Information fuel-injection pump
BOSCH
9 410 610 248
9410610248
ZEXEL
101069-1891
1010691891
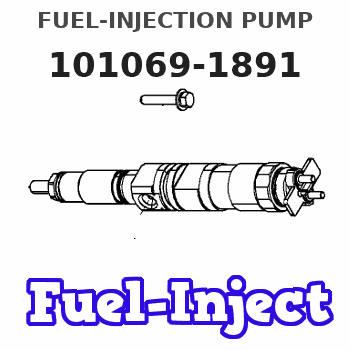
Rating:
Scheme ###:
1. | [1] | 131071-1120 | PUMP HOUSING |
1/30. | [3] | 029040-6020 | STUD |
1/35A. | [1] | 131400-0100 | ADAPTOR |
1/35A. | [1] | 131400-0100 | ADAPTOR |
1/40. | [1] | 131420-0420 | BLEEDER SCREW |
1/40A. | [1] | 131420-0420 | BLEEDER SCREW |
2. | [1] | 131028-6020 | COVER |
2/2. | [1] | 131011-0800 | GASKET |
3. | [2] | 131017-1000 | FLAT-HEAD SCREW |
5. | [2] | 029340-6020 | GASKET D10&6.5T1.00 |
16. | [6] | 131034-1401 | CAPSULE |
21. | [3] | 139206-0400 | UNION NUT |
23. | [1] | 029633-1010 | O-RING |
30. | [6] | 131101-7620 | PLUNGER-AND-BARREL ASSY |
36. | [6] | 131110-0620 | DELIVERY-VALVE ASSEMBLY |
37. | [6] | 131112-0100 | COILED SPRING |
40. | [6] | 131115-0200 | GASKET |
41. | [6] | 131116-0500 | FITTING |
45. | [3] | 131122-0520 | PLATE |
55. | [6] | 131200-1820 | TAPPET |
55/2. | [1] | 131201-0100 | UNION NUT |
55/3. | [1] | 131202-0100 | HEXAGON SCREW |
55/4. | [1] | 131203-0200 | BEARING PIN |
55/5. | [1] | 131204-1000 | ROLLER |
55/6. | [1] | 131205-0500 | BUSHING |
55/7. | [1] | 131206-0500 | SLIDER |
61. | [6] | 131215-2400 | COMPRESSION SPRING |
62. | [6] | 131216-0100 | SLOTTED WASHER |
63. | [6] | 131217-0100 | SLOTTED WASHER |
67. | [1] | 131256-0000 | CONTROL RACK |
68. | [1] | 131226-0300 | FLAT-HEAD SCREW |
76. | [6] | 131240-0100 | PINION |
77. | [6] | 131241-0100 | CONTROL SLEEVE |
78. | [6] | 131242-0100 | FLAT-HEAD SCREW |
90. | [1] | 131370-1000 | CAMSHAFT |
91. | [1] | 016630-2030 | BEARING PLATE |
91A. | [1] | 016630-2030 | BEARING PLATE |
92. | [1] | 131302-0300 | SPACER RING |
92A. | [1] | 131302-0300 | SPACER RING |
93/1. | [0] | 029311-7010 | SHIM D22&17T0.1 |
93/1. | [0] | 029311-7020 | SHIM D22&17T0.12 |
93/1. | [0] | 029311-7030 | SHIM D22&17T0.14 |
93/1. | [0] | 029311-7040 | SHIM D22&17T0.16 |
93/1. | [0] | 029311-7050 | SHIM D22&17T0.18 |
93/1. | [0] | 029311-7060 | SHIM D22&17T0.5 |
93/1. | [0] | 029311-7070 | SHIM D22&17T1.0 |
93/1. | [0] | 029311-7090 | SHIM D22&17T0.3 |
93/1. | [0] | 029311-7210 | SHIM D22&17T0.7 |
93/1. | [0] | 029311-7220 | SHIM D22&17T1.4 |
93/1. | [0] | 139417-0000 | SHIM D22&17T2.4 |
93A/1. | [0] | 029311-7010 | SHIM D22&17T0.1 |
93A/1. | [0] | 029311-7020 | SHIM D22&17T0.12 |
93A/1. | [0] | 029311-7030 | SHIM D22&17T0.14 |
93A/1. | [0] | 029311-7040 | SHIM D22&17T0.16 |
93A/1. | [0] | 029311-7050 | SHIM D22&17T0.18 |
93A/1. | [0] | 029311-7060 | SHIM D22&17T0.5 |
93A/1. | [0] | 029311-7070 | SHIM D22&17T1.0 |
93A/1. | [0] | 029311-7090 | SHIM D22&17T0.3 |
93A/1. | [0] | 029311-7210 | SHIM D22&17T0.7 |
93A/1. | [0] | 029311-7220 | SHIM D22&17T1.4 |
93A/1. | [0] | 139417-0000 | SHIM D22&17T2.4 |
95. | [1] | 131306-0800 | BEARING SHELL |
96. | [2] | 029050-5010 | FLAT-HEAD SCREW M5P0.8L32 |
97. | [2] | 026505-0940 | GASKET |
100A. | [1] | 139617-0000 | PACKING RING |
101A. | [1] | 131330-3100 | COVER |
102A. | [1] | 131563-0900 | SLIDING PIECE |
104A. | [4] | 020006-1440 | BLEEDER SCREW M6P1L14 |
106A. | [1] | 029634-4020 | O-RING |
112A. | [1] | 025803-1610 | WOODRUFF KEY |
117A. | [1] | 029731-4570 | EYE BOLT |
118A. | [2] | 029341-4130 | GASKET D20&13.8T2* |
152. | [1] | 131456-4300 | EYE BOLT |
153. | [1] | 029711-2180 | INLET UNION |
154. | [2] | 026512-1540 | GASKET D15.4&12.2T1.50 |
334. | [1] | 029731-0120 | EYE BOLT |
336. | [2] | 026510-1340 | GASKET D13.4&10.2T1 |
360A. | [1] | 131496-0300 | POINTER |
361A. | [2] | 029010-6680 | BLEEDER SCREW |
Cross reference number
Zexel num
Bosch num
Firm num
Name
Information:
Introduction
This Special Instruction covers the removal procedure for DEF connectors on the models and applications listed above.Safety Section
Care must be taken to ensure that fluids are contained during performance of inspection, maintenance, testing, adjusting, and repair of the product. Be prepared to collect the fluid with suitable containers before opening any compartment or disassembling any component containing fluids.Refer to Special Publication, PERJ1017, "Dealer Service Tool Catalog" for tools and supplies suitable to collect and contain fluids on Cat® products.Dispose of all fluids according to local regulations and mandates.
Personal injury or death can result from improperly checking for a leak.Always use a board or cardboard when checking for a leak. Escaping air or fluid under pressure, even a pin-hole size leak, can penetrate body tissue causing serious injury, and possible death.If fluid is injected into your skin, it must be treated immediately by a doctor familiar with this type of injury.
Illustration 1 g00104545Prevent the machine from movement. Park the machine on a level surface.Attach a "Do Not Operate" warning tag or a similar warning tag to the start switch or to the controls before you service the equipment. These warning tags (Special Instruction, SEHS7332) are available from your Caterpillar dealer.Removal Procedure for Single Clip Connectors
Illustration 2 g03468077
(1) Line
(2) Retaining Clip
Clean the area around the connector with compressed air. Be sure to remove any dirt or debris before continuing with this procedure.
Press down on the line (1).
Press IN on the retaining clip (2).
Gently pull straight up on the line.Note: Do not pull out the clip, damage will occur to the retaining clip.Note: Do not pull off the line without the clip being fully depressed, damage will occur to the retaining clip.Removal Procedure for Dual Clip Connectors
Illustration 3 g03468506
(1) Line
(2) Retaining Clips
Clean the area around the connector with compressed air. Be sure to remove any dirt or debris before continuing with this procedure.
Press down on the line (1).
Press IN on the retaining clips (2).
Gently pull straight up on the line.Note: Do not pull out the clip, damage will occur to the retaining clip.Note: Do not pull off the line without the clip being fully depressed, damage will occur to the retaining clip.
This Special Instruction covers the removal procedure for DEF connectors on the models and applications listed above.Safety Section
Care must be taken to ensure that fluids are contained during performance of inspection, maintenance, testing, adjusting, and repair of the product. Be prepared to collect the fluid with suitable containers before opening any compartment or disassembling any component containing fluids.Refer to Special Publication, PERJ1017, "Dealer Service Tool Catalog" for tools and supplies suitable to collect and contain fluids on Cat® products.Dispose of all fluids according to local regulations and mandates.
Personal injury or death can result from improperly checking for a leak.Always use a board or cardboard when checking for a leak. Escaping air or fluid under pressure, even a pin-hole size leak, can penetrate body tissue causing serious injury, and possible death.If fluid is injected into your skin, it must be treated immediately by a doctor familiar with this type of injury.
Illustration 1 g00104545Prevent the machine from movement. Park the machine on a level surface.Attach a "Do Not Operate" warning tag or a similar warning tag to the start switch or to the controls before you service the equipment. These warning tags (Special Instruction, SEHS7332) are available from your Caterpillar dealer.Removal Procedure for Single Clip Connectors
Illustration 2 g03468077
(1) Line
(2) Retaining Clip
Clean the area around the connector with compressed air. Be sure to remove any dirt or debris before continuing with this procedure.
Press down on the line (1).
Press IN on the retaining clip (2).
Gently pull straight up on the line.Note: Do not pull out the clip, damage will occur to the retaining clip.Note: Do not pull off the line without the clip being fully depressed, damage will occur to the retaining clip.Removal Procedure for Dual Clip Connectors
Illustration 3 g03468506
(1) Line
(2) Retaining Clips
Clean the area around the connector with compressed air. Be sure to remove any dirt or debris before continuing with this procedure.
Press down on the line (1).
Press IN on the retaining clips (2).
Gently pull straight up on the line.Note: Do not pull out the clip, damage will occur to the retaining clip.Note: Do not pull off the line without the clip being fully depressed, damage will occur to the retaining clip.