Information fuel-injection pump
BOSCH
9 410 611 752
9410611752
ZEXEL
106068-2621
1060682621
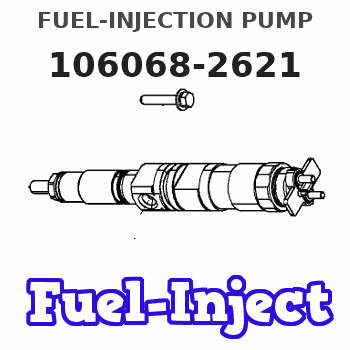
Rating:
Scheme ###:
1. | [1] | 134070-2420 | PUMP HOUSING |
1/3. | [1] | 131002-2700 | ADAPTOR |
1/8. | [1] | 131002-2700 | ADAPTOR |
1/11. | [1] | 134026-0000 | CAPSULE |
1/30. | [3] | 029040-6020 | STUD |
1/45. | [1] | 134311-0000 | SPACER RING |
1/50. | [12] | 134138-0100 | STUD |
7. | [6] | 134147-8220 | PLUNGER-AND-BARREL ASSY |
7/1. | [1] | 134173-1820 | PLUNGER-AND-BARREL ASSY |
7/3. | [1] | 134110-8020 | DELIVERY-VALVE ASSEMBLY |
7/4. | [1] | 134171-0120 | FITTING |
7/5. | [1] | 016500-1850 | O-RING |
7/6. | [1] | 134117-1700 | FILLER PIECE |
7/7. | [1] | 134112-2200 | COILED SPRING |
7/8. | [1] | 134115-0300 | GASKET |
7/10. | [1] | 134135-0300 | CAPSULE |
7/11. | [1] | 029602-0010 | LOCKING WASHER |
7/13. | [1] | 139727-0300 | O-RING |
7/14. | [1] | 139715-0300 | O-RING |
7/15. | [1] | 139715-0300 | O-RING |
23/1. | [0] | 139400-0900 | SHIM T0.500 |
23/1. | [0] | 139400-1000 | SHIM T0.525 |
23/1. | [0] | 139400-1100 | SHIM T0.550 |
23/1. | [0] | 139400-1200 | SHIM T0.575 |
23/1. | [0] | 139400-1300 | SHIM T0.600 |
23/1. | [0] | 139400-1400 | SHIM T0.625 |
23/1. | [0] | 139400-1500 | SHIM T0.650 |
23/1. | [0] | 139400-1600 | SHIM T0.675 |
23/1. | [0] | 139400-1700 | SHIM T0.700 |
23/1. | [0] | 139400-1800 | SHIM T0.725 |
23/1. | [0] | 139400-1900 | SHIM T0.750 |
23/1. | [0] | 139400-2000 | SHIM T0.775 |
23/1. | [0] | 139400-2100 | SHIM T0.800 |
23/1. | [0] | 139400-2200 | SHIM T0.825 |
23/1. | [0] | 139400-2300 | SHIM T0.850 |
23/1. | [0] | 139400-2400 | SHIM T0.875 |
23/1. | [0] | 139400-2500 | SHIM T0.900 |
23/1. | [0] | 139400-2600 | SHIM T0.925 |
23/1. | [0] | 139400-2700 | SHIM T0.950 |
23/1. | [0] | 139400-2800 | SHIM T0.975 |
23/1. | [0] | 139400-2900 | SHIM T1.000 |
23/1. | [0] | 139400-3000 | SHIM T1.025 |
23/1. | [0] | 139400-3100 | SHIM T1.050 |
23/1. | [0] | 139400-3200 | SHIM T1.075 |
23/1. | [0] | 139400-3300 | SHIM T1.100 |
23/1. | [0] | 139400-3400 | SHIM T1.125 |
23/1. | [0] | 139400-3500 | SHIM T1.150 |
23/1. | [0] | 139400-3600 | SHIM T1.175 |
23/1. | [0] | 139400-3700 | SHIM T1.200 |
23/1. | [0] | 139400-3800 | SHIM T1.225 |
23/1. | [0] | 139400-3900 | SHIM T1.250 |
23/1. | [0] | 139400-3900 | SHIM T1.250 |
23/1. | [0] | 139400-4000 | SHIM T1.275 |
23/1. | [0] | 139400-4100 | SHIM T1.300 |
23/1. | [0] | 139400-4200 | SHIM T1.325 |
23/1. | [0] | 139400-4300 | SHIM T1.350 |
23/1. | [0] | 139400-4400 | SHIM T1.375 |
23/1. | [0] | 139400-4500 | SHIM T1.400 |
23/1. | [0] | 139400-4600 | SHIM T1.425 |
23/1. | [0] | 139400-4700 | SHIM T1.450 |
23/1. | [0] | 139400-4800 | SHIM T1.475 |
23/1. | [0] | 139400-4900 | SHIM T1.500 |
23/1. | [0] | 139400-5000 | SHIM T1.525 |
23/1. | [0] | 139400-5100 | SHIM T1.550 |
23/1. | [0] | 139400-5200 | SHIM T1.575 |
23/1. | [0] | 139400-5300 | SHIM T1.600 |
23/1. | [0] | 139400-5400 | SHIM T1.625 |
23/1. | [0] | 139400-5500 | SHIM T1.650 |
23/1. | [0] | 139400-5600 | SHIM T1.675 |
23/1. | [0] | 139400-5700 | SHIM T1.700 |
23/1. | [0] | 139400-5800 | SHIM T1.725 |
23/1. | [0] | 139400-5900 | SHIM T1.750 |
23/1. | [0] | 139400-6000 | SHIM T1.775 |
23/1. | [0] | 139400-6100 | SHIM T1.800 |
23/1. | [0] | 139400-6200 | SHIM T1.825 |
23/1. | [0] | 139400-6300 | SHIM T1.850 |
23/1. | [0] | 139400-6400 | SHIM T1.875 |
23/1. | [0] | 139400-6500 | SHIM T1.900 |
23/1. | [0] | 139400-6600 | SHIM T1.925 |
23/1. | [0] | 139400-6700 | SHIM T1.950 |
23/1. | [0] | 139400-6800 | SHIM T1.975 |
24. | [12] | 134132-0300 | PLAIN WASHER D20&11T2.5 |
26. | [12] | 139210-0200 | UNION NUT |
30. | [2] | 134001-0400 | BUSHING |
30. | [2] | 134001-0400 | BUSHING |
32. | [1] | 134256-3700 | CONTROL RACK |
33. | [1] | 024030-2030 | BEARING PIN |
34. | [1] | 134222-0000 | BUSHING |
37. | [1] | 134510-6800 | GASKET |
38. | [1] | 134222-1300 | ADAPTOR |
39. | [4] | 014110-4440 | LOCKING WASHER |
40. | [4] | 012154-1440 | FLAT-HEAD SCREW M4P0.7L14 |
41. | [6] | 134241-0620 | CONTROL SLEEVE |
43. | [6] | 134216-0000 | SLOTTED WASHER |
44. | [6] | 134215-0800 | COMPRESSION SPRING |
45. | [6] | 134217-0700 | SLOTTED WASHER |
46. | [6] | 134563-2700 | SPRING SEAT |
47. | [4] | 134200-0820 | TAPPET |
47/2. | [1] | 134204-0200 | ROLLER |
47/3. | [1] | 134203-0000 | BEARING PIN |
47/4. | [1] | 131206-0500 | SLIDER |
48. | [2] | 134200-0720 | TAPPET |
48/2. | [1] | 134204-0200 | ROLLER |
48/3. | [1] | 134203-0000 | BEARING PIN |
48/4. | [1] | 131206-0500 | SLIDER |
59. | [1] | 016650-2230 | BEARING PLATE |
64. | [1] | 134303-0500 | SHIM D59.8&43T1.6 |
67. | [4] | 139006-4200 | BLEEDER SCREW |
71. | [1] | 134340-0100 | CAMSHAFT |
74. | [1] | 134306-1000 | BEARING SHELL |
75. | [2] | 020106-2040 | BLEEDER SCREW M6P1L20 |
76. | [2] | 134306-1100 | BEARING SHELL |
77. | [4] | 020106-2040 | BLEEDER SCREW M6P1L20 |
79. | [1] | 035302-0600 | BEARING PLATE |
80. | [1] | 134316-3300 | COVER |
81. | [1] | 139634-0200 | PACKING RING |
82/1. | [0] | 134314-0700 | SHIM T0.1 |
82/1. | [0] | 134314-0800 | SHIM T0.12 |
82/1. | [0] | 134314-0900 | SHIM T0.14 |
82/1. | [0] | 134314-1000 | SHIM T0.16 |
82/1. | [0] | 134314-1100 | SHIM T0.18 |
82/1. | [0] | 134314-1200 | SHIM T0.3 |
82/1. | [0] | 134314-1300 | SHIM T0.5 |
83. | [1] | 139766-0000 | O-RING |
84. | [1] | 134563-2500 | SLIDING PIECE |
85. | [1] | 134043-0800 | COVER |
86. | [1] | 134042-1400 | GASKET |
87. | [12] | 012206-1640 | FLAT-HEAD SCREW M6P1L16 |
88. | [1] | 134045-0100 | CAPSULE |
89. | [1] | 026524-2940 | GASKET D28.9&24.3T2 |
93. | [3] | 139206-0400 | UNION NUT |
95. | [1] | 131041-0800 | GASKET |
96. | [6] | 134047-0000 | CAPSULE |
98. | [1] | 025806-2210 | WOODRUFF KEY |
99. | [1] | 014112-0440 | LOCKING WASHER |
100. | [1] | 023012-0040 | UNION NUT M20P1.5H16 |
116. | [1] | 156637-5900 | COUPLING PLATE |
132. | [1] | 029731-4680 | EYE BOLT |
133. | [2] | 029341-4130 | GASKET D20&13.8T2* |
142. | [1] | 029731-0120 | EYE BOLT |
143. | [2] | 029341-0110 | GASKET |
152. | [1] | 131425-1620 | OVER FLOW VALVE |
153. | [2] | 029341-4130 | GASKET D20&13.8T2* |
162. | [1] | 029731-4680 | EYE BOLT |
163. | [2] | 029341-4130 | GASKET D20&13.8T2* |
208. | [1] | 134563-4000 | CONNECTOR |
209. | [2] | 010635-1040 | FLAT-HEAD SCREW M5P0.8L10 |
210. | [2] | 014110-5440 | LOCKING WASHER |
211. | [1] | 134563-4200 | COVER |
212. | [1] | 134563-4300 | CLAMPING BAND |
213. | [1] | 134563-3700 | CLAMPING BAND |
Cross reference number
Zexel num
Bosch num
Firm num
Name
Information:
Fuel System Information
Check the fuel level in the tank daily by observing the sight gauge, if equipped.
Fill the fuel tank at the end of each day of operation to drive out moist air and to prevent condensation. Maintain a fairly constant level in the tank (near the top) to avoid drawing moisture into the tank as the level decreases. Do not fill the tank to the top. Fuel expands as it gets warm and may overflow.Drain water and sediment from tank at the interval specified in the Maintenance Schedule.Do not fill fuel filters with fuel before installing them. Contaminated fuel will cause accelerated wear to fuel system parts.
Fuel Recommendations
Use only fuel as recommended in this section. The fuels recommended for use in Caterpillar engines are No.2-D diesel fuel and No.2 fuel oil, although No. 1 grades are acceptable. The following fuel specifications are some of the worldwide fuels which may meet the requirements. Caterpillar Diesel Engines are capable of burning a wide range of distillate fuels. The use of clean, stable blends of distillate fuel which meet the following requirements will provide quality engine service life. Sulfur
The percentage of sulfur in the fuel will affect the engine oil recommendations. Fuel sulfur is chemically changed during combustion to form both sulfurous and sulfuric acid. These acids chemically attack metal surfaces and cause corrosive wear.Certain additives used in lubricating oils contain alkaline compounds that are formulated to neutralize these acids. The measure of this reserve alkalinity in a lubricating oil is known as its Total Base Number (TBN). TBN values are essential to neutralize the acids from combustion gases and to minimize corrosive wear.Fuels containing 0.5% or less sulfur may be used with recommended crankcase oil drain intervals using API CF-4 performance oils. With sulfur above the 0.5% level, use API CF-4 performance oils with an ASTM D-2896 Total Base Number (TBN) of 10 times the fuel sulfur for normal oil drain intervals.Caterpillar recommends infrared analysis (in conjunction with wear metal analysis) of used oil in determining the effectiveness of oil TBN and acid neutralization. The Caterpillar dealer S O S program provides this information. Regular oil analysis (S O S) will provide information to monitor oil properties and engine wear metals to maintain successful engine protection and establish oil drain intervals.Periodically request fuel sulfur content information from your fuel supplier. Fuel sulfur content can change with each bulk delivery. ASTM D-2896 can normally be found at your local technological society, library or college. Any American Petroleum Institute (API) classification performance oil should have sufficient TBN for fuels with less than 0.5% sulfur. Fuels containing 0.5% or less sulfur may be used with recommended crankcase oil drain intervals using API CF-4 performance oils.Additives
Fuel additives are generally not recommended nor needed for the specified fuels listed. Cetane improvers can be used as necessary for the direct injection engine requirements. Biocides may be needed to eliminate microorganism growth in storage tanks. In cold conditions, treatment for entrained water may also
Check the fuel level in the tank daily by observing the sight gauge, if equipped.
Fill the fuel tank at the end of each day of operation to drive out moist air and to prevent condensation. Maintain a fairly constant level in the tank (near the top) to avoid drawing moisture into the tank as the level decreases. Do not fill the tank to the top. Fuel expands as it gets warm and may overflow.Drain water and sediment from tank at the interval specified in the Maintenance Schedule.Do not fill fuel filters with fuel before installing them. Contaminated fuel will cause accelerated wear to fuel system parts.
Fuel Recommendations
Use only fuel as recommended in this section. The fuels recommended for use in Caterpillar engines are No.2-D diesel fuel and No.2 fuel oil, although No. 1 grades are acceptable. The following fuel specifications are some of the worldwide fuels which may meet the requirements. Caterpillar Diesel Engines are capable of burning a wide range of distillate fuels. The use of clean, stable blends of distillate fuel which meet the following requirements will provide quality engine service life. Sulfur
The percentage of sulfur in the fuel will affect the engine oil recommendations. Fuel sulfur is chemically changed during combustion to form both sulfurous and sulfuric acid. These acids chemically attack metal surfaces and cause corrosive wear.Certain additives used in lubricating oils contain alkaline compounds that are formulated to neutralize these acids. The measure of this reserve alkalinity in a lubricating oil is known as its Total Base Number (TBN). TBN values are essential to neutralize the acids from combustion gases and to minimize corrosive wear.Fuels containing 0.5% or less sulfur may be used with recommended crankcase oil drain intervals using API CF-4 performance oils. With sulfur above the 0.5% level, use API CF-4 performance oils with an ASTM D-2896 Total Base Number (TBN) of 10 times the fuel sulfur for normal oil drain intervals.Caterpillar recommends infrared analysis (in conjunction with wear metal analysis) of used oil in determining the effectiveness of oil TBN and acid neutralization. The Caterpillar dealer S O S program provides this information. Regular oil analysis (S O S) will provide information to monitor oil properties and engine wear metals to maintain successful engine protection and establish oil drain intervals.Periodically request fuel sulfur content information from your fuel supplier. Fuel sulfur content can change with each bulk delivery. ASTM D-2896 can normally be found at your local technological society, library or college. Any American Petroleum Institute (API) classification performance oil should have sufficient TBN for fuels with less than 0.5% sulfur. Fuels containing 0.5% or less sulfur may be used with recommended crankcase oil drain intervals using API CF-4 performance oils.Additives
Fuel additives are generally not recommended nor needed for the specified fuels listed. Cetane improvers can be used as necessary for the direct injection engine requirements. Biocides may be needed to eliminate microorganism growth in storage tanks. In cold conditions, treatment for entrained water may also