Information fuel-injection pump
BOSCH
9 410 617 827
9410617827
ZEXEL
104264-5102
1042645102
AKASAKA-DIESEL
001254288000
001254288000
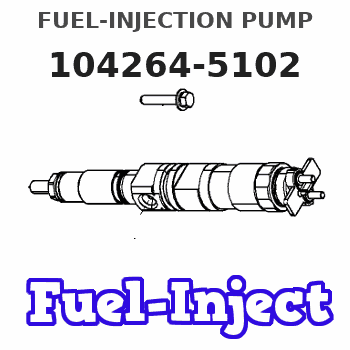
Rating:
Components :
0. | INJECTION-PUMP ASSEMBLY | 104264-5102 |
1. | _ | |
2. | FUEL INJECTION PUMP | |
3. | NUMBER PLATE | |
4. | _ | |
5. | CAPSULE | |
6. | ADJUSTING DEVICE | |
7. | NOZZLE AND HOLDER ASSY | |
8. | Nozzle and Holder | |
9. | Open Pre:MPa(Kqf/cm2) | |
10. | NOZZLE-HOLDER | |
11. | NOZZLE |
Scheme ###:
1. | [1] | 141055-5920 | PUMP HOUSING |
5. | [1] | 141176-1121 | PLUNGER-AND-BARREL ASSY |
7. | [1] | 141133-0500 | CAPSULE |
8. | [1] | 141403-0400 | GASKET |
12. | [1] | 141145-4721 | DELIVERY-VALVE ASSEMBLY |
12/1. | [1] | 141145-5500 | SEAT;D.V. |
12/2. | [1] | 141145-5600 | SEAT;D.V. |
12/3. | [1] | 016808-0020 | BALL |
12/4. | [1] | 141113-0404 | SLOTTED WASHER |
12/5. | [1] | 141112-6901 | COMPRESSION SPRING |
12/6. | [1] | 141113-2500 | FILLER PIECE |
12/7. | [1] | 016806-0020 | BALL |
12/8. | [1] | 141113-0900 | SLOTTED WASHER |
12/9. | [1] | 141112-8701 | COILED SPRING |
12/10. | [1] | 141113-2003 | FILLER PIECE |
12/11. | [2] | 010233-2020 | HEX-SOCKET-HEAD CAP SCREW |
17. | [1] | 141138-0900 | FITTING |
20. | [1] | 141118-2000 | O-RING |
21. | [1] | 141119-3600 | FLANGE BUSHING |
22. | [6] | 141124-1300 | BLEEDER SCREW |
25. | [1] | 141482-9600 | O-RING |
50. | [1] | 141215-5402 | COMPRESSION SPRING |
51. | [1] | 141216-1800 | SLOTTED WASHER |
52. | [1] | 141217-5500 | SLOTTED WASHER |
53. | [1] | 141218-7920 | GUIDE |
55. | [1] | 141220-1200 | LOCKING WASHER |
60. | [1] | 141244-5600 | CONTROL RACK |
77. | [1] | 141241-7200 | CONTROL SLEEVE |
81. | [1] | 141245-2900 | POINTER |
82/1. | [0] | 023500-6210 | PLAIN WASHER D11&6.4T1.5 |
82/1. | [0] | 029300-6010 | PLAIN WASHER D11&6.4T0.8 |
82/1. | [0] | 029300-6020 | PLAIN WASHER D11&6.4T0.35 |
83. | [1] | 020006-1440 | BLEEDER SCREW M6P1L14 |
93. | [1] | 141402-5200 | EYE BOLT |
110. | [1] | 141420-0800 | BLEEDER SCREW |
111. | [1] | 141421-0000 | GASKET |
160. | [1] | 141418-1400 | SET OF NUTS |
161. | [1] | 141107-0700 | GASKET |
162. | [1] | 141480-0900 | COVER |
163. | [1] | 373658-1400 | CAPSULE |
164. | [1] | 141107-0500 | GASKET |
170. | [1] | 141133-1000 | CAPSULE |
171. | [1] | 141403-0600 | GASKET |
172. | [2] | 141401-5000 | INLET UNION |
172. | [2] | 141401-5000 | INLET UNION |
173. | [1] | 141402-7120 | EYE BOLT |
174. | [4] | 141482-9400 | O-RING |
174. | [4] | 141482-9400 | O-RING |
Include in #1:
101491-9157
as _
Include in #2:
104264-5102
as INJECTION-PUMP ASSEMBLY
Cross reference number
Zexel num
Bosch num
Firm num
Name
104264-5102
001254288000 AKASAKA-DIESEL
FUEL-INJECTION PUMP
K 24FX FUEL INJECTION PUMP PF-1GX PF
K 24FX FUEL INJECTION PUMP PF-1GX PF
Information:
Do not use the same vacuum sampling pump for extracting oil samples that is used for extracting coolant samples.A small residue of either type sample may remain in the pump and may cause a false positive analysis for the sample being taken.Always use a separate pump for oil sampling and a separate pump for coolant sampling.Failure to do so may cause a false analysis which could lead to customer and dealer concerns.
New Systems, Refilled Systems, and Converted Systems
Perform an S O S coolant analysis (Level 2) at the following maintenance intervals.
Every Year
Initial 500 service hoursPerform this analysis at the interval that occurs first for new systems, for refilled systems, or for converted systems that use Cat coolant products. This 500 hour check will also check for any residual cleaner that may have contaminated the system.Recommended Sampling Interval for S O S Services Coolant Analysis
Table 1
Recommended Interval
Type of Finished Coolant Level 1 Level 2
Cat DEAC
Cat SCA
Conventional Heavy-Duty Coolants Every 250 hours(1)(2) Yearly(1)(2)(3)
Cat ELC
Cat ELI
Commercial EC-1 Coolants Optional(3) Yearly(3)
(1) The recommended sampling interval for all commercial coolants that meet Cat EC-1 (Engine Coolant specification - 1)
(2) The recommended sampling interval for all conventional heavy-duty coolant/antifreeze.
(3) The Level 2 Coolant Analysis should be performed sooner if a problem is suspected or identified.Note: Check the SCA (Supplemental Coolant Additive) of the conventional coolant at every oil change or at every 250 hours. Perform this check at the interval that occurs first.S O S Services Coolant Analysis (Level 1)
A coolant analysis (Level 1) is a test of the properties of the coolant.The following properties of the coolant are tested:
Glycol concentration for freeze protection and boil protection
Ability to protect from erosion and corrosion
pH
Conductivity
Visual analysis
Odor analysisThe results are reported, and appropriate recommendations are made.S O S Services Coolant Analysis (Level 2)
A coolant analysis (Level 2) is a comprehensive chemical evaluation of the coolant. This analysis is also a check of the overall condition of the cooling system.The S O S coolant analysis (Level 2) has the following features:
Full coolant analysis (Level 1)
Identification of metal corrosion and of contaminants
Identification of buildup of the impurities that cause corrosion
Identification of buildup of the impurities that cause scaling
Determination of the possibility of electrolysis within the cooling system of the engineThe results are reported, and appropriate recommendations are made.For more information on S O S coolant analysis, consult your Cat dealer.