use a hoist to remove heavy components. Use an adjustable lifting beam to lift the engine. All supporting members (chains and cables) should be parallel to each other, and perpendicular as possible to the top of the object being lifted.Some removals require the use of lifting fixtures, to obtain proper balance and provide safe handling.To remove the engine ONLY, use the lifting eyes equipped with the engine.The lifting eyes are designed for the engine arrangement as sold. Modifying the lifting eyes and/or engine arrangement weight renders the lifting eyes and devices obsolete.If you modify the lifting eyes and/or engine arrangement weight, you are responsible for providing adequate lifting devices. Contact your Caterpillar dealer for information regarding fixtures for proper engine package lifting.Engine Lifting With Generator
Do not use the engine lifting eyes to remove the engine and generator together.
Lifting the engine and generator together requires special equipment and procedures. Contact your Caterpillar dealer for information regarding proper engine and fuel tank lifting.Engine Storage
The following Engine Storage procedures and recommendations minimize the possibility of damage to engines stored for one year or less.When an engine is not started for several weeks, the lubricating oil drains from the cylinder walls and piston rings. Rust can then form on the cylinder liner surface, increasing engine wear and decreasing engine life.Special precautions should be used with engines remaining out of service for extended periods.After one year, a complete protection procedure must be followed if the engine is kept in storage longer. To prevent excessive engine wear:* Be sure all lubrication recommendations mentioned in the Maintenance Schedule intervals chart are completed.* If freezing temperatures are expected, check the cooling system for adequate protection against freezing. A 50/50 solution of Caterpillar (permanent-type) Antifreeze and approved water will give protection to -29°C (-20°F).If it will be impossible to start the engine periodically, consult your Caterpillar dealer for instructions to prepare your engine for longer storage periods.Refer to Storage Procedures For Caterpillar Products, SEHS9031, for more detailed information on engine storage.Generator Storage Procedure
When a generator is stored, moisture may condense in the windings. Use a dry storage space and space heaters to minimize condensation. Refer to: Service Manual for SR4 Generators, SENR3985, or Special Instruction, SEHS9124, Cleaning and Drying of Caterpillar Electric Set Generators, or contact your Caterpillar dealer.After Storage
Test the main stator windings with a megohmmeter:* Before the initial startup of the generator set.* Every 3 months* if the generator is operating in a humid environment.* If the generator has not been run under load for 3 months* or more.*This is a guideline only. It may be necessary to megger more frequently if the environment is extremely humid or salty.
When servicing or repairing electric power generation
When it is necessary to remove a component on an angle, remember that the capacity of an eyebolt is less as the angle between the supporting members and the object becomes less than 90 degrees. Eye Bolts and brackets should never be bent, and should only be loaded under tension.
Use a hoist to remove heavy components. Use an adjustable lifting beam to lift the engine. All supporting members (chains and cables) should be parallel to each other, and perpendicular as possible to the top of the object being lifted.Some removals require the use of lifting fixtures, to obtain proper balance and provide safe handling.To remove the engine ONLY, use the lifting eyes equipped with the engine.The lifting eyes are designed for the engine arrangement as sold. Modifying the lifting eyes and/or engine arrangement weight renders the lifting eyes and devices obsolete.If you modify the lifting eyes and/or engine arrangement weight, you are responsible for providing adequate lifting devices. Contact your Caterpillar dealer for information regarding fixtures for proper engine package lifting.Engine Lifting With Generator
Do not use the engine lifting eyes to remove the engine and generator together.
Lifting the engine and generator together requires special equipment and procedures. Contact your Caterpillar dealer for information regarding proper engine and fuel tank lifting.Engine Storage
The following Engine Storage procedures and recommendations minimize the possibility of damage to engines stored for one year or less.When an engine is not started for several weeks, the lubricating oil drains from the cylinder walls and piston rings. Rust can then form on the cylinder liner surface, increasing engine wear and decreasing engine life.Special precautions should be used with engines remaining out of service for extended periods.After one year, a complete protection procedure must be followed if the engine is kept in storage longer. To prevent excessive engine wear:* Be sure all lubrication recommendations mentioned in the Maintenance Schedule intervals chart are completed.* If freezing temperatures are expected, check the cooling system for adequate protection against freezing. A 50/50 solution of Caterpillar (permanent-type) Antifreeze and approved water will give protection to -29°C (-20°F).If it will be impossible to start the engine periodically, consult your Caterpillar dealer for instructions to prepare your engine for longer storage periods.Refer to Storage Procedures For Caterpillar Products, SEHS9031, for more detailed information on engine storage.Generator Storage Procedure
When a generator is stored, moisture may condense in the windings. Use a dry storage space and space heaters to minimize condensation. Refer to: Service Manual for SR4 Generators, SENR3985, or Special Instruction, SEHS9124, Cleaning and Drying of Caterpillar Electric Set Generators, or contact your Caterpillar dealer.After Storage
Test the main stator windings with a megohmmeter:* Before the initial startup of the generator set.* Every 3 months* if the generator is operating in a humid environment.* If the generator has not been run under load for 3 months* or more.*This is a guideline only. It may be necessary to megger more frequently if the environment is extremely humid or salty.
When servicing or repairing electric power generation