Information fuel-injection pump
BOSCH
9 410 617 363
9410617363
ZEXEL
104298-3010
1042983010
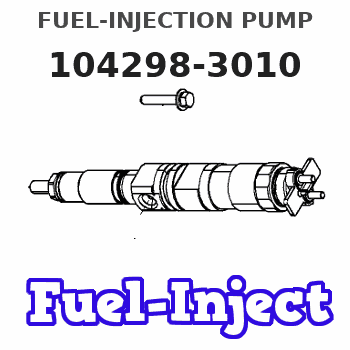
Rating:
Components :
0. | INJECTION-PUMP ASSEMBLY | 104298-3010 |
1. | _ | |
2. | FUEL INJECTION PUMP | |
3. | NUMBER PLATE | |
4. | _ | |
5. | CAPSULE | |
6. | ADJUSTING DEVICE | |
7. | NOZZLE AND HOLDER ASSY | |
8. | Nozzle and Holder | |
9. | Open Pre:MPa(Kqf/cm2) | |
10. | NOZZLE-HOLDER | |
11. | NOZZLE |
Scheme ###:
5. | [3] | 140153-6720 | PLUNGER-AND-BARREL ASSY |
12. | [3] | 140110-4720 | DELIVERY-VALVE ASSEMBLY |
13. | [3] | 140112-2900 | COMPRESSION SPRING |
16. | [3] | 140115-1400 | GASKET |
17. | [3] | 140116-4800 | FITTING |
18. | [3] | 140117-1500 | SLOTTED WASHER |
20. | [3] | 016500-1520 | O-RING |
40. | [3] | 140200-1620 | TAPPET |
44. | [3] | 140212-0300 | BEARING PIN |
45. | [1] | 140213-0500 | WIRE |
50. | [3] | 140215-1900 | COMPRESSION SPRING |
51. | [3] | 140216-0800 | SLOTTED WASHER |
52. | [3] | 140217-2200 | SLOTTED WASHER |
53/1. | [1] | 140217-5000 | PLATE D19T2.60 |
53/1. | [1] | 140217-5100 | PLATE D19T2.65 |
53/1. | [1] | 140217-5200 | PLATE D19T2.70 |
53/1. | [1] | 140217-5300 | PLATE D19T2.75 |
53/1. | [1] | 140217-5400 | PLATE D19T2.80 |
53/1. | [1] | 140217-5500 | PLATE D19T2.85 |
53/1. | [1] | 140217-5600 | PLATE D19T2.90 |
53/1. | [1] | 140217-5700 | PLATE D19T2.95 |
53/1. | [1] | 140217-5800 | PLATE D19T3.00 |
53/1. | [1] | 140217-5900 | PLATE D19T3.05 |
53/1. | [1] | 140217-6000 | PLATE D19T3.10 |
53/1. | [1] | 140217-6100 | PLATE D19T3.15 |
53/1. | [1] | 140217-6200 | PLATE D19T3.20 |
53/1. | [1] | 140217-6300 | PLATE D19T3.25 |
53/1. | [1] | 140217-6400 | PLATE D19T3.30 |
53/1. | [1] | 140217-6500 | PLATE D19T3.35 |
53/1. | [1] | 140217-6600 | PLATE D19T3.40 |
53/1. | [1] | 140217-6700 | PLATE D19T3.45 |
53/1. | [1] | 140217-6800 | PLATE D19T3.50 |
53/1. | [1] | 140217-6900 | PLATE D19T3.55 |
53/1. | [1] | 140217-7000 | PLATE D19T3.60 |
53/1. | [1] | 140217-7100 | PLATE D19T3.65 |
53/1. | [1] | 140217-7200 | PLATE D19T3.70 |
53/1. | [1] | 140217-7300 | PLATE D19T3.75 |
53/1. | [1] | 140217-7400 | PLATE D19T3.80 |
53/1. | [1] | 140217-7500 | PLATE D19T3.85 |
53/1. | [1] | 140217-7600 | PLATE D19T3.90 |
53/1. | [1] | 140217-7700 | PLATE D19T3.95 |
53/1. | [1] | 140217-7800 | PLATE D19T4.00 |
53/1. | [1] | 140217-7900 | PLATE D19T4.05 |
53/1. | [1] | 140217-8000 | PLATE D19T4.10 |
53/1. | [1] | 140253-2000 | PLATE |
53/1. | [1] | 140253-2100 | PLATE |
53/1. | [1] | 140253-2200 | PLATE |
53/1. | [1] | 140253-2300 | PLATE |
53/1. | [1] | 140253-2400 | PLATE |
53/1. | [1] | 140253-2500 | PLATE |
53/1. | [1] | 140253-2600 | PLATE |
53/1. | [1] | 140253-2700 | PLATE |
53/1. | [1] | 140253-2800 | PLATE |
53/1. | [1] | 140253-2900 | PLATE |
53/1. | [1] | 140253-3000 | PLATE |
53/1. | [1] | 140253-3100 | PLATE |
53/1. | [1] | 140253-3200 | PLATE |
53/1. | [1] | 140253-3300 | PLATE |
53/1. | [1] | 140253-3400 | PLATE |
53/1. | [1] | 140253-3500 | PLATE |
53/1. | [1] | 140253-3600 | PLATE |
53/1. | [1] | 140253-3700 | PLATE |
53/1. | [1] | 140253-3800 | PLATE |
53/1. | [1] | 140253-3900 | PLATE |
53/1. | [1] | 140253-4000 | PLATE |
53/1. | [1] | 140253-4100 | PLATE |
53/1. | [1] | 140253-4200 | PLATE |
53/1. | [1] | 140253-4300 | PLATE |
53/1. | [1] | 140253-4400 | PLATE |
53/1. | [1] | 140253-4500 | PLATE |
53/1. | [1] | 140253-4600 | PLATE |
53/1. | [1] | 140253-4700 | PLATE |
53/1. | [1] | 140253-4800 | PLATE |
53/1. | [1] | 140253-4900 | PLATE |
60. | [1] | 140243-2220 | CONTROL RACK |
77. | [3] | 140241-2700 | CONTROL SLEEVE |
93. | [1] | 140402-1200 | EYE BOLT |
94. | [2] | 026512-1540 | GASKET D15.4&12.2T1.50 |
156. | [2] | 140255-0000 | BEARING PIN |
157. | [2] | 029320-6010 | LOCKING WASHER |
158. | [1] | 140256-0400 | COVER |
159. | [2] | 010735-1020 | FLAT-HEAD SCREW M5P0.9L10 |
Include in #2:
104298-3010
as INJECTION-PUMP ASSEMBLY
Cross reference number
Zexel num
Bosch num
Firm num
Name
Information:
Always use a wrench to hold the hex fitting on top of the master nozzle, when assembling or disassembling lines. If a wrench is not used, the master nozzle and manifold it is installed into may be damaged.
Check fuel line for "Close-in" Do NOT use fuel lines with an ID (inside diameter) LESS than 1.191 mm (0.0469 in). The fuel line ID can be checked using a 1.2 mm (.047 in) drill.If the drill bit can NOT be inserted into the fuel line high pressure hole, either drill out the line using a 1.6 mm (.063 in) drill or replace the fuel line with a new line. Use the same length and internal diameter lines each time the reference pump is tested.
If the fuel lines are not completely and thoroughly cleaned out after the drilling procedure, metal particles or foreign debris in the line will damage the master nozzles and contaminate the calibration fluid in the test stand.
After the hole has been drilled to the correct size, clean the line with solvent and remove any metal particles. Blow compressed air through the lines, after cleaning, to remove any solvent.
When using pressure air, wear a protective face shield and protective clothing. The maximum air pressure at the nozzle must be less than 205 kPa (30 psi) for cleaning purposes.
9. Identify fuel lines and nozzles in the same order as the reference pump plunger and barrels (1-6 or 1-12) and use the same lines and nozzles each time the reference pump is run on the test bench.10. Select two test points (speeds and shot settings) that will cover the delivery range realized in a dealer's shop.Always set up the test points using only the pump rack zero pin. Do not set the rack full load or idle stops.11. The test stand and reference pump should be run for ten minutes.Make sure test stand pressures and temperatures are within published specifications and that they are stable.12. Set the first test point.Take five samples (draws) and record the individual pump and barrel deliveries for each sample (draw).13. Examine pump and barrel sample data:* Are the samples consistent?The MAXIMUM allowable difference between the HIGH and LOW delivery pump and barrel in the reference pump should be three cc's.If there is NOT a three cc difference, swap pump and barrels in the pump housing (or check master nozzles for damage) and re-test UNTIL the maximum HIGH to LOW