Information fuel-injection pump
BOSCH
9 410 613 669
9410613669
ZEXEL
106067-7632
1060677632
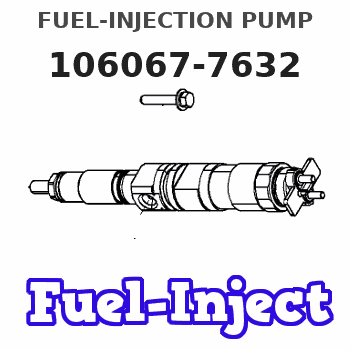
Rating:
Scheme ###:
1. | [1] | 134051-0520 | PUMP HOUSING |
1/30. | [3] | 029040-6020 | STUD |
1/45. | [1] | 134311-0000 | SPACER RING |
1/50. | [12] | 134138-0000 | STUD |
7. | [6] | 134145-2920 | PLUNGER-AND-BARREL ASSY |
7/1. | [1] | 134131-1020 | FLANGE BUSHING |
7/2. | [1] | 134101-7320 | PLUNGER-AND-BARREL ASSY |
7/3. | [1] | 134110-4820 | DELIVERY-VALVE ASSEMBLY |
7/4. | [1] | 134116-2820 | FITTING |
7/5. | [1] | 029632-2070 | O-RING |
7/6. | [1] | 134117-0500 | FILLER PIECE |
7/7. | [1] | 134112-1600 | COILED SPRING |
7/8. | [1] | 134115-0100 | GASKET |
7/9. | [1] | 029302-0140 | PLAIN WASHER |
7/10. | [1] | 134135-0200 | CAPSULE |
7/11. | [1] | 029602-0010 | LOCKING WASHER |
7/12. | [1] | 134137-0100 | SPACER RING |
7/13. | [1] | 029632-9030 | O-RING |
7/14. | [1] | 029631-5020 | O-RING |
7/15. | [1] | 029631-5020 | O-RING |
23/1. | [0] | 139400-0900 | SHIM T0.500 |
23/1. | [0] | 139400-1000 | SHIM T0.525 |
23/1. | [0] | 139400-1100 | SHIM T0.550 |
23/1. | [0] | 139400-1200 | SHIM T0.575 |
23/1. | [0] | 139400-1300 | SHIM T0.600 |
23/1. | [0] | 139400-1400 | SHIM T0.625 |
23/1. | [0] | 139400-1500 | SHIM T0.650 |
23/1. | [0] | 139400-1600 | SHIM T0.675 |
23/1. | [0] | 139400-1700 | SHIM T0.700 |
23/1. | [0] | 139400-1800 | SHIM T0.725 |
23/1. | [0] | 139400-1900 | SHIM T0.750 |
23/1. | [0] | 139400-2000 | SHIM T0.775 |
23/1. | [0] | 139400-2100 | SHIM T0.800 |
23/1. | [0] | 139400-2200 | SHIM T0.825 |
23/1. | [0] | 139400-2300 | SHIM T0.850 |
23/1. | [0] | 139400-2400 | SHIM T0.875 |
23/1. | [0] | 139400-2500 | SHIM T0.900 |
23/1. | [0] | 139400-2600 | SHIM T0.925 |
23/1. | [0] | 139400-2700 | SHIM T0.950 |
23/1. | [0] | 139400-2800 | SHIM T0.975 |
23/1. | [0] | 139400-2900 | SHIM T1.000 |
23/1. | [0] | 139400-3000 | SHIM T1.025 |
23/1. | [0] | 139400-3100 | SHIM T1.050 |
23/1. | [0] | 139400-3200 | SHIM T1.075 |
23/1. | [0] | 139400-3300 | SHIM T1.100 |
23/1. | [0] | 139400-3400 | SHIM T1.125 |
23/1. | [0] | 139400-3500 | SHIM T1.150 |
23/1. | [0] | 139400-3600 | SHIM T1.175 |
23/1. | [0] | 139400-3700 | SHIM T1.200 |
23/1. | [0] | 139400-3800 | SHIM T1.225 |
23/1. | [0] | 139400-3900 | SHIM T1.250 |
23/1. | [0] | 139400-4000 | SHIM T1.275 |
23/1. | [0] | 139400-4100 | SHIM T1.300 |
23/1. | [0] | 139400-4200 | SHIM T1.325 |
23/1. | [0] | 139400-4300 | SHIM T1.350 |
23/1. | [0] | 139400-4400 | SHIM T1.375 |
23/1. | [0] | 139400-4500 | SHIM T1.400 |
23/1. | [0] | 139400-4600 | SHIM T1.425 |
23/1. | [0] | 139400-4700 | SHIM T1.450 |
23/1. | [0] | 139400-4800 | SHIM T1.475 |
23/1. | [0] | 139400-4900 | SHIM T1.500 |
23/1. | [0] | 139400-5000 | SHIM T1.525 |
23/1. | [0] | 139400-5100 | SHIM T1.550 |
23/1. | [0] | 139400-5200 | SHIM T1.575 |
23/1. | [0] | 139400-5300 | SHIM T1.600 |
23/1. | [0] | 139400-5400 | SHIM T1.625 |
23/1. | [0] | 139400-5500 | SHIM T1.650 |
23/1. | [0] | 139400-5600 | SHIM T1.675 |
23/1. | [0] | 139400-5700 | SHIM T1.700 |
23/1. | [0] | 139400-5800 | SHIM T1.725 |
23/1. | [0] | 139400-5900 | SHIM T1.750 |
23/1. | [0] | 139400-6000 | SHIM T1.775 |
23/1. | [0] | 139400-6100 | SHIM T1.800 |
23/1. | [0] | 139400-6200 | SHIM T1.825 |
23/1. | [0] | 139400-6300 | SHIM T1.850 |
23/1. | [0] | 139400-6300 | SHIM T1.850 |
23/1. | [0] | 139400-6400 | SHIM T1.875 |
23/1. | [0] | 139400-6500 | SHIM T1.900 |
23/1. | [0] | 139400-6600 | SHIM T1.925 |
23/1. | [0] | 139400-6700 | SHIM T1.950 |
23/1. | [0] | 139400-6800 | SHIM T1.975 |
24. | [12] | 134132-0300 | PLAIN WASHER D20&11T2.5 |
26. | [12] | 013021-0040 | UNION NUT M10P1.5H8 |
30. | [2] | 134001-0000 | BUSHING |
30. | [2] | 134001-0000 | BUSHING |
32. | [1] | 134256-4500 | CONTROL RACK |
33. | [1] | 024030-2030 | BEARING PIN |
34. | [1] | 134222-0000 | BUSHING |
41. | [6] | 134241-0021 | CONTROL SLEEVE |
43. | [6] | 134216-0000 | SLOTTED WASHER |
44. | [6] | 134215-0400 | COMPRESSION SPRING |
45. | [6] | 134217-0500 | SLOTTED WASHER |
47. | [6] | 134200-0020 | TAPPET |
47/2. | [1] | 134204-0000 | ROLLER |
47/3. | [1] | 134205-0000 | BUSHING |
47/4. | [1] | 134203-0000 | BEARING PIN |
47/5. | [1] | 131206-0500 | SLIDER |
59. | [1] | 016650-2230 | BEARING PLATE |
59B. | [1] | 028222-5010 | BEARING PLATE |
64/1. | [0] | 134303-0000 | SHIM D59.8&43T1.2 |
64/1. | [0] | 134303-0100 | SHIM D59.8&43T1.5 |
64/1. | [0] | 134303-0200 | SHIM D59.8&43T1.8 |
64/1. | [0] | 134303-0300 | SHIM D59.8&43T2.0 |
64/1. | [0] | 134303-0400 | SHIM D59.8&43T0.6 |
67. | [4] | 029010-6810 | BLEEDER SCREW |
71. | [1] | 134371-1500 | CAMSHAFT |
74. | [1] | 134306-0100 | BEARING SHELL |
75. | [2] | 020106-2040 | BLEEDER SCREW M6P1L20 |
79. | [1] | 016650-2230 | BEARING PLATE |
79B. | [1] | 028222-5010 | BEARING PLATE |
80. | [1] | 134316-0600 | COVER |
81. | [1] | 026712-5010 | PACKING RING |
82/1. | [0] | 134314-0000 | SHIM T0.1 |
82/1. | [0] | 134314-0100 | SHIM T0.12 |
82/1. | [0] | 134314-0200 | SHIM T0.14 |
82/1. | [0] | 134314-0300 | SHIM T0.16 |
82/1. | [0] | 134314-0400 | SHIM T0.18 |
82/1. | [0] | 134314-0500 | SHIM T0.3 |
82/1. | [0] | 134314-0600 | SHIM T0.5 |
83. | [1] | 029635-5010 | O-RING |
85. | [1] | 134043-0800 | COVER |
86. | [1] | 134042-1400 | GASKET |
87. | [12] | 012206-1640 | FLAT-HEAD SCREW M6P1L16 |
88. | [1] | 134045-0100 | CAPSULE |
89. | [1] | 026524-2940 | GASKET D28.9&24.3T2 |
93. | [3] | 139206-0400 | UNION NUT |
95. | [1] | 131041-0800 | GASKET |
96. | [6] | 134047-0000 | CAPSULE |
98. | [1] | 025805-1910 | WOODRUFF KEY |
118. | [1] | 134496-1000 | POINTER |
119. | [2] | 020006-1240 | BLEEDER SCREW M6P1L12 4T |
132. | [1] | 029731-4680 | EYE BOLT |
133. | [2] | 029341-4130 | GASKET D20&13.8T2* |
141. | [1] | 134433-5620 | PIPE |
142. | [1] | 029731-0490 | EYE BOLT |
143. | [3] | 029341-0110 | GASKET |
152. | [1] | 133424-0221 | OVER FLOW VALVE |
153. | [2] | 029341-4130 | GASKET D20&13.8T2* |
162. | [1] | 029731-4570 | EYE BOLT |
163. | [2] | 029341-4130 | GASKET D20&13.8T2* |
172. | [1] | 131420-0400 | BLEEDER SCREW |
173. | [1] | 026506-1040 | GASKET D9.9&6.2T1 |
186. | [1] | 134510-8220 | BRACKET |
187. | [1] | 134510-8320 | BRACKET |
Include in #1:
106671-2743
as FUEL INJECTION PUMP
Cross reference number
Zexel num
Bosch num
Firm num
Name
Information:
Introduction
The objective of this topic is to assist users in establishing a Preventive Maintenance Program for Standby Generator Sets or as an aid in evaluating their present programs.Standby Generator Sets may not be needed very often, but when they are, it is usually under emergency conditions. Maintenance of these standby units is very important. They must always be in excellent operating condition, ready to work under load at any time.Establishing a Preventive Maintenance Program will provide maximum availability of a standby generator set when needed, longer engine and generator life, and a minimum of expensive repairs.The recommended WEEKLY maintenance checks can be performed by an operator. The checks consist of basic maintenance requirements to ensure the standby generator set will be ready for immediate use should the need arise.All YEARLY and THREE YEAR maintenance should be performed by an authorized mechanic or your Caterpillar dealer. These checks and maintenance requirements will require that the standby generator be run under load conditions, and may require special test equipment.These guidelines are to be used with the information contained in the Operation and Maintenance sections of this manual. The Operation and Maintenance sections of the manual will provide the necessary information on how to perform the checks and routine maintenance.Refer to the Generator and Engine Service Manuals and Recommended Preventive Maintenance Schedules for Standby Generator Sets, SEBU6042 for additional information, or contact your Caterpillar dealer for assistance.Inspection and Maintenance Agreements
Your Caterpillar dealer can establish an Inspection and Preventive Maintenance Program for your generator set to provide maximum reliability, increased engine and generator life, and minimize expensive repairs. Contact your Caterpillar dealer for details.General Recommendations
Safety
The stop-manual-automatic switch on the cranking panel must be set at STOP position when performing maintenance or repair work on a standby generator set. This prevents the unit from starting if a power failure or voltage drop should occur while working on the unit.To prevent personal injury due to accidental starting of the engine, disconnect the batteries or disable the starting system before doing maintenance or repair work.Lock out all switch gear and automatic transfer switches associated with the generator while performing any generator maintenance or repairs. Make sure no shock hazard exists.Failure to comply could result in personal injury or death.
Always make repairs with the engine stopped and the starting system disabled. When servicing the generator, make sure that switch gear and automatic transfer switches will not present a shock hazard. Lock them out on the generator being serviced.Record Keeping
Maintain a log or record keeping system to document all gauge readings, problems, repairs, and maintenance performed on the equipment.Space Heaters
Moisture is a natural enemy of generators and all electrical equipment. Every effort must be made to keep the generator as dry as possible. Space heaters should be operated inside the generator when it is not in use to maintain the integrity of the generator windings.
The objective of this topic is to assist users in establishing a Preventive Maintenance Program for Standby Generator Sets or as an aid in evaluating their present programs.Standby Generator Sets may not be needed very often, but when they are, it is usually under emergency conditions. Maintenance of these standby units is very important. They must always be in excellent operating condition, ready to work under load at any time.Establishing a Preventive Maintenance Program will provide maximum availability of a standby generator set when needed, longer engine and generator life, and a minimum of expensive repairs.The recommended WEEKLY maintenance checks can be performed by an operator. The checks consist of basic maintenance requirements to ensure the standby generator set will be ready for immediate use should the need arise.All YEARLY and THREE YEAR maintenance should be performed by an authorized mechanic or your Caterpillar dealer. These checks and maintenance requirements will require that the standby generator be run under load conditions, and may require special test equipment.These guidelines are to be used with the information contained in the Operation and Maintenance sections of this manual. The Operation and Maintenance sections of the manual will provide the necessary information on how to perform the checks and routine maintenance.Refer to the Generator and Engine Service Manuals and Recommended Preventive Maintenance Schedules for Standby Generator Sets, SEBU6042 for additional information, or contact your Caterpillar dealer for assistance.Inspection and Maintenance Agreements
Your Caterpillar dealer can establish an Inspection and Preventive Maintenance Program for your generator set to provide maximum reliability, increased engine and generator life, and minimize expensive repairs. Contact your Caterpillar dealer for details.General Recommendations
Safety
The stop-manual-automatic switch on the cranking panel must be set at STOP position when performing maintenance or repair work on a standby generator set. This prevents the unit from starting if a power failure or voltage drop should occur while working on the unit.To prevent personal injury due to accidental starting of the engine, disconnect the batteries or disable the starting system before doing maintenance or repair work.Lock out all switch gear and automatic transfer switches associated with the generator while performing any generator maintenance or repairs. Make sure no shock hazard exists.Failure to comply could result in personal injury or death.
Always make repairs with the engine stopped and the starting system disabled. When servicing the generator, make sure that switch gear and automatic transfer switches will not present a shock hazard. Lock them out on the generator being serviced.Record Keeping
Maintain a log or record keeping system to document all gauge readings, problems, repairs, and maintenance performed on the equipment.Space Heaters
Moisture is a natural enemy of generators and all electrical equipment. Every effort must be made to keep the generator as dry as possible. Space heaters should be operated inside the generator when it is not in use to maintain the integrity of the generator windings.