Information fuel-injection pump
BOSCH
9 410 611 169
9410611169
ZEXEL
108062-0100
1080620100
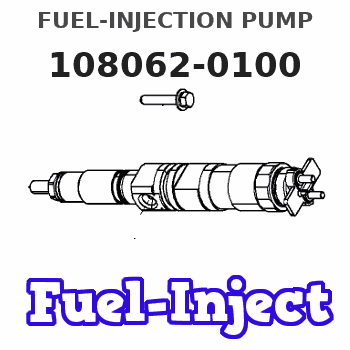
Rating:
Scheme ###:
1. | [1] | 134080-0821 | PUMP HOUSING |
1/30. | [3] | 029040-6020 | STUD |
1/45. | [1] | 134311-0000 | SPACER RING |
1/50. | [12] | 134138-0200 | STUD |
7. | [6] | 134149-3220 | PLUNGER-AND-BARREL ASSY |
7/1. | [1] | 134176-1920 | PLUNGER-AND-BARREL ASSY |
7/3. | [1] | 134160-0120 | DELIVERY-VALVE ASSEMBLY |
7/4. | [1] | 134171-0320 | FITTING |
7/5. | [1] | 016500-1800 | O-RING |
7/6. | [1] | 134117-1700 | FILLER PIECE |
7/7. | [1] | 134112-2200 | COILED SPRING |
7/8. | [1] | 134115-0300 | GASKET |
7/13. | [1] | 139727-0200 | O-RING |
7/14. | [1] | 016560-2310 | O-RING |
10. | [1] | 026516-2040 | GASKET D19.9&16.2T1 |
11. | [1] | 134227-1200 | CAPSULE |
12. | [1] | 134227-1300 | CONTROL ROD |
13. | [1] | 134227-1400 | BEARING PLATE |
14. | [1] | 134227-0300 | BUSHING |
15. | [6] | 014160-6110 | CONICAL SPRING WASHER |
16. | [6] | 134227-0400 | BEARING PIN |
17. | [6] | 134227-0501 | FLAT-HEAD SCREW |
18. | [1] | 134227-2600 | CONNECTOR |
19. | [1] | 139005-0300 | HEX-SOCKET-HEAD CAP SCREW |
20. | [1] | 139320-0000 | PLAIN WASHER |
23/1. | [0] | 139400-0900 | SHIM T0.500 |
23/1. | [0] | 139400-1000 | SHIM T0.525 |
23/1. | [0] | 139400-1100 | SHIM T0.550 |
23/1. | [0] | 139400-1200 | SHIM T0.575 |
23/1. | [0] | 139400-1300 | SHIM T0.600 |
23/1. | [0] | 139400-1400 | SHIM T0.625 |
23/1. | [0] | 139400-1500 | SHIM T0.650 |
23/1. | [0] | 139400-1600 | SHIM T0.675 |
23/1. | [0] | 139400-1700 | SHIM T0.700 |
23/1. | [0] | 139400-1800 | SHIM T0.725 |
23/1. | [0] | 139400-1900 | SHIM T0.750 |
23/1. | [0] | 139400-2000 | SHIM T0.775 |
23/1. | [0] | 139400-2100 | SHIM T0.800 |
23/1. | [0] | 139400-2200 | SHIM T0.825 |
23/1. | [0] | 139400-2300 | SHIM T0.850 |
23/1. | [0] | 139400-2400 | SHIM T0.875 |
23/1. | [0] | 139400-2500 | SHIM T0.900 |
23/1. | [0] | 139400-2600 | SHIM T0.925 |
23/1. | [0] | 139400-2700 | SHIM T0.950 |
23/1. | [0] | 139400-2700 | SHIM T0.950 |
23/1. | [0] | 139400-2800 | SHIM T0.975 |
23/1. | [0] | 139400-2900 | SHIM T1.000 |
23/1. | [0] | 139400-3000 | SHIM T1.025 |
23/1. | [0] | 139400-3100 | SHIM T1.050 |
23/1. | [0] | 139400-3200 | SHIM T1.075 |
23/1. | [0] | 139400-3300 | SHIM T1.100 |
23/1. | [0] | 139400-3400 | SHIM T1.125 |
23/1. | [0] | 139400-3500 | SHIM T1.150 |
23/1. | [0] | 139400-3600 | SHIM T1.175 |
23/1. | [0] | 139400-3700 | SHIM T1.200 |
23/1. | [0] | 139400-3800 | SHIM T1.225 |
23/1. | [0] | 139400-3900 | SHIM T1.250 |
23/1. | [0] | 139400-4000 | SHIM T1.275 |
23/1. | [0] | 139400-4100 | SHIM T1.300 |
23/1. | [0] | 139400-4200 | SHIM T1.325 |
23/1. | [0] | 139400-4300 | SHIM T1.350 |
23/1. | [0] | 139400-4400 | SHIM T1.375 |
23/1. | [0] | 139400-4500 | SHIM T1.400 |
23/1. | [0] | 139400-4600 | SHIM T1.425 |
23/1. | [0] | 139400-4700 | SHIM T1.450 |
23/1. | [0] | 139400-4800 | SHIM T1.475 |
23/1. | [0] | 139400-4900 | SHIM T1.500 |
23/1. | [0] | 139400-5000 | SHIM T1.525 |
23/1. | [0] | 139400-5100 | SHIM T1.550 |
23/1. | [0] | 139400-5200 | SHIM T1.575 |
23/1. | [0] | 139400-5300 | SHIM T1.600 |
23/1. | [0] | 139400-5400 | SHIM T1.625 |
23/1. | [0] | 139400-5500 | SHIM T1.650 |
23/1. | [0] | 139400-5600 | SHIM T1.675 |
23/1. | [0] | 139400-5700 | SHIM T1.700 |
23/1. | [0] | 139400-5800 | SHIM T1.725 |
23/1. | [0] | 139400-5900 | SHIM T1.750 |
23/1. | [0] | 139400-6000 | SHIM T1.775 |
23/1. | [0] | 139400-6100 | SHIM T1.800 |
23/1. | [0] | 139400-6200 | SHIM T1.825 |
23/1. | [0] | 139400-6300 | SHIM T1.850 |
23/1. | [0] | 139400-6400 | SHIM T1.875 |
23/1. | [0] | 139400-6500 | SHIM T1.900 |
23/1. | [0] | 139400-6600 | SHIM T1.925 |
23/1. | [0] | 139400-6700 | SHIM T1.950 |
23/1. | [0] | 139400-6800 | SHIM T1.975 |
24. | [12] | 134132-0300 | PLAIN WASHER D20&11T2.5 |
26. | [12] | 139210-0200 | UNION NUT |
30. | [2] | 134001-0000 | BUSHING |
30. | [2] | 134001-0000 | BUSHING |
32. | [1] | 134256-4020 | CONTROL RACK |
33. | [1] | 024030-2030 | BEARING PIN |
34. | [1] | 134222-0000 | BUSHING |
41. | [6] | 134241-0620 | CONTROL SLEEVE |
43. | [6] | 134216-0100 | SLOTTED WASHER |
44. | [6] | 134215-0900 | COMPRESSION SPRING |
45. | [6] | 134217-0800 | SLOTTED WASHER |
46. | [6] | 134563-2800 | SPRING SEAT |
47. | [4] | 134200-1020 | TAPPET |
47/2. | [1] | 134204-0300 | ROLLER |
47/3. | [1] | 134203-0200 | BEARING PIN |
47/4. | [1] | 131206-0500 | SLIDER |
47/5. | [1] | 134208-0000 | LOCKING WASHER |
48. | [2] | 134200-0920 | TAPPET |
48/2. | [1] | 134204-0300 | ROLLER |
48/3. | [1] | 134203-0200 | BEARING PIN |
48/4. | [1] | 131206-0500 | SLIDER |
48/5. | [1] | 134208-0000 | LOCKING WASHER |
59. | [1] | 016650-2230 | BEARING PLATE |
64. | [1] | 134303-0500 | SHIM D59.8&43T1.6 |
67. | [4] | 139006-4200 | BLEEDER SCREW |
71. | [1] | 134377-0300 | CAMSHAFT |
74. | [1] | 134306-1300 | BEARING SHELL |
75. | [2] | 020106-2040 | BLEEDER SCREW M6P1L20 |
76. | [2] | 134306-1400 | BEARING SHELL |
77. | [4] | 020106-2040 | BLEEDER SCREW M6P1L20 |
79. | [1] | 035302-0600 | BEARING PLATE |
80. | [1] | 134316-3300 | COVER |
81. | [1] | 139634-0200 | PACKING RING |
82/1. | [0] | 134314-0700 | SHIM T0.1 |
82/1. | [0] | 134314-0800 | SHIM T0.12 |
82/1. | [0] | 134314-0900 | SHIM T0.14 |
82/1. | [0] | 134314-1000 | SHIM T0.16 |
82/1. | [0] | 134314-1100 | SHIM T0.18 |
82/1. | [0] | 134314-1200 | SHIM T0.3 |
82/1. | [0] | 134314-1300 | SHIM T0.5 |
83. | [1] | 139766-0000 | O-RING |
84. | [1] | 134563-2500 | SLIDING PIECE |
85. | [1] | 134043-0800 | COVER |
86. | [1] | 134042-1400 | GASKET |
87. | [12] | 134563-2900 | FLAT-HEAD SCREW |
88. | [1] | 134045-0100 | CAPSULE |
89. | [1] | 026524-2940 | GASKET D28.9&24.3T2 |
93. | [3] | 139206-0400 | UNION NUT |
95. | [1] | 131041-0800 | GASKET |
96. | [6] | 134047-0000 | CAPSULE |
98. | [1] | 025806-2210 | WOODRUFF KEY |
118. | [1] | 134496-4200 | POINTER |
119. | [2] | 029020-6210 | BLEEDER SCREW |
120/1. | [0] | 139400-0100 | SHIM T0.2 |
120/1. | [0] | 139400-0200 | SHIM T0.3 |
120/1. | [0] | 139400-0300 | SHIM T0.5 |
120/1. | [0] | 139400-0400 | SHIM T1.0 |
120/1. | [0] | 139400-7200 | SHIM T0.1 |
132. | [1] | 134430-3820 | EYE BOLT |
133. | [2] | 139516-0000 | GASKET |
142. | [1] | 139810-0700 | EYE BOLT |
143. | [3] | 139510-0100 | GASKET |
162. | [1] | 134424-1520 | OVER FLOW VALVE |
163. | [3] | 139514-0100 | GASKET |
Include in #1:
108622-3080
as FUEL INJECTION PUMP
Cross reference number
Zexel num
Bosch num
Firm num
Name
Information:
Test Procedure
System Operation
The SLC 5/04 diagnostic indicators are located on the front of the following components: Power Supply, CPU and I/O Modules.The diagnostic indicators help trace the source of the fault. Faults can be found in the following components: Input devices, Output devices, Wiring and The controller.The thermocouple module has five LED indicators. Four of the LED indicators are "Channel Status" indicators. The "Channel Status" indicators are numbered according to the channel. One of the LED indicators is a "Module Status" indicator.Diagnostics are displayed on the "Module Status" LED indicator. Operating errors are displayed on the "Module Status" LED indicator. Problems may be detected during powerup or problems may be detected during operation. When an error occurs, the module will not communicate with the processor. The channel is disabled and the data is cleared.
Illustration 1 g00563417
Diagram of the LED indicators
Illustration 2 g00563392
Diagram of the LED indicators
Illustration 3 g00563575
Diagram of the RTD module
Illustration 4 g00563579
Schematic of the RTD moduleFunctional Test
The "Module Status" LED is on. The module is operating normally. Stop.
The "Channel Status" LED is on. The module is operating normally. Stop.
The "Module Status" LED is off. The module is in a fault condition. Proceed to 6.
The "Channel Status" LED is off. The channel is not enabled. This is normal if the sensor is not wired.
The "Channel Status" LED is blinking. The module is in a fault condition. Proceed to 10.
Check the electrical connectors and check the wiring.
Bodily contact with electrical potential can cause bodily injury or death.To avoid the possibility of injury or death, ensure that the main power supply has been disconnected before performing any maintenance or removing any modules.
Disconnect the power supply.
Check the electrical connectors and check the wiring for damage or bad connections.
Verify that all modules are properly seated.
Verify the status of the LED on the SLC 5/04.The results of the preceding procedure are in the following list:
All of the components are fully installed. All of the components are free of corrosion. All of the components are free of damage. All of the modules are properly seated. Proceed to 7.
The components are not fully installed. The components are not free of corrosion. The components are damaged. All of the modules are not properly seated. Repair the component. Verify that the repair resolves the problem. STOP.
Check the LED indicator on the module.
Connect the power supply.
Cycle the power to the module.The results of the preceding procedure are in the following list:
No errors are displayed on the LED indicators. Stop.
Errors are displayed on the LED indicators. Proceed to 8.
Check the module for a fault.
Bodily contact with electrical potential can cause bodily injury or death.To avoid the possibility of injury or death, ensure that the main power supply has been disconnected before performing any maintenance or removing any modules.
To avoid potential damage to the processor, handle all modules by the ends of the carrier or edges of the plastic housing. Skin oil or dirt can corrode metallic surfaces, inhibiting electrical contact.
Disconnect the power supply.
Remove the module from the chassis.Reference: Maintenance Procedure, "Input Module
System Operation
The SLC 5/04 diagnostic indicators are located on the front of the following components: Power Supply, CPU and I/O Modules.The diagnostic indicators help trace the source of the fault. Faults can be found in the following components: Input devices, Output devices, Wiring and The controller.The thermocouple module has five LED indicators. Four of the LED indicators are "Channel Status" indicators. The "Channel Status" indicators are numbered according to the channel. One of the LED indicators is a "Module Status" indicator.Diagnostics are displayed on the "Module Status" LED indicator. Operating errors are displayed on the "Module Status" LED indicator. Problems may be detected during powerup or problems may be detected during operation. When an error occurs, the module will not communicate with the processor. The channel is disabled and the data is cleared.
Illustration 1 g00563417
Diagram of the LED indicators
Illustration 2 g00563392
Diagram of the LED indicators
Illustration 3 g00563575
Diagram of the RTD module
Illustration 4 g00563579
Schematic of the RTD moduleFunctional Test
The "Module Status" LED is on. The module is operating normally. Stop.
The "Channel Status" LED is on. The module is operating normally. Stop.
The "Module Status" LED is off. The module is in a fault condition. Proceed to 6.
The "Channel Status" LED is off. The channel is not enabled. This is normal if the sensor is not wired.
The "Channel Status" LED is blinking. The module is in a fault condition. Proceed to 10.
Check the electrical connectors and check the wiring.
Bodily contact with electrical potential can cause bodily injury or death.To avoid the possibility of injury or death, ensure that the main power supply has been disconnected before performing any maintenance or removing any modules.
Disconnect the power supply.
Check the electrical connectors and check the wiring for damage or bad connections.
Verify that all modules are properly seated.
Verify the status of the LED on the SLC 5/04.The results of the preceding procedure are in the following list:
All of the components are fully installed. All of the components are free of corrosion. All of the components are free of damage. All of the modules are properly seated. Proceed to 7.
The components are not fully installed. The components are not free of corrosion. The components are damaged. All of the modules are not properly seated. Repair the component. Verify that the repair resolves the problem. STOP.
Check the LED indicator on the module.
Connect the power supply.
Cycle the power to the module.The results of the preceding procedure are in the following list:
No errors are displayed on the LED indicators. Stop.
Errors are displayed on the LED indicators. Proceed to 8.
Check the module for a fault.
Bodily contact with electrical potential can cause bodily injury or death.To avoid the possibility of injury or death, ensure that the main power supply has been disconnected before performing any maintenance or removing any modules.
To avoid potential damage to the processor, handle all modules by the ends of the carrier or edges of the plastic housing. Skin oil or dirt can corrode metallic surfaces, inhibiting electrical contact.
Disconnect the power supply.
Remove the module from the chassis.Reference: Maintenance Procedure, "Input Module