Information fuel-injection pump
BOSCH
9 410 612 306
9410612306
ZEXEL
101068-8050
1010688050
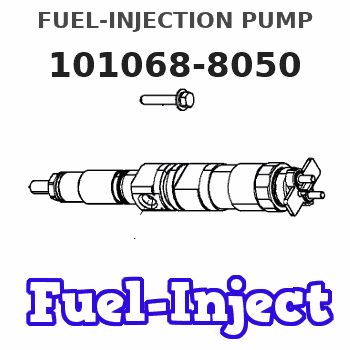
Rating:
Compare Prices: .
As an associate, we earn commssions on qualifying purchases through the links below
$3,773.39
08 Sep 2024
0.1102[0.05] pounds
CN: Parts Assembly Cente
E320 E320B E320C Excavator Fuel Injection Pump 101068-8050 3066 High Pressure Injector Pump 212-8559
FPAIZTRJ Precise fuel pressure control: High pressure fuel pumps maintain accurate fuel pressure, and the engine's fuel injection system is critical. Precise pressure control helps optimize combustion efficiency, reduce emissions and improve engine performance. || Enhanced engine performance: By providing a steady flow of high pressure fuel, the high pressure fuel pump improves engine responsiveness and power output, making the vehicle smoother and more robust when accelerating. || Reduced emissions: High pressure fuel pumps ensure that fuel is injected into the combustion chamber under pressure, helping to achieve a more complete combustion, reducing unburned fuel and exhaust gases, thereby reducing vehicle emissions. || Durability and reliability: High pressure fuel pumps are designed to withstand high temperatures, maintain reliable performance in harsh operating environments, and reduce the frequency of failures. || E320 E320B E320C Excavator Fuel Injection Pump 101068-8050 3066 High Pressure Injector Pump 212-8559
FPAIZTRJ Precise fuel pressure control: High pressure fuel pumps maintain accurate fuel pressure, and the engine's fuel injection system is critical. Precise pressure control helps optimize combustion efficiency, reduce emissions and improve engine performance. || Enhanced engine performance: By providing a steady flow of high pressure fuel, the high pressure fuel pump improves engine responsiveness and power output, making the vehicle smoother and more robust when accelerating. || Reduced emissions: High pressure fuel pumps ensure that fuel is injected into the combustion chamber under pressure, helping to achieve a more complete combustion, reducing unburned fuel and exhaust gases, thereby reducing vehicle emissions. || Durability and reliability: High pressure fuel pumps are designed to withstand high temperatures, maintain reliable performance in harsh operating environments, and reduce the frequency of failures. || E320 E320B E320C Excavator Fuel Injection Pump 101068-8050 3066 High Pressure Injector Pump 212-8559
You can express buy:
USD 1201.39
14-06-2025
14-06-2025
101068-8050 212-8559 3066 High Pressure Injector Pump E320 E320B E320C Excavator Fuel injection Pump
Scheme ###:
1. | [1] | 131072-5220 | PUMP HOUSING |
1. | [1] | 131072-5220 | PUMP HOUSING |
1/30. | [3] | 029040-6020 | STUD |
1/30. | [3] | 029040-6020 | STUD |
1/35A. | [1] | 131400-0100 | ADAPTOR |
1/35A. | [1] | 131400-0100 | ADAPTOR |
1/40. | [1] | 131423-0800 | ADAPTOR |
1/40. | [1] | 131423-0800 | ADAPTOR |
1/40A. | [1] | 131420-0420 | BLEEDER SCREW |
1/40A. | [1] | 131420-0420 | BLEEDER SCREW |
1/41A. | [1] | 026512-1540 | GASKET D15.4&12.2T1.50 |
1/41A. | [1] | 026512-1540 | GASKET D15.4&12.2T1.50 |
2. | [1] | 131028-6020 | COVER |
2. | [1] | 131028-6020 | COVER |
2/2. | [1] | 131011-0800 | GASKET |
2/2. | [1] | 131011-0800 | GASKET |
3. | [2] | 131017-1000 | FLAT-HEAD SCREW |
3. | [2] | 131017-1000 | FLAT-HEAD SCREW |
5. | [2] | 029340-6020 | GASKET D10&6.5T1.00 |
5. | [2] | 029340-6020 | GASKET D10&6.5T1.00 |
16. | [6] | 131034-1401 | CAPSULE |
16. | [6] | 131034-1401 | CAPSULE |
21. | [3] | 139206-0400 | UNION NUT |
21. | [3] | 139206-0400 | UNION NUT |
23. | [1] | 029633-1010 | O-RING |
23. | [1] | 029633-1010 | O-RING |
30. | [6] | 131102-0020 | PLUNGER-AND-BARREL ASSY |
30. | [6] | 131102-0020 | PLUNGER-AND-BARREL ASSY |
36. | [6] | 131110-4720 | DELIVERY-VALVE ASSEMBLY |
36. | [6] | 131110-4720 | DELIVERY-VALVE ASSEMBLY |
37. | [6] | 131112-2300 | COILED SPRING |
37. | [6] | 131112-2300 | COILED SPRING |
40. | [6] | 131115-1600 | GASKET |
40. | [6] | 131115-1600 | GASKET |
41. | [6] | 131116-4220 | FITTING |
41. | [6] | 131116-4220 | FITTING |
45. | [3] | 131122-0520 | PLATE |
45. | [3] | 131122-0520 | PLATE |
49. | [6] | 029632-0030 | O-RING |
49. | [6] | 029632-0030 | O-RING |
55. | [6] | 131200-0220 | TAPPET |
55. | [6] | 131200-0220 | TAPPET |
55/2. | [1] | 131203-0200 | BEARING PIN |
55/2. | [1] | 131203-0200 | BEARING PIN |
55/3. | [1] | 131204-1000 | ROLLER |
55/3. | [1] | 131204-1000 | ROLLER |
55/4. | [1] | 131205-0500 | BUSHING |
55/4. | [1] | 131205-0500 | BUSHING |
55/5. | [1] | 131206-0200 | SLIDER |
55/5. | [1] | 131206-0200 | SLIDER |
56/1. | [0] | 029311-0020 | SHIM D19&10T0.30 |
56/1. | [0] | 029311-0030 | SHIM D19&10T0.40 |
56/1. | [0] | 029311-0040 | SHIM D19&10T0.50 |
56/1. | [0] | 029311-0040 | SHIM D19&10T0.50 |
56/1. | [0] | 029311-0050 | SHIM D19&10T0.6 |
56/1. | [0] | 029311-0060 | SHIM D19&10T0.7 |
56/1. | [0] | 029311-0070 | SHIM D19&10T0.8 |
56/1. | [0] | 029311-0080 | SHIM D19&10T0.9 |
56/1. | [0] | 029311-0090 | SHIM D19&10T1 |
56/1. | [0] | 029311-0110 | SHIM D19&10T1.1 |
56/1. | [0] | 029311-0120 | SHIM D19&10T1.2 |
56/1. | [0] | 029311-0130 | SHIM D19&10T1.3 |
56/1. | [0] | 029311-0140 | SHIM D19&10T1.4 |
56/1. | [0] | 029311-0270 | SHIM D19&10T0.55 |
56/1. | [0] | 029311-0280 | SHIM D19&10T0.65 |
56/1. | [0] | 029311-0290 | SHIM D19&10T0.75 |
56/1. | [0] | 029311-0310 | SHIM D19&10T0.85 |
56/1. | [0] | 029311-0320 | SHIM D19&10T0.95 |
56/1. | [0] | 029311-0330 | SHIM D19&10T1.05 |
56/1. | [0] | 029311-0340 | SHIM D19&10T1.15 |
56/1. | [0] | 029311-0350 | SHIM D19&10T1.25 |
56/1. | [0] | 029311-0490 | SHIM D19&10T1.5 |
56/1. | [0] | 029311-0500 | SHIM D19&10T1.6 |
56/1. | [0] | 029311-0580 | SHIM D19&10T0.2 |
56/1. | [0] | 029311-0590 | SHIM D19&10T0.25 |
56/1. | [0] | 029311-0600 | SHIM D19&10T0.35 |
56/1. | [0] | 029311-0610 | SHIM D19&10T0.45 |
56/1. | [0] | 029311-0620 | SHIM D19&10T1.35 |
56/1. | [0] | 029311-0630 | SHIM D19&10T1.45 |
56/1. | [0] | 029311-0710 | SHIM D19&10T1.55 |
61. | [6] | 131215-2500 | COMPRESSION SPRING |
61. | [6] | 131215-2500 | COMPRESSION SPRING |
62. | [6] | 131216-0100 | SLOTTED WASHER |
62. | [6] | 131216-0100 | SLOTTED WASHER |
63. | [6] | 131217-0200 | SLOTTED WASHER |
63. | [6] | 131217-0200 | SLOTTED WASHER |
67. | [1] | 131256-0000 | CONTROL RACK |
67. | [1] | 131256-0000 | CONTROL RACK |
68. | [1] | 131226-0300 | FLAT-HEAD SCREW |
68. | [1] | 131226-0300 | FLAT-HEAD SCREW |
76. | [6] | 131240-0100 | PINION |
76. | [6] | 131240-0100 | PINION |
77. | [6] | 131241-0100 | CONTROL SLEEVE |
77. | [6] | 131241-0100 | CONTROL SLEEVE |
78. | [6] | 131242-0100 | FLAT-HEAD SCREW |
78. | [6] | 131242-0100 | FLAT-HEAD SCREW |
90. | [1] | 131370-0800 | CAMSHAFT |
90. | [1] | 131370-0800 | CAMSHAFT |
91A. | [1] | 016630-2030 | BEARING PLATE |
91A. | [1] | 016630-2030 | BEARING PLATE |
91B. | [1] | 028201-7020 | BEARING PLATE |
91B. | [1] | 028201-7020 | BEARING PLATE |
91E. | [1] | 016630-2030 | BEARING PLATE |
91E. | [1] | 016630-2030 | BEARING PLATE |
91F. | [1] | 028201-7020 | BEARING PLATE |
91F. | [1] | 028201-7020 | BEARING PLATE |
92. | [1] | 131302-0300 | SPACER RING |
92. | [1] | 131302-0300 | SPACER RING |
92A. | [1] | 131302-0300 | SPACER RING |
92A. | [1] | 131302-0300 | SPACER RING |
93/1. | [0] | 029311-7010 | SHIM D22&17T0.1 |
93/1. | [0] | 029311-7020 | SHIM D22&17T0.12 |
93/1. | [0] | 029311-7020 | SHIM D22&17T0.12 |
93/1. | [0] | 029311-7030 | SHIM D22&17T0.14 |
93/1. | [0] | 029311-7040 | SHIM D22&17T0.16 |
93/1. | [0] | 029311-7050 | SHIM D22&17T0.18 |
93/1. | [0] | 029311-7060 | SHIM D22&17T0.5 |
93/1. | [0] | 029311-7070 | SHIM D22&17T1.0 |
93/1. | [0] | 029311-7090 | SHIM D22&17T0.3 |
93/1. | [0] | 029311-7210 | SHIM D22&17T0.7 |
93/1. | [0] | 029311-7220 | SHIM D22&17T1.4 |
93/1. | [0] | 139417-0000 | SHIM D22&17T2.4 |
93A/1. | [0] | 029311-7010 | SHIM D22&17T0.1 |
93A/1. | [0] | 029311-7020 | SHIM D22&17T0.12 |
93A/1. | [0] | 029311-7030 | SHIM D22&17T0.14 |
93A/1. | [0] | 029311-7040 | SHIM D22&17T0.16 |
93A/1. | [0] | 029311-7050 | SHIM D22&17T0.18 |
93A/1. | [0] | 029311-7060 | SHIM D22&17T0.5 |
93A/1. | [0] | 029311-7070 | SHIM D22&17T1.0 |
93A/1. | [0] | 029311-7090 | SHIM D22&17T0.3 |
93A/1. | [0] | 029311-7210 | SHIM D22&17T0.7 |
93A/1. | [0] | 029311-7220 | SHIM D22&17T1.4 |
93A/1. | [0] | 139417-0000 | SHIM D22&17T2.4 |
93A/1. | [0] | 139417-0000 | SHIM D22&17T2.4 |
95. | [1] | 131306-0800 | BEARING SHELL |
95. | [1] | 131306-0800 | BEARING SHELL |
96. | [2] | 029050-5010 | FLAT-HEAD SCREW M5P0.8L32 |
96. | [2] | 029050-5010 | FLAT-HEAD SCREW M5P0.8L32 |
97. | [2] | 026505-0940 | GASKET |
97. | [2] | 026505-0940 | GASKET |
101A. | [1] | 131316-5500 | COVER |
101A. | [1] | 131316-5500 | COVER |
104A. | [4] | 020006-1440 | BLEEDER SCREW M6P1L14 |
104A. | [4] | 020006-1440 | BLEEDER SCREW M6P1L14 |
112A. | [1] | 025803-1610 | WOODRUFF KEY |
112A. | [1] | 025803-1610 | WOODRUFF KEY |
117A. | [1] | 029731-4580 | EYE BOLT |
117A. | [1] | 029731-4580 | EYE BOLT |
118A. | [2] | 029341-4080 | GASKET |
118A. | [2] | 029341-4080 | GASKET |
191. | [1] | 131459-1920 | BRACKET |
191. | [1] | 131459-1920 | BRACKET |
191/2. | [4] | 029041-0010 | STUD |
191/2. | [4] | 029041-0010 | STUD |
192. | [1] | 139768-0000 | O-RING |
192. | [1] | 139768-0000 | O-RING |
194. | [4] | 014011-0140 | PLAIN WASHER D22&10.5T1.6 |
194. | [4] | 014011-0140 | PLAIN WASHER D22&10.5T1.6 |
195. | [4] | 014111-0440 | LOCKING WASHER |
195. | [4] | 014111-0440 | LOCKING WASHER |
196. | [4] | 131465-0000 | UNION NUT |
196. | [4] | 131465-0000 | UNION NUT |
334. | [1] | 029731-0410 | EYE BOLT |
334. | [1] | 029731-0410 | EYE BOLT |
336. | [2] | 029341-0090 | GASKET |
336. | [2] | 029341-0090 | GASKET |
Cross reference number
Zexel num
Bosch num
Firm num
Name
Information:
The current API categories represent the minimum requirements for diesel engine oils. These categories are developed in collaboration of OEMs and the Oil and Chemical industries.The current licensed oils are:
API CK-4, released December 2016
API CJ-4, released 2006
API CI-4, API CI-4PLUS released 2002
API CH-4, released 1998Each API category is technically more advanced and of higher performance than the prior one.Refer to API 1509 document and/or ASTM D4485 for details of the API tests requirements and limits.Note: Obsolete API oil categories are not licensed by the API and hence are of uncontrolled quality. These oils are technically inferior to current oils and can result in reduced engine performance and life. These obsolete oil categories are not allowed in Cat engines.API FA-4 is NOT recommended for Caterpillar engines. API FA oil is designed with low High Temperature High Shear (HTHS) viscosity oil for use in certain 2017 On-Highway truck engines that have to meet certain on-road emissions regulations. This category is not backwards compatible.In order to help protect your engine, and in order to help optimize oil drain intervals for engine applications and duty cycles, use Cat S O S Services oil analysis. Refer to the section below and to the section on Cat S O S Services given later in the Special Publication.
Depending on application severity and localized environmental conditions, and also depending on maintenance practices, operating Direct Injection (DI) diesel engines and operating PC (Precombustion Chamber) diesel engines on fuel with sulfur levels over 0.1 percent (1000 ppm) may require significantly shortened oil change intervals in order to help maintain adequate wear protection. Refer to this Special Publication, "Fuel Specifications" section, “Diesel Fuel Sulfur” topic for additional information.
Fuel Sulfur Impact on Engine Oil
The use of Cat S O S Services oil analysis is recommended for determining oil life.For Caterpillar machines operating under emissions regulations such as US EPA Tier4, EU Stage V or other emission regulations controls, the maximum fuel sulfur level permitted by regulations in the US is 0.0015% or 15 ppm. Maximum permitted fuel sulfur levels in other emissions regulated countries may vary from .0015% or 15 ppm slightly and must be followed.In order to help protect your engine and optimize oil drain intervals for engine applications and duty cycles, it is important to use SOS Services oil analysis to determine if the sulfur has degraded the oil. Use Cat S O S Services oil analysis per the following general guidelines:
Recommended normally
For fuel sulfur level up to 0.05 percent (500 ppm), no additional sampling is required. Follow the recommended oil sampling in the machine OMM
For fuel sulfur level of > 0.05 percent to 0.5 percent (500 ppm to 5000 ppm), SOS services oil analysis is strongly recommended to determine oil drain intervals. Sample the oil every 250 hours until a trend is established,
API CK-4, released December 2016
API CJ-4, released 2006
API CI-4, API CI-4PLUS released 2002
API CH-4, released 1998Each API category is technically more advanced and of higher performance than the prior one.Refer to API 1509 document and/or ASTM D4485 for details of the API tests requirements and limits.Note: Obsolete API oil categories are not licensed by the API and hence are of uncontrolled quality. These oils are technically inferior to current oils and can result in reduced engine performance and life. These obsolete oil categories are not allowed in Cat engines.API FA-4 is NOT recommended for Caterpillar engines. API FA oil is designed with low High Temperature High Shear (HTHS) viscosity oil for use in certain 2017 On-Highway truck engines that have to meet certain on-road emissions regulations. This category is not backwards compatible.In order to help protect your engine, and in order to help optimize oil drain intervals for engine applications and duty cycles, use Cat S O S Services oil analysis. Refer to the section below and to the section on Cat S O S Services given later in the Special Publication.
Depending on application severity and localized environmental conditions, and also depending on maintenance practices, operating Direct Injection (DI) diesel engines and operating PC (Precombustion Chamber) diesel engines on fuel with sulfur levels over 0.1 percent (1000 ppm) may require significantly shortened oil change intervals in order to help maintain adequate wear protection. Refer to this Special Publication, "Fuel Specifications" section, “Diesel Fuel Sulfur” topic for additional information.
Fuel Sulfur Impact on Engine Oil
The use of Cat S O S Services oil analysis is recommended for determining oil life.For Caterpillar machines operating under emissions regulations such as US EPA Tier4, EU Stage V or other emission regulations controls, the maximum fuel sulfur level permitted by regulations in the US is 0.0015% or 15 ppm. Maximum permitted fuel sulfur levels in other emissions regulated countries may vary from .0015% or 15 ppm slightly and must be followed.In order to help protect your engine and optimize oil drain intervals for engine applications and duty cycles, it is important to use SOS Services oil analysis to determine if the sulfur has degraded the oil. Use Cat S O S Services oil analysis per the following general guidelines:
Recommended normally
For fuel sulfur level up to 0.05 percent (500 ppm), no additional sampling is required. Follow the recommended oil sampling in the machine OMM
For fuel sulfur level of > 0.05 percent to 0.5 percent (500 ppm to 5000 ppm), SOS services oil analysis is strongly recommended to determine oil drain intervals. Sample the oil every 250 hours until a trend is established,