Information fuel-injection pump
BOSCH
9 410 614 378
9410614378
ZEXEL
106096-9302
1060969302
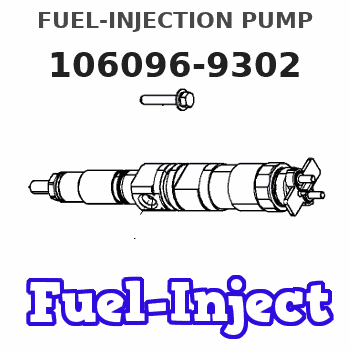
Rating:
Scheme ###:
1. | [1] | 134056-0020 | PUMP HOUSING |
1/30. | [3] | 029040-6020 | STUD |
1/45. | [1] | 134311-0000 | SPACER RING |
1/50. | [20] | 134138-0000 | STUD |
7. | [10] | 134143-2920 | PLUNGER-AND-BARREL ASSY |
7/1. | [10] | 134131-1020 | FLANGE BUSHING |
7/2. | [10] | 134101-9120 | PLUNGER-AND-BARREL ASSY |
7/3. | [10] | 134110-4220 | DELIVERY-VALVE ASSEMBLY |
7/4. | [10] | 134116-4400 | FITTING |
7/5. | [10] | 029632-2070 | O-RING |
7/6. | [10] | 131117-2100 | FILLER PIECE |
7/7. | [10] | 131112-2300 | COILED SPRING |
7/8. | [10] | 134115-0100 | GASKET |
7/9. | [10] | 029302-0140 | PLAIN WASHER |
7/10. | [10] | 134135-0200 | CAPSULE |
7/11. | [10] | 029602-0010 | LOCKING WASHER |
7/12. | [10] | 134137-0100 | SPACER RING |
7/13. | [10] | 029632-9030 | O-RING |
7/14. | [10] | 029631-5020 | O-RING |
7/15. | [10] | 029631-5020 | O-RING |
23/1. | [0] | 139400-0900 | SHIM T0.500 |
23/1. | [0] | 139400-0900 | SHIM T0.500 |
23/1. | [0] | 139400-1000 | SHIM T0.525 |
23/1. | [0] | 139400-1100 | SHIM T0.550 |
23/1. | [0] | 139400-1200 | SHIM T0.575 |
23/1. | [0] | 139400-1300 | SHIM T0.600 |
23/1. | [0] | 139400-1400 | SHIM T0.625 |
23/1. | [0] | 139400-1500 | SHIM T0.650 |
23/1. | [0] | 139400-1600 | SHIM T0.675 |
23/1. | [0] | 139400-1700 | SHIM T0.700 |
23/1. | [0] | 139400-1800 | SHIM T0.725 |
23/1. | [0] | 139400-1900 | SHIM T0.750 |
23/1. | [0] | 139400-2000 | SHIM T0.775 |
23/1. | [0] | 139400-2100 | SHIM T0.800 |
23/1. | [0] | 139400-2200 | SHIM T0.825 |
23/1. | [0] | 139400-2300 | SHIM T0.850 |
23/1. | [0] | 139400-2400 | SHIM T0.875 |
23/1. | [0] | 139400-2500 | SHIM T0.900 |
23/1. | [0] | 139400-2600 | SHIM T0.925 |
23/1. | [0] | 139400-2700 | SHIM T0.950 |
23/1. | [0] | 139400-2800 | SHIM T0.975 |
23/1. | [0] | 139400-2900 | SHIM T1.000 |
23/1. | [0] | 139400-3000 | SHIM T1.025 |
23/1. | [0] | 139400-3100 | SHIM T1.050 |
23/1. | [0] | 139400-3200 | SHIM T1.075 |
23/1. | [0] | 139400-3300 | SHIM T1.100 |
23/1. | [0] | 139400-3400 | SHIM T1.125 |
23/1. | [0] | 139400-3500 | SHIM T1.150 |
23/1. | [0] | 139400-3600 | SHIM T1.175 |
23/1. | [0] | 139400-3700 | SHIM T1.200 |
23/1. | [0] | 139400-3800 | SHIM T1.225 |
23/1. | [0] | 139400-3900 | SHIM T1.250 |
23/1. | [0] | 139400-4000 | SHIM T1.275 |
23/1. | [0] | 139400-4100 | SHIM T1.300 |
23/1. | [0] | 139400-4200 | SHIM T1.325 |
23/1. | [0] | 139400-4300 | SHIM T1.350 |
23/1. | [0] | 139400-4400 | SHIM T1.375 |
23/1. | [0] | 139400-4500 | SHIM T1.400 |
23/1. | [0] | 139400-4600 | SHIM T1.425 |
23/1. | [0] | 139400-4700 | SHIM T1.450 |
23/1. | [0] | 139400-4800 | SHIM T1.475 |
23/1. | [0] | 139400-4900 | SHIM T1.500 |
23/1. | [0] | 139400-5000 | SHIM T1.525 |
23/1. | [0] | 139400-5100 | SHIM T1.550 |
23/1. | [0] | 139400-5200 | SHIM T1.575 |
23/1. | [0] | 139400-5300 | SHIM T1.600 |
23/1. | [0] | 139400-5400 | SHIM T1.625 |
23/1. | [0] | 139400-5500 | SHIM T1.650 |
23/1. | [0] | 139400-5600 | SHIM T1.675 |
23/1. | [0] | 139400-5700 | SHIM T1.700 |
23/1. | [0] | 139400-5800 | SHIM T1.725 |
23/1. | [0] | 139400-5900 | SHIM T1.750 |
23/1. | [0] | 139400-6000 | SHIM T1.775 |
23/1. | [0] | 139400-6100 | SHIM T1.800 |
23/1. | [0] | 139400-6200 | SHIM T1.825 |
23/1. | [0] | 139400-6300 | SHIM T1.850 |
23/1. | [0] | 139400-6400 | SHIM T1.875 |
23/1. | [0] | 139400-6500 | SHIM T1.900 |
23/1. | [0] | 139400-6600 | SHIM T1.925 |
23/1. | [0] | 139400-6700 | SHIM T1.950 |
23/1. | [0] | 139400-6800 | SHIM T1.975 |
24. | [20] | 134132-0300 | PLAIN WASHER D20&11T2.5 |
26. | [20] | 013021-0040 | UNION NUT M10P1.5H8 |
30. | [2] | 134001-0000 | BUSHING |
30. | [2] | 134001-0000 | BUSHING |
32. | [1] | 134250-0000 | CONTROL RACK |
33. | [1] | 024030-2030 | BEARING PIN |
34. | [1] | 134222-0000 | BUSHING |
41. | [10] | 134241-0021 | CONTROL SLEEVE |
43. | [10] | 134216-0000 | SLOTTED WASHER |
44. | [10] | 134215-0400 | COMPRESSION SPRING |
45. | [10] | 134217-0500 | SLOTTED WASHER |
47. | [10] | 134200-0020 | TAPPET |
47/2. | [1] | 134204-0000 | ROLLER |
47/3. | [1] | 134205-0000 | BUSHING |
47/4. | [1] | 134203-0000 | BEARING PIN |
47/5. | [1] | 131206-0500 | SLIDER |
59. | [1] | 016650-2230 | BEARING PLATE |
64/1. | [0] | 134303-0000 | SHIM D59.8&43T1.2 |
64/1. | [0] | 134303-0100 | SHIM D59.8&43T1.5 |
64/1. | [0] | 134303-0200 | SHIM D59.8&43T1.8 |
64/1. | [0] | 134303-0300 | SHIM D59.8&43T2.0 |
64/1. | [0] | 134303-0400 | SHIM D59.8&43T0.6 |
67. | [4] | 134329-0000 | BLEEDER SCREW |
68. | [4] | 029320-6010 | LOCKING WASHER |
69. | [4] | 029300-6170 | SHIM D12&6.2T1 |
70. | [4] | 029340-6120 | GASKET |
71. | [1] | 134391-0600 | CAMSHAFT |
74. | [2] | 134306-0000 | BEARING SHELL |
75. | [4] | 020106-2040 | BLEEDER SCREW M6P1L20 |
79. | [1] | 016650-2230 | BEARING PLATE |
80. | [1] | 134316-2400 | COVER |
81. | [1] | 026712-5010 | PACKING RING |
82/1. | [0] | 134314-0000 | SHIM T0.1 |
82/1. | [0] | 134314-0100 | SHIM T0.12 |
82/1. | [0] | 134314-0200 | SHIM T0.14 |
82/1. | [0] | 134314-0300 | SHIM T0.16 |
82/1. | [0] | 134314-0400 | SHIM T0.18 |
82/1. | [0] | 134314-0500 | SHIM T0.3 |
82/1. | [0] | 134314-0600 | SHIM T0.5 |
83. | [1] | 029635-5010 | O-RING |
85. | [1] | 134043-1400 | COVER |
86. | [1] | 134042-1600 | GASKET |
87. | [16] | 012206-1640 | FLAT-HEAD SCREW M6P1L16 |
88. | [1] | 134045-0100 | CAPSULE |
89. | [1] | 026524-2940 | GASKET D28.9&24.3T2 |
93. | [3] | 139206-0400 | UNION NUT |
95. | [1] | 131041-0800 | GASKET |
96. | [10] | 134047-0000 | CAPSULE |
98. | [1] | 025805-1910 | WOODRUFF KEY |
147. | [1] | 139810-0000 | EYE BOLT |
148. | [2] | 139510-0000 | GASKET D15.2&10.2T1.0 |
157. | [1] | 134424-3520 | OVER FLOW VALVE |
158. | [2] | 139514-0000 | GASKET D19.2&14.2T1.0 |
158. | [2] | 139514-0000 | GASKET D19.2&14.2T1.0 |
167. | [1] | 134424-2720 | OVER FLOW VALVE |
168. | [3] | 139514-0000 | GASKET D19.2&14.2T1.0 |
180. | [1] | 134459-0320 | BRACKET |
180/2. | [4] | 029041-0300 | STUD |
181. | [1] | 139789-0100 | O-RING |
183. | [4] | 014011-0140 | PLAIN WASHER D22&10.5T1.6 |
184. | [4] | 014111-0440 | LOCKING WASHER |
185. | [4] | 013021-0040 | UNION NUT M10P1.5H8 |
186. | [1] | 139799-0500 | O-RING |
187. | [1] | 139926-0000 | CAPSULE |
188. | [1] | 026526-3140 | GASKET D30.9&26.3T2 |
225. | [1] | 131439-0300 | HANGER |
227. | [1] | 131329-0300 | BLEEDER SCREW |
228. | [1] | 131439-0300 | HANGER |
230. | [1] | 131329-0300 | BLEEDER SCREW |
263. | [1] | 134510-9720 | BRACKET |
264. | [1] | 134442-1020 | PIPE |
357. | [1] | 139814-1000 | EYE BOLT |
358. | [2] | 139514-0000 | GASKET D19.2&14.2T1.0 |
359. | [1] | 134442-2220 | CONNECTOR |
367. | [1] | 139814-1000 | EYE BOLT |
368. | [2] | 139514-0000 | GASKET D19.2&14.2T1.0 |
Cross reference number
Zexel num
Bosch num
Firm num
Name
Information:
Precautions for Electrical System
* Before working on the electrical system, disconnect the (-) battery cable to prevent short circuits.
* Make sure the electrical equipment is OFF before disconnecting or connecting battery cable. Semiconductor components may otherwise be damaged.
* Carefully handle sensors relays, and other items that are sensitive to shock and heat. * When applying a voltage to a part for inspection purposes, check that the (+) and (-) cables are connected properly then gradually increase the voltage from zero. Do not exceed the specified voltage. Remember that sensors do not necessarily operate on the battery voltage. * When separating connectors, grasp the connectors themselves rather than the harnesses. * To separate locking connectors, first push them in the direction of the arrows. To reconnect locking connectors, push them together until they click.* Before washing the parts, cover electrical parts to keep them dry. (Use plastic sheets or the like.) Keep water away from harness connectors and sensors and immediately wipe off any water that gets on them. Handling precautions for electric circuits
* Do not pierce wire insulation with test probes or alligator clips when performing electrical inspections. Doing so can, particularly with the chassis harness, hasten corrosion.
(1) Inspection of harnesses (1.1) Inspections with connectors fitted together* Waterproof connectors* Connect an inspection harness and connector. A between the connectors B of the circuit to be inspected. Perform the inspection by applying a test probe C to the connectors of the inspection harness. Do not insert the test probe C into the wire-entry sides of the waterproof connectors since this would damage their waterproof seals and lead to rust. * Non-waterproof connectors* Perform the inspection by inserting a test probe C into the wire-entry sides of the connectors. An extra-narrow probe is required for control unit connectors, which are smaller than other types of connector. Do not force a regular-size probe into control unit connectors since this would cause damage. (1.2) Inspections with connectors separated* Inspections on female terminals* Perform the inspection by carefully inserting a test probe into the terminals. Do not force the test probe into the terminals since this could deform them and cause poor connections. * Inspections on male terminals* Perform the inspection by applying test probes directly to the pins.
* Be careful not to short-circuit pins together with the test probes. With control unit connectors, short-circuiting of pins can cause damage to the control unit's internal circuitry.
* When using a multimeter to check continuity, do not allow the test probes to touch the wrong terminals. (2) Inspection of connectors (2.1) Visual inspection* Check that the connectors are fitted together securely. * Check whether wires have been separated from their terminals due to pulling of the harness. * Check that male and female terminals fit together tightly. * Check for defective connections caused by loose terminals, by rust on terminals, or by contamination of terminals by foreign substances. (2.2) Checking for loose terminals* If connector terminal retainers become damaged, male and female terminals may not
* Before working on the electrical system, disconnect the (-) battery cable to prevent short circuits.
* Make sure the electrical equipment is OFF before disconnecting or connecting battery cable. Semiconductor components may otherwise be damaged.
* Carefully handle sensors relays, and other items that are sensitive to shock and heat. * When applying a voltage to a part for inspection purposes, check that the (+) and (-) cables are connected properly then gradually increase the voltage from zero. Do not exceed the specified voltage. Remember that sensors do not necessarily operate on the battery voltage. * When separating connectors, grasp the connectors themselves rather than the harnesses. * To separate locking connectors, first push them in the direction of the arrows. To reconnect locking connectors, push them together until they click.* Before washing the parts, cover electrical parts to keep them dry. (Use plastic sheets or the like.) Keep water away from harness connectors and sensors and immediately wipe off any water that gets on them. Handling precautions for electric circuits
* Do not pierce wire insulation with test probes or alligator clips when performing electrical inspections. Doing so can, particularly with the chassis harness, hasten corrosion.
(1) Inspection of harnesses (1.1) Inspections with connectors fitted together* Waterproof connectors* Connect an inspection harness and connector. A between the connectors B of the circuit to be inspected. Perform the inspection by applying a test probe C to the connectors of the inspection harness. Do not insert the test probe C into the wire-entry sides of the waterproof connectors since this would damage their waterproof seals and lead to rust. * Non-waterproof connectors* Perform the inspection by inserting a test probe C into the wire-entry sides of the connectors. An extra-narrow probe is required for control unit connectors, which are smaller than other types of connector. Do not force a regular-size probe into control unit connectors since this would cause damage. (1.2) Inspections with connectors separated* Inspections on female terminals* Perform the inspection by carefully inserting a test probe into the terminals. Do not force the test probe into the terminals since this could deform them and cause poor connections. * Inspections on male terminals* Perform the inspection by applying test probes directly to the pins.
* Be careful not to short-circuit pins together with the test probes. With control unit connectors, short-circuiting of pins can cause damage to the control unit's internal circuitry.
* When using a multimeter to check continuity, do not allow the test probes to touch the wrong terminals. (2) Inspection of connectors (2.1) Visual inspection* Check that the connectors are fitted together securely. * Check whether wires have been separated from their terminals due to pulling of the harness. * Check that male and female terminals fit together tightly. * Check for defective connections caused by loose terminals, by rust on terminals, or by contamination of terminals by foreign substances. (2.2) Checking for loose terminals* If connector terminal retainers become damaged, male and female terminals may not