Information fuel-injection pump
BOSCH
9 410 613 103
9410613103
ZEXEL
103067-1001
1030671001
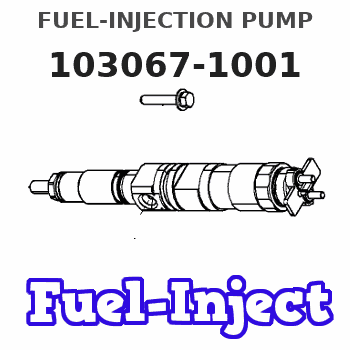
Rating:
Scheme ###:
1. | [1] | 133051-6721 | PUMP HOUSING |
1/35. | [1] | 029112-4010 | CAPSULE |
1/35A. | [1] | 029112-4010 | CAPSULE |
1/43. | [1] | 131420-0420 | BLEEDER SCREW |
2. | [1] | 133010-7600 | COVER |
3. | [16] | 020106-1440 | BLEEDER SCREW M6P1.0L14 |
4. | [1] | 133011-2000 | GASKET |
16. | [6] | 133034-0100 | CAPSULE |
24. | [6] | 029633-4010 | O-RING |
30. | [6] | 133151-9220 | PLUNGER-AND-BARREL ASSY |
31. | [6] | 133106-0800 | CAPSULE |
32. | [6] | 026510-1340 | GASKET D13.4&10.2T1 |
36. | [6] | 133110-3520 | DELIVERY-VALVE ASSEMBLY |
37. | [6] | 134112-0000 | COILED SPRING |
40. | [6] | 133115-1400 | GASKET D20.0&10.5T0.50 |
41. | [6] | 133116-3820 | FITTING |
42. | [6] | 029632-5030 | O-RING |
43. | [6] | 133117-0200 | FILLER PIECE |
45. | [4] | 133122-1420 | PLATE |
55. | [6] | 133200-1920 | TAPPET |
55/2. | [1] | 133201-0300 | UNION NUT |
55/3. | [1] | 133202-0400 | HEXAGON SCREW |
55/4. | [1] | 133203-0400 | BEARING PIN |
55/5. | [1] | 133204-0600 | ROLLER |
55/6. | [1] | 133205-0300 | BUSHING |
57. | [6] | 133210-0400 | FLAT-HEAD SCREW |
58. | [6] | 026510-1340 | GASKET D13.4&10.2T1 |
61. | [6] | 133215-0600 | COMPRESSION SPRING |
62. | [6] | 133216-0100 | SLOTTED WASHER |
63. | [6] | 133217-0300 | SLOTTED WASHER |
67. | [1] | 133256-5600 | CONTROL RACK |
68. | [1] | 133226-0700 | FLAT-HEAD SCREW |
69. | [1] | 133516-0400 | TAB WASHER |
76. | [6] | 133240-0100 | PINION |
77. | [6] | 133241-0200 | CONTROL SLEEVE |
78. | [6] | 131242-0100 | FLAT-HEAD SCREW |
90. | [1] | 133371-2100 | CAMSHAFT |
91. | [1] | 016603-3230 | BEARING PLATE |
91A. | [1] | 016603-3230 | BEARING PLATE |
92. | [1] | 133302-0200 | SPACER RING |
92A. | [1] | 133302-0200 | SPACER RING |
93/1. | [0] | 029313-0010 | SHIM D45&30.2T0.1 |
93/1. | [0] | 029313-0020 | SHIM D45&30.2T0.12 |
93/1. | [0] | 029313-0030 | SHIM D45&30.2T0.14 |
93/1. | [0] | 029313-0040 | SHIM D45&30.2T0.16 |
93/1. | [0] | 029313-0050 | SHIM D45&30.2T0.18 |
93/1. | [0] | 029313-0060 | SHIM D45&30.2T0.5 |
93/1. | [0] | 029313-0070 | SHIM D45&30.2T1 |
93A/1. | [0] | 029313-0010 | SHIM D45&30.2T0.1 |
93A/1. | [0] | 029313-0020 | SHIM D45&30.2T0.12 |
93A/1. | [0] | 029313-0030 | SHIM D45&30.2T0.14 |
93A/1. | [0] | 029313-0040 | SHIM D45&30.2T0.16 |
93A/1. | [0] | 029313-0050 | SHIM D45&30.2T0.18 |
93A/1. | [0] | 029313-0060 | SHIM D45&30.2T0.5 |
93A/1. | [0] | 029313-0070 | SHIM D45&30.2T1 |
95. | [1] | 133305-0900 | BEARING SHELL |
96. | [2] | 010208-4040 | HEX-SOCKET-HEAD CAP SCREW |
97. | [2] | 023500-8120 | PLAIN WASHER |
98. | [2] | 023650-8310 | LOCKING WASHER |
99. | [2] | 029630-9020 | O-RING |
100. | [1] | 139634-0200 | PACKING RING |
100A. | [1] | 029622-5010 | PACKING RING |
101. | [1] | 133316-3000 | COVER |
101A. | [1] | 133316-0900 | COVER |
102. | [1] | 134563-2500 | SLIDING PIECE |
104. | [6] | 010208-2040 | HEX-SOCKET-HEAD CAP SCREW |
104A. | [3] | 010208-2040 | HEX-SOCKET-HEAD CAP SCREW |
105. | [6] | 014110-8440 | LOCKING WASHER |
105A. | [3] | 014110-8440 | LOCKING WASHER |
107. | [1] | 156638-5600 | COUPLING PLATE |
108. | [1] | 029637-6010 | O-RING |
108A. | [1] | 029637-6010 | O-RING |
110. | [1] | 023012-0040 | UNION NUT M20P1.5H16 |
111. | [1] | 014112-0440 | LOCKING WASHER |
112. | [1] | 025806-2210 | WOODRUFF KEY |
113A. | [1] | 133328-0820 | CAP |
114A. | [3] | 021308-3520 | FLAT-HEAD SCREW |
135. | [1] | 029731-4170 | EYE BOLT |
135A. | [1] | 131424-1420 | OVER FLOW VALVE |
136. | [2] | 026514-1840 | GASKET D17.9&14.2T1 |
136A. | [2] | 026514-1840 | GASKET D17.9&14.2T1 |
137A. | [1] | 027114-1040 | INLET UNION |
156. | [1] | 029731-4680 | EYE BOLT |
158. | [2] | 026514-1840 | GASKET D17.9&14.2T1 |
165. | [1] | 155404-1400 | CAP |
217. | [1] | 139812-2300 | EYE BOLT |
218. | [1] | 029701-2020 | INLET UNION |
219. | [2] | 026512-1540 | GASKET D15.4&12.2T1.50 |
305. | [1] | 026524-2940 | GASKET D28.9&24.3T2 |
306. | [1] | 133510-2700 | CAP |
307. | [1] | 133510-2800 | COVER |
308. | [1] | 029632-6030 | O-RING |
Cross reference number
Zexel num
Bosch num
Firm num
Name
Information:
Storage Procedure
1. Clean the outside of the engine and repaint areas that have paint damage with a good quality paint.2. Remove the batteries and use them in some other place or put them in storage where they can be checked and electrically charged again when needed. If the batteries are not removed, wash the tops. Put an electrical charge to the battery to a specific gravity of 1.275. Disconnect the battery terminals. Put a plastic cover over the battery.3. Loosen all fan, alternator belts, etc. Attach a tag to indicate what work has been done.4. Put a waterproof cover over engines with enclosures stored outdoors. Make the cover tight, but loose enough to allow air to circulate around the engine to prevent damage to exposed metal parts from condensation. Remove the waterproof cover every two or three months and check the engine for corrosion. If the engine has signs of corrosion at the check period, follow the protection procedure again. To operate the engine, it is not necessary to remove the preservative oil mixture. If a compartment under protection of VCI vapors is opened, put more VCI mixture in to make up for the vapor loss. Install all covers and/or put tape over all openings, air intake, exhaust openings, flywheel housing, crankcase breathers, dipstick tubes, etc. Make sure all covers are air tight and weatherproof. Use a waterproof, weather resistant tape.5. Put lubricant on all points given in the Lubrication and Maintenance Chart.6. Put a heavy amount of multipurpose grease on all outside parts that move; rod threads, ball joints, linkage, etc.7. Oil and oil filter elements used less than 50 hours in the engine do not need to be changed. (Otherwise, change the oil, filling the engine to the "add oil" mark on the dipstick.) Add 3% to 4% of VCI oil per engine volume. If the engine is drained, install a mixture of 50% VCI oil and 50% engine oil in the crankcase and in all lubricating oil compartments at the rate of one part VCI oil mixture per fifteen parts of compartment capacity at full level. If possible, operate the engine three to five minutes. Put tape over all openings to seal VCI vapors in the engine. If necessary, drain some lubricant to add to the mixture.8. Remove any dirt from the air cleaner. Check all seals and gaskets.9. Remove the air filter elements. Turn the engine at cranking speed with throttle control in fuel OFF position, remove pressure plug for boost pressure and use a sprayer to add a mixture of 50% VCI oil and 50% engine oil. Minimum application rate is 5.5 milliliters per liter (3 oz. per
1. Clean the outside of the engine and repaint areas that have paint damage with a good quality paint.2. Remove the batteries and use them in some other place or put them in storage where they can be checked and electrically charged again when needed. If the batteries are not removed, wash the tops. Put an electrical charge to the battery to a specific gravity of 1.275. Disconnect the battery terminals. Put a plastic cover over the battery.3. Loosen all fan, alternator belts, etc. Attach a tag to indicate what work has been done.4. Put a waterproof cover over engines with enclosures stored outdoors. Make the cover tight, but loose enough to allow air to circulate around the engine to prevent damage to exposed metal parts from condensation. Remove the waterproof cover every two or three months and check the engine for corrosion. If the engine has signs of corrosion at the check period, follow the protection procedure again. To operate the engine, it is not necessary to remove the preservative oil mixture. If a compartment under protection of VCI vapors is opened, put more VCI mixture in to make up for the vapor loss. Install all covers and/or put tape over all openings, air intake, exhaust openings, flywheel housing, crankcase breathers, dipstick tubes, etc. Make sure all covers are air tight and weatherproof. Use a waterproof, weather resistant tape.5. Put lubricant on all points given in the Lubrication and Maintenance Chart.6. Put a heavy amount of multipurpose grease on all outside parts that move; rod threads, ball joints, linkage, etc.7. Oil and oil filter elements used less than 50 hours in the engine do not need to be changed. (Otherwise, change the oil, filling the engine to the "add oil" mark on the dipstick.) Add 3% to 4% of VCI oil per engine volume. If the engine is drained, install a mixture of 50% VCI oil and 50% engine oil in the crankcase and in all lubricating oil compartments at the rate of one part VCI oil mixture per fifteen parts of compartment capacity at full level. If possible, operate the engine three to five minutes. Put tape over all openings to seal VCI vapors in the engine. If necessary, drain some lubricant to add to the mixture.8. Remove any dirt from the air cleaner. Check all seals and gaskets.9. Remove the air filter elements. Turn the engine at cranking speed with throttle control in fuel OFF position, remove pressure plug for boost pressure and use a sprayer to add a mixture of 50% VCI oil and 50% engine oil. Minimum application rate is 5.5 milliliters per liter (3 oz. per