Information fuel-injection pump
BOSCH
9 410 617 818
9410617818
ZEXEL
104262-5000
1042625000
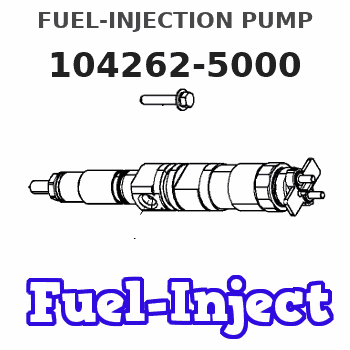
Rating:
Components :
0. | INJECTION-PUMP ASSEMBLY | 104262-5000 |
1. | _ | |
2. | FUEL INJECTION PUMP | |
3. | NUMBER PLATE | |
4. | _ | |
5. | CAPSULE | |
6. | ADJUSTING DEVICE | |
7. | NOZZLE AND HOLDER ASSY | |
8. | Nozzle and Holder | |
9. | Open Pre:MPa(Kqf/cm2) | |
10. | NOZZLE-HOLDER | |
11. | NOZZLE |
Scheme ###:
5. | [1] | 141176-2320 | PLUNGER-AND-BARREL ASSY |
7. | [1] | 141133-0500 | CAPSULE |
8. | [1] | 141403-0400 | GASKET |
12. | [1] | 141140-8620 | DELIVERY-VALVE ASSEMBLY |
17. | [1] | 141136-5200 | FITTING |
20. | [1] | 141118-2000 | O-RING |
21. | [1] | 141119-3600 | FLANGE BUSHING |
22. | [6] | 141124-1300 | BLEEDER SCREW |
25. | [1] | 141482-9600 | O-RING |
50. | [1] | 141215-5401 | COMPRESSION SPRING |
51. | [1] | 141216-1800 | SLOTTED WASHER |
52. | [1] | 141217-5500 | SLOTTED WASHER |
53. | [1] | 141218-7920 | GUIDE |
55. | [1] | 141220-1200 | LOCKING WASHER |
60. | [1] | 141244-5600 | CONTROL RACK |
77. | [1] | 141241-7200 | CONTROL SLEEVE |
81. | [1] | 141245-2900 | POINTER |
82/1. | [0] | 023500-6210 | PLAIN WASHER D11&6.4T1.5 |
82/1. | [0] | 029300-6010 | PLAIN WASHER D11&6.4T0.8 |
82/1. | [0] | 029300-6020 | PLAIN WASHER D11&6.4T0.35 |
83. | [1] | 020006-1440 | BLEEDER SCREW M6P1L14 |
93. | [2] | 141402-2220 | EYE BOLT |
93. | [2] | 141402-2220 | EYE BOLT |
94. | [4] | 141403-0600 | GASKET |
94. | [4] | 141403-0600 | GASKET |
110. | [1] | 141420-0800 | BLEEDER SCREW |
111. | [1] | 141421-0000 | GASKET |
160. | [1] | 141418-1400 | SET OF NUTS |
161. | [1] | 141107-0700 | GASKET |
162. | [1] | 141480-0900 | COVER |
164. | [1] | 373658-1400 | CAPSULE |
165. | [1] | 141107-0500 | GASKET |
Include in #1:
101491-9034
as _
Include in #2:
104262-5000
as INJECTION-PUMP ASSEMBLY
Cross reference number
Zexel num
Bosch num
Firm num
Name
104262-5000
9 410 617 818
FUEL-INJECTION PUMP
* K
* K
Information:
Table 1
S O S Oil Analysis Guidelines    
Test Parameter     Guideline    
Oxidation     (1)    
Soot     (1)    
Sulfation     (1)    
Wear Metals     Trend Analysis and Cat Wear Table (1) norms    
Water     0.5% maximum    
Glycol     0%    
Fuel Dilution     Based on viscosity (1) and GC (2) fuel dilution in excess of 4%    
Viscosity "ASTM D445" measured at 100° C (212° F)     +/-3 centistokes (cSt) change from new oil viscosity.    
( 1 ) Acceptable values for these parameters are proprietary to the S O S oil analysis program.
( 2 ) Gas ChromatographConsult your Caterpillar dealer for complete information and assistance about the S O S oil analysis program.Obtaining S O S Oil Samples
Before you obtain an S O S oil sample, operate the engine until the oil is warm and the oil is well circulated. Then obtain the S O S oil sample.In order to obtain a good oil sample, do not take the oil sample from the drain stream. The drain stream method can allow a stream of dirty oil from the bottom of the compartment to contaminate the sample. Likewise, never dip an oil sample from an oil container or pour a sample from a used filter.There are two acceptable ways to obtain S O S oil samples. The following methods are listed in the order that is preferred:
Use an in-line sampling valve on the pressurized oil manifold.
Use a sampling gun (vacuum pump) that is inserted into the sump.Use of the in-line sampling valve is the preferred method. This method provides samples that are less likely to be contaminated. In order to obtain an oil sample from the engine, it may be necessary to increase the engine's speed. Normally, the oil sample is taken at low idle. If the flow rate is too low, increase engine speed to high idle in order to obtain the oil sample.
Do not use the same vacuum sampling pump for extracting oil samples that is used for extracting coolant samples.A small residue of either type sample may remain in the pump and may cause a false positive analysis for the sample being taken.Always use a separate pump for oil sampling and a separate pump for coolant sampling.Failure to do so may cause a false analysis which could lead to customer and dealer concerns.
Oil Sampling Interval
Take the oil samples as close as possible to the standard intervals. In order to receive the full value from S O S oil analysis, you must establish a consistent trend of data. In order to establish pertinent history of data, perform consistent oil samplings that are evenly spaced.
Table 2
Compartment     Engine    
Recommended Sampling Interval    
24140 kilometers (15000 miles)
(1) (2)    
Sampling Valve     Yes    
Oil Type     DEO, DEO-ULS    
Recommended Oil Change Interval     (3)    
( 1 ) Under certain conditions, the Caterpillar dealer or the Operation and Maintenance Manual may allow a longer
Have questions with 104262-5000?
Group cross 104262-5000 ZEXEL
104262-5000
9 410 617 818
FUEL-INJECTION PUMP