Information fuel-injection pump
BOSCH
9 410 618 477
9410618477
ZEXEL
104264-4044
1042644044
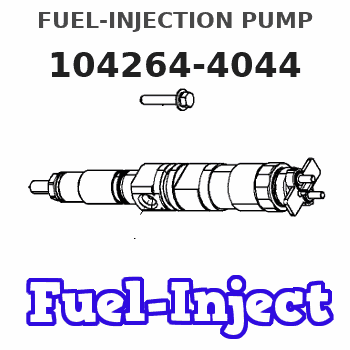
Rating:
Components :
0. | INJECTION-PUMP ASSEMBLY | 104264-4044 |
1. | _ | |
2. | FUEL INJECTION PUMP | |
3. | NUMBER PLATE | |
4. | _ | |
5. | CAPSULE | |
6. | ADJUSTING DEVICE | |
7. | NOZZLE AND HOLDER ASSY | |
8. | Nozzle and Holder | |
9. | Open Pre:MPa(Kqf/cm2) | |
10. | NOZZLE-HOLDER | |
11. | NOZZLE |
Scheme ###:
1. | [1] | 141054-7520 | PUMP HOUSING |
5. | [1] | 141176-3421 | PLUNGER-AND-BARREL ASSY |
7. | [2] | 141133-0500 | CAPSULE |
7. | [2] | 141133-0500 | CAPSULE |
8. | [2] | 141403-1300 | GASKET |
8. | [2] | 141403-1300 | GASKET |
12. | [1] | 141142-1421 | DELIVERY-VALVE ASSEMBLY |
12/1. | [1] | 141142-1401 | VALVE BODY |
12/2. | [1] | 141141-2100 | SEAT;D.V. |
13. | [1] | 141112-6400 | COMPRESSION SPRING |
17. | [1] | 141136-7500 | FITTING |
18. | [1] | 141117-8400 | FILLER PIECE |
20. | [1] | 141118-2000 | O-RING |
21. | [1] | 141119-3600 | FLANGE BUSHING |
22. | [6] | 141124-1300 | BLEEDER SCREW |
25. | [1] | 141482-9600 | O-RING |
25. | [1] | 141482-9600 | O-RING |
50. | [1] | 141215-5402 | COMPRESSION SPRING |
51. | [1] | 141216-1800 | SLOTTED WASHER |
52. | [1] | 141217-5500 | SLOTTED WASHER |
53. | [1] | 141218-7920 | GUIDE |
55. | [1] | 141220-1200 | LOCKING WASHER |
60. | [1] | 141244-9400 | CONTROL RACK |
77. | [1] | 141292-1500 | CONTROL SLEEVE |
81. | [1] | 141245-2000 | POINTER |
82/1. | [0] | 023500-6210 | PLAIN WASHER D11&6.4T1.5 |
82/1. | [0] | 029300-6010 | PLAIN WASHER D11&6.4T0.8 |
82/1. | [0] | 029300-6020 | PLAIN WASHER D11&6.4T0.35 |
83. | [1] | 020006-1440 | BLEEDER SCREW M6P1L14 |
110. | [1] | 141420-0800 | BLEEDER SCREW |
111. | [1] | 141421-0000 | GASKET |
160. | [1] | 141418-1400 | SET OF NUTS |
161. | [1] | 141107-0700 | GASKET |
162. | [1] | 141480-0900 | COVER |
163. | [1] | 373658-1400 | CAPSULE |
164. | [1] | 026510-1340 | GASKET D13.4&10.2T1 |
Include in #1:
101491-9043
as _
Include in #2:
104264-4044
as INJECTION-PUMP ASSEMBLY
Cross reference number
Zexel num
Bosch num
Firm num
Name
Information:
Table 1
Required Tools    
Tool     Part Number     Part Description     Qty    
A     380-5200     Tool Kit     1    
B     366-7782     Attenuator     1    Testing Procedure
Perform a "Manual Diesel Particulate Filter Regeneration" using the electronic service tool. If the "Manual Diesel Particulate Filter Regeneration" procedure follows the removal of excess oil from the exhaust system, proceed to Step 2.
Follow the procedure that is detailed by Step 1.b through to Step 1.m to clean oil from the exhaust system.
Remove excess oil from all pipes with a clean cloth.
Remove the DPF from the bracket for the clean emission module. Refer to Disassembly and Assembly, "Diesel Particulate Filter - Remove" for the correct procedure.
Use a suitable supporting device, position the DPF in a vertical position. Ensure that the inlet side of the DPF faces in a DOWNWARDS position.
Let the DPF drain overnight. The oil will collect inside the inlet face of the DPF. Position a suitable container under the inlet face of the DPF. Incline the inlet face of the DPF to drain the oil into the container.
If amount drained from DPF equals less than 1 L (0.26 US gal), proceed to Step 1.g. If amount is greater than 1 L (0.26 US gal), then the DPF should be replaced.
Remove excess oil from the inlet and outlet of the DPF with a clean cloth.
Install the DPF from the bracket for the clean emission module. Refer to Disassembly and Assembly, "Diesel Particulate Filter - Install" for the correct procedure.
Start the engine. Operate the engine a 100 percent throttle for a MINIMUM of 20 minutes. Do not operate the application under load at this time period.
After 20 minutes, use the electronic service tool to perform the "DPF Desulphation Procedure". The "DPF Desulphation Procedure" will last 60 minutes.
Once the "DPF Desulphation Procedure" has been completed, observe the soot load. If the soot load is at a value less than 80 percent, then the application can be returned to service.
Check the application for any signs of visible black smoke coming from the exhaust stack after the cleaning procedure has been completed. This could indicate a cracked DPF that will need to be replaced.Note: Black soot residue on the surface of the inside of the exhaust stack does not necessarily indicate a cracked DPF therefore should not be used in determining a problem with the DPF.
If white smoke does not dissipate, contact the Technical Communicator at a Caterpillar dealer. For further assistance, the Technical Communicator can confer with the Dealer Solutions Network.
After the manual DPF regeneration is complete, operate the engine at 1800 rpm for a MINIMUM of 20 minutes to stabilize the DPF temperatures.Note: The engine must maintain a steady speed for the entire duration of the test.
Hot engine components can cause injury from burns. Before performing maintenance on the engine, allow the engine and the components to cool.
Illustration 1 g02597531
Typical example (1) DPF Outlet Cap (2) Filter Paper (3) Hose Assembly (4) Air Pump
Illustration