Information fuel-injection pump
BOSCH
9 410 610 993
9410610993
ZEXEL
106061-5902
1060615902
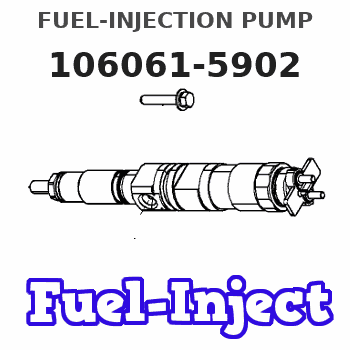
Rating:
Scheme ###:
1. | [1] | 134051-5820 | PUMP HOUSING |
1/30. | [3] | 029040-6020 | STUD |
1/45. | [1] | 134311-0000 | SPACER RING |
1/50. | [12] | 134138-0000 | STUD |
7. | [6] | 134146-3720 | PLUNGER-AND-BARREL ASSY |
7/1. | [6] | 134131-1020 | FLANGE BUSHING |
7/2. | [6] | 134152-3820 | PLUNGER-AND-BARREL ASSY |
7/3. | [6] | 134110-4820 | DELIVERY-VALVE ASSEMBLY |
7/4. | [6] | 134116-4820 | FITTING |
7/5. | [6] | 029632-2070 | O-RING |
7/6. | [6] | 134117-0500 | FILLER PIECE |
7/7. | [6] | 134112-1600 | COILED SPRING |
7/8. | [6] | 134115-0100 | GASKET |
7/9. | [6] | 029302-0140 | PLAIN WASHER |
7/10. | [6] | 134135-0200 | CAPSULE |
7/11. | [6] | 029602-0010 | LOCKING WASHER |
7/12. | [6] | 134137-0100 | SPACER RING |
7/13. | [6] | 029632-9030 | O-RING |
7/14. | [6] | 029631-5020 | O-RING |
7/15. | [6] | 029631-5020 | O-RING |
23/1. | [0] | 139400-0900 | SHIM T0.500 |
23/1. | [0] | 139400-0900 | SHIM T0.500 |
23/1. | [0] | 139400-1000 | SHIM T0.525 |
23/1. | [0] | 139400-1100 | SHIM T0.550 |
23/1. | [0] | 139400-1200 | SHIM T0.575 |
23/1. | [0] | 139400-1300 | SHIM T0.600 |
23/1. | [0] | 139400-1400 | SHIM T0.625 |
23/1. | [0] | 139400-1500 | SHIM T0.650 |
23/1. | [0] | 139400-1600 | SHIM T0.675 |
23/1. | [0] | 139400-1700 | SHIM T0.700 |
23/1. | [0] | 139400-1800 | SHIM T0.725 |
23/1. | [0] | 139400-1900 | SHIM T0.750 |
23/1. | [0] | 139400-2000 | SHIM T0.775 |
23/1. | [0] | 139400-2100 | SHIM T0.800 |
23/1. | [0] | 139400-2200 | SHIM T0.825 |
23/1. | [0] | 139400-2300 | SHIM T0.850 |
23/1. | [0] | 139400-2400 | SHIM T0.875 |
23/1. | [0] | 139400-2500 | SHIM T0.900 |
23/1. | [0] | 139400-2600 | SHIM T0.925 |
23/1. | [0] | 139400-2700 | SHIM T0.950 |
23/1. | [0] | 139400-2800 | SHIM T0.975 |
23/1. | [0] | 139400-2900 | SHIM T1.000 |
23/1. | [0] | 139400-3000 | SHIM T1.025 |
23/1. | [0] | 139400-3100 | SHIM T1.050 |
23/1. | [0] | 139400-3200 | SHIM T1.075 |
23/1. | [0] | 139400-3300 | SHIM T1.100 |
23/1. | [0] | 139400-3400 | SHIM T1.125 |
23/1. | [0] | 139400-3500 | SHIM T1.150 |
23/1. | [0] | 139400-3600 | SHIM T1.175 |
23/1. | [0] | 139400-3700 | SHIM T1.200 |
23/1. | [0] | 139400-3800 | SHIM T1.225 |
23/1. | [0] | 139400-3900 | SHIM T1.250 |
23/1. | [0] | 139400-4000 | SHIM T1.275 |
23/1. | [0] | 139400-4100 | SHIM T1.300 |
23/1. | [0] | 139400-4200 | SHIM T1.325 |
23/1. | [0] | 139400-4300 | SHIM T1.350 |
23/1. | [0] | 139400-4400 | SHIM T1.375 |
23/1. | [0] | 139400-4500 | SHIM T1.400 |
23/1. | [0] | 139400-4600 | SHIM T1.425 |
23/1. | [0] | 139400-4700 | SHIM T1.450 |
23/1. | [0] | 139400-4800 | SHIM T1.475 |
23/1. | [0] | 139400-4900 | SHIM T1.500 |
23/1. | [0] | 139400-5000 | SHIM T1.525 |
23/1. | [0] | 139400-5100 | SHIM T1.550 |
23/1. | [0] | 139400-5200 | SHIM T1.575 |
23/1. | [0] | 139400-5300 | SHIM T1.600 |
23/1. | [0] | 139400-5400 | SHIM T1.625 |
23/1. | [0] | 139400-5500 | SHIM T1.650 |
23/1. | [0] | 139400-5600 | SHIM T1.675 |
23/1. | [0] | 139400-5700 | SHIM T1.700 |
23/1. | [0] | 139400-5800 | SHIM T1.725 |
23/1. | [0] | 139400-5900 | SHIM T1.750 |
23/1. | [0] | 139400-6000 | SHIM T1.775 |
23/1. | [0] | 139400-6100 | SHIM T1.800 |
23/1. | [0] | 139400-6200 | SHIM T1.825 |
23/1. | [0] | 139400-6300 | SHIM T1.850 |
23/1. | [0] | 139400-6400 | SHIM T1.875 |
23/1. | [0] | 139400-6500 | SHIM T1.900 |
23/1. | [0] | 139400-6600 | SHIM T1.925 |
23/1. | [0] | 139400-6700 | SHIM T1.950 |
23/1. | [0] | 139400-6800 | SHIM T1.975 |
24. | [12] | 134132-0300 | PLAIN WASHER D20&11T2.5 |
26. | [12] | 013021-0040 | UNION NUT M10P1.5H8 |
30. | [1] | 134001-0200 | BUSHING |
30A. | [1] | 134001-0000 | BUSHING |
32. | [1] | 134256-2500 | CONTROL RACK |
33. | [1] | 024030-2030 | BEARING PIN |
34. | [1] | 134222-0000 | BUSHING |
37. | [1] | 134510-6800 | GASKET |
38. | [1] | 134222-1000 | ADAPTOR |
39. | [4] | 014110-4440 | LOCKING WASHER |
40. | [4] | 012154-1440 | FLAT-HEAD SCREW M4P0.7L14 |
41. | [6] | 134241-0320 | CONTROL SLEEVE |
43. | [6] | 134216-0000 | SLOTTED WASHER |
44. | [6] | 134215-0700 | COILED SPRING |
45. | [6] | 134217-0500 | SLOTTED WASHER |
47. | [6] | 134200-0420 | TAPPET |
47/2. | [1] | 134204-0100 | ROLLER |
47/3. | [1] | 134205-0000 | BUSHING |
47/4. | [1] | 134203-0000 | BEARING PIN |
47/5. | [1] | 131206-0500 | SLIDER |
59. | [1] | 016650-2230 | BEARING PLATE |
64/1. | [0] | 134303-0000 | SHIM D59.8&43T1.2 |
64/1. | [0] | 134303-0100 | SHIM D59.8&43T1.5 |
64/1. | [0] | 134303-0200 | SHIM D59.8&43T1.8 |
64/1. | [0] | 134303-0300 | SHIM D59.8&43T2.0 |
64/1. | [0] | 134303-0400 | SHIM D59.8&43T0.6 |
67. | [4] | 029010-6810 | BLEEDER SCREW |
71. | [1] | 134371-4900 | CAMSHAFT |
74. | [1] | 134306-0300 | BEARING SHELL |
75. | [2] | 020106-2040 | BLEEDER SCREW M6P1L20 |
79. | [1] | 016650-2230 | BEARING PLATE |
80. | [1] | 134316-1700 | COVER |
81. | [1] | 139625-0000 | PACKING RING |
82/1. | [0] | 134314-0000 | SHIM T0.1 |
82/1. | [0] | 134314-0100 | SHIM T0.12 |
82/1. | [0] | 134314-0200 | SHIM T0.14 |
82/1. | [0] | 134314-0300 | SHIM T0.16 |
82/1. | [0] | 134314-0400 | SHIM T0.18 |
82/1. | [0] | 134314-0500 | SHIM T0.3 |
82/1. | [0] | 134314-0600 | SHIM T0.5 |
83. | [1] | 029635-5010 | O-RING |
84. | [1] | 134563-0900 | SLIDING PIECE |
85. | [1] | 134043-0800 | COVER |
86. | [1] | 134042-1400 | GASKET |
87. | [12] | 012206-1640 | FLAT-HEAD SCREW M6P1L16 |
88. | [1] | 134045-0100 | CAPSULE |
89. | [1] | 026524-2940 | GASKET D28.9&24.3T2 |
93. | [3] | 139206-0400 | UNION NUT |
95. | [1] | 131041-0800 | GASKET |
96. | [6] | 134047-0000 | CAPSULE |
98. | [1] | 025805-1910 | WOODRUFF KEY |
118. | [1] | 134496-0900 | POINTER |
119. | [2] | 020006-1240 | BLEEDER SCREW M6P1L12 4T |
137. | [1] | 029731-4680 | EYE BOLT |
138. | [2] | 029341-4130 | GASKET D20&13.8T2* |
146. | [1] | 134433-2420 | PIPE |
147. | [1] | 029731-0490 | EYE BOLT |
148. | [3] | 029341-0110 | GASKET |
157. | [1] | 029731-4570 | EYE BOLT |
158. | [2] | 029341-4130 | GASKET D20&13.8T2* |
167. | [1] | 133424-0221 | OVER FLOW VALVE |
168. | [2] | 029341-4130 | GASKET D20&13.8T2* |
172. | [1] | 131420-0400 | BLEEDER SCREW |
173. | [1] | 029340-6020 | GASKET D10&6.5T1.00 |
186. | [1] | 154355-0020 | BRACKET |
208. | [1] | 134510-7200 | CONNECTOR |
209. | [2] | 010635-1040 | FLAT-HEAD SCREW M5P0.8L10 |
210. | [2] | 014110-5440 | LOCKING WASHER |
211. | [1] | 134510-5000 | COVER |
212. | [1] | 029632-6030 | O-RING |
Include in #1:
106671-4682
as FUEL INJECTION PUMP
Cross reference number
Zexel num
Bosch num
Firm num
Name
Information:
1. Preparation of vehicle for fuel consumption test (consult dynamometer manufacturer's operating instructions for specific details on correct operation). Always perform the Primary Engine Test procedure before vehicle is installed on chassis dynamometer.a. Place vehicle on the chassis dynamometer. Tie the vehicle in a way that will not add any load to the drive wheels. Do not pull wheels down into dynamometer drive rolls. Check the radiator coolant level, crankcase oil level, tire pressure, tire condition, remove rocks from the tire tread and connect exhaust system.
Recapped tires should be run on a chassis dynamometer only at the customer's own risk.
b. The maximum acceptable fuel rate must be calculated for the customer's engine by use of the formula that follows: Find the rated brake specific fuel consumption (lb-bhp/hr) from the RACK SETTING INFORMATION and add .010 in. manufacturing tolerance. Multiply this value by the advertised engine horsepower (plus 3% manf. tol.) and divide by the density of the fuel (lbs/gal).c. Calculate the allowable limits that the customer can expect from his engine and present these figures to him. Caterpillar engines are rated with the conditions that follow: Measure and record these variables. Advertised engine bhp (less 3% manufacturing tolerance) can then be corrected to test conditions by use of procedure and correction tables found in Special Instruction GEG01024.2. Operate vehicle at 60% of rated speed with moderate load until oil and coolant temperatures reach their normal range for operation.
If there is a heavy vibration, drive shaft whip, tire bounce, etc., do not continue with dynamometer test until cause of the problem is corrected. Engines that have had new internal parts installed should be operated on a run-in schedule before operation at full load.
Put transmission in direct gear and the differential in the highest speed ratio. Operate vehicle at maximum engine speed and increase chassis dynamometer load until a speed of 50 rpm less than rated speed is reached (continuity light should be on). Maintain this speed for one minute and record the engine speed, wheel horsepower and fuel rate.3. If the fuel rate and the wheel horsepower are both acceptable, then the engine is not the cause of the complaint, or the complaint is not valid. Refer to section PROBLEM WITH VEHICLE OR VEHICLE OPERATION.4. If the
Recapped tires should be run on a chassis dynamometer only at the customer's own risk.
b. The maximum acceptable fuel rate must be calculated for the customer's engine by use of the formula that follows: Find the rated brake specific fuel consumption (lb-bhp/hr) from the RACK SETTING INFORMATION and add .010 in. manufacturing tolerance. Multiply this value by the advertised engine horsepower (plus 3% manf. tol.) and divide by the density of the fuel (lbs/gal).c. Calculate the allowable limits that the customer can expect from his engine and present these figures to him. Caterpillar engines are rated with the conditions that follow: Measure and record these variables. Advertised engine bhp (less 3% manufacturing tolerance) can then be corrected to test conditions by use of procedure and correction tables found in Special Instruction GEG01024.2. Operate vehicle at 60% of rated speed with moderate load until oil and coolant temperatures reach their normal range for operation.
If there is a heavy vibration, drive shaft whip, tire bounce, etc., do not continue with dynamometer test until cause of the problem is corrected. Engines that have had new internal parts installed should be operated on a run-in schedule before operation at full load.
Put transmission in direct gear and the differential in the highest speed ratio. Operate vehicle at maximum engine speed and increase chassis dynamometer load until a speed of 50 rpm less than rated speed is reached (continuity light should be on). Maintain this speed for one minute and record the engine speed, wheel horsepower and fuel rate.3. If the fuel rate and the wheel horsepower are both acceptable, then the engine is not the cause of the complaint, or the complaint is not valid. Refer to section PROBLEM WITH VEHICLE OR VEHICLE OPERATION.4. If the