Information governor
BOSCH
9 420 610 140
9420610140
ZEXEL
105470-1130
1054701130
ISUZU
1157204280
1157204280
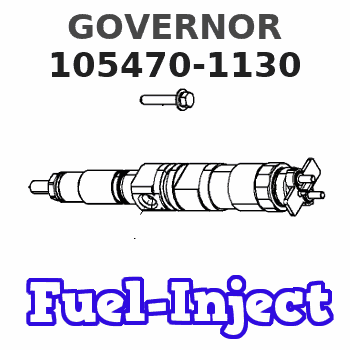
Rating:
Scheme ###:
1. | [1] | 154000-6400 | GOVERNOR HOUSING |
4. | [1] | 154364-2320 | CONTROL LEVER |
4. | [1] | 154364-2320 | CONTROL LEVER |
4/1. | [1] | 154304-3500 | CONTROL LEVER |
4/2. | [2] | 154352-2000 | BLEEDER SCREW |
4/2. | [2] | 154352-2000 | BLEEDER SCREW |
4/3. | [1] | 154364-2300 | CONTROL LEVER |
4/4. | [1] | 029311-0230 | SHIM |
4/5. | [1] | 154321-1500 | BUSHING |
4/6. | [1] | 154327-3500 | COILED SPRING |
4/7. | [1] | 154322-0100 | CAP |
4/8. | [1] | 029311-0220 | SHIM |
4/9. | [1] | 154324-2700 | LEVER SHAFT |
4/10. | [1] | 029631-0030 | O-RING |
6. | [1] | 154007-0200 | ADAPTOR |
7. | [1] | 020018-1840 | BLEEDER SCREW |
9. | [1] | 154350-1800 | PLATE |
10. | [5] | 029010-6810 | BLEEDER SCREW |
11. | [1] | 020106-1640 | BLEEDER SCREW |
13. | [1] | 029240-6010 | UNION NUT |
35. | [1] | 154510-5720 | GOVERNOR COVER |
35/1. | [1] | 154510-5700 | GOVERNOR COVER |
35/2. | [1] | 154321-1800 | BUSHING |
35/3. | [1] | 029621-0080 | PACKING RING |
38. | [1] | 154031-3500 | FLAT-HEAD SCREW |
39. | [1] | 154011-1600 | UNION NUT |
44. | [1] | 154034-0600 | FLAT-HEAD SCREW |
45. | [1] | 029200-8500 | UNION NUT |
46. | [1] | 154035-1700 | CAP NUT |
47. | [2] | 154036-0300 | CAPSULE |
47. | [2] | 154036-0300 | CAPSULE |
48. | [1] | 154010-5500 | BLEEDER SCREW |
49. | [1] | 154011-2100 | UNION NUT |
50. | [1] | 155615-1100 | FLAT-HEAD SCREW |
51. | [4] | 020106-3840 | BLEEDER SCREW |
52. | [2] | 020106-5040 | BLEEDER SCREW |
65. | [1] | 153043-5520 | STOPPING DEVICE |
80. | [1] | 154060-7900 | COVER |
82. | [1] | 029020-6210 | BLEEDER SCREW |
83. | [1] | 020006-1640 | BLEEDER SCREW |
84. | [1] | 029020-6220 | BLEEDER SCREW |
85. | [1] | 014110-6440 | LOCKING WASHER D12.2&6.1T1.5 |
86. | [1] | 020006-1640 | BLEEDER SCREW |
100. | [1] | 154100-9520 | FLYWEIGHT ASSEMBLY |
101. | [1] | 025803-1610 | WOODRUFF KEY 16 MM |
102. | [1] | 029321-2020 | LOCKING WASHER |
103. | [1] | 029231-2030 | UNION NUT |
117. | [1] | 154123-0420 | SLIDING PIECE |
118/1. | [0] | 029311-0010 | SHIM D14&10.1T0.2 |
118/1. | [0] | 029311-0180 | SHIM D14&10.1T0.3 |
118/1. | [0] | 029311-0190 | SHIM D14&10.1T0.40 |
118/1. | [0] | 029311-0210 | SHIM D14&10.1T1 |
118/1. | [0] | 139410-0000 | SHIM D14.0&10.1T0.5 |
118/1. | [0] | 139410-0100 | SHIM D14.0&10.1T1.5 |
118/1. | [0] | 139410-3000 | SHIM D14&10.1T2.0 |
118/1. | [0] | 139410-3100 | SHIM D14&10.1T3.0 |
118/1. | [0] | 139410-3200 | SHIM D14&10.1T4.0 |
130. | [1] | 154150-2400 | GOVERNOR SPRING |
132. | [1] | 154154-1200 | COILED SPRING |
140. | [1] | 154178-5521 | HEADLESS SCREW |
141. | [1] | 029201-6220 | UNION NUT |
150. | [1] | 154200-2300 | CONTROL LEVER |
170. | [1] | 154211-8420 | FORK LEVER |
173. | [1] | 016010-0540 | LOCKING WASHER |
174. | [1] | 154230-4720 | STRAP |
179. | [1] | 154238-0301 | BEARING PIN |
180. | [1] | 016010-0540 | LOCKING WASHER |
181. | [1] | 154236-5300 | TENSIONING LEVER |
182. | [1] | 154237-0400 | BEARING PIN |
183. | [2] | 154237-0600 | BUSHING |
190. | [1] | 154360-2800 | CONTROL LEVER |
192. | [1] | 020006-1670 | BLEEDER SCREW |
193. | [1] | 154362-2220 | CONTROL LEVER |
194. | [2] | 020006-1240 | BLEEDER SCREW |
203/1. | [0] | 029311-0640 | SHIM D26.0&10.2T0.95 |
203/1. | [0] | 029311-0650 | SHIM D26.0&10.2T0.20 |
203/1. | [0] | 029311-0660 | SHIM D26.0&10.2T0.25 |
203/1. | [0] | 029311-0670 | SHIM D26.0&10.2T0.30 |
203/1. | [0] | 029311-0680 | SHIM D26.0&10.2T0.35 |
203/1. | [0] | 029311-0690 | SHIM D26.0&10.2T0.40 |
203/1. | [0] | 029311-0700 | SHIM D26.0&10.2T0.50 |
203/1. | [0] | 139410-1400 | SHIM D26&10.2T0.7 |
203/1. | [0] | 139410-1500 | SHIM D26&10.2T0.9 |
203/1. | [0] | 139410-1600 | SHIM D26&10.2T0.8 |
203/1. | [0] | 139410-2700 | SHIM D26&10.2T0.6 |
205. | [1] | 154324-3000 | LEVER SHAFT |
207. | [1] | 154326-0300 | CONTROL LEVER |
211. | [1] | 016010-0840 | LOCKING WASHER |
220. | [1] | 154050-1220 | HEADLESS SCREW |
221. | [1] | 029201-2140 | UNION NUT |
222. | [2] | 139512-0000 | GASKET |
223. | [1] | 154159-1200 | CAP NUT |
236. | [1] | 154390-0000 | GASKET |
237. | [1] | 154390-0300 | GASKET |
238. | [1] | 029635-2020 | O-RING |
239. | [1] | 026508-1240 | GASKET D11.9&8.2T1.0 |
331. | [1] | 154172-3920 | HEADLESS SCREW |
332. | [1] | 029201-6010 | UNION NUT |
Include in #1:
101601-7480
as GOVERNOR
Cross reference number
Zexel num
Bosch num
Firm num
Name
105470-1130
1157204280 ISUZU
GOVERNOR
* K 14JL MECHANICAL GOVERNOR GOV RAD GOV
* K 14JL MECHANICAL GOVERNOR GOV RAD GOV
Information:
If complete injector sets are replacedon 3412E machines:
PART Hours/Age, whichevercomes first Caterpillar Dealer Suggested Customer Suggested
Parts (D/N) Labor Hrs (Cost) Parts Labor Hrs Parts (C/L) Labor Hrs (Sell)
0-4000 0-48 mos 100% 7 0 0 0 0
4001-8000 0-48 mos 33.3% 3.5 0 0 50% 3.5
* This is a 7-hour job. Actual hourspermitted up to maximums noted above.PARTS DISPOSITION
NACD Dealers, return Injector(s) to:Caterpillar Inc.Attn: Fergal O?Shea ? PS50424
Service Claims Room
8201 N. University
Peoria, IL 61615 ***** All Other Dealers *****
Handle the parts in accordance with yourWarranty Bulletin on warranty parts handling.
Attach. (1-Rework Procedure)Rework Procedure
The two tests below provide the appropriateinjector troubleshooting and repair steps for injector updates.
Use "Test for Cylinder Cutout" to determine ifindividual injector replacements (using original injector part) are needed.
Use "Test for Leakage from Poppet Valve" to determineif full injector sets (using new injector parts and software change) areappropriate for repair.
Test for Cylinder Cutout:
Warm the engine out of Cold Mode.
Connect Caterpillar Electronic Technician (ET)to the engine while the engine is running.
Ensure that the engine speed is 1200 rpm +/- 125rpm. An extremely rough running engine well need to be diagnosed by othermethods.
Cut out one bank of cylinders. Note engine rpmand the fuel position on the ET screen at that time.
Cut out one of the remaining cylinders from thecylinder bank that is running. Allow the engine to stabilize and note thefuel position.
Give power back to that cylinder. Allow the engineto stabilize and note the fuel position.
Repeat steps 5 through 6 until the cylinder bankhas been completely checked.
Power all cylinders. Allow the engine to stabilize.
Cut out the other cylinder bank and repeat steps5 through 8.
Repeat steps 4 through 9 with the engine at 2000rpm.
Compare the results from the fuel position fromeach cylinder.
If the cylinder was cut out and the fuel positiondid not change, the cylinder may not have producing power. This cylinderwould be suspect.
When you are finished with the test, decreaseengine rpm to low idle and shut the engine off.
Replace any suspect injector with a similar originalinjector. Install new seals for the injector and the jumper tube duringthis repair. The injector repair procedure is found in Special InstructionREHS0116.
If this is the third injector failure,related to this Service Letter, and to the same engine serial number within120 calendar days, replace all the injectors and software following SpecialInstruction article REHS1385.It is also possible that multiple injectors arefunctioning improperly. Complete "Test for Leakage from Poppet Valve" inorder to evaluate potential excessive injector leakage and need for fuelsystem conversion.Test for Leakage from PoppetValve:
Warm engine out of Cold Mode to normal operatingtemperature.
Turn off the engine.
Remove the valve cover bolts in preparation toobserve the injectors. Leave covers in place.
: Hot oil and components can causepersonal injury. Do not allow hot oil or components to contact skin.
Restart the engine and run at low idle with noload.
Use the ET service tool in order to perform theoverride test for the injection actuation system. Increase injection actuationpressure to the maximum value.
Observe all of the injectors under each valvecover for leakage at the spill port. A small amount of dripping is acceptable.However, a continuous stream of oil is an indication of excessive leakageof the poppet valve. Only leaks at the spill port
PART Hours/Age, whichevercomes first Caterpillar Dealer Suggested Customer Suggested
Parts (D/N) Labor Hrs (Cost) Parts Labor Hrs Parts (C/L) Labor Hrs (Sell)
0-4000 0-48 mos 100% 7 0 0 0 0
4001-8000 0-48 mos 33.3% 3.5 0 0 50% 3.5
* This is a 7-hour job. Actual hourspermitted up to maximums noted above.PARTS DISPOSITION
NACD Dealers, return Injector(s) to:Caterpillar Inc.Attn: Fergal O?Shea ? PS50424
Service Claims Room
8201 N. University
Peoria, IL 61615 ***** All Other Dealers *****
Handle the parts in accordance with yourWarranty Bulletin on warranty parts handling.
Attach. (1-Rework Procedure)Rework Procedure
The two tests below provide the appropriateinjector troubleshooting and repair steps for injector updates.
Use "Test for Cylinder Cutout" to determine ifindividual injector replacements (using original injector part) are needed.
Use "Test for Leakage from Poppet Valve" to determineif full injector sets (using new injector parts and software change) areappropriate for repair.
Test for Cylinder Cutout:
Warm the engine out of Cold Mode.
Connect Caterpillar Electronic Technician (ET)to the engine while the engine is running.
Ensure that the engine speed is 1200 rpm +/- 125rpm. An extremely rough running engine well need to be diagnosed by othermethods.
Cut out one bank of cylinders. Note engine rpmand the fuel position on the ET screen at that time.
Cut out one of the remaining cylinders from thecylinder bank that is running. Allow the engine to stabilize and note thefuel position.
Give power back to that cylinder. Allow the engineto stabilize and note the fuel position.
Repeat steps 5 through 6 until the cylinder bankhas been completely checked.
Power all cylinders. Allow the engine to stabilize.
Cut out the other cylinder bank and repeat steps5 through 8.
Repeat steps 4 through 9 with the engine at 2000rpm.
Compare the results from the fuel position fromeach cylinder.
If the cylinder was cut out and the fuel positiondid not change, the cylinder may not have producing power. This cylinderwould be suspect.
When you are finished with the test, decreaseengine rpm to low idle and shut the engine off.
Replace any suspect injector with a similar originalinjector. Install new seals for the injector and the jumper tube duringthis repair. The injector repair procedure is found in Special InstructionREHS0116.
If this is the third injector failure,related to this Service Letter, and to the same engine serial number within120 calendar days, replace all the injectors and software following SpecialInstruction article REHS1385.It is also possible that multiple injectors arefunctioning improperly. Complete "Test for Leakage from Poppet Valve" inorder to evaluate potential excessive injector leakage and need for fuelsystem conversion.Test for Leakage from PoppetValve:
Warm engine out of Cold Mode to normal operatingtemperature.
Turn off the engine.
Remove the valve cover bolts in preparation toobserve the injectors. Leave covers in place.
: Hot oil and components can causepersonal injury. Do not allow hot oil or components to contact skin.
Restart the engine and run at low idle with noload.
Use the ET service tool in order to perform theoverride test for the injection actuation system. Increase injection actuationpressure to the maximum value.
Observe all of the injectors under each valvecover for leakage at the spill port. A small amount of dripping is acceptable.However, a continuous stream of oil is an indication of excessive leakageof the poppet valve. Only leaks at the spill port