Information governor
BOSCH
F 01G 29N 0EG
f01g29n0eg
ZEXEL
105419-3312
1054193312
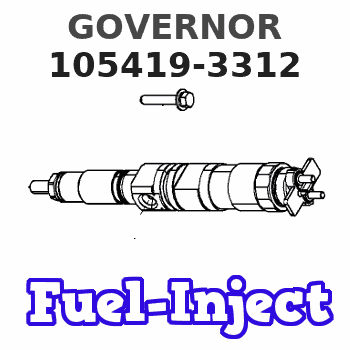
Rating:
Scheme ###:
1. | [1] | 154000-6400 | GOVERNOR HOUSING |
3. | [1] | 029632-5070 | O-RING |
4. | [1] | 154007-2900 | CAPSULE |
6. | [1] | 154007-0200 | ADAPTOR |
7. | [1] | 020018-1840 | BLEEDER SCREW |
9. | [1] | 154350-1900 | PLATE |
10. | [6] | 029010-6810 | BLEEDER SCREW |
12. | [1] | 154013-4000 | FLAT-HEAD SCREW |
13. | [1] | 154011-0100 | HEXAGON NUT |
35. | [1] | 154500-3020 | GOVERNOR COVER |
35/2. | [1] | 154321-0400 | BUSHING |
38. | [1] | 154031-3000 | FLAT-HEAD SCREW |
39. | [1] | 139206-0600 | UNION NUT |
47. | [2] | 154036-0300 | CAPSULE |
47. | [2] | 154036-0300 | CAPSULE |
51. | [2] | 020106-5040 | BLEEDER SCREW |
53. | [1] | 154010-0100 | FLAT-HEAD SCREW |
54. | [1] | 154011-4900 | UNION NUT |
56. | [2] | 020106-3840 | BLEEDER SCREW |
56B. | [2] | 139006-8500 | BLEEDER SCREW |
65. | [1] | 154050-6120 | STOPPING DEVICE |
80. | [1] | 154064-0400 | COVER |
82. | [1] | 020006-1640 | BLEEDER SCREW |
83. | [1] | 020006-1640 | BLEEDER SCREW |
84. | [1] | 020006-1640 | BLEEDER SCREW |
86. | [1] | 020006-1640 | BLEEDER SCREW |
100. | [1] | 154101-0520 | FLYWEIGHT |
101. | [1] | 025803-1610 | WOODRUFF KEY 16 MM |
102. | [1] | 029321-2020 | LOCKING WASHER |
103. | [1] | 029231-2030 | UNION NUT |
117. | [1] | 154123-0120 | SLIDING PIECE |
118/1. | [0] | 029311-0010 | SHIM D14&10.1T0.2 |
118/1. | [0] | 029311-0180 | SHIM D14&10.1T0.3 |
118/1. | [0] | 029311-0190 | SHIM D14&10.1T0.40 |
118/1. | [0] | 029311-0210 | SHIM D14&10.1T1 |
118/1. | [0] | 139410-0000 | SHIM D14&10.1T0.5 |
118/1. | [0] | 139410-0100 | SHIM D14&10.1T1.5 |
118/1. | [0] | 139410-3000 | SHIM D14&10.1T2.0 |
118/1. | [0] | 139410-3100 | SHIM D14&10.1T3.0 |
118/1. | [0] | 139410-3200 | SHIM D14&10.1T4.0 |
130. | [1] | 154150-2700 | GOVERNOR SPRING |
132. | [1] | 154154-0500 | COILED SPRING |
135. | [1] | 154158-0920 | HEADLESS SCREW |
136. | [1] | 154011-2700 | UNION NUT |
137. | [2] | 026512-1540 | GASKET |
138. | [1] | 154159-1200 | CAP NUT |
140. | [1] | 154185-3620 | HEADLESS SCREW |
141. | [1] | 029201-6080 | UNION NUT |
150. | [1] | 154200-7220 | SWIVELLING LEVER |
151. | [1] | 154204-4300 | BUSHING |
152. | [2] | 029631-8020 | O-RING |
152. | [2] | 029631-8020 | O-RING |
153. | [2] | 016010-1640 | LOCKING WASHER |
153. | [2] | 016010-1640 | LOCKING WASHER |
154. | [1] | 139611-0000 | PACKING RING |
155. | [1] | 139411-0000 | SHIM |
156. | [0] | 029311-1070 | SHIM D16&11T0.5 |
157. | [1] | 154204-4400 | BUSHING |
159. | [1] | 025803-1310 | WOODRUFF KEY 13 MM |
160. | [1] | 154206-2800 | BUSHING |
161. | [0] | 154206-0200 | PLAIN WASHER D19.5&11.2T1.0 |
170. | [1] | 154210-7420 | FORK LEVER |
174. | [1] | 154230-3920 | STRAP |
175. | [1] | 016010-0540 | LOCKING WASHER |
181. | [1] | 154236-1500 | TENSIONING LEVER |
182. | [1] | 154237-0100 | BEARING PIN |
190. | [1] | 154340-2020 | CONTROL LEVER |
191. | [1] | 154381-7601 | CONTROL LEVER |
192. | [1] | 020006-1640 | BLEEDER SCREW |
201. | [1] | 029631-0030 | O-RING |
203. | [1] | 154322-0100 | CAP |
207. | [1] | 154326-5120 | CONTROL LEVER |
208. | [1] | 154327-9900 | COILED SPRING |
211/1. | [0] | 029311-0520 | SHIM D20.8&10.3T0.2 |
211/1. | [0] | 029311-0530 | SHIM D20.8&10.3T0.25 |
211/1. | [0] | 029311-0540 | SHIM D20.8&10.3T0.3 |
211/1. | [0] | 029311-0550 | SHIM D20.8&10.3T0.35 |
211/1. | [0] | 029311-0560 | SHIM D20.8&10.3T0.4 |
211/1. | [0] | 029311-0570 | SHIM D20.8&10.3T0.5 |
236. | [1] | 154390-0000 | GASKET |
237. | [1] | 154390-0300 | GASKET |
238. | [1] | 029635-2020 | O-RING |
331. | [1] | 154188-4920 | HEADLESS SCREW |
332. | [1] | 029201-6010 | UNION NUT |
335. | [2] | 026506-1040 | GASKET |
336. | [1] | 154035-2800 | CAP NUT |
400. | [1] | 154371-9620 | BRACKET |
835S. | [1] | 154062-4120 | CAP |
836S. | [1] | 154062-3520 | CAP |
839S. | [1] | 154062-3800 | ADAPTOR |
Include in #1:
101482-9312
as GOVERNOR
Cross reference number
Zexel num
Bosch num
Firm num
Name
Information:
Operating Cost Information
The term "Life Cycle Costs" can be defined as the sum of the individual costs experienced by an engine from the day of purchase until the day of retirement. In other words, the total Owning and Operating Costs. Owning Costs are fixed costs such as initial purchase price, interest on borrowed money, depreciation and taxes. Operating Costs are a combination of fixed and variable costs such as fuel, oil, operator expenses, equipment maintenance and repair, engine maintenance and repair, and downtime.The difference between revenues generated and Life Cycle Costs (total Owning and Operating Costs) is profit.Caterpillar and your Caterpillar dealer cannot guarantee that you will make a profit. However, Caterpillar and your Caterpillar dealer can provide you with a variety of services that can help you reduce the costs that impact your profits.An Engine Operating Cost Analysis is a service provided by your dealer that was developed by Caterpillar to help you reduce the Life Cycle Cost of your engine. More specifically, an Engine Operating Cost Analysis is a computerized program that examines current and prospective oil, fuel, maintenance, minor repair, overhaul and downtime costs for the period of time you expect to own the engine. It also calculates the operating cost per hour.This useful tool provides your dealer with the specific information needed to develop a customized Maintenance Management program for your operation which will minimize your engine's operating costs.Before a cost analysis can be performed, your dealer needs to gather as much information as possible about your operation. He will need to know the length of time you plan to keep your engine, your average cost of fuel and oil as well as a variety of other ownership and cost related facts and figures.Once this information is obtained, your dealer will enter the data into an established computerized program to produce an Engine Operating Cost Analysis printout reflecting your current and projected operating costs per hour. Current and expected cost information is reflected in the data provided by you. These are the costs that affect your engine's operating cost.The General Information section contains basic user data such as name, business, location, ownership, usage per year, etc., information.The Engine Operating Information section is divided into eight subsections that address fuel consumption, oil consumption, preventive maintenance, component repairs such as water pumps, turbochargers, air compressors, etc., before failure repairs, after failure repairs, user's revenue rate per hour and lastly, miscellaneous costs such as operator wages, insurance premiums, etc.Engine Operating Cost Summary
The Operating Cost Summary is exactly what it implies, a summary. Here the total dollar expense and percentage of the total operating expense is calculated for each subsection. The individual elements are then totaled and divided by the ownership period to yield the cost per hour. Similar calculations are also made for only the maintenance and repair portion of the total operating cost.An Engine Operating Cost Analysis is a useful tool that can be used to: * Project the expected operating cost of a Caterpillar engine.*
The term "Life Cycle Costs" can be defined as the sum of the individual costs experienced by an engine from the day of purchase until the day of retirement. In other words, the total Owning and Operating Costs. Owning Costs are fixed costs such as initial purchase price, interest on borrowed money, depreciation and taxes. Operating Costs are a combination of fixed and variable costs such as fuel, oil, operator expenses, equipment maintenance and repair, engine maintenance and repair, and downtime.The difference between revenues generated and Life Cycle Costs (total Owning and Operating Costs) is profit.Caterpillar and your Caterpillar dealer cannot guarantee that you will make a profit. However, Caterpillar and your Caterpillar dealer can provide you with a variety of services that can help you reduce the costs that impact your profits.An Engine Operating Cost Analysis is a service provided by your dealer that was developed by Caterpillar to help you reduce the Life Cycle Cost of your engine. More specifically, an Engine Operating Cost Analysis is a computerized program that examines current and prospective oil, fuel, maintenance, minor repair, overhaul and downtime costs for the period of time you expect to own the engine. It also calculates the operating cost per hour.This useful tool provides your dealer with the specific information needed to develop a customized Maintenance Management program for your operation which will minimize your engine's operating costs.Before a cost analysis can be performed, your dealer needs to gather as much information as possible about your operation. He will need to know the length of time you plan to keep your engine, your average cost of fuel and oil as well as a variety of other ownership and cost related facts and figures.Once this information is obtained, your dealer will enter the data into an established computerized program to produce an Engine Operating Cost Analysis printout reflecting your current and projected operating costs per hour. Current and expected cost information is reflected in the data provided by you. These are the costs that affect your engine's operating cost.The General Information section contains basic user data such as name, business, location, ownership, usage per year, etc., information.The Engine Operating Information section is divided into eight subsections that address fuel consumption, oil consumption, preventive maintenance, component repairs such as water pumps, turbochargers, air compressors, etc., before failure repairs, after failure repairs, user's revenue rate per hour and lastly, miscellaneous costs such as operator wages, insurance premiums, etc.Engine Operating Cost Summary
The Operating Cost Summary is exactly what it implies, a summary. Here the total dollar expense and percentage of the total operating expense is calculated for each subsection. The individual elements are then totaled and divided by the ownership period to yield the cost per hour. Similar calculations are also made for only the maintenance and repair portion of the total operating cost.An Engine Operating Cost Analysis is a useful tool that can be used to: * Project the expected operating cost of a Caterpillar engine.*