Information fuel-injection pump
BOSCH
9 410 617 714
9410617714
ZEXEL
104134-3040
1041343040
ISHIKAWAJIMA-H
131017670
131017670
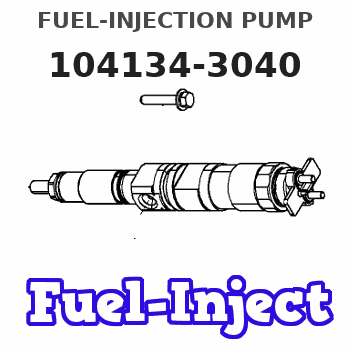
Rating:
Compare Prices: .
As an associate, we earn commssions on qualifying purchases through the links below
Original Fuel Injection Pump Compatible With Kubota Perkins 131017670 104134-3040 9410617714 Excavator Engine Replacement Parts
YERCBX Enhance the engine's power output || Low-noise operation: Optimized internal structure and materials, resulting in low noise during operation || The key components have excellent wear resistance, extending the overall service life || Integrated design: Compact structure, small space occupation, and convenient for vehicle installation and layout. || Easy maintenance: The design is reasonable, and daily inspection and maintenance operations are simple, saving time
YERCBX Enhance the engine's power output || Low-noise operation: Optimized internal structure and materials, resulting in low noise during operation || The key components have excellent wear resistance, extending the overall service life || Integrated design: Compact structure, small space occupation, and convenient for vehicle installation and layout. || Easy maintenance: The design is reasonable, and daily inspection and maintenance operations are simple, saving time
$892.68
24 Dec 2024
CN: GSHLGAO Flagship sto
New Fuel Injection Pump Fits for Perkins Engine Parts 131017670 104134-3040 9410617714
GSHLGAO Part Name: Fuel Injection Pump || Part Number:1041343040 9410617714 131017670 104134-3040 || Designed specifically for Perkins engines, this application offers tailored solutions for optimal performance and compatibility. Emphasizing quality and reliability, it ensures efficient operation and long-lasting durability. Ideal for industrial, commercial, or residential use, it maximizes the potential of Perkins engines for peak performance. || Notification-The application information provided is for guidance purposes only. It is recommended to verify the part number and conduct a comparison with the old parts before making a purchase. Should you have any inquiries, please do not hesitate to contact us. || Premium Selection-This item boasts consistent performance, exceptional reliability, effortless installation, and rapid response times.
GSHLGAO Part Name: Fuel Injection Pump || Part Number:1041343040 9410617714 131017670 104134-3040 || Designed specifically for Perkins engines, this application offers tailored solutions for optimal performance and compatibility. Emphasizing quality and reliability, it ensures efficient operation and long-lasting durability. Ideal for industrial, commercial, or residential use, it maximizes the potential of Perkins engines for peak performance. || Notification-The application information provided is for guidance purposes only. It is recommended to verify the part number and conduct a comparison with the old parts before making a purchase. Should you have any inquiries, please do not hesitate to contact us. || Premium Selection-This item boasts consistent performance, exceptional reliability, effortless installation, and rapid response times.
You can express buy:
Components :
0. | INJECTION-PUMP ASSEMBLY | 104134-3040 |
1. | _ | |
2. | FUEL INJECTION PUMP | |
3. | NUMBER PLATE | |
4. | _ | |
5. | CAPSULE | |
6. | ADJUSTING DEVICE | |
7. | NOZZLE AND HOLDER ASSY | 105148-1170 |
8. | Nozzle and Holder | |
9. | Open Pre:MPa(Kqf/cm2) | 14.7{150} |
10. | NOZZLE-HOLDER | 105078-0100 |
11. | NOZZLE | 105007-1170 |
Scheme ###:
5. | [3] | 140154-9720 | PLUNGER-AND-BARREL ASSY |
12. | [3] | 140110-3620 | DELIVERY-VALVE ASSEMBLY |
13. | [3] | 140112-2900 | COMPRESSION SPRING |
16. | [3] | 140115-1400 | GASKET |
17. | [3] | 140116-7520 | FITTING |
20. | [3] | 140118-0300 | O-RING |
30. | [3] | 140131-0521 | FLANGE BUSHING |
32. | [6] | 140118-0200 | O-RING |
37. | [6] | 140124-0200 | BLEEDER SCREW |
40. | [3] | 140200-2620 | TAPPET |
44. | [3] | 140212-0300 | BEARING PIN |
45. | [1] | 140213-1400 | LOCKING WASHER |
50. | [3] | 140215-1900 | COMPRESSION SPRING |
51. | [3] | 140216-0800 | SLOTTED WASHER |
52. | [3] | 140217-2200 | SLOTTED WASHER |
53/1. | [1] | 140217-5000 | PLATE D19T2.60 |
53/1. | [1] | 140217-5100 | PLATE D19T2.65 |
53/1. | [1] | 140217-5200 | PLATE D19T2.70 |
53/1. | [1] | 140217-5300 | PLATE D19T2.75 |
53/1. | [1] | 140217-5400 | PLATE D19T2.80 |
53/1. | [1] | 140217-5500 | PLATE D19T2.85 |
53/1. | [1] | 140217-5600 | PLATE D19T2.90 |
53/1. | [1] | 140217-5700 | PLATE D19T2.95 |
53/1. | [1] | 140217-5800 | PLATE D19T3.00 |
53/1. | [1] | 140217-5900 | PLATE D19T3.05 |
53/1. | [1] | 140217-6000 | PLATE D19T3.10 |
53/1. | [1] | 140217-6100 | PLATE D19T3.15 |
53/1. | [1] | 140217-6200 | PLATE D19T3.20 |
53/1. | [1] | 140217-6300 | PLATE D19T3.25 |
53/1. | [1] | 140217-6400 | PLATE D19T3.30 |
53/1. | [1] | 140217-6500 | PLATE D19T3.35 |
53/1. | [1] | 140217-6600 | PLATE D19T3.40 |
53/1. | [1] | 140217-6700 | PLATE D19T3.45 |
53/1. | [1] | 140217-6800 | PLATE D19T3.50 |
53/1. | [1] | 140217-6900 | PLATE D19T3.55 |
53/1. | [1] | 140217-7000 | PLATE D19T3.60 |
53/1. | [1] | 140217-7100 | PLATE D19T3.65 |
53/1. | [1] | 140217-7200 | PLATE D19T3.70 |
53/1. | [1] | 140217-7300 | PLATE D19T3.75 |
53/1. | [1] | 140217-7400 | PLATE D19T3.80 |
53/1. | [1] | 140217-7500 | PLATE D19T3.85 |
53/1. | [1] | 140217-7600 | PLATE D19T3.90 |
53/1. | [1] | 140217-7700 | PLATE D19T3.95 |
53/1. | [1] | 140217-7800 | PLATE D19T4.00 |
53/1. | [1] | 140217-7900 | PLATE D19T4.05 |
53/1. | [1] | 140217-8000 | PLATE D19T4.10 |
53/1. | [1] | 140253-2000 | PLATE |
53/1. | [1] | 140253-2100 | PLATE |
53/1. | [1] | 140253-2200 | PLATE |
53/1. | [1] | 140253-2300 | PLATE |
53/1. | [1] | 140253-2400 | PLATE |
53/1. | [1] | 140253-2500 | PLATE |
53/1. | [1] | 140253-2600 | PLATE |
53/1. | [1] | 140253-2700 | PLATE |
53/1. | [1] | 140253-2800 | PLATE |
53/1. | [1] | 140253-2900 | PLATE |
53/1. | [1] | 140253-3000 | PLATE |
53/1. | [1] | 140253-3100 | PLATE |
53/1. | [1] | 140253-3200 | PLATE |
53/1. | [1] | 140253-3300 | PLATE |
53/1. | [1] | 140253-3400 | PLATE |
53/1. | [1] | 140253-3500 | PLATE |
53/1. | [1] | 140253-3600 | PLATE |
53/1. | [1] | 140253-3700 | PLATE |
53/1. | [1] | 140253-3800 | PLATE |
53/1. | [1] | 140253-3900 | PLATE |
53/1. | [1] | 140253-4000 | PLATE |
53/1. | [1] | 140253-4100 | PLATE |
53/1. | [1] | 140253-4200 | PLATE |
53/1. | [1] | 140253-4300 | PLATE |
53/1. | [1] | 140253-4400 | PLATE |
53/1. | [1] | 140253-4500 | PLATE |
53/1. | [1] | 140253-4600 | PLATE |
53/1. | [1] | 140253-4700 | PLATE |
53/1. | [1] | 140253-4800 | PLATE |
53/1. | [1] | 140253-4900 | PLATE |
60. | [1] | 140243-5520 | CONTROL RACK |
77. | [3] | 140241-2700 | CONTROL SLEEVE |
92. | [1] | 029711-2050 | INLET UNION |
93. | [1] | 140402-1300 | EYE BOLT |
94. | [2] | 026512-1540 | GASKET D15.4&12.2T1.50 |
Include in #1:
106673-2120
as _
Include in #2:
104134-3040
as INJECTION-PUMP ASSEMBLY
Cross reference number
Zexel num
Bosch num
Firm num
Name
104134-3040
131017670 ISHIKAWAJIMA-H
FUEL-INJECTION PUMP
K 23AC FUEL INJECTION PUMP PFR-3KX PFR
K 23AC FUEL INJECTION PUMP PFR-3KX PFR
104134-3040
131017670 ISHIKAWAJIMA-S
FUEL-INJECTION PUMP
K 23AC FUEL INJECTION PUMP PFR-3KX PFR
K 23AC FUEL INJECTION PUMP PFR-3KX PFR
Information:
T-T-T Procedure
A torque-turn-tighten (T-T-T) procedure is used in many specifications and instructions.1. Clean the bolt and nut threads.2. Put lubricant on the threads and the seat face of the bolt and the nut.3. Turn the bolt or the nut tight according to the torque specification.4. Put a location mark on the part and on the bolt or the nut.5. Turn the bolt or the nut tighter the amount of degrees according to the specifications. The side of a nut or bolt head can be used for reference if a mark can not be put on. Torque Wrench Extension
When a torque wrench extension is used with a torque wrench, the torque indication on the torque wrench will be less than the real torque.
TORQUE WRENCH WITH TORQUE WRENCH EXTENSION.
E: Torque wrench drive axis-to-torque wrench extension drive axis. W: Mark on handle-to-torque wrench drive axis.1. Put a mark on the handle. Measure the handle from the mark to the axis of the torque wrench drive (W).2. Measure the torque wrench extension from the torque wrench drive to the axis of the torque wrench extension drive (E).3. To get correct torque indication (TI) when the real torque (RT) is known: Example: W = 304.8 mm (12 in.); E = 65.0 mm (2.56 in.); RT (from specifications) = 170 N m (125 lb. ft.). 4. Hold the torque wrench handle with the longest finger of the hand over the mark on the handle to get the real torque (RT) with low torque indication (TI) on the torque wrench.Locks
Flat metal locks must be installed properly to be effective. Bend one end of the lock around the edge of the part. Bend the other end against one flat surface of the nut or bolt head.Always install new locks in compartments which house moving parts.If lockwashers are installed on housings made of aluminum, use a flat washer between the lockwasher and the housing. Lines And Wires
When removing or disconnecting a group of lines or wires, tag each one to assure proper assembly.Lubrication
Where applicable, fill the compartments of the components serviced with the amount, type and grade of lubricant recommended in the Lubrication and Maintenance Guide.Rust Preventive Compound
Clean the rust preventive compound from all machined surfaces of new parts before installing them.Shims
When shims are removed, tie them together and identify them as to location. Keep shims clean and flat until they are reinstalled.Bearings
Anti-Friction Bearings
When an anti-friction bearing is removed, cover it to keep out dirt and abrasives. Wash bearings in nonflammable cleaning solution and allow them to drain dry. The bearing may be dried with compressed air, but DO NOT SPIN THE BEARING. Discard the bearings if the races and balls or rollers are pitted, scored or burned. If the bearing is serviceable, coat it with oil and wrap it in clean paper. Do not unwrap new bearings until time of installation.The life of an anti-friction bearing will be shortened if not properly lubricated.Double Row, Tapered Roller
Double row, tapered roller bearings are precision fit during manufacture and
A torque-turn-tighten (T-T-T) procedure is used in many specifications and instructions.1. Clean the bolt and nut threads.2. Put lubricant on the threads and the seat face of the bolt and the nut.3. Turn the bolt or the nut tight according to the torque specification.4. Put a location mark on the part and on the bolt or the nut.5. Turn the bolt or the nut tighter the amount of degrees according to the specifications. The side of a nut or bolt head can be used for reference if a mark can not be put on. Torque Wrench Extension
When a torque wrench extension is used with a torque wrench, the torque indication on the torque wrench will be less than the real torque.
TORQUE WRENCH WITH TORQUE WRENCH EXTENSION.
E: Torque wrench drive axis-to-torque wrench extension drive axis. W: Mark on handle-to-torque wrench drive axis.1. Put a mark on the handle. Measure the handle from the mark to the axis of the torque wrench drive (W).2. Measure the torque wrench extension from the torque wrench drive to the axis of the torque wrench extension drive (E).3. To get correct torque indication (TI) when the real torque (RT) is known: Example: W = 304.8 mm (12 in.); E = 65.0 mm (2.56 in.); RT (from specifications) = 170 N m (125 lb. ft.). 4. Hold the torque wrench handle with the longest finger of the hand over the mark on the handle to get the real torque (RT) with low torque indication (TI) on the torque wrench.Locks
Flat metal locks must be installed properly to be effective. Bend one end of the lock around the edge of the part. Bend the other end against one flat surface of the nut or bolt head.Always install new locks in compartments which house moving parts.If lockwashers are installed on housings made of aluminum, use a flat washer between the lockwasher and the housing. Lines And Wires
When removing or disconnecting a group of lines or wires, tag each one to assure proper assembly.Lubrication
Where applicable, fill the compartments of the components serviced with the amount, type and grade of lubricant recommended in the Lubrication and Maintenance Guide.Rust Preventive Compound
Clean the rust preventive compound from all machined surfaces of new parts before installing them.Shims
When shims are removed, tie them together and identify them as to location. Keep shims clean and flat until they are reinstalled.Bearings
Anti-Friction Bearings
When an anti-friction bearing is removed, cover it to keep out dirt and abrasives. Wash bearings in nonflammable cleaning solution and allow them to drain dry. The bearing may be dried with compressed air, but DO NOT SPIN THE BEARING. Discard the bearings if the races and balls or rollers are pitted, scored or burned. If the bearing is serviceable, coat it with oil and wrap it in clean paper. Do not unwrap new bearings until time of installation.The life of an anti-friction bearing will be shortened if not properly lubricated.Double Row, Tapered Roller
Double row, tapered roller bearings are precision fit during manufacture and