Information governor
BOSCH
9 420 610 180
9420610180
ZEXEL
105407-2822
1054072822
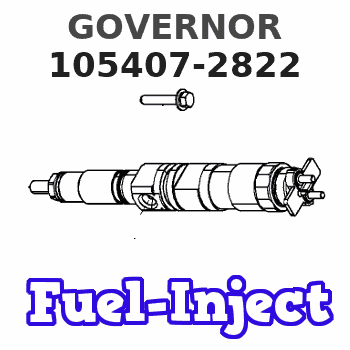
Rating:
Scheme ###:
1. | [1] | 154000-5720 | GOVERNOR HOUSING |
3. | [1] | 029632-5070 | O-RING |
4. | [1] | 154007-2900 | CAPSULE |
9. | [1] | 154350-6000 | PLATE |
10. | [8] | 020106-2040 | BLEEDER SCREW M6P1L20 |
10. | [8] | 020106-2040 | BLEEDER SCREW M6P1L20 |
12. | [1] | 154010-9300 | FLAT-HEAD SCREW |
13. | [2] | 154011-0100 | HEXAGON NUT |
13. | [2] | 154011-0100 | HEXAGON NUT |
35. | [1] | 154500-8820 | GOVERNOR COVER |
38. | [1] | 154031-4300 | FLAT-HEAD SCREW |
39. | [1] | 139208-0400 | UNION NUT |
47. | [1] | 154036-0300 | CAPSULE |
51. | [2] | 020106-5040 | BLEEDER SCREW |
53. | [1] | 154010-0300 | FLAT-HEAD SCREW |
56. | [4] | 020106-3840 | BLEEDER SCREW |
65. | [1] | 155404-1700 | CAP |
66. | [1] | 026524-3040 | GASKET |
80. | [1] | 154063-7300 | COVER |
82. | [2] | 029020-6210 | BLEEDER SCREW |
83. | [2] | 020006-1640 | BLEEDER SCREW M6P1L16 4T |
100. | [1] | 154101-0020 | FLYWEIGHT ASSEMBLY |
101. | [1] | 025803-1310 | WOODRUFF KEY |
102. | [1] | 029321-2020 | LOCKING WASHER |
103. | [1] | 029231-2030 | UNION NUT |
117. | [1] | 154123-2320 | SLIDING PIECE |
118/1. | [0] | 029311-0010 | SHIM D14&10.1T0.2 |
118/1. | [0] | 029311-0180 | SHIM D14&10.1T0.3 |
118/1. | [0] | 029311-0190 | SHIM D14&10.1T0.40 |
118/1. | [0] | 029311-0210 | SHIM D14&10.1T1 |
118/1. | [0] | 139410-0000 | SHIM D14.0&10.1T0.5 |
118/1. | [0] | 139410-0100 | SHIM D14.0&10.1T1.5 |
118/1. | [0] | 139410-3000 | SHIM D14&10.1T2.0 |
118/1. | [0] | 139410-3100 | SHIM D14&10.1T3.0 |
118/1. | [0] | 139410-3200 | SHIM D14&10.1T4.0 |
130. | [1] | 154150-0100 | GOVERNOR SPRING |
132. | [1] | 154154-0500 | COILED SPRING |
135. | [1] | 154158-0820 | HEADLESS SCREW |
136. | [1] | 154011-1700 | UNION NUT |
137. | [2] | 026512-1540 | GASKET D15.4&12.2T1.50 |
138. | [1] | 154159-1200 | CAP NUT |
140. | [1] | 154177-1520 | HEADLESS SCREW |
141. | [1] | 029201-6010 | UNION NUT |
150. | [1] | 154200-7020 | SWIVELLING LEVER |
151. | [1] | 154204-3000 | BUSHING |
152. | [2] | 029631-8020 | O-RING |
152. | [2] | 029631-8020 | O-RING |
153. | [2] | 016010-1640 | LOCKING WASHER |
153. | [2] | 016010-1640 | LOCKING WASHER |
154. | [1] | 139611-0000 | PACKING RING |
155. | [1] | 139411-0000 | SHIM |
156. | [0] | 029311-1070 | SHIM D16&11T0.5 |
157. | [1] | 154204-3100 | BUSHING |
159. | [1] | 025803-1310 | WOODRUFF KEY |
160. | [1] | 154206-2800 | BUSHING |
161. | [0] | 154206-0200 | PLAIN WASHER D19.5&11.2T1.0 |
170. | [1] | 154210-2720 | FORK LEVER |
174. | [1] | 154230-2920 | STRAP |
175. | [1] | 016010-0540 | LOCKING WASHER |
181. | [1] | 154236-4100 | TENSIONING LEVER |
182. | [1] | 154237-1100 | BEARING PIN |
190. | [1] | 154343-3220 | CONTROL LEVER |
235. | [1] | 155412-5300 | IMPELLER WHEEL |
236. | [1] | 154371-5600 | GASKET |
237. | [1] | 154390-0300 | GASKET |
238. | [1] | 029635-2020 | O-RING |
335. | [2] | 026508-1140 | GASKET D11.4&8.2T1 |
336. | [1] | 154035-2000 | CAP NUT |
900S. | [1] | 025803-1310 | WOODRUFF KEY |
901S. | [1] | 025803-1610 | WOODRUFF KEY |
Cross reference number
Zexel num
Bosch num
Firm num
Name
Information:
General Operation Guidelines
For Generator Set Installations of Cat DPF Filter Systems
Ensure that the engine operation will adhere to the Cat DPF Filter ARB verification guidelines below:
At least 30 percent of the operating time the exhaust temperature is above 300° C (572° F) and the engine load is above 40 percent.
Fuel sulfur content is less than 15 ppm, ULSD
Engine PM output of less than 0.2 g/bhp-hr
Insulate all exhaust components between the turbocharger and Cat DPF Filter inlet. This inspection includes piping, expansion joints, and bellows.
Install the Cat DLAS monitor/alarm system as the monitoring/alarm system is the key component to ensuring the Cat DPF Filter unit is working as intended. The monitoring/alarm system also ensures that the filter media is not plugging up with particulate matter. This unit records date, time, temperature and backpressure data, allowing the user a comprehensive understanding of engine duty cycle and Cat DPF Filter performance. Follow the installation instructions carefully. Check the integrity of all plumbing and wiring connections. Once installed, download data using the optional software and check that the temperature and backpressure data correspond to engine load output.
Investigate all warnings that the Cat DLAS generates. Solid yellow or red alarms indicate an increase in backpressure and must be investigated. Blinking yellow or red lights indicate a problem with temperature or pressure measurements and require physical checks of the sensors and connections. Data must be collected when an error is generated.
The data stored in the DLAS is easily down loaded using an Ethernet browser and is required to see real-time data and stored data. This data can then be transferred into Microsoft Excel for viewing and graphing. The data includes a history of all errors generated plus 26,000 lines of temperature, backpressure, time, and date values. This data equates to approximately 100 hours of operation when the logging interval is set at 30 seconds.
Create a schedule for downloading Cat DLAS data and graphing the performance. Backpressure may go up and down but over time should be flat, meaning that particulate is not accumulating on the Cat DPF Filter. If particulate is not accumulating, the Cat DPF Filter is said to be regenerating, or self cleaning. This process is the intended operation of regeneration.
DO NOT operate the generator after a red alarm is triggered. Monitor the backpressure during operation using the Cat DLAS interface to an Ethernet browser or a pressure gauge. If the backpressure continues to increase, stop the engine as soon as possible, and allow the exhaust to cool. Remove the Cat DPF Filter for cleaning. If the backpressure decreases, the engine may continue operation until the backpressure has stabilized. Consult your local Cat dealer.
Continuous low load operation should be limited to under 2 hours. After 2 hours but less than 4 hours, and if no alarms have been triggered, regenerate the Cat DPF Filter by operating the engine at 80 percent to 100 percent load for 45 minutes. The Cat DPF can also be removed for cleaning off the machine or engine.
If
For Generator Set Installations of Cat DPF Filter Systems
Ensure that the engine operation will adhere to the Cat DPF Filter ARB verification guidelines below:
At least 30 percent of the operating time the exhaust temperature is above 300° C (572° F) and the engine load is above 40 percent.
Fuel sulfur content is less than 15 ppm, ULSD
Engine PM output of less than 0.2 g/bhp-hr
Insulate all exhaust components between the turbocharger and Cat DPF Filter inlet. This inspection includes piping, expansion joints, and bellows.
Install the Cat DLAS monitor/alarm system as the monitoring/alarm system is the key component to ensuring the Cat DPF Filter unit is working as intended. The monitoring/alarm system also ensures that the filter media is not plugging up with particulate matter. This unit records date, time, temperature and backpressure data, allowing the user a comprehensive understanding of engine duty cycle and Cat DPF Filter performance. Follow the installation instructions carefully. Check the integrity of all plumbing and wiring connections. Once installed, download data using the optional software and check that the temperature and backpressure data correspond to engine load output.
Investigate all warnings that the Cat DLAS generates. Solid yellow or red alarms indicate an increase in backpressure and must be investigated. Blinking yellow or red lights indicate a problem with temperature or pressure measurements and require physical checks of the sensors and connections. Data must be collected when an error is generated.
The data stored in the DLAS is easily down loaded using an Ethernet browser and is required to see real-time data and stored data. This data can then be transferred into Microsoft Excel for viewing and graphing. The data includes a history of all errors generated plus 26,000 lines of temperature, backpressure, time, and date values. This data equates to approximately 100 hours of operation when the logging interval is set at 30 seconds.
Create a schedule for downloading Cat DLAS data and graphing the performance. Backpressure may go up and down but over time should be flat, meaning that particulate is not accumulating on the Cat DPF Filter. If particulate is not accumulating, the Cat DPF Filter is said to be regenerating, or self cleaning. This process is the intended operation of regeneration.
DO NOT operate the generator after a red alarm is triggered. Monitor the backpressure during operation using the Cat DLAS interface to an Ethernet browser or a pressure gauge. If the backpressure continues to increase, stop the engine as soon as possible, and allow the exhaust to cool. Remove the Cat DPF Filter for cleaning. If the backpressure decreases, the engine may continue operation until the backpressure has stabilized. Consult your local Cat dealer.
Continuous low load operation should be limited to under 2 hours. After 2 hours but less than 4 hours, and if no alarms have been triggered, regenerate the Cat DPF Filter by operating the engine at 80 percent to 100 percent load for 45 minutes. The Cat DPF can also be removed for cleaning off the machine or engine.
If