Information fuel-injection pump
BOSCH
9 410 617 147
9410617147
ZEXEL
104277-5000
1042775000
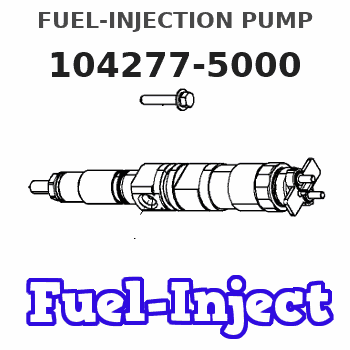
Rating:
Components :
0. | INJECTION-PUMP ASSEMBLY | 104277-5000 |
1. | _ | |
2. | FUEL INJECTION PUMP | |
3. | NUMBER PLATE | |
4. | _ | |
5. | CAPSULE | |
6. | ADJUSTING DEVICE | |
7. | NOZZLE AND HOLDER ASSY | |
8. | Nozzle and Holder | |
9. | Open Pre:MPa(Kqf/cm2) | |
10. | NOZZLE-HOLDER | |
11. | NOZZLE |
Scheme ###:
5. | [1] | 141176-5721 | PLUNGER-AND-BARREL ASSY |
7. | [1] | 141133-7700 | CAPSULE |
8. | [1] | 141485-1203 | O-RING |
12. | [1] | 141145-2320 | DELIVERY-VALVE ASSEMBLY |
20. | [1] | 141482-8600 | O-RING |
21. | [1] | 141119-3700 | FLANGE BUSHING |
22. | [6] | 141124-1400 | BLEEDER SCREW |
25. | [1] | 141403-0001 | O-RING |
50. | [1] | 141215-5501 | COMPRESSION SPRING |
51. | [1] | 141216-1200 | SLOTTED WASHER |
52. | [1] | 141217-5600 | SLOTTED WASHER |
53. | [1] | 141218-8020 | GUIDE |
55. | [1] | 141220-0700 | LOCKING WASHER |
60. | [1] | 141291-3900 | CONTROL RACK |
77. | [1] | 141292-2700 | CONTROL SLEEVE |
81. | [1] | 141245-2000 | POINTER |
82/1. | [0] | 023500-6210 | PLAIN WASHER D11&6.4T1.5 |
82/1. | [0] | 029300-6010 | PLAIN WASHER D11&6.4T0.8 |
82/1. | [0] | 029300-6020 | PLAIN WASHER D11&6.4T0.35 |
83. | [1] | 020006-1440 | BLEEDER SCREW M6P1L14 |
90. | [1] | 029112-2020 | CAPSULE |
91. | [1] | 026522-2740 | GASKET D26.9&22.2T1 |
92A. | [1] | 141401-3900 | INLET UNION |
93. | [1] | 141402-3420 | EYE BOLT |
94. | [2] | 141485-3300 | O-RING |
110. | [1] | 141420-0600 | BLEEDER SCREW |
111. | [1] | 141107-0500 | GASKET |
160. | [1] | 141418-1500 | SET OF NUTS |
161. | [1] | 141107-0700 | GASKET |
162. | [1] | 141480-1000 | COVER |
165. | [2] | 373658-1400 | CAPSULE |
166. | [2] | 026510-1340 | GASKET D13.4&10.2T1 |
170. | [1] | 141405-4300 | CAPSULE |
171. | [1] | 141485-1201 | O-RING |
172. | [1] | 141401-5900 | INLET UNION |
173. | [1] | 141402-6700 | EYE BOLT |
174. | [2] | 141485-3300 | O-RING |
Include in #1:
101401-9451
as _
Include in #2:
104277-5000
as INJECTION-PUMP ASSEMBLY
Cross reference number
Zexel num
Bosch num
Firm num
Name
104277-5000
FUEL-INJECTION PUMP
K 24JX FUEL INJECTION PUMP PF-1DX PF
K 24JX FUEL INJECTION PUMP PF-1DX PF
Information:
Illustration 9 g06286243
Typical example
Illustration 9 shows the governor plate displaying high wear at the sleeve contact points.
Illustration 10 g06286261
Typical example
Illustration 8 shows the thrust sleeve displaying an excessive wear groove.
Illustration 11 g06286627
Typical example
Illustration 12 g06286629
Typical example
Illustration 11 and Illustration 11 show the weight thrust fingers badly worn.
Illustration 13 g06286630
Typical example
Illustration 13 shows pivot heels showing excessive wear.Fuel Quality
Illustration 14 g06286604
Typical example
Illustration 14 shows that nitrile rubber seals have cracked causing fuel leakage. The cracks in the seals are attributed to fuel attacking the rubber. Ensure that there is no particle contamination in the fuel injection pump.Unmodified Vegetable Oil or Poor Quality FAME
Illustration 15 g06286612
Typical example
Stuck metering valve causing engine overspeed. Top cover of fuel injection pump removed. Black sticky material adhering to all non-alloy surfaces, this is due to the use of unmodified vegetable oil or poor quality FAME. Refer to Illustration 15.High Water Content in Fuel
Illustration 16 g06286613
Typical example
Illustration 17 g06286615
Typical example
Illustration 16 and Illustration 17 show corrosion on component surfaces, due to high water content in fuel.Characteristics Associated with Poor Quality Fuel and Potential Issue
Table 1
Fuel Characteristics Effect Issue
FAMEs in general Causes some elastomers to soften, swell, harden, and crack. Fuel leakage.
Free methanol in FAME Corrodes aluminum and zinc. Low flash point. Corrosion on fuel injection equipment.
FAME process chemicals Potassium and sodium compound. Solid particles. Blocked nozzles.
Dissolved water in FAME Reversion of FAME to a fatty acid. Fuel filter plugging.
Free water in FAME Corrosion. Sustains bacteria. Corrosion on fuel injection equipment. Sludging.
Free glycerine, mono, and
di-glycerines in FAME Corrodes non-ferrous metals.
Sediments on moving parts and lacquering. Fuel filter clogging.
Fuel injector clogging.
Free fatty acid Corrosion of Zinc plating.
Slats of organic acids.
Organic compound formed. Corrosion on fuel injection equipment.
Fuel filter plugging.
Sediment on components
High viscosity at low temperature Generates excessive localized heat.
Higher stressed components. Fuel injection pump seizures.
Early life issues.
Poor nozzle spray.
Corrosive acids Corrodes all metallic parts. Corrosion on fuel injection equipment.
High molecular organic acids Corrosion of Zinc plating.
Slats of organic acids.
Organic compound formed. Corrosion on fuel injection equipment.
Fuel filter plugging.
Sediment on components
Polymerization products Deposits in fuel mixes Fuel filter plugging. Lacquering formation in hot areas. Recommended Procedures
Prime the fuel system to remove any air. Refer to Operation and Maintenance Manual, Fuel System - Prime for the correct procedure.Check the pressure of the fuel system. Refer to Systems Operation, Testing and Adjusting, Fuel System Pressure - Test for the correct procedure.Check the operation of the fuel injection nozzles. Refer to Systems Operation, Testing and Adjusting, Fuel Injection Nozzle - Test for the correct procedure.To inspect the fuel injection pump, refer to Special Instruction, REHS3767, Inspection of Fuel Injection Pumps on 3054C, C3.3, C4.4 (Mechanical), and C7.1 (Mechanical) Engines for the correct procedure.