Information fuel-injection pump
BOSCH
9 410 613 713
9410613713
ZEXEL
101060-6860
1010606860
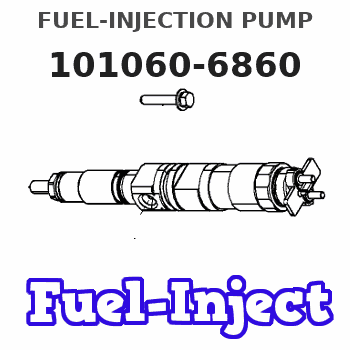
Rating:
Scheme ###:
1. | [1] | 131077-4820 | PUMP HOUSING |
1/30. | [3] | 029040-6020 | STUD |
1/35A. | [1] | 131400-0100 | ADAPTOR |
1/40. | [1] | 131002-9500 | ADAPTOR |
1/40A. | [1] | 131420-3120 | BLEEDER SCREW |
1/50. | [1] | 131311-0000 | SPACER RING |
2. | [1] | 131028-6020 | COVER |
2/2. | [1] | 131011-0800 | GASKET |
3. | [2] | 131017-1000 | FLAT-HEAD SCREW |
5. | [2] | 029340-6020 | GASKET D10&6.5T1.00 |
16. | [6] | 131034-1501 | CAPSULE |
21. | [3] | 139206-0400 | UNION NUT |
23. | [1] | 029633-1010 | O-RING |
30. | [6] | 131150-4320 | PLUNGER-AND-BARREL ASSY |
36. | [6] | 131160-5320 | DELIVERY-VALVE ASSEMBLY |
37. | [6] | 131112-5600 | COMPRESSION SPRING |
40. | [6] | 131115-1200 | GASKET D16&8T0.5 |
41. | [6] | 131116-8300 | FITTING |
42. | [6] | 131117-2100 | FILLER PIECE |
45. | [3] | 131122-0520 | PLATE |
49. | [6] | 139720-0400 | O-RING |
55. | [6] | 131200-2720 | TAPPET |
55/2. | [1] | 131203-0500 | BEARING PIN |
55/3. | [1] | 131204-1100 | ROLLER |
55/4. | [1] | 131205-0600 | BUSHING |
55/5. | [1] | 131206-0700 | SLIDER |
56/1. | [0] | 029311-0020 | SHIM D19&10T0.30 |
56/1. | [0] | 029311-0030 | SHIM D19&10T0.40 |
56/1. | [0] | 029311-0040 | SHIM D19&10T0.50 |
56/1. | [0] | 029311-0050 | SHIM D19&10T0.6 |
56/1. | [0] | 029311-0060 | SHIM D19&10T0.7 |
56/1. | [0] | 029311-0070 | SHIM D19&10T0.8 |
56/1. | [0] | 029311-0080 | SHIM D19&10T0.9 |
56/1. | [0] | 029311-0090 | SHIM D19&10T1 |
56/1. | [0] | 029311-0110 | SHIM D19&10T1.1 |
56/1. | [0] | 029311-0120 | SHIM D19&10T1.2 |
56/1. | [0] | 029311-0130 | SHIM D19&10T1.3 |
56/1. | [0] | 029311-0140 | SHIM D19&10T1.4 |
56/1. | [0] | 029311-0270 | SHIM D19&10T0.55 |
56/1. | [0] | 029311-0280 | SHIM D19&10T0.65 |
56/1. | [0] | 029311-0290 | SHIM D19&10T0.75 |
56/1. | [0] | 029311-0310 | SHIM D19&10T0.85 |
56/1. | [0] | 029311-0320 | SHIM D19&10T0.95 |
56/1. | [0] | 029311-0330 | SHIM D19&10T1.05 |
56/1. | [0] | 029311-0340 | SHIM D19&10T1.15 |
56/1. | [0] | 029311-0350 | SHIM D19&10T1.25 |
56/1. | [0] | 029311-0490 | SHIM D19&10T1.5 |
56/1. | [0] | 029311-0500 | SHIM D19&10T1.6 |
56/1. | [0] | 029311-0580 | SHIM D19&10T0.2 |
56/1. | [0] | 029311-0590 | SHIM D19&10T0.25 |
56/1. | [0] | 029311-0600 | SHIM D19&10T0.35 |
56/1. | [0] | 029311-0610 | SHIM D19&10T0.45 |
56/1. | [0] | 029311-0620 | SHIM D19&10T1.35 |
56/1. | [0] | 029311-0630 | SHIM D19&10T1.45 |
56/1. | [0] | 029311-0710 | SHIM D19&10T1.55 |
61. | [6] | 131215-2100 | COMPRESSION SPRING |
62. | [6] | 131216-0400 | SLOTTED WASHER |
63. | [6] | 131217-0600 | SLOTTED WASHER |
67. | [1] | 131256-0000 | CONTROL RACK |
68. | [1] | 131226-0300 | FLAT-HEAD SCREW |
76. | [6] | 131240-0100 | PINION |
77. | [6] | 131241-0500 | CONTROL SLEEVE |
78. | [6] | 131242-0100 | FLAT-HEAD SCREW |
90. | [1] | 131376-4400 | CAMSHAFT |
91A. | [1] | 016640-2030 | BEARING PLATE |
91B. | [1] | 028202-0020 | BEARING PLATE |
91E. | [1] | 016640-2030 | BEARING PLATE |
91F. | [1] | 028202-0020 | BEARING PLATE |
92. | [1] | 131302-1301 | SPACER RING |
92A. | [1] | 131302-1301 | SPACER RING |
93/1. | [0] | 029312-0220 | SHIM D27&20T0.1 |
93/1. | [0] | 029312-0230 | SHIM D27&20T0.12 |
93/1. | [0] | 029312-0240 | SHIM D27&20T0.14 |
93/1. | [0] | 029312-0250 | SHIM D27&20T0.16 |
93/1. | [0] | 029312-0260 | SHIM D27&20T0.18 |
93/1. | [0] | 029312-0270 | SHIM D27&20T0.5 |
93/1. | [0] | 029312-0290 | SHIM D27&20T0.3 |
93/1. | [0] | 029312-0300 | SHIM D27&20T1.0 |
93/1. | [0] | 029312-0310 | SHIM D24&20T0.10 |
93/1. | [0] | 029312-0320 | SHIM D24&20T0.12 |
93/1. | [0] | 029312-0330 | SHIM D24&20T0.14 |
93/1. | [0] | 029312-0340 | SHIM D24&20T0.16 |
93/1. | [0] | 029312-0350 | SHIM D24&20T0.18 |
93/1. | [0] | 029312-0360 | SHIM D24&20T0.3 |
93/1. | [0] | 029312-0370 | SHIM D24&20T0.5 |
93/1. | [0] | 029312-0380 | SHIM D24&20T1.0 |
93/1. | [0] | 139420-0400 | SHIM D27&20T0.7 |
93A/1. | [0] | 029312-0220 | SHIM D27&20T0.1 |
93A/1. | [0] | 029312-0230 | SHIM D27&20T0.12 |
93A/1. | [0] | 029312-0240 | SHIM D27&20T0.14 |
93A/1. | [0] | 029312-0250 | SHIM D27&20T0.16 |
93A/1. | [0] | 029312-0260 | SHIM D27&20T0.18 |
93A/1. | [0] | 029312-0270 | SHIM D27&20T0.5 |
93A/1. | [0] | 029312-0290 | SHIM D27&20T0.3 |
93A/1. | [0] | 029312-0300 | SHIM D27&20T1.0 |
93A/1. | [0] | 029312-0310 | SHIM D24&20T0.10 |
93A/1. | [0] | 029312-0320 | SHIM D24&20T0.12 |
93A/1. | [0] | 029312-0330 | SHIM D24&20T0.14 |
93A/1. | [0] | 029312-0340 | SHIM D24&20T0.16 |
93A/1. | [0] | 029312-0350 | SHIM D24&20T0.18 |
93A/1. | [0] | 029312-0360 | SHIM D24&20T0.3 |
93A/1. | [0] | 029312-0370 | SHIM D24&20T0.5 |
93A/1. | [0] | 029312-0380 | SHIM D24&20T1.0 |
93A/1. | [0] | 139420-0400 | SHIM D27&20T0.7 |
95. | [1] | 131305-0700 | BEARING SHELL |
96. | [2] | 139105-0200 | FLAT-HEAD SCREW |
97. | [2] | 026505-0940 | GASKET |
100A. | [1] | 029622-0190 | PACKING RING |
101A. | [1] | 131316-2000 | COVER |
104A. | [4] | 020006-1440 | BLEEDER SCREW M6P1L14 |
106A. | [1] | 029635-0050 | O-RING |
112A. | [1] | 025804-1610 | WOODRUFF KEY |
117A. | [1] | 139814-0000 | EYE BOLT |
118A. | [2] | 139514-0000 | GASKET D19.2&14.2T1.0 |
131. | [1] | 134424-4120 | OVER FLOW VALVE |
133. | [2] | 139514-0000 | GASKET D19.2&14.2T1.0 |
152. | [1] | 139812-0100 | EYE BOLT |
154. | [2] | 139512-0000 | GASKET D17.2&12.2T1.0 |
334. | [1] | 139810-0000 | EYE BOLT |
336. | [2] | 139510-0000 | GASKET D15.2&10.2T1.0 |
360A. | [1] | 131496-0300 | POINTER |
361A. | [2] | 029010-6680 | BLEEDER SCREW |
Cross reference number
Zexel num
Bosch num
Firm num
Name
101060-6860
FUEL-INJECTION PUMP
Q 14BF FUEL INJECTION PUMP PE6AD PE
Q 14BF FUEL INJECTION PUMP PE6AD PE
Information:
2. Loosen the fuel injection line nut at the fuel pump, one at a time, with the engine running. Use a cloth or similar material to prevent fuel from spraying on hot exhaust component. Be sure to tighten each fuel line nut after the test, before the next fuel line nut is loosened. 3. When a cylinder is found where the loosened fuel line nut does not make a difference in engine performance or smoking, have that cylinder injection nozzle tested. Purge the fuel lines of air. 4. Check for any fuel leaks. Stop the engine by following the procedure in the Engine Stopping topic in this manual and correct any fuel leaks that may occur. To Remove and Install Injection Nozzles
Special tooling is required. Refer to the Service Manual for your engine to remove and install injection nozzles or contact your Caterpillar dealer for assistance.Starting Motor and Alternator
Inspect for Proper Operation
Electric Starting Motor
AlternatorFor good life of the air starting motor, the air supply should be free of dirt and water. A lubricator should be used with the starting system. Use 10 weight non-detergent engine oil above 0°C (32°F) or diesel fuel at temperatures below 0°C (32°F). See the Lubricant Specifications for the proper oil to use.One unscheduled failure caused by any of these components will cost more in downtime than maintaining them before failure. The cost incurred to maintain these components before failure as recommended could be significantly less than if the component fails. By maintaining these components before failure, unscheduled downtime and potential damage to other engine parts are reduced. The prevention of unscheduled downtime saves money and lowers operating costs.Caterpillar recommends that the most cost effective method of operation and maintenance for these components is to inspect the unit before it fails and make the decision to rebuild or exchange the components.Before deciding which repair method is best, make sure all of the options and costs associated with repair have been considered. Some considerations are:* The costs associated with using separate parts from inventory versus the cost of a repair kit.* Downtime costs while the product is being rebuilt or repaired.* Total parts and labor costs for repairs versus the actual Remanufactured cost.* Remanufactured components from Caterpillar (if available) are covered by a standard, factory warranty.Caterpillar Recommendation
To minimize downtime, Caterpillar recommends that the use of Remanufactured components (subject to availability) is the most cost effective option.Removal and Installation
Refer to the established procedure in the Service Manual for this engine to Remove and Install these components or contact your Caterpillar dealer for assistance.Turbochargers
Rebuild or Exchange
The cost incurred to maintain your turbochargers before failure as recommended could be significantly less than if you wait until your turbocharger fails. By maintaining your turbochargers before failure, you will minimize unscheduled downtime and reduce the chances for potential damage to other engine parts. If you choose to operate your engine until the turbochargers fail, your repair costs could be as much as twenty-five times or more compared
Special tooling is required. Refer to the Service Manual for your engine to remove and install injection nozzles or contact your Caterpillar dealer for assistance.Starting Motor and Alternator
Inspect for Proper Operation
Electric Starting Motor
AlternatorFor good life of the air starting motor, the air supply should be free of dirt and water. A lubricator should be used with the starting system. Use 10 weight non-detergent engine oil above 0°C (32°F) or diesel fuel at temperatures below 0°C (32°F). See the Lubricant Specifications for the proper oil to use.One unscheduled failure caused by any of these components will cost more in downtime than maintaining them before failure. The cost incurred to maintain these components before failure as recommended could be significantly less than if the component fails. By maintaining these components before failure, unscheduled downtime and potential damage to other engine parts are reduced. The prevention of unscheduled downtime saves money and lowers operating costs.Caterpillar recommends that the most cost effective method of operation and maintenance for these components is to inspect the unit before it fails and make the decision to rebuild or exchange the components.Before deciding which repair method is best, make sure all of the options and costs associated with repair have been considered. Some considerations are:* The costs associated with using separate parts from inventory versus the cost of a repair kit.* Downtime costs while the product is being rebuilt or repaired.* Total parts and labor costs for repairs versus the actual Remanufactured cost.* Remanufactured components from Caterpillar (if available) are covered by a standard, factory warranty.Caterpillar Recommendation
To minimize downtime, Caterpillar recommends that the use of Remanufactured components (subject to availability) is the most cost effective option.Removal and Installation
Refer to the established procedure in the Service Manual for this engine to Remove and Install these components or contact your Caterpillar dealer for assistance.Turbochargers
Rebuild or Exchange
The cost incurred to maintain your turbochargers before failure as recommended could be significantly less than if you wait until your turbocharger fails. By maintaining your turbochargers before failure, you will minimize unscheduled downtime and reduce the chances for potential damage to other engine parts. If you choose to operate your engine until the turbochargers fail, your repair costs could be as much as twenty-five times or more compared