Information governor
BOSCH
9 420 610 181
9420610181
ZEXEL
105407-2901
1054072901
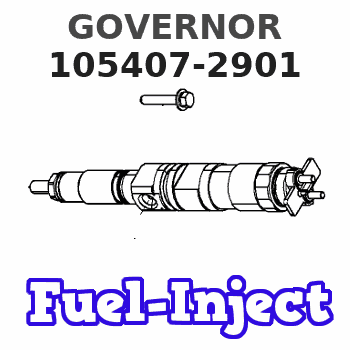
Rating:
Scheme ###:
1. | [1] | 154000-5720 | GOVERNOR HOUSING |
3. | [1] | 029632-5070 | O-RING |
4. | [1] | 154007-2900 | CAPSULE |
9. | [1] | 154350-6000 | PLATE |
10. | [8] | 020106-2040 | BLEEDER SCREW M6P1L20 |
10. | [8] | 020106-2040 | BLEEDER SCREW M6P1L20 |
12. | [1] | 154010-0100 | FLAT-HEAD SCREW |
13. | [2] | 154011-0100 | HEXAGON NUT |
13. | [2] | 154011-0100 | HEXAGON NUT |
14. | [1] | 154012-2220 | BLEEDER SCREW |
15. | [1] | 014110-8440 | LOCKING WASHER |
35. | [1] | 154500-8120 | GOVERNOR COVER |
35/2. | [1] | 154321-0400 | BUSHING |
38. | [1] | 154031-4300 | FLAT-HEAD SCREW |
39. | [1] | 139208-0400 | UNION NUT |
47. | [1] | 154036-0300 | CAPSULE |
51. | [2] | 020106-5040 | BLEEDER SCREW |
53. | [1] | 154010-0200 | FLAT-HEAD SCREW |
56. | [4] | 020106-3840 | BLEEDER SCREW |
65. | [1] | 155404-1700 | CAP |
66. | [1] | 026524-3040 | GASKET |
80. | [1] | 154063-7300 | COVER |
82. | [2] | 029020-6210 | BLEEDER SCREW |
83. | [2] | 020006-1640 | BLEEDER SCREW M6P1L16 4T |
100. | [1] | 154101-0020 | FLYWEIGHT ASSEMBLY |
101. | [1] | 025803-1310 | WOODRUFF KEY |
102. | [1] | 029321-2020 | LOCKING WASHER |
103. | [1] | 029231-2030 | UNION NUT |
117. | [1] | 154123-2320 | SLIDING PIECE |
118/1. | [0] | 029311-0010 | SHIM D14&10.1T0.2 |
118/1. | [0] | 029311-0180 | SHIM D14&10.1T0.3 |
118/1. | [0] | 029311-0190 | SHIM D14&10.1T0.40 |
118/1. | [0] | 029311-0210 | SHIM D14&10.1T1 |
118/1. | [0] | 139410-0000 | SHIM D14.0&10.1T0.5 |
118/1. | [0] | 139410-0100 | SHIM D14.0&10.1T1.5 |
118/1. | [0] | 139410-3000 | SHIM D14&10.1T2.0 |
118/1. | [0] | 139410-3100 | SHIM D14&10.1T3.0 |
118/1. | [0] | 139410-3200 | SHIM D14&10.1T4.0 |
130. | [1] | 154150-2900 | GOVERNOR SPRING |
132. | [1] | 154154-0500 | COILED SPRING |
135. | [1] | 154158-3420 | HEADLESS SCREW |
136. | [1] | 154011-1700 | UNION NUT |
137. | [2] | 026512-1540 | GASKET D15.4&12.2T1.50 |
138. | [1] | 154159-1200 | CAP NUT |
140. | [1] | 154177-0720 | HEADLESS SCREW |
141. | [1] | 029201-6010 | UNION NUT |
150. | [1] | 154200-7020 | SWIVELLING LEVER |
151. | [1] | 154204-3000 | BUSHING |
152. | [2] | 139718-0200 | O-RING |
152. | [2] | 139718-0200 | O-RING |
153. | [2] | 016010-1640 | LOCKING WASHER |
153. | [2] | 016010-1640 | LOCKING WASHER |
154. | [1] | 139611-0300 | PACKING RING |
155. | [1] | 139411-0000 | SHIM |
156. | [0] | 029311-1070 | SHIM D16&11T0.5 |
157. | [1] | 154204-3100 | BUSHING |
159. | [1] | 025803-1310 | WOODRUFF KEY |
160. | [1] | 154206-2800 | BUSHING |
161. | [0] | 154206-0200 | PLAIN WASHER D19.5&11.2T1.0 |
170. | [1] | 154210-2720 | FORK LEVER |
174. | [1] | 154230-2920 | STRAP |
175. | [1] | 016010-0540 | LOCKING WASHER |
181. | [1] | 154236-4100 | TENSIONING LEVER |
182. | [1] | 154237-1100 | BEARING PIN |
190. | [1] | 154343-1520 | CONTROL LEVER |
191. | [1] | 154366-3300 | CONTROL LEVER |
192. | [1] | 020006-1640 | BLEEDER SCREW M6P1L16 4T |
195. | [1] | 154317-0300 | COILED SPRING |
201. | [1] | 139710-0500 | O-RING |
207. | [1] | 154326-5020 | CONTROL LEVER |
211. | [0] | 029311-0220 | SHIM D18&10.3T0.2 |
211B. | [0] | 029311-0230 | SHIM D18&10.3T0.5 |
235. | [1] | 155412-5200 | IMPELLER WHEEL |
236. | [1] | 154371-5600 | GASKET |
237. | [1] | 154390-0300 | GASKET |
238. | [1] | 029635-2020 | O-RING |
335. | [2] | 026508-1140 | GASKET D11.4&8.2T1 |
336. | [1] | 154035-2000 | CAP NUT |
900S. | [1] | 025803-1310 | WOODRUFF KEY |
901S. | [1] | 025803-1610 | WOODRUFF KEY |
Include in #1:
106672-9183
as GOVERNOR
Cross reference number
Zexel num
Bosch num
Firm num
Name
Information:
Reference for 3500 Series Engines
Troubleshooting, M0080819, "3516E Engine for Tier 4 Final 994K Wheel Loaders".Testing and Adjusting, M0080815, "3516E Engine for Tier 4 Final 994K Wheel Loaders".Disassembly and Assembly, M0092351, "3516E Engines for Caterpillar Built Machines".Procedure
Note: If failed parts need to be shipped back, please cap off the ports using the caps from the new part.
What code are you troubleshooting? ____________________
Follow the correct troubleshooting procedure. Refer to "Reference for C175 Engines" and "Reference for 3500 Series Engines" Sections for correct media number to use.
When troubleshooting procedure requests the DEF quality check, DEF system inspection filter replacement or dosing accuracy, document those results in Table 1, Table 2, Table 3, and Table 4.
Table 1
DEF Quality Results
Step Instruction Completed (Yes/No) Result Comments Units
1 Follow the Testing and Adjusting procedure for "Diesel Exhaust Fluid Quality - Test"
2 DEF Contamination Test (include photo of test strip is possible) Pass/Fail
3 DEF concentration Test % at 20° C (68° F)
Table 2
DEF Tank Vent Line, Breather, and Cap Inspection Results
Step Instruction Completed (Yes/No) Result Comments Units
1 Follow the Testing and Adjusting procedure for "Diesel Exhaust Fluid Quality - Test"
2 DEF Contamination Test (include photo of test strip is possible)
3 DEF concentration Test
4 Remove the breather and inspect at the breather-to-vent line connections if debris is bypassing the breather (take photo)
5 Inspect the DEF tank manual fill cap for damage or debris (take photo)
6 Remove the DEF tank manual fill cap and inspect for damage or debris at the manual fill inlet to the tank (take a photo)
7 Remove the fill neck strainer and inspect for damage or debris (take a photo)
8 Clean or replace the strainer (if necessary) (take a photo)
Table 3
DEF Pump Filters Replaced
Step Instruction Completed (Yes/No) Result Comments Units
1 Prior to removal, inspect the DEF pump suction line fitting and DEF pump filter cap for any damage (take a photo)
2 Replace the DEF pump suction line filter fitting and DEF pump filter on the affected DEF pump. Comment on any notable damage or debris (take a photo of each post removal)
3 Bag, label (pump number in PETU, pump serial number, date removed), and return with pump.
Table 4
Dosing Accuracy Test
Step Instruction Completed (Yes/No) Result Comments Units
1 Follow the Testing and Adjusting, Aftertreatment SCR system Dosing Test.
2 For the pump in question, take a photograph of both DEF injectors, mounts, gaskets, bolts on the SCR inlet prior to removal. Ensure that the picture captures the DEF injector serial number and part number and not which position and which aftertreatment it was installed.
3 For the pump in question, remove both injectors from the SCR inlet.
4 Take a photograph of both DEF injector mounts on the SCR inlet and the tip of both DEF injectors.
5 Install each injector on the beaker.
6 Run the DEF System Dosing Accuracy test through Cat® ET for each injector.
7 Use the beaker to measure the amount of fluid from the dosing test for each injector. ____________________ml
____________________ml
8 Repeat the test for each injector to verify consistency.
Troubleshooting, M0080819, "3516E Engine for Tier 4 Final 994K Wheel Loaders".Testing and Adjusting, M0080815, "3516E Engine for Tier 4 Final 994K Wheel Loaders".Disassembly and Assembly, M0092351, "3516E Engines for Caterpillar Built Machines".Procedure
Note: If failed parts need to be shipped back, please cap off the ports using the caps from the new part.
What code are you troubleshooting? ____________________
Follow the correct troubleshooting procedure. Refer to "Reference for C175 Engines" and "Reference for 3500 Series Engines" Sections for correct media number to use.
When troubleshooting procedure requests the DEF quality check, DEF system inspection filter replacement or dosing accuracy, document those results in Table 1, Table 2, Table 3, and Table 4.
Table 1
DEF Quality Results
Step Instruction Completed (Yes/No) Result Comments Units
1 Follow the Testing and Adjusting procedure for "Diesel Exhaust Fluid Quality - Test"
2 DEF Contamination Test (include photo of test strip is possible) Pass/Fail
3 DEF concentration Test % at 20° C (68° F)
Table 2
DEF Tank Vent Line, Breather, and Cap Inspection Results
Step Instruction Completed (Yes/No) Result Comments Units
1 Follow the Testing and Adjusting procedure for "Diesel Exhaust Fluid Quality - Test"
2 DEF Contamination Test (include photo of test strip is possible)
3 DEF concentration Test
4 Remove the breather and inspect at the breather-to-vent line connections if debris is bypassing the breather (take photo)
5 Inspect the DEF tank manual fill cap for damage or debris (take photo)
6 Remove the DEF tank manual fill cap and inspect for damage or debris at the manual fill inlet to the tank (take a photo)
7 Remove the fill neck strainer and inspect for damage or debris (take a photo)
8 Clean or replace the strainer (if necessary) (take a photo)
Table 3
DEF Pump Filters Replaced
Step Instruction Completed (Yes/No) Result Comments Units
1 Prior to removal, inspect the DEF pump suction line fitting and DEF pump filter cap for any damage (take a photo)
2 Replace the DEF pump suction line filter fitting and DEF pump filter on the affected DEF pump. Comment on any notable damage or debris (take a photo of each post removal)
3 Bag, label (pump number in PETU, pump serial number, date removed), and return with pump.
Table 4
Dosing Accuracy Test
Step Instruction Completed (Yes/No) Result Comments Units
1 Follow the Testing and Adjusting, Aftertreatment SCR system Dosing Test.
2 For the pump in question, take a photograph of both DEF injectors, mounts, gaskets, bolts on the SCR inlet prior to removal. Ensure that the picture captures the DEF injector serial number and part number and not which position and which aftertreatment it was installed.
3 For the pump in question, remove both injectors from the SCR inlet.
4 Take a photograph of both DEF injector mounts on the SCR inlet and the tip of both DEF injectors.
5 Install each injector on the beaker.
6 Run the DEF System Dosing Accuracy test through Cat® ET for each injector.
7 Use the beaker to measure the amount of fluid from the dosing test for each injector. ____________________ml
____________________ml
8 Repeat the test for each injector to verify consistency.