Information governor
BOSCH
9 420 614 558
9420614558
ZEXEL
105404-5630
1054045630
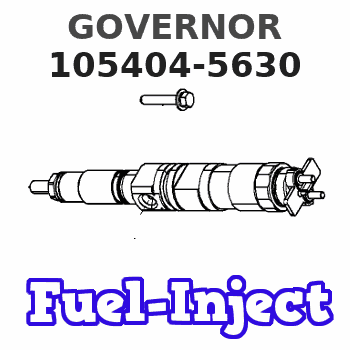
Rating:
Scheme ###:
1. | [1] | 154620-0200 | GOVERNOR HOUSING |
2. | [1] | 154007-2900 | CAPSULE |
3. | [1] | 154620-3200 | GASKET |
4. | [1] | 154620-1400 | COVER |
5. | [4] | 020006-1640 | BLEEDER SCREW M6P1L16 4T |
6. | [1] | 154621-4300 | BLEEDER SCREW |
7. | [1] | 154621-4100 | PLAIN WASHER |
8. | [1] | 154620-7900 | ADAPTOR |
9. | [1] | 154375-9020 | PLATE |
10. | [5] | 029010-6810 | BLEEDER SCREW |
11. | [1] | 020106-1840 | BLEEDER SCREW M6P1L18 |
12. | [1] | 154010-0100 | FLAT-HEAD SCREW |
13. | [2] | 154011-0100 | HEXAGON NUT |
13. | [2] | 154011-0100 | HEXAGON NUT |
16. | [1] | 029632-5070 | O-RING |
35. | [1] | 154500-3020 | GOVERNOR COVER |
35/2. | [1] | 154321-0400 | BUSHING |
38. | [1] | 154031-3000 | FLAT-HEAD SCREW |
39. | [1] | 139206-0600 | UNION NUT |
47. | [1] | 154036-0300 | CAPSULE |
51. | [2] | 139006-7100 | BLEEDER SCREW |
53. | [1] | 154010-0200 | FLAT-HEAD SCREW |
56. | [4] | 020106-3840 | BLEEDER SCREW |
65. | [1] | 155404-5120 | STOPPING DEVICE |
66. | [1] | 026518-2240 | GASKET D21.9&18.2T1 |
80. | [1] | 154063-5100 | COVER |
81. | [1] | 154358-7200 | BRACKET |
82. | [1] | 029020-6260 | BLEEDER SCREW |
83. | [1] | 029020-6260 | BLEEDER SCREW |
84. | [1] | 020006-1640 | BLEEDER SCREW M6P1L16 4T |
86. | [1] | 020006-2040 | BLEEDER SCREW M6P1L20 4T |
100. | [1] | 154621-2120 | FLYWEIGHT ASSEMBLY |
102. | [1] | 029321-2020 | LOCKING WASHER |
103. | [1] | 029231-2030 | UNION NUT |
117. | [1] | 154123-0120 | SLIDING PIECE |
118/1. | [0] | 029311-0010 | SHIM D14&10.1T0.2 |
118/1. | [0] | 029311-0180 | SHIM D14&10.1T0.3 |
118/1. | [0] | 029311-0190 | SHIM D14&10.1T0.40 |
118/1. | [0] | 029311-0210 | SHIM D14&10.1T1 |
118/1. | [0] | 139410-0000 | SHIM D14.0&10.1T0.5 |
118/1. | [0] | 139410-0100 | SHIM D14.0&10.1T1.5 |
118/1. | [0] | 139410-3000 | SHIM D14&10.1T2.0 |
118/1. | [0] | 139410-3100 | SHIM D14&10.1T3.0 |
118/1. | [0] | 139410-3200 | SHIM D14&10.1T4.0 |
130. | [1] | 154150-0400 | GOVERNOR SPRING |
132. | [1] | 154154-5200 | COILED SPRING |
135. | [1] | 154158-0920 | HEADLESS SCREW |
136. | [1] | 154011-1700 | UNION NUT |
137. | [2] | 026512-1540 | GASKET D15.4&12.2T1.50 |
138. | [1] | 154159-1200 | CAP NUT |
140. | [1] | 154177-1020 | HEADLESS SCREW |
141. | [1] | 029201-6010 | UNION NUT |
150. | [1] | 154200-7020 | SWIVELLING LEVER |
151. | [1] | 154204-3000 | BUSHING |
152. | [2] | 029631-8020 | O-RING |
152. | [2] | 029631-8020 | O-RING |
153. | [2] | 016010-1640 | LOCKING WASHER |
153. | [2] | 016010-1640 | LOCKING WASHER |
154. | [1] | 139611-0000 | PACKING RING |
155. | [1] | 139411-0000 | SHIM |
156. | [0] | 029311-1070 | SHIM D16&11T0.5 |
157. | [1] | 154204-3100 | BUSHING |
159. | [1] | 025803-1310 | WOODRUFF KEY |
160. | [1] | 154206-2800 | BUSHING |
161. | [0] | 154206-0200 | PLAIN WASHER D19.5&11.2T1.0 |
170. | [1] | 154211-4420 | FORK LEVER |
174. | [1] | 154620-2520 | STRAP |
175. | [1] | 016010-0540 | LOCKING WASHER |
181. | [1] | 154236-4100 | TENSIONING LEVER |
182. | [1] | 154237-1100 | BEARING PIN |
190. | [1] | 154343-9220 | CONTROL LEVER |
191. | [1] | 154382-3720 | CONTROL LEVER |
192. | [1] | 020006-1840 | BLEEDER SCREW M6P1L18 |
201. | [1] | 029631-0030 | O-RING &9.8W2.3 |
207. | [1] | 154326-8520 | LEVER GROUP |
211. | [0] | 029311-0220 | SHIM D18&10.3T0.2 |
211B. | [0] | 029311-0230 | SHIM D18&10.3T0.5 |
236. | [1] | 154390-0000 | GASKET |
237. | [1] | 154390-0300 | GASKET |
238. | [1] | 029635-2020 | O-RING |
335. | [2] | 026506-1040 | GASKET D9.9&6.2T1 |
336. | [1] | 154035-1600 | CAP NUT |
400. | [1] | 154620-8700 | CAPSULE |
401. | [1] | 154620-3100 | GASKET |
402. | [1] | 154620-8800 | BEARING PIN |
403. | [1] | 154620-8901 | PLATE |
404. | [1] | 010038-1840 | BLEEDER SCREW M8P1.25L18 |
405. | [1] | 154620-1500 | FLANGE BUSHING |
406. | [1] | 154620-4700 | BLEEDER SCREW |
407. | [2] | 014110-8440 | LOCKING WASHER |
407. | [2] | 014110-8440 | LOCKING WASHER |
408. | [2] | 014010-8140 | PLAIN WASHER D18&8.5T1.6 |
408. | [2] | 014010-8140 | PLAIN WASHER D18&8.5T1.6 |
409. | [1] | 154620-9000 | O-RING |
Include in #1:
101405-3090
as GOVERNOR
Cross reference number
Zexel num
Bosch num
Firm num
Name
Information:
Introduction
The problem that is identified below does not have a known permanent solution. Until a permanent solution is known, use the solution that is identified below.Problem
An industry-wide issue has arisen with a specific type of deposit that forms in modern fuel injection systems and has a negative effect on operation.The C175 fuel system operates under higher pressures and temperatures than previous injection systems. Clearances between precision moving parts can be minute, typically less than 5 microns.A soapy type of deposit has been found in some C175 fuel injection systems. The formation of the deposits is being investigated by Caterpillar, along with the fuel industry and the petroleum industry.The cause of the deposits is complex, involving these kinds of variables:
Temperature
Pressure
Fuel chemistry
Water and contaminants in the fuelThe following symptoms are associated with the soapy deposits in the fuel injectors:
A loss of power
Excessive variations in exhaust temperature
Rough running
Hard starting, especially after allowing an engine to cool down before restarting
Stuck injectorsSevere deposits cause the injector to stick in one position, resulting in a cylinder that does not fire.To verify the presence of the deposits, the injector from a cold cylinder must be returned to Caterpillar.Solution
If the above symptoms are diagnosed or if the deposits are confirmed, use 343-6210 Cleaner (FUEL) to remove the deposits.The 343-6210 Cleaner (FUEL) is the only fuel system cleaner that has been tested and approved by Cat for use in Cat diesel engines.For sites that are more susceptible to injector deposits, maintain a supply of 343-6210 Cleaner (FUEL) in order to address the problem quickly.For more information, refer to the "Cat Diesel Fuel System Cleaner" topic in Operation and Maintenance Manual, SEBU6250, "Caterpillar Machine Fluids Recommendations" or in Operation and Maintenance Manual, SEBU6251, "Cat Commercial Diesel Engine Fluids Recommendations".Note: Depending on the amounts of deposits, the fuel filter may plug after initial use of the cleaner due to removal of the deposits. The frequency of the plugging will decrease as the fuel system returns to a condition that is clean and stable.Perform the following recommendations in order to reduce the potential for the formation of injector deposits:
Prior to filling the engine fuel tank with fuel from a storage tank, filter the fuel through an absolute filter of 4 µm.
Use filters of 4 µm filtration on the breathers of fuel storage tanks. In dusty environments, use a filter of 4 µm on the breather of the engine fuel tank.
Regularly monitor bulk fuel in order to ensure that concentrations of calcium, sodium, zinc, and magnesium are less than 1 ppm.
Caterpillar does not generally recommend the use of aftermarket fuel additives. If an aftermarket fuel additive is considered to be necessary, use the additive with caution. Follow the guidelines in the "Aftermarket Fuel Additives" topic in Operation and Maintenance Manual, SEBU6250, "Caterpillar Machine Fluids Recommendations" or in Operation and Maintenance Manual, SEBU6251, "Cat Commercial Diesel Engine Fluids Recommendations".
Make sure that the
The problem that is identified below does not have a known permanent solution. Until a permanent solution is known, use the solution that is identified below.Problem
An industry-wide issue has arisen with a specific type of deposit that forms in modern fuel injection systems and has a negative effect on operation.The C175 fuel system operates under higher pressures and temperatures than previous injection systems. Clearances between precision moving parts can be minute, typically less than 5 microns.A soapy type of deposit has been found in some C175 fuel injection systems. The formation of the deposits is being investigated by Caterpillar, along with the fuel industry and the petroleum industry.The cause of the deposits is complex, involving these kinds of variables:
Temperature
Pressure
Fuel chemistry
Water and contaminants in the fuelThe following symptoms are associated with the soapy deposits in the fuel injectors:
A loss of power
Excessive variations in exhaust temperature
Rough running
Hard starting, especially after allowing an engine to cool down before restarting
Stuck injectorsSevere deposits cause the injector to stick in one position, resulting in a cylinder that does not fire.To verify the presence of the deposits, the injector from a cold cylinder must be returned to Caterpillar.Solution
If the above symptoms are diagnosed or if the deposits are confirmed, use 343-6210 Cleaner (FUEL) to remove the deposits.The 343-6210 Cleaner (FUEL) is the only fuel system cleaner that has been tested and approved by Cat for use in Cat diesel engines.For sites that are more susceptible to injector deposits, maintain a supply of 343-6210 Cleaner (FUEL) in order to address the problem quickly.For more information, refer to the "Cat Diesel Fuel System Cleaner" topic in Operation and Maintenance Manual, SEBU6250, "Caterpillar Machine Fluids Recommendations" or in Operation and Maintenance Manual, SEBU6251, "Cat Commercial Diesel Engine Fluids Recommendations".Note: Depending on the amounts of deposits, the fuel filter may plug after initial use of the cleaner due to removal of the deposits. The frequency of the plugging will decrease as the fuel system returns to a condition that is clean and stable.Perform the following recommendations in order to reduce the potential for the formation of injector deposits:
Prior to filling the engine fuel tank with fuel from a storage tank, filter the fuel through an absolute filter of 4 µm.
Use filters of 4 µm filtration on the breathers of fuel storage tanks. In dusty environments, use a filter of 4 µm on the breather of the engine fuel tank.
Regularly monitor bulk fuel in order to ensure that concentrations of calcium, sodium, zinc, and magnesium are less than 1 ppm.
Caterpillar does not generally recommend the use of aftermarket fuel additives. If an aftermarket fuel additive is considered to be necessary, use the additive with caution. Follow the guidelines in the "Aftermarket Fuel Additives" topic in Operation and Maintenance Manual, SEBU6250, "Caterpillar Machine Fluids Recommendations" or in Operation and Maintenance Manual, SEBU6251, "Cat Commercial Diesel Engine Fluids Recommendations".
Make sure that the