Information fuel-injection pump
BOSCH
9 410 610 542
9410610542
ZEXEL
106068-2552
1060682552
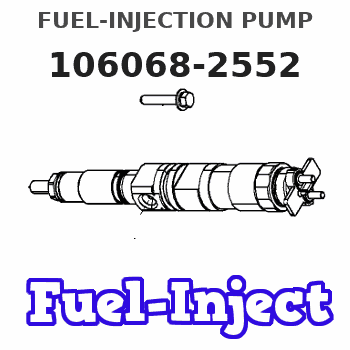
Rating:
Scheme ###:
1. | [1] | 134070-0720 | PUMP HOUSING |
1/2. | [1] | 131400-0100 | ADAPTOR |
1/3. | [1] | 131400-0100 | ADAPTOR |
1/11. | [1] | 134419-0000 | ADAPTOR |
1/30. | [3] | 029040-6020 | STUD |
1/45. | [1] | 134311-0000 | SPACER RING |
1/50. | [12] | 134138-0100 | STUD |
7. | [4] | 134147-6420 | PLUNGER-AND-BARREL ASSY |
7/1. | [1] | 134173-2520 | PLUNGER-AND-BARREL ASSY |
7/3. | [1] | 134160-5720 | DELIVERY-VALVE ASSEMBLY |
7/4. | [1] | 134171-0320 | FITTING |
7/5. | [1] | 016500-1850 | O-RING |
7/6. | [1] | 134117-1700 | FILLER PIECE |
7/7. | [1] | 134112-2200 | COILED SPRING |
7/8. | [1] | 134115-0300 | GASKET |
7/10. | [1] | 134135-0300 | CAPSULE |
7/11. | [1] | 029602-0010 | LOCKING WASHER |
7/13. | [1] | 139727-0300 | O-RING |
7/14. | [1] | 139715-0200 | O-RING |
7/15. | [1] | 139715-0200 | O-RING |
7B. | [2] | 134147-6520 | PLUNGER-AND-BARREL ASSY |
7B/1. | [1] | 134173-2620 | PLUNGER-AND-BARREL ASSY |
7B/3. | [1] | 134160-5720 | DELIVERY-VALVE ASSEMBLY |
7B/4. | [1] | 134171-0320 | FITTING |
7B/5. | [1] | 016500-1850 | O-RING |
7B/6. | [1] | 134117-1700 | FILLER PIECE |
7B/7. | [1] | 134112-2200 | COILED SPRING |
7B/8. | [1] | 134115-0300 | GASKET |
7B/10. | [1] | 134135-0300 | CAPSULE |
7B/11. | [1] | 029602-0010 | LOCKING WASHER |
7B/13. | [1] | 139727-0300 | O-RING |
7B/14. | [1] | 139715-0200 | O-RING |
7B/15. | [1] | 139715-0200 | O-RING |
23/1. | [0] | 139400-0900 | SHIM T0.500 |
23/1. | [0] | 139400-1000 | SHIM T0.525 |
23/1. | [0] | 139400-1100 | SHIM T0.550 |
23/1. | [0] | 139400-1200 | SHIM T0.575 |
23/1. | [0] | 139400-1300 | SHIM T0.600 |
23/1. | [0] | 139400-1400 | SHIM T0.625 |
23/1. | [0] | 139400-1400 | SHIM T0.625 |
23/1. | [0] | 139400-1500 | SHIM T0.650 |
23/1. | [0] | 139400-1600 | SHIM T0.675 |
23/1. | [0] | 139400-1700 | SHIM T0.700 |
23/1. | [0] | 139400-1800 | SHIM T0.725 |
23/1. | [0] | 139400-1900 | SHIM T0.750 |
23/1. | [0] | 139400-2000 | SHIM T0.775 |
23/1. | [0] | 139400-2100 | SHIM T0.800 |
23/1. | [0] | 139400-2200 | SHIM T0.825 |
23/1. | [0] | 139400-2300 | SHIM T0.850 |
23/1. | [0] | 139400-2400 | SHIM T0.875 |
23/1. | [0] | 139400-2500 | SHIM T0.900 |
23/1. | [0] | 139400-2600 | SHIM T0.925 |
23/1. | [0] | 139400-2700 | SHIM T0.950 |
23/1. | [0] | 139400-2800 | SHIM T0.975 |
23/1. | [0] | 139400-2900 | SHIM T1.000 |
23/1. | [0] | 139400-3000 | SHIM T1.025 |
23/1. | [0] | 139400-3100 | SHIM T1.050 |
23/1. | [0] | 139400-3200 | SHIM T1.075 |
23/1. | [0] | 139400-3300 | SHIM T1.100 |
23/1. | [0] | 139400-3400 | SHIM T1.125 |
23/1. | [0] | 139400-3500 | SHIM T1.150 |
23/1. | [0] | 139400-3600 | SHIM T1.175 |
23/1. | [0] | 139400-3700 | SHIM T1.200 |
23/1. | [0] | 139400-3800 | SHIM T1.225 |
23/1. | [0] | 139400-3900 | SHIM T1.250 |
23/1. | [0] | 139400-4000 | SHIM T1.275 |
23/1. | [0] | 139400-4100 | SHIM T1.300 |
23/1. | [0] | 139400-4200 | SHIM T1.325 |
23/1. | [0] | 139400-4300 | SHIM T1.350 |
23/1. | [0] | 139400-4400 | SHIM T1.375 |
23/1. | [0] | 139400-4500 | SHIM T1.400 |
23/1. | [0] | 139400-4600 | SHIM T1.425 |
23/1. | [0] | 139400-4700 | SHIM T1.450 |
23/1. | [0] | 139400-4800 | SHIM T1.475 |
23/1. | [0] | 139400-4900 | SHIM T1.500 |
23/1. | [0] | 139400-5000 | SHIM T1.525 |
23/1. | [0] | 139400-5100 | SHIM T1.550 |
23/1. | [0] | 139400-5200 | SHIM T1.575 |
23/1. | [0] | 139400-5300 | SHIM T1.600 |
23/1. | [0] | 139400-5400 | SHIM T1.625 |
23/1. | [0] | 139400-5500 | SHIM T1.650 |
23/1. | [0] | 139400-5600 | SHIM T1.675 |
23/1. | [0] | 139400-5700 | SHIM T1.700 |
23/1. | [0] | 139400-5800 | SHIM T1.725 |
23/1. | [0] | 139400-5900 | SHIM T1.750 |
23/1. | [0] | 139400-6000 | SHIM T1.775 |
23/1. | [0] | 139400-6100 | SHIM T1.800 |
23/1. | [0] | 139400-6200 | SHIM T1.825 |
23/1. | [0] | 139400-6300 | SHIM T1.850 |
23/1. | [0] | 139400-6400 | SHIM T1.875 |
23/1. | [0] | 139400-6500 | SHIM T1.900 |
23/1. | [0] | 139400-6600 | SHIM T1.925 |
23/1. | [0] | 139400-6700 | SHIM T1.950 |
23/1. | [0] | 139400-6800 | SHIM T1.975 |
24. | [12] | 134132-0300 | PLAIN WASHER D20&11T2.5 |
26. | [12] | 139210-0200 | UNION NUT |
30. | [2] | 134001-0000 | BUSHING |
30. | [2] | 134001-0000 | BUSHING |
32. | [1] | 134256-0000 | CONTROL RACK |
33. | [1] | 024030-2030 | BEARING PIN |
34. | [1] | 134222-0000 | BUSHING |
41. | [6] | 134241-0620 | CONTROL SLEEVE |
43. | [6] | 134216-0000 | SLOTTED WASHER |
44. | [6] | 134215-0800 | COMPRESSION SPRING |
45. | [6] | 134217-0700 | SLOTTED WASHER |
45. | [6] | 134217-0700 | SLOTTED WASHER |
46. | [6] | 134563-2700 | SPRING SEAT |
47. | [4] | 134200-0820 | TAPPET |
47/2. | [1] | 134204-0200 | ROLLER |
47/3. | [1] | 134203-0000 | BEARING PIN |
47/4. | [1] | 131206-0500 | SLIDER |
48. | [2] | 134200-0720 | TAPPET |
48/2. | [1] | 134204-0200 | ROLLER |
48/3. | [1] | 134203-0000 | BEARING PIN |
48/4. | [1] | 131206-0500 | SLIDER |
59. | [1] | 016650-2230 | BEARING PLATE |
64. | [1] | 134303-0500 | SHIM D59.8&43T1.6 |
67. | [4] | 139006-4200 | BLEEDER SCREW |
71. | [1] | 134340-1300 | CAMSHAFT |
74. | [1] | 134306-1000 | BEARING SHELL |
75. | [2] | 020106-2040 | BLEEDER SCREW M6P1L20 |
76. | [2] | 134306-1100 | BEARING SHELL |
77. | [4] | 020106-2040 | BLEEDER SCREW M6P1L20 |
79. | [1] | 035302-0600 | BEARING PLATE |
80. | [1] | 134316-3300 | COVER |
81. | [1] | 139634-0400 | PACKING RING |
82/1. | [0] | 134314-0700 | SHIM T0.1 |
82/1. | [0] | 134314-0800 | SHIM T0.12 |
82/1. | [0] | 134314-0900 | SHIM T0.14 |
82/1. | [0] | 134314-1000 | SHIM T0.16 |
82/1. | [0] | 134314-1100 | SHIM T0.18 |
82/1. | [0] | 134314-1200 | SHIM T0.3 |
82/1. | [0] | 134314-1300 | SHIM T0.5 |
83. | [1] | 139766-0200 | O-RING |
84. | [1] | 134563-2500 | SLIDING PIECE |
85. | [1] | 134043-0800 | COVER |
86. | [1] | 134042-1400 | GASKET |
87. | [12] | 012206-1640 | FLAT-HEAD SCREW M6P1L16 |
88. | [1] | 134045-0100 | CAPSULE |
89. | [1] | 026524-2940 | GASKET D28.9&24.3T2 |
93. | [3] | 139206-0400 | UNION NUT |
95. | [1] | 131041-0800 | GASKET |
96. | [6] | 134047-0000 | CAPSULE |
98. | [1] | 025806-2210 | WOODRUFF KEY |
118. | [1] | 134496-3400 | POINTER |
119. | [2] | 020006-1240 | BLEEDER SCREW M6P1L12 4T |
132. | [1] | 029731-4680 | EYE BOLT |
133. | [2] | 029341-4130 | GASKET D20&13.8T2* |
141. | [1] | 134433-4820 | PIPE |
142. | [1] | 029731-0490 | EYE BOLT |
143. | [3] | 029341-0110 | GASKET |
152. | [1] | 131424-3420 | OVER FLOW VALVE |
153. | [2] | 029341-4130 | GASKET D20&13.8T2* |
162. | [1] | 029731-4570 | EYE BOLT |
163. | [2] | 029341-4130 | GASKET D20&13.8T2* |
172. | [1] | 131420-0400 | BLEEDER SCREW |
173. | [1] | 026506-1040 | GASKET D9.9&6.2T1 |
186. | [1] | 134510-8220 | BRACKET |
Cross reference number
Zexel num
Bosch num
Firm num
Name
Information:
Cleaning Air Filter Elements
The primary element (Caterpillar air filters) can be cleaned several times before replacement. The element, when cleaned, should be thoroughly checked for rips or tears in the filter material.Replace the primary element at least every year regardless of the number of operating hours the element has accumulated.
Do not clean filter elements by bumping or tapping.Do not use filter elements with damaged pleats, gaskets or seals. Engine damage could result.
Filter elements can be cleaned with air pressure, 205 kPa (30 psi) maximum, or water pressure, 280 kPa (40 psi) maximum, or detergent washing. Have spare elements on hand to use while cleaning used elements.* Direct air or water along the length of the pleats inside and outside of filter element. The element can be washed in warm water and nonsudsing household detergent, such as automatic dishwasher detergent. Rinse inside and outside the pleats. The filter should then be thoroughly air dried and inspected. * Inspect the filter elements after cleaning for any rips, tears or damage. Insert a light inside of the clean, dry element. Do not use a filter element with damaged pleats, gaskets or seals. Discard the element if damaged. * Wrap and store the clean filter elements in a clean, dry place.For more information on air cleaner element cleaning, refer to SEBF8062, Guideline for Reusable Parts-Cleaning and Inspection of Air Filters.Belts
Check/Adjust
Inspect the condition and adjustment of alternator and accessory drive belts. Examine all drive belts for wear and replace if they show any signs of wear. Loose or worn pulley grooves cause belt slippage and low accessory drive speed. If belts are too loose, they vibrate enough to cause unnecessary wear on the belts and pulleys and possibly slip enough to cause overheating.If belts are too tight, unnecessary stresses are placed upon the pulley bearings and belts which might shorten the life of both.If one belt in a set requires replacement, always install a new matched set of belts. Never replace just the worn belt. If only the worn belt is replaced, the new belt will carry all the load, as it will not be stretched as much as the older belts. All the belts will fail in rapid succession.Remove the belt guard. Inspect the condition and adjustment of alternator belts and accessory drive belts (if equipped).To check the belt tension, apply 110 Newton (25 lb) force, perpendicular to the belt, midway between the driving and driven pulley. Measure the belt deflection. Correctly adjusted belts will deflect 15 to 20 mm (9/16 to 7/8 inch).If the belt does not require replacement or adjustment, install the belt guard. If the belt requires adjustment or replacement, perform the following procedure to adjust the belt tension.
Typical belt assembly mounting bolt (1) and adjusting nuts (2).1. Loosen the mounting bolt (1) and the locknut on the adjusting bolt.2. Turn the adjusting nuts (2) to increase or decrease the belt tension.3. Tighten the adjusting bolt locknut. Tighten the mounting bolts. Refer to the Torque Specifications in
The primary element (Caterpillar air filters) can be cleaned several times before replacement. The element, when cleaned, should be thoroughly checked for rips or tears in the filter material.Replace the primary element at least every year regardless of the number of operating hours the element has accumulated.
Do not clean filter elements by bumping or tapping.Do not use filter elements with damaged pleats, gaskets or seals. Engine damage could result.
Filter elements can be cleaned with air pressure, 205 kPa (30 psi) maximum, or water pressure, 280 kPa (40 psi) maximum, or detergent washing. Have spare elements on hand to use while cleaning used elements.* Direct air or water along the length of the pleats inside and outside of filter element. The element can be washed in warm water and nonsudsing household detergent, such as automatic dishwasher detergent. Rinse inside and outside the pleats. The filter should then be thoroughly air dried and inspected. * Inspect the filter elements after cleaning for any rips, tears or damage. Insert a light inside of the clean, dry element. Do not use a filter element with damaged pleats, gaskets or seals. Discard the element if damaged. * Wrap and store the clean filter elements in a clean, dry place.For more information on air cleaner element cleaning, refer to SEBF8062, Guideline for Reusable Parts-Cleaning and Inspection of Air Filters.Belts
Check/Adjust
Inspect the condition and adjustment of alternator and accessory drive belts. Examine all drive belts for wear and replace if they show any signs of wear. Loose or worn pulley grooves cause belt slippage and low accessory drive speed. If belts are too loose, they vibrate enough to cause unnecessary wear on the belts and pulleys and possibly slip enough to cause overheating.If belts are too tight, unnecessary stresses are placed upon the pulley bearings and belts which might shorten the life of both.If one belt in a set requires replacement, always install a new matched set of belts. Never replace just the worn belt. If only the worn belt is replaced, the new belt will carry all the load, as it will not be stretched as much as the older belts. All the belts will fail in rapid succession.Remove the belt guard. Inspect the condition and adjustment of alternator belts and accessory drive belts (if equipped).To check the belt tension, apply 110 Newton (25 lb) force, perpendicular to the belt, midway between the driving and driven pulley. Measure the belt deflection. Correctly adjusted belts will deflect 15 to 20 mm (9/16 to 7/8 inch).If the belt does not require replacement or adjustment, install the belt guard. If the belt requires adjustment or replacement, perform the following procedure to adjust the belt tension.
Typical belt assembly mounting bolt (1) and adjusting nuts (2).1. Loosen the mounting bolt (1) and the locknut on the adjusting bolt.2. Turn the adjusting nuts (2) to increase or decrease the belt tension.3. Tighten the adjusting bolt locknut. Tighten the mounting bolts. Refer to the Torque Specifications in