Information fuel-injection pump
BOSCH
9 410 613 104
9410613104
ZEXEL
103067-8040
1030678040
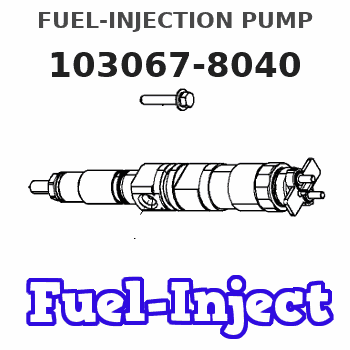
Rating:
Scheme ###:
1. | [1] | 133050-8520 | PUMP HOUSING |
1/30. | [3] | 029040-6020 | STUD |
1/35A. | [1] | 132400-0200 | ADAPTOR |
2. | [1] | 133010-5420 | COVER |
2/2. | [1] | 133011-0900 | GASKET |
3. | [8] | 020106-1240 | BLEEDER SCREW M6P1.0L12 |
6. | [4] | 013020-6020 | UNION NUT M6P1H5 |
6. | [4] | 013020-6020 | UNION NUT M6P1H5 |
7. | [1] | 133021-0300 | COVER |
8. | [2] | 014110-6410 | LOCKING WASHER |
10. | [2] | 139006-0300 | STUD |
15. | [1] | 133030-0520 | LEVEL INDICATOR |
16. | [6] | 133034-0100 | CAPSULE |
20. | [3] | 014110-6440 | LOCKING WASHER |
21. | [3] | 013020-6040 | UNION NUT M6P1H5 |
23. | [1] | 133041-0400 | GASKET |
24. | [6] | 029633-4010 | O-RING |
30. | [6] | 133151-6220 | PLUNGER-AND-BARREL ASSY |
31. | [6] | 133106-0500 | CAPSULE |
32. | [6] | 026510-1340 | GASKET D13.4&10.2T1 |
36. | [6] | 133110-2620 | DELIVERY-VALVE ASSEMBLY |
37. | [6] | 134112-0000 | COILED SPRING |
40. | [6] | 133115-1400 | GASKET D20.0&10.5T0.50 |
41. | [6] | 133116-3300 | FITTING |
42. | [6] | 029632-5030 | O-RING |
43. | [6] | 133117-0200 | FILLER PIECE |
45. | [4] | 133122-1420 | PLATE |
55. | [6] | 133200-1120 | TAPPET |
55/2. | [1] | 133201-0101 | UNION NUT |
55/3. | [1] | 133202-0100 | HEXAGON SCREW |
55/4. | [1] | 133203-0400 | BEARING PIN |
55/5. | [1] | 133204-0300 | ROLLER |
55/6. | [1] | 133205-0300 | BUSHING |
57. | [6] | 133210-0300 | FLAT-HEAD SCREW |
58. | [6] | 026510-1340 | GASKET D13.4&10.2T1 |
61. | [6] | 133215-0600 | COMPRESSION SPRING |
62. | [6] | 133216-0100 | SLOTTED WASHER |
63. | [6] | 133217-0300 | SLOTTED WASHER |
67. | [1] | 133256-1600 | CONTROL RACK |
68. | [1] | 133226-0600 | FLAT-HEAD SCREW |
69. | [1] | 023700-8120 | TAB WASHER |
76. | [6] | 133240-0100 | PINION |
77. | [6] | 133241-0200 | CONTROL SLEEVE |
78. | [6] | 131242-0100 | FLAT-HEAD SCREW |
81A. | [1] | 133245-0400 | POINTER |
82A/1. | [0] | 029300-5020 | PLAIN WASHER D10&5.1T1.5 |
82A/1. | [0] | 029310-5080 | SHIM D10&5T0.2 |
82A/1. | [0] | 029310-5090 | SHIM D10&5.1T0.5 |
82A/1. | [0] | 029310-5110 | SHIM D10&5.1T1 |
83A. | [1] | 021305-0940 | FLAT-HEAD SCREW |
90. | [1] | 133371-1800 | CAMSHAFT |
91. | [1] | 016603-3230 | BEARING PLATE |
91A. | [1] | 016603-3230 | BEARING PLATE |
92. | [1] | 133302-0200 | SPACER RING |
92A. | [1] | 133302-0200 | SPACER RING |
93/1. | [0] | 029313-0010 | SHIM D45&30.2T0.1 |
93/1. | [0] | 029313-0020 | SHIM D45&30.2T0.12 |
93/1. | [0] | 029313-0030 | SHIM D45&30.2T0.14 |
93/1. | [0] | 029313-0040 | SHIM D45&30.2T0.16 |
93/1. | [0] | 029313-0050 | SHIM D45&30.2T0.18 |
93/1. | [0] | 029313-0060 | SHIM D45&30.2T0.5 |
93/1. | [0] | 029313-0070 | SHIM D45&30.2T1 |
93A/1. | [0] | 029313-0010 | SHIM D45&30.2T0.1 |
93A/1. | [0] | 029313-0020 | SHIM D45&30.2T0.12 |
93A/1. | [0] | 029313-0030 | SHIM D45&30.2T0.14 |
93A/1. | [0] | 029313-0040 | SHIM D45&30.2T0.16 |
93A/1. | [0] | 029313-0050 | SHIM D45&30.2T0.18 |
93A/1. | [0] | 029313-0060 | SHIM D45&30.2T0.5 |
93A/1. | [0] | 029313-0070 | SHIM D45&30.2T1 |
95. | [1] | 133305-0900 | BEARING SHELL |
96. | [2] | 010208-4040 | HEX-SOCKET-HEAD CAP SCREW |
97. | [2] | 023500-8120 | PLAIN WASHER |
98. | [2] | 023650-8310 | LOCKING WASHER |
99. | [2] | 029630-9020 | O-RING |
100A. | [1] | 029623-0010 | PACKING RING |
101A. | [1] | 133316-3000 | COVER |
104A. | [6] | 010208-2040 | HEX-SOCKET-HEAD CAP SCREW |
105A. | [6] | 014110-8440 | LOCKING WASHER |
107A. | [1] | 156635-4800 | COUPLING PLATE |
108A. | [1] | 029637-6010 | O-RING |
110A. | [1] | 156023-1600 | UNION NUT |
111A. | [1] | 014112-0440 | LOCKING WASHER |
112A. | [1] | 025806-2210 | WOODRUFF KEY |
116A. | [1] | 029701-4310 | INLET UNION |
117A. | [1] | 029731-4170 | EYE BOLT |
118A. | [2] | 026514-1840 | GASKET D17.9&14.2T1 |
121. | [1] | 029701-0260 | INLET UNION |
122. | [2] | 026510-1340 | GASKET D13.4&10.2T1 |
123. | [1] | 131456-2120 | DRAINAGE PIPE |
130. | [1] | 131423-0200 | ADAPTOR |
130A. | [1] | 131420-0420 | BLEEDER SCREW |
131. | [1] | 131424-1420 | OVER FLOW VALVE |
132. | [1] | 026512-1540 | GASKET D15.4&12.2T1.50 |
132A. | [1] | 026512-1540 | GASKET D15.4&12.2T1.50 |
133. | [2] | 029341-4010 | GASKET D20&14.2T1.5 |
145. | [1] | 155406-0220 | AIR FILTER |
146. | [1] | 026512-1540 | GASKET D15.4&12.2T1.50 |
152. | [1] | 133430-0300 | EYE BOLT |
153. | [1] | 133431-1320 | PIPE |
154. | [2] | 026516-2040 | GASKET D19.9&16.2T1 |
156. | [1] | 029111-0010 | CAPSULE |
158. | [1] | 026510-1340 | GASKET D13.4&10.2T1 |
Cross reference number
Zexel num
Bosch num
Firm num
Name
Information:
Storage Procedure
When a generator is in storage for any length of time, moisture condenses in the windings. Minimize the condensation by use of a dry storage space and space heaters. Refer to step 2 belowIf a brush-type generator (SRCR) is to be in storage for a year or more, lift the brushes off the slip ring to prevent damage to the slip ring by chemical action.After Storage
Test the main stator windings with a megohmmeter in the following situations: 1. Before initial startup of generator set.2. Every 3 months* if generator is operating in a humid environment.3. If generator has not been run under load for 3 months* or more.*This is a guideline only. It may be necessary to megger more frequently if environment is extremely humid, salty or if the last megger test was close to 1 megohm.The megohmmeter test is described in Service Manuals SENR2180 or SENR7968. A reading of 1 meghom or less indicates that the winding has absorbed too much moisture.To Remove Moisture
To remove moisture caused by high humidity, use one of the following methods to make the generator dry:1. Energize space heaters in generator if so equipped.2. Put the generator in an oven at a temperature of not more than 85°C (185°F) for four hours.
If an oven is used for drying, use a forced air type rather than a radiant type. Radiant ovens can cause localized overheating.
3. Space heaters of the same type used in marine applications, can be installed on generators. (See the Parts Book.) These heaters heat the windings to remove moisture and should be connected at all times in high humidity conditions whenever the generator is not running.4. Use a canvas enclosure around the generator and heating lamps to increase the temperature. Make an opening in the top for release of moisture.5. Send a low voltage current through the windings to increase the temperature of the windings. Do not exceed 85°C (185°F).If the megohmmeter test reads under 1 megohm after the drying or if it goes below 1 megohm shortly after drying, contact your Caterpillar dealer. The insulation has deteriorated and should be reconditioned.
When a generator is in storage for any length of time, moisture condenses in the windings. Minimize the condensation by use of a dry storage space and space heaters. Refer to step 2 belowIf a brush-type generator (SRCR) is to be in storage for a year or more, lift the brushes off the slip ring to prevent damage to the slip ring by chemical action.After Storage
Test the main stator windings with a megohmmeter in the following situations: 1. Before initial startup of generator set.2. Every 3 months* if generator is operating in a humid environment.3. If generator has not been run under load for 3 months* or more.*This is a guideline only. It may be necessary to megger more frequently if environment is extremely humid, salty or if the last megger test was close to 1 megohm.The megohmmeter test is described in Service Manuals SENR2180 or SENR7968. A reading of 1 meghom or less indicates that the winding has absorbed too much moisture.To Remove Moisture
To remove moisture caused by high humidity, use one of the following methods to make the generator dry:1. Energize space heaters in generator if so equipped.2. Put the generator in an oven at a temperature of not more than 85°C (185°F) for four hours.
If an oven is used for drying, use a forced air type rather than a radiant type. Radiant ovens can cause localized overheating.
3. Space heaters of the same type used in marine applications, can be installed on generators. (See the Parts Book.) These heaters heat the windings to remove moisture and should be connected at all times in high humidity conditions whenever the generator is not running.4. Use a canvas enclosure around the generator and heating lamps to increase the temperature. Make an opening in the top for release of moisture.5. Send a low voltage current through the windings to increase the temperature of the windings. Do not exceed 85°C (185°F).If the megohmmeter test reads under 1 megohm after the drying or if it goes below 1 megohm shortly after drying, contact your Caterpillar dealer. The insulation has deteriorated and should be reconditioned.