Information governor
BOSCH
9 420 612 739
9420612739
ZEXEL
105401-0261
1054010261
KUBOTA
12748761560
12748761560
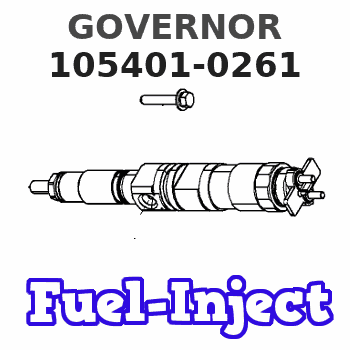
Rating:
Scheme ###:
1. | [1] | 154004-5120 | GOVERNOR HOUSING |
2. | [1] | 154007-2900 | CAPSULE |
3. | [1] | 154390-2000 | GASKET |
4. | [1] | 154063-7900 | COVER |
5. | [4] | 020006-1640 | BLEEDER SCREW M6P1L16 4T |
6. | [1] | 154007-0200 | ADAPTOR |
7. | [1] | 020018-1840 | BLEEDER SCREW M8P1.25L18 |
8. | [1] | 029632-5070 | O-RING |
9. | [1] | 154350-1800 | PLATE |
10. | [5] | 029010-6810 | BLEEDER SCREW |
11. | [1] | 020106-1640 | BLEEDER SCREW M6P1.0L14 |
12. | [1] | 154010-0100 | FLAT-HEAD SCREW |
13. | [2] | 154011-0100 | HEXAGON NUT |
13. | [2] | 154011-0100 | HEXAGON NUT |
16. | [1] | 155004-3200 | LEVER SHAFT |
18. | [1] | 155003-2620 | CONTROL LEVER |
19. | [1] | 155006-0700 | BLEEDER SCREW |
20. | [1] | 139308-0900 | PLAIN WASHER D16&8T1 |
20. | [1] | 139308-0900 | PLAIN WASHER D16&8T1 |
20B. | [1] | 139308-1000 | PLAIN WASHER D16&8T1.5 |
20B. | [1] | 139308-1000 | PLAIN WASHER D16&8T1.5 |
23. | [1] | 025520-1210 | SPLIT PIN |
24. | [1] | 154206-2000 | BUSHING |
25. | [1] | 154327-3600 | COILED SPRING |
26. | [1] | 154367-4400 | CONTROL LEVER |
27. | [1] | 014110-8440 | LOCKING WASHER |
28. | [1] | 013020-8040 | UNION NUT M8P1.25H7 |
29. | [1] | 139408-1500 | SHIM |
29B. | [0] | 139408-1400 | SHIM |
29C. | [0] | 139408-1500 | SHIM |
30. | [2] | 029620-8050 | PACKING RING |
30. | [2] | 029620-8050 | PACKING RING |
35. | [1] | 154022-7920 | GOVERNOR COVER |
38. | [1] | 154031-1300 | FLAT-HEAD SCREW |
39. | [1] | 139206-0600 | UNION NUT |
47. | [2] | 154036-0300 | CAPSULE |
47. | [2] | 154036-0300 | CAPSULE |
51. | [2] | 139006-7100 | BLEEDER SCREW |
51B. | [4] | 020106-5040 | BLEEDER SCREW |
53. | [1] | 154010-0100 | FLAT-HEAD SCREW |
65. | [1] | 153020-4420 | STOPPING DEVICE |
66. | [1] | 026518-2240 | GASKET D21.9&18.2T1 |
80. | [1] | 154063-4520 | COVER |
82. | [2] | 029020-6210 | BLEEDER SCREW |
83. | [2] | 020006-1640 | BLEEDER SCREW M6P1L16 4T |
100. | [1] | 154101-0020 | FLYWEIGHT ASSEMBLY |
101. | [1] | 025803-1610 | WOODRUFF KEY |
102. | [1] | 029321-2020 | LOCKING WASHER |
103. | [1] | 029231-2030 | UNION NUT |
117. | [1] | 154123-0120 | SLIDING PIECE |
118/1. | [0] | 029311-0010 | SHIM D14&10.1T0.2 |
118/1. | [0] | 029311-0180 | SHIM D14&10.1T0.3 |
118/1. | [0] | 029311-0190 | SHIM D14&10.1T0.40 |
118/1. | [0] | 029311-0210 | SHIM D14&10.1T1 |
118/1. | [0] | 139410-0000 | SHIM D14.0&10.1T0.5 |
118/1. | [0] | 139410-0100 | SHIM D14.0&10.1T1.5 |
118/1. | [0] | 139410-3000 | SHIM D14&10.1T2.0 |
118/1. | [0] | 139410-3100 | SHIM D14&10.1T3.0 |
118/1. | [0] | 139410-3200 | SHIM D14&10.1T4.0 |
130. | [1] | 154150-6400 | GOVERNOR SPRING |
132. | [1] | 154154-0701 | COILED SPRING |
135. | [1] | 154158-0820 | HEADLESS SCREW |
136. | [1] | 029201-2290 | UNION NUT |
137. | [2] | 026512-1540 | GASKET D15.4&12.2T1.50 |
138. | [1] | 154159-1200 | CAP NUT |
140. | [1] | 154185-1320 | HEADLESS SCREW |
141. | [1] | 029201-6010 | UNION NUT |
150. | [1] | 154200-7020 | SWIVELLING LEVER |
151. | [1] | 154204-3000 | BUSHING |
151. | [1] | 154204-3000 | BUSHING |
152. | [2] | 029631-8020 | O-RING |
152. | [2] | 029631-8020 | O-RING |
153. | [2] | 016010-1640 | LOCKING WASHER |
153. | [2] | 016010-1640 | LOCKING WASHER |
154. | [1] | 139611-0000 | PACKING RING |
155. | [1] | 139411-0000 | SHIM |
156. | [0] | 029311-1070 | SHIM D16&11T0.5 |
157. | [1] | 154204-3100 | BUSHING |
159. | [1] | 025803-1310 | WOODRUFF KEY |
160. | [1] | 154206-2800 | BUSHING |
161. | [0] | 154206-0200 | PLAIN WASHER D19.5&11.2T1.0 |
170. | [1] | 154217-2920 | FORK LEVER |
171. | [1] | 016010-0540 | LOCKING WASHER |
172. | [4] | 029310-5170 | SHIM D8&5.3T0.5 |
173. | [3] | 025520-1210 | SPLIT PIN |
174. | [1] | 154234-4120 | STRAP |
175. | [1] | 154232-3100 | CONNECTOR |
176. | [1] | 154222-5800 | BEARING PIN |
177. | [1] | 155402-3800 | SAFETY PIN |
181. | [1] | 154236-4100 | TENSIONING LEVER |
182. | [1] | 154237-0100 | BEARING PIN |
190. | [1] | 154345-5320 | CONTROL LEVER |
195. | [1] | 154314-2600 | COILED SPRING |
235. | [1] | 155412-5200 | IMPELLER WHEEL |
236. | [1] | 154390-0000 | GASKET |
237. | [1] | 154390-0300 | GASKET |
238. | [1] | 029635-2020 | O-RING |
255. | [1] | 154400-7420 | DIAPHRAGM |
256. | [1] | 154400-4800 | STOP PIN |
257. | [2] | 029330-8050 | GASKET |
257. | [2] | 029330-8050 | GASKET |
258. | [1] | 139308-0700 | LOCKING WASHER |
259. | [1] | 013030-6040 | UNION NUT M6P1H3.6 |
260. | [1] | 154401-3620 | CONTROL LEVER |
261. | [1] | 154401-1320 | STRAP |
262. | [1] | 026510-1440 | GASKET D13.9&10.2T1 |
263. | [1] | 154401-2100 | BLEEDER SCREW |
264. | [1] | 016010-0540 | LOCKING WASHER |
265. | [1] | 154222-6200 | BEARING PIN |
266. | [1] | 029300-4010 | PLAIN WASHER |
267. | [1] | 154402-5700 | COILED SPRING |
268. | [1] | 154404-3900 | COVER |
269. | [2] | 020106-2540 | BLEEDER SCREW M6P1L25 |
270. | [1] | 154034-1900 | FLAT-HEAD SCREW |
271. | [1] | 023040-6040 | UNION NUT |
273. | [1] | 029731-0180 | EYE BOLT |
274. | [2] | 026510-1340 | GASKET D13.4&10.2T1 |
275. | [0] | 029312-0180 | SHIM D25.5&20T0.5 |
275B. | [0] | 029312-0210 | SHIM D25.5&20T0.2 |
276. | [1] | 154035-0320 | CAP NUT |
277. | [1] | 014110-6440 | LOCKING WASHER |
278. | [2] | 154413-2600 | GASKET |
281. | [1] | 029010-6010 | CAPSULE M6P1.0L7 |
282. | [1] | 026506-1040 | GASKET D9.9&6.2T1 |
283. | [1] | 016010-0440 | LOCKING WASHER |
285. | [1] | 029010-6310 | BLEEDER SCREW |
300. | [1] | 154359-1320 | BRACKET |
301. | [1] | 154371-0420 | BLEEDER SCREW |
302. | [1] | 014110-8440 | LOCKING WASHER |
303. | [1] | 154011-1100 | UNION NUT |
304. | [1] | 029300-8320 | SHIM |
310. | [1] | 013020-8040 | UNION NUT M8P1.25H7 |
311. | [1] | 014010-8140 | PLAIN WASHER D18&8.5T1.6 |
312. | [1] | 014110-8440 | LOCKING WASHER |
335. | [2] | 026506-1040 | GASKET D9.9&6.2T1 |
336. | [1] | 154035-1600 | CAP NUT |
353. | [2] | 029310-9080 | SHIM D16&9T1.7 |
Include in #1:
101402-9182
as GOVERNOR
Cross reference number
Zexel num
Bosch num
Firm num
Name
105401-0261
12748761560 KUBOTA
GOVERNOR
K 14JB MECHANICAL GOVERNOR GOV RSV GOV
K 14JB MECHANICAL GOVERNOR GOV RSV GOV
105401-0261
12748761560 YANMAR
GOVERNOR
K 14JB MECHANICAL GOVERNOR GOV RSV GOV
K 14JB MECHANICAL GOVERNOR GOV RSV GOV
Information:
Jacket Water Pump
A failed water pump might cause severe engine overheating problems that could result in cracks in the cylinder head, a piston seizure or other potential damage to the engine.Visually inspect the water pump for leaks. If leaking is observed, replace all seals. Refer to the Service Manual for the procedure to replace the seals.Turbocharger
Refer to the Turbocharger topic in the Every 3000 Hours maintenance interval for information regarding turbocharger inspection. Refer to the Service Manual, or consult with your Caterpillar dealer for the complete turbocharger inspection procedure.Alternator and Starting Motor
Caterpillar recommends a scheduled inspection of the alternator. Inspect the alternator for loose connections and proper battery charging. Inspect the ammeter gauge during engine operation to ensure the batteries and/or electrical system is performing correctly. Make repairs as necessary. Refer to the Service Manual.Check the alternator and battery charger for proper operation. If the batteries are properly charged, ammeter reading should be very near zero. All batteries should be kept charged. The batteries should be kept warm because temperature affects the cranking power. If the battery is too cold, it will not crank the engine, even if the engine is warm.When the engine is not run for long periods of time or run for short periods, the batteries may not fully recharge. Ensure the alternator performs properly to charge the battery and to help prevent the battery from freezing.If the starting motor fails, the engine may not start in an emergency situation. Caterpillar recommends a schedule inspection/check of your starting motor. The starting motor should be checked for correct operation. All electrical connections should be cleaned and checked. Refer to the established procedure for inspection and specifications in the Service Manual, or contact your Caterpillar dealer for assistance.Repair Before Failure
Until recently, engine maintenance and repair management involved changing the oil when it was convenient and repairing the engine when it was damaged. This seemed to be the accepted way of managing a maintenance operation.However, due to a variety of circumstances, increasing competition have caused users to look for ways to prolong equipment life and lower operating costs so that they could be competitive.To assist Caterpillar engine users in prolonging engine life and reducing operating costs, the Value Planned Repair approach to engine maintenance was developed.The Value Planned Repair approach can be tailored for any engine. This approach, when properly structured, outlines every maintenance and repair service required to support an engine from the day it enters service until the day it is retired.To ensure the repair is performed efficiently and expediently, the Value Planned Repair concept approaches a given repair in three basis steps:1. Repair determination2. Evaluation of repair options3. Selection of the most appropriate optionThe Value Planned Repair approach addresses:* Services required to maintain an engine at optimum efficiency.* Scheduled maintenance, repairs and overhauls to minimize unscheduled downtime.* Preplanned repairs and overhauls that can be flat-rated, putting you in charge of costs.* Repair
A failed water pump might cause severe engine overheating problems that could result in cracks in the cylinder head, a piston seizure or other potential damage to the engine.Visually inspect the water pump for leaks. If leaking is observed, replace all seals. Refer to the Service Manual for the procedure to replace the seals.Turbocharger
Refer to the Turbocharger topic in the Every 3000 Hours maintenance interval for information regarding turbocharger inspection. Refer to the Service Manual, or consult with your Caterpillar dealer for the complete turbocharger inspection procedure.Alternator and Starting Motor
Caterpillar recommends a scheduled inspection of the alternator. Inspect the alternator for loose connections and proper battery charging. Inspect the ammeter gauge during engine operation to ensure the batteries and/or electrical system is performing correctly. Make repairs as necessary. Refer to the Service Manual.Check the alternator and battery charger for proper operation. If the batteries are properly charged, ammeter reading should be very near zero. All batteries should be kept charged. The batteries should be kept warm because temperature affects the cranking power. If the battery is too cold, it will not crank the engine, even if the engine is warm.When the engine is not run for long periods of time or run for short periods, the batteries may not fully recharge. Ensure the alternator performs properly to charge the battery and to help prevent the battery from freezing.If the starting motor fails, the engine may not start in an emergency situation. Caterpillar recommends a schedule inspection/check of your starting motor. The starting motor should be checked for correct operation. All electrical connections should be cleaned and checked. Refer to the established procedure for inspection and specifications in the Service Manual, or contact your Caterpillar dealer for assistance.Repair Before Failure
Until recently, engine maintenance and repair management involved changing the oil when it was convenient and repairing the engine when it was damaged. This seemed to be the accepted way of managing a maintenance operation.However, due to a variety of circumstances, increasing competition have caused users to look for ways to prolong equipment life and lower operating costs so that they could be competitive.To assist Caterpillar engine users in prolonging engine life and reducing operating costs, the Value Planned Repair approach to engine maintenance was developed.The Value Planned Repair approach can be tailored for any engine. This approach, when properly structured, outlines every maintenance and repair service required to support an engine from the day it enters service until the day it is retired.To ensure the repair is performed efficiently and expediently, the Value Planned Repair concept approaches a given repair in three basis steps:1. Repair determination2. Evaluation of repair options3. Selection of the most appropriate optionThe Value Planned Repair approach addresses:* Services required to maintain an engine at optimum efficiency.* Scheduled maintenance, repairs and overhauls to minimize unscheduled downtime.* Preplanned repairs and overhauls that can be flat-rated, putting you in charge of costs.* Repair