Information fuel-injection pump
BOSCH
9 461 627 094
9461627094
ZEXEL
104646-5461
1046465461
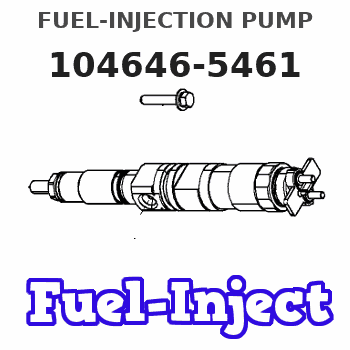
Rating:
Include in #2:
104746-5461
as FUEL INJECTION PUMP
Cross reference number
Zexel num
Bosch num
Firm num
Name
Information:
Important
Clean the oil supply line to the compressor and run the engine for a few seconds to be sure the oil supply is flowing freely.Connect oil and/or air pipes, ensuring that the air cleaner or filter is clean and properly installed.Check after Installation
With the compressor running, check for noisy operation and oil and air leaks.Dismantling
Marking before dismantling
The compressor should have the following items marked to show the correct relationship prior to dismantling.1. Position of cylinder head in relation to cylinder and crankcase.2. Position of end-cover(s) in relation to crankcase.3. Position of crankshaft in relation to crankcase.Removing and Dismantling Cylinder Head and Cylinder
Remove the unloader cap and copper washer and withdraw the unloader plunger assembly and spring.Remove the delivery valve cap and copper washer, and remove delivery valve spring and seat retaining spring.Unscrew the four nuts and washers from cylinder head studs and lift off cylinder head. Remove the joint.Remove the delivery valve and screw out the valve seat.Withdraw inlet valve spring guide. (A simple extractor can be made from two 1/4 in U.N.F. bolts and a strip of metal formed to bridge the guide). Remove the inlet valve spring, inlet valve and valve seat.Withdraw cylinder and remove the joint.Removing and Dismantling Piston and Connecting Rod Assemblies
Remove the compressor mounting bracket and joint.Turn the crankshaft to B.D.C. position and release the tabs of the locking strap. Unscrew the two bolts and remove the connecting rod cap. Withdraw piston assembly and replace connecting rod cap.Remove the piston rings from the piston. If the piston is to be detached from the connecting rod, release one gudgeon pin retaining circlip and press the gudgeon pin from the piston and connecting rod.Removing Crankshaft
Remove compressor drive gear.Remove drive key from crankshaft.Unscrew the four setscrews or nuts together with washers securing the rear end-cover to crankcase. Withdraw the end-cover, plain bearing, thrust washer and joint.Unscrew the four setscrews or nuts securing the drive end-cover, and withdraw the end-cover complete with crankshaft and joint. Tap crankshaft with bearing from drive end-cover.Cleaning
Ensure that all carbon is removed from the cylinder head. Check that the air passages in the head and the oilways in the crankcase, where applicable, rear end-cover and crankshaft are clear and clean.Clean inlet and discharge valves, not damaged or worn excessively, by lapping them on a sheet of crocus cloth held on a flat surface.Inspection of Parts
Cylinder
Check cylinder bore for excessive wear, out-of-round or scoring. If scored or out-of-round more than 0.002 in (0,05 mm) or tapered more than 0.003 in (0,08 mm) cylinder should be rebored. The original cylinder bore is to the limits 2.6255/2.6265 in (66,69/66,71 mm) and the clearance for the piston is 0.002/0.003 in (0,05/0,08 mm). Check for wear in cylinder bore and rectify in accordance with following table:-Piston and Connecting Rod
Inspect piston for scores, cracks or damage of any kind. Check fit of rings in ring grooves, clearance should be 0.0005/0.0025 in (0,01/0,06 mm). Install rings in cylinder and check that gaps are 0.002/0.007 in (0,08/0,18 mm). Check fit
Clean the oil supply line to the compressor and run the engine for a few seconds to be sure the oil supply is flowing freely.Connect oil and/or air pipes, ensuring that the air cleaner or filter is clean and properly installed.Check after Installation
With the compressor running, check for noisy operation and oil and air leaks.Dismantling
Marking before dismantling
The compressor should have the following items marked to show the correct relationship prior to dismantling.1. Position of cylinder head in relation to cylinder and crankcase.2. Position of end-cover(s) in relation to crankcase.3. Position of crankshaft in relation to crankcase.Removing and Dismantling Cylinder Head and Cylinder
Remove the unloader cap and copper washer and withdraw the unloader plunger assembly and spring.Remove the delivery valve cap and copper washer, and remove delivery valve spring and seat retaining spring.Unscrew the four nuts and washers from cylinder head studs and lift off cylinder head. Remove the joint.Remove the delivery valve and screw out the valve seat.Withdraw inlet valve spring guide. (A simple extractor can be made from two 1/4 in U.N.F. bolts and a strip of metal formed to bridge the guide). Remove the inlet valve spring, inlet valve and valve seat.Withdraw cylinder and remove the joint.Removing and Dismantling Piston and Connecting Rod Assemblies
Remove the compressor mounting bracket and joint.Turn the crankshaft to B.D.C. position and release the tabs of the locking strap. Unscrew the two bolts and remove the connecting rod cap. Withdraw piston assembly and replace connecting rod cap.Remove the piston rings from the piston. If the piston is to be detached from the connecting rod, release one gudgeon pin retaining circlip and press the gudgeon pin from the piston and connecting rod.Removing Crankshaft
Remove compressor drive gear.Remove drive key from crankshaft.Unscrew the four setscrews or nuts together with washers securing the rear end-cover to crankcase. Withdraw the end-cover, plain bearing, thrust washer and joint.Unscrew the four setscrews or nuts securing the drive end-cover, and withdraw the end-cover complete with crankshaft and joint. Tap crankshaft with bearing from drive end-cover.Cleaning
Ensure that all carbon is removed from the cylinder head. Check that the air passages in the head and the oilways in the crankcase, where applicable, rear end-cover and crankshaft are clear and clean.Clean inlet and discharge valves, not damaged or worn excessively, by lapping them on a sheet of crocus cloth held on a flat surface.Inspection of Parts
Cylinder
Check cylinder bore for excessive wear, out-of-round or scoring. If scored or out-of-round more than 0.002 in (0,05 mm) or tapered more than 0.003 in (0,08 mm) cylinder should be rebored. The original cylinder bore is to the limits 2.6255/2.6265 in (66,69/66,71 mm) and the clearance for the piston is 0.002/0.003 in (0,05/0,08 mm). Check for wear in cylinder bore and rectify in accordance with following table:-Piston and Connecting Rod
Inspect piston for scores, cracks or damage of any kind. Check fit of rings in ring grooves, clearance should be 0.0005/0.0025 in (0,01/0,06 mm). Install rings in cylinder and check that gaps are 0.002/0.007 in (0,08/0,18 mm). Check fit