Information governor
BOSCH
F 019 Z4E 574
f019z4e574
ZEXEL
105419-0100
1054190100
ISUZU
1157701530
1157701530
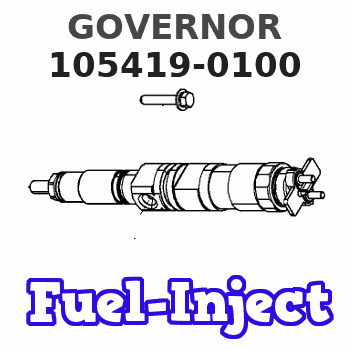
Rating:
Scheme ###:
1. | [1] | 154000-6400 | GOVERNOR HOUSING |
3. | [1] | 029632-5070 | O-RING |
4. | [1] | 154007-2900 | CAPSULE |
6. | [1] | 154007-0200 | ADAPTOR |
7. | [1] | 020018-1840 | BLEEDER SCREW M8P1.25L18 |
9. | [1] | 154350-1900 | PLATE |
10. | [6] | 029010-6810 | BLEEDER SCREW |
12. | [1] | 154010-0100 | FLAT-HEAD SCREW |
13. | [2] | 154011-0100 | HEXAGON NUT |
13. | [2] | 154011-0100 | HEXAGON NUT |
14. | [1] | 154012-1500 | BLEEDER SCREW |
15. | [1] | 014110-8440 | LOCKING WASHER |
35. | [1] | 154500-3720 | GOVERNOR COVER |
35/2. | [1] | 154321-0400 | BUSHING |
38. | [1] | 154031-0100 | FLAT-HEAD SCREW |
39. | [1] | 013020-6020 | UNION NUT M6P1H5 |
47. | [2] | 154036-0300 | CAPSULE |
47. | [2] | 154036-0300 | CAPSULE |
48. | [1] | 154037-0700 | BLEEDER SCREW |
49. | [1] | 154038-0200 | HEXAGON NUT |
51. | [2] | 020106-5040 | BLEEDER SCREW |
53. | [1] | 154010-0200 | FLAT-HEAD SCREW |
56. | [4] | 020106-3840 | BLEEDER SCREW |
65. | [1] | 155404-0200 | CAP |
80. | [1] | 154063-1220 | COVER |
82. | [1] | 020006-1640 | BLEEDER SCREW M6P1L16 4T |
83. | [1] | 020006-1640 | BLEEDER SCREW M6P1L16 4T |
84. | [1] | 029020-6250 | BLEEDER SCREW |
85. | [1] | 014110-6440 | LOCKING WASHER |
86. | [1] | 020006-1640 | BLEEDER SCREW M6P1L16 4T |
100. | [1] | 154101-0020 | FLYWEIGHT ASSEMBLY |
101. | [1] | 025803-1610 | WOODRUFF KEY |
102. | [1] | 029321-2020 | LOCKING WASHER |
103. | [1] | 029231-2030 | UNION NUT |
117. | [1] | 154123-0120 | SLIDING PIECE |
118/1. | [0] | 029311-0010 | SHIM D14&10.1T0.2 |
118/1. | [0] | 029311-0180 | SHIM D14&10.1T0.3 |
118/1. | [0] | 029311-0190 | SHIM D14&10.1T0.40 |
118/1. | [0] | 029311-0210 | SHIM D14&10.1T1 |
118/1. | [0] | 139410-0000 | SHIM D14.0&10.1T0.5 |
118/1. | [0] | 139410-0100 | SHIM D14.0&10.1T1.5 |
118/1. | [0] | 139410-3000 | SHIM D14&10.1T2.0 |
118/1. | [0] | 139410-3100 | SHIM D14&10.1T3.0 |
118/1. | [0] | 139410-3200 | SHIM D14&10.1T4.0 |
130. | [1] | 154150-2700 | GOVERNOR SPRING |
132. | [1] | 154154-0800 | COILED SPRING |
135. | [1] | 154158-1320 | HEADLESS SCREW |
136. | [1] | 154011-1700 | UNION NUT |
137. | [2] | 026512-1540 | GASKET D15.4&12.2T1.50 |
138. | [1] | 154159-1200 | CAP NUT |
140. | [1] | 154185-2120 | HEADLESS SCREW |
141. | [1] | 029201-6080 | UNION NUT |
150. | [1] | 154200-7220 | SWIVELLING LEVER |
151. | [1] | 154204-4300 | BUSHING |
152. | [2] | 029631-8020 | O-RING |
152. | [2] | 029631-8020 | O-RING |
153. | [2] | 016010-1640 | LOCKING WASHER |
153. | [2] | 016010-1640 | LOCKING WASHER |
154. | [1] | 139611-0000 | PACKING RING |
155. | [1] | 139411-0000 | SHIM |
156. | [0] | 029311-1070 | SHIM D16&11T0.5 |
157. | [1] | 154204-4400 | BUSHING |
159. | [1] | 025803-1310 | WOODRUFF KEY |
160. | [1] | 154206-2800 | BUSHING |
161. | [0] | 154206-0200 | PLAIN WASHER D19.5&11.2T1.0 |
170. | [1] | 154210-7420 | FORK LEVER |
174. | [1] | 154230-3920 | STRAP |
175. | [1] | 016010-0540 | LOCKING WASHER |
181. | [1] | 154236-1500 | TENSIONING LEVER |
182. | [1] | 154237-0100 | BEARING PIN |
190. | [1] | 154342-1420 | CONTROL LEVER |
191. | [1] | 154304-8900 | CONTROL LEVER |
192. | [1] | 020006-1640 | BLEEDER SCREW M6P1L16 4T |
195. | [1] | 154314-0200 | COILED SPRING |
201. | [1] | 029631-0030 | O-RING &9.8W2.3 |
203. | [1] | 154322-0100 | CAP |
207. | [1] | 154326-5120 | CONTROL LEVER |
208. | [1] | 154327-7300 | COILED SPRING |
211/1. | [0] | 029311-0520 | SHIM D20.8&10.3T0.2 |
211/1. | [0] | 029311-0530 | SHIM D20.8&10.3T0.25 |
211/1. | [0] | 029311-0540 | SHIM D20.8&10.3T0.3 |
211/1. | [0] | 029311-0550 | SHIM D20.8&10.3T0.35 |
211/1. | [0] | 029311-0560 | SHIM D20.8&10.3T0.4 |
211/1. | [0] | 029311-0570 | SHIM D20.8&10.3T0.5 |
236. | [1] | 154390-0000 | GASKET |
237. | [1] | 154390-0300 | GASKET |
238. | [1] | 029635-2020 | O-RING |
331. | [1] | 154179-0220 | HEADLESS SCREW |
332. | [1] | 029201-6010 | UNION NUT |
Include in #1:
101602-7240
as GOVERNOR
Cross reference number
Zexel num
Bosch num
Firm num
Name
105419-0100
1157701530 ISUZU
GOVERNOR
K 14JB MECHANICAL GOVERNOR GOV RSV GOV
K 14JB MECHANICAL GOVERNOR GOV RSV GOV
Information:
Lubrication For A Rebuilt Engine
It is very important for a rebuilt engine to have "adequate" (needed) lubrication during the first seconds of operation. A "dry start" (without needed lubrication) on a rebuilt engine or an engine that has been in storage can cause bearing damage.To prevent the possibility of a "dry start" and bearing damage during the first few seconds of running, use the 1P0540 Flow Checking Tool Group and shop air pressure to pressure lubricate (fill the main oil passage with oil under pressure) all rebuilt engines and all engines that have been in storage.Procedure For Pressure Lubrication
1. Clean the tank of the 1P0540 Flow Checking Tool Group thoroughly, and set the pressure regulator to 240 35 kPa (35 5 psi).
Air pressure should not be more than 345 kPa (50 psi) at any time.
2. Put the correct engine oil into the tank. Use a minimum of 30% of the engine oil capacity. For some engines it will be necessary to fill the tank several times to get the correct amount of oil in the engine.3. Connect the tooling to the main oil passage of the engine.4. Add air pressure to the tank, with the regulator set at 240 35 kPa (35 5 psi). Although the tank has a hand pump, it is difficult to get enough air pressure to do the job with the hand pump. Therefore, use of shop air is recommended.5. Let the engine oil flow into the oil passage under pressure.Fill the crankcase with the correct engine oil. The amount of oil used in the pressure lubrication procedure must be subtracted from the recommended refill capacity in the Operation Maintenance Manual. If the engine is not going to be used for a long time, do the above procedure again before the first start.If shop air is not available, for charging the tank, the hand pump may be used to get the minimum required pressure.
DO NOT use the same 1P0540 Flow Checking Tool Group for both "pressure lubrication application" and for checking fuel flow. Incorrect cleaning is probable if the tool is used for both fuel and lubrication oil. Even a minute amount of dirt in the fuel system can cause fuel nozzle failure.
It is very important for a rebuilt engine to have "adequate" (needed) lubrication during the first seconds of operation. A "dry start" (without needed lubrication) on a rebuilt engine or an engine that has been in storage can cause bearing damage.To prevent the possibility of a "dry start" and bearing damage during the first few seconds of running, use the 1P0540 Flow Checking Tool Group and shop air pressure to pressure lubricate (fill the main oil passage with oil under pressure) all rebuilt engines and all engines that have been in storage.Procedure For Pressure Lubrication
1. Clean the tank of the 1P0540 Flow Checking Tool Group thoroughly, and set the pressure regulator to 240 35 kPa (35 5 psi).
Air pressure should not be more than 345 kPa (50 psi) at any time.
2. Put the correct engine oil into the tank. Use a minimum of 30% of the engine oil capacity. For some engines it will be necessary to fill the tank several times to get the correct amount of oil in the engine.3. Connect the tooling to the main oil passage of the engine.4. Add air pressure to the tank, with the regulator set at 240 35 kPa (35 5 psi). Although the tank has a hand pump, it is difficult to get enough air pressure to do the job with the hand pump. Therefore, use of shop air is recommended.5. Let the engine oil flow into the oil passage under pressure.Fill the crankcase with the correct engine oil. The amount of oil used in the pressure lubrication procedure must be subtracted from the recommended refill capacity in the Operation Maintenance Manual. If the engine is not going to be used for a long time, do the above procedure again before the first start.If shop air is not available, for charging the tank, the hand pump may be used to get the minimum required pressure.
DO NOT use the same 1P0540 Flow Checking Tool Group for both "pressure lubrication application" and for checking fuel flow. Incorrect cleaning is probable if the tool is used for both fuel and lubrication oil. Even a minute amount of dirt in the fuel system can cause fuel nozzle failure.