Information fuel-injection pump
BOSCH
9 410 612 754
9410612754
ZEXEL
101060-9500
1010609500
MITSUBISHI
ME035913
me035913
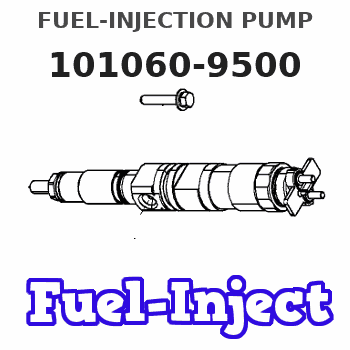
Rating:
Scheme ###:
1. | [1] | 131072-8220 | PUMP HOUSING |
1/30. | [3] | 029040-6220 | STUD |
1/35A. | [1] | 134419-0000 | ADAPTOR |
1/40. | [1] | 131423-0900 | ADAPTOR |
1/40A. | [1] | 131423-1300 | ADAPTOR |
2. | [1] | 131028-6020 | COVER |
2/2. | [1] | 131011-0800 | GASKET |
3. | [2] | 131017-1000 | FLAT-HEAD SCREW |
5. | [2] | 029340-6020 | GASKET D10&6.5T1.00 |
16. | [6] | 131034-1401 | CAPSULE |
21. | [3] | 139206-0400 | UNION NUT |
23. | [1] | 029633-1010 | O-RING |
30. | [6] | 131151-2220 | PLUNGER-AND-BARREL ASSY |
36. | [6] | 131110-4720 | DELIVERY-VALVE ASSEMBLY |
37. | [6] | 131112-2300 | COILED SPRING |
40. | [6] | 131115-1600 | GASKET |
41. | [6] | 131116-7920 | FITTING |
42. | [6] | 131117-3100 | FILLER PIECE |
45. | [3] | 131122-0320 | PLATE |
49. | [6] | 029632-0030 | O-RING |
55. | [6] | 131200-0620 | TAPPET |
55/2. | [1] | 131201-0100 | UNION NUT |
55/3. | [1] | 131202-0100 | HEXAGON SCREW |
55/4. | [1] | 131203-0200 | BEARING PIN |
55/5. | [1] | 131204-1000 | ROLLER |
55/6. | [1] | 131205-0500 | BUSHING |
55/7. | [1] | 131206-0200 | SLIDER |
61. | [6] | 131215-2400 | COMPRESSION SPRING |
62. | [6] | 131216-0100 | SLOTTED WASHER |
63. | [6] | 131217-0100 | SLOTTED WASHER |
67. | [1] | 131256-0000 | CONTROL RACK |
68. | [1] | 131226-0300 | FLAT-HEAD SCREW |
76. | [6] | 131240-0100 | PINION |
77. | [6] | 131241-0100 | CONTROL SLEEVE |
78. | [6] | 131242-0100 | FLAT-HEAD SCREW |
90. | [1] | 131371-1700 | CAMSHAFT |
91A. | [1] | 016640-2030 | BEARING PLATE |
91B. | [1] | 028202-0020 | BEARING PLATE |
91E. | [1] | 016630-2030 | BEARING PLATE |
91F. | [1] | 028201-7020 | BEARING PLATE |
92. | [1] | 131302-0400 | SPACER RING |
92A. | [1] | 131302-1000 | SPACER RING |
93/1. | [0] | 029311-7010 | SHIM D22&17T0.1 |
93/1. | [0] | 029311-7020 | SHIM D22&17T0.12 |
93/1. | [0] | 029311-7030 | SHIM D22&17T0.14 |
93/1. | [0] | 029311-7040 | SHIM D22&17T0.16 |
93/1. | [0] | 029311-7050 | SHIM D22&17T0.18 |
93/1. | [0] | 029311-7060 | SHIM D22&17T0.5 |
93/1. | [0] | 029311-7070 | SHIM D22&17T1.0 |
93/1. | [0] | 029311-7090 | SHIM D22&17T0.3 |
93/1. | [0] | 029311-7210 | SHIM D22&17T0.7 |
93/1. | [0] | 029311-7220 | SHIM D22&17T1.4 |
93/1. | [0] | 139417-0000 | SHIM D22&17T2.4 |
93A/1. | [0] | 029312-0220 | SHIM D27&20T0.1 |
93A/1. | [0] | 029312-0230 | SHIM D27&20T0.12 |
93A/1. | [0] | 029312-0240 | SHIM D27&20T0.14 |
93A/1. | [0] | 029312-0250 | SHIM D27&20T0.16 |
93A/1. | [0] | 029312-0260 | SHIM D27&20T0.18 |
93A/1. | [0] | 029312-0270 | SHIM D27&20T0.5 |
93A/1. | [0] | 029312-0290 | SHIM D27&20T0.3 |
93A/1. | [0] | 029312-0300 | SHIM D27&20T1.0 |
93A/1. | [0] | 139420-0400 | SHIM D27&20T0.7 |
95. | [1] | 131306-0800 | BEARING SHELL |
96. | [2] | 029050-5010 | FLAT-HEAD SCREW M5P0.8L32 |
97. | [2] | 026505-0940 | GASKET |
100A. | [1] | 029622-0190 | PACKING RING |
101A. | [1] | 131330-1800 | COVER |
104A. | [4] | 020006-2040 | BLEEDER SCREW M6P1L20 4T |
106A. | [1] | 131321-1900 | GASKET |
112A. | [1] | 029470-4030 | WOODRUFF KEY |
117A. | [1] | 131420-0400 | BLEEDER SCREW |
118A. | [1] | 026506-1040 | GASKET D9.9&6.2T1 |
131. | [1] | 139814-0900 | EYE BOLT |
131A. | [1] | 131424-5520 | OVER FLOW VALVE |
132. | [2] | 029341-4130 | GASKET D20&13.8T2* |
132A. | [2] | 029341-4130 | GASKET D20&13.8T2* |
191. | [1] | 131459-6720 | BRACKET |
191/2. | [4] | 029041-0300 | STUD |
191/2. | [4] | 029041-0300 | STUD |
191/2. | [4] | 029041-0300 | STUD |
191/3. | [2] | 029041-0390 | STUD |
191/3. | [2] | 029041-0390 | STUD |
192. | [1] | 029637-5020 | O-RING &73.5W2 |
194. | [4] | 139310-0000 | PLAIN WASHER |
195. | [4] | 014111-0440 | LOCKING WASHER |
196. | [4] | 013021-0040 | UNION NUT M10P1.5H8 |
334. | [1] | 029731-0120 | EYE BOLT |
336. | [2] | 026510-1340 | GASKET D13.4&10.2T1 |
Include in #1:
101603-1220
as FUEL INJECTION PUMP
Include in #2:
104298-6000
as _
Cross reference number
Zexel num
Bosch num
Firm num
Name
Information:
Introduction
The following special instructions must be used to test for a crack in the Diesel Particulate Filter (DPF). Do not perform any procedure that is outlined in this Special Instruction until you have read and understand the information that is contained in this document.Required Tools
Table 1
Required Tools
Part Number Part Name Quantity
380-5200 Tool Kit 1 Testing Procedure
Perform a “Manual Diesel Particulate Filter Regeneration” using Caterpillar Electronic Technician (Cat ® ET).
After the manual DPF regeneration is complete, run the engine at 1800 rpm for a MINIMUM of 20 minutes to stabilize the DPF temperatures.Note: Manually set the engine speed to 1800 rpm, the engine must maintain a steady speed for the entire duration of the test.
Illustration 1 g02597531
(1) DPF Outlet Cap
(2) Filter Paper
(3) Hose Assembly
(4) Air Pump
Illustration 2 g02599276
(5) DPF Outlet Port
Hot parts or hot components can cause burns or personal injury. Do not allow hot parts or components to contact your skin. Use protective clothing or protective equipment to protect your skin.
Shut down the engine and remove the Delta P line from the DPF outlet port. Refer to Illustrations 1 and 2.
Illustration 3 g02599418
(6) Filter Paper
Install the filter in the fitting, Refer to Illustration 3. Install the fitting in the DPF outlet port. The filter must be installed in less than 10 minutes after the engine has shut down.
Turn the vacuum pump ON.
Disable automatic regeneration in Cat ET.
Illustration 4 g02597737
Select "Service" - "Configuration" - "Emissions Parameters" and "ARD Manual Disable Status". Select "Disabled". The check engine light and a 3714-31 active code will be present.
Override the "DPF Differential Pressure Line Override" to "Disconnected", using Cat ET. Refer to Illustration 4.
Start the engine. Run the engine at 1800 rpm for 15 minutes.Note: Manually set the engine speed to 1800 rpm, the engine must maintain a steady speed for the entire duration of the test.
Hot parts or hot components can cause burns or personal injury. Do not allow hot parts or components to contact your skin. Use protective clothing or protective equipment to protect your skin.
Shut the engine down and remove the filter holder within 25 minutes. Use proper personal protective equipment to remove the filter holder.
Allow the filter holder time to cool down before disassembly.
Carefully disassemble the filter holder to prevent contamination. Tip the fitting down on a clean surface to remove the filter paper. Handle the filter paper with clean hands and only by the edges.
Illustration 5 g02597796
Compare the stained area in the center of the filter paper to the color coded sheet provided. Refer to Illustration 5.
If the shade is equal to or darker than the "Color Code Sheet", the DPF has a crack or leak. Replace the DPF. Refer to Special Instruction, "Diesel Particulate Filter (DPF) Maintenance on Tier 4 Products Equipped with a Diesel Particulate Filter".
If the shade is lighter than the "Color Code Sheet", then return the unit to service.
Enable the Automatic regeneration in Cat ET.
Select "Service" - "Configuration" - "Emissions Parameters" and "ARD Manual Disable Status". Select "Not - Disabled". The check engine light will go off unless
The following special instructions must be used to test for a crack in the Diesel Particulate Filter (DPF). Do not perform any procedure that is outlined in this Special Instruction until you have read and understand the information that is contained in this document.Required Tools
Table 1
Required Tools
Part Number Part Name Quantity
380-5200 Tool Kit 1 Testing Procedure
Perform a “Manual Diesel Particulate Filter Regeneration” using Caterpillar Electronic Technician (Cat ® ET).
After the manual DPF regeneration is complete, run the engine at 1800 rpm for a MINIMUM of 20 minutes to stabilize the DPF temperatures.Note: Manually set the engine speed to 1800 rpm, the engine must maintain a steady speed for the entire duration of the test.
Illustration 1 g02597531
(1) DPF Outlet Cap
(2) Filter Paper
(3) Hose Assembly
(4) Air Pump
Illustration 2 g02599276
(5) DPF Outlet Port
Hot parts or hot components can cause burns or personal injury. Do not allow hot parts or components to contact your skin. Use protective clothing or protective equipment to protect your skin.
Shut down the engine and remove the Delta P line from the DPF outlet port. Refer to Illustrations 1 and 2.
Illustration 3 g02599418
(6) Filter Paper
Install the filter in the fitting, Refer to Illustration 3. Install the fitting in the DPF outlet port. The filter must be installed in less than 10 minutes after the engine has shut down.
Turn the vacuum pump ON.
Disable automatic regeneration in Cat ET.
Illustration 4 g02597737
Select "Service" - "Configuration" - "Emissions Parameters" and "ARD Manual Disable Status". Select "Disabled". The check engine light and a 3714-31 active code will be present.
Override the "DPF Differential Pressure Line Override" to "Disconnected", using Cat ET. Refer to Illustration 4.
Start the engine. Run the engine at 1800 rpm for 15 minutes.Note: Manually set the engine speed to 1800 rpm, the engine must maintain a steady speed for the entire duration of the test.
Hot parts or hot components can cause burns or personal injury. Do not allow hot parts or components to contact your skin. Use protective clothing or protective equipment to protect your skin.
Shut the engine down and remove the filter holder within 25 minutes. Use proper personal protective equipment to remove the filter holder.
Allow the filter holder time to cool down before disassembly.
Carefully disassemble the filter holder to prevent contamination. Tip the fitting down on a clean surface to remove the filter paper. Handle the filter paper with clean hands and only by the edges.
Illustration 5 g02597796
Compare the stained area in the center of the filter paper to the color coded sheet provided. Refer to Illustration 5.
If the shade is equal to or darker than the "Color Code Sheet", the DPF has a crack or leak. Replace the DPF. Refer to Special Instruction, "Diesel Particulate Filter (DPF) Maintenance on Tier 4 Products Equipped with a Diesel Particulate Filter".
If the shade is lighter than the "Color Code Sheet", then return the unit to service.
Enable the Automatic regeneration in Cat ET.
Select "Service" - "Configuration" - "Emissions Parameters" and "ARD Manual Disable Status". Select "Not - Disabled". The check engine light will go off unless