Information fuel-injection pump
BOSCH
9 410 610 616
9410610616
ZEXEL
101060-5340
1010605340
NISSAN-DIESEL
16703Z5865
16703z5865
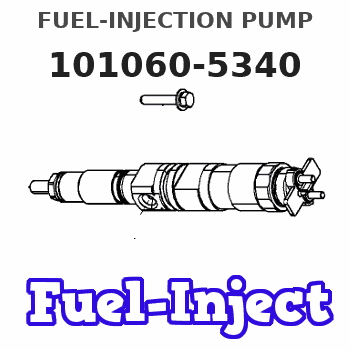
Rating:
Scheme ###:
1. | [1] | 131077-0320 | PUMP HOUSING |
1/14. | [1] | 131002-2000 | ADAPTOR |
1/22. | [1] | 139916-0100 | CAPSULE |
1/30. | [3] | 029040-6020 | STUD |
1/35. | [1] | 134026-0000 | CAPSULE |
1/40. | [1] | 131002-4700 | ADAPTOR |
1/40A. | [1] | 131002-6700 | ADAPTOR |
1/50A. | [1] | 131311-0100 | SPACER RING |
2. | [1] | 131028-6020 | COVER |
2/2. | [1] | 131011-0800 | GASKET |
3. | [2] | 131017-1000 | FLAT-HEAD SCREW |
5. | [2] | 029340-6020 | GASKET D10&6.5T1.00 |
16. | [6] | 131034-1501 | CAPSULE |
21. | [3] | 139206-0400 | UNION NUT |
23. | [1] | 029633-1010 | O-RING |
30. | [6] | 131153-5320 | PLUNGER-AND-BARREL ASSY |
36. | [6] | 131160-0620 | DELIVERY-VALVE ASSEMBLY |
37. | [6] | 131112-5400 | COMPRESSION SPRING |
40. | [6] | 131115-1200 | GASKET D16&8T0.5 |
41. | [6] | 131116-8300 | FITTING |
42. | [6] | 131117-4600 | FILLER PIECE |
45. | [3] | 131122-0520 | PLATE |
49. | [6] | 029632-0070 | O-RING &20W2 |
55. | [6] | 131200-2720 | TAPPET |
55/2. | [1] | 131203-0500 | BEARING PIN |
55/3. | [1] | 131204-1100 | ROLLER |
55/4. | [1] | 131205-0600 | BUSHING |
55/5. | [1] | 131206-0700 | SLIDER |
56/1. | [0] | 029311-0020 | SHIM D19&10T0.30 |
56/1. | [0] | 029311-0030 | SHIM D19&10T0.40 |
56/1. | [0] | 029311-0040 | SHIM D19&10T0.50 |
56/1. | [0] | 029311-0050 | SHIM D19&10T0.6 |
56/1. | [0] | 029311-0060 | SHIM D19&10T0.7 |
56/1. | [0] | 029311-0070 | SHIM D19&10T0.8 |
56/1. | [0] | 029311-0080 | SHIM D19&10T0.9 |
56/1. | [0] | 029311-0090 | SHIM D19&10T1 |
56/1. | [0] | 029311-0110 | SHIM D19&10T1.1 |
56/1. | [0] | 029311-0120 | SHIM D19&10T1.2 |
56/1. | [0] | 029311-0130 | SHIM D19&10T1.3 |
56/1. | [0] | 029311-0140 | SHIM D19&10T1.4 |
56/1. | [0] | 029311-0270 | SHIM D19&10T0.55 |
56/1. | [0] | 029311-0280 | SHIM D19&10T0.65 |
56/1. | [0] | 029311-0290 | SHIM D19&10T0.75 |
56/1. | [0] | 029311-0310 | SHIM D19&10T0.85 |
56/1. | [0] | 029311-0320 | SHIM D19&10T0.95 |
56/1. | [0] | 029311-0330 | SHIM D19&10T1.05 |
56/1. | [0] | 029311-0340 | SHIM D19&10T1.15 |
56/1. | [0] | 029311-0350 | SHIM D19&10T1.25 |
56/1. | [0] | 029311-0490 | SHIM D19&10T1.5 |
56/1. | [0] | 029311-0500 | SHIM D19&10T1.6 |
56/1. | [0] | 029311-0580 | SHIM D19&10T0.2 |
56/1. | [0] | 029311-0590 | SHIM D19&10T0.25 |
56/1. | [0] | 029311-0600 | SHIM D19&10T0.35 |
56/1. | [0] | 029311-0610 | SHIM D19&10T0.45 |
56/1. | [0] | 029311-0620 | SHIM D19&10T1.35 |
56/1. | [0] | 029311-0630 | SHIM D19&10T1.45 |
56/1. | [0] | 029311-0710 | SHIM D19&10T1.55 |
61. | [6] | 131215-2100 | COMPRESSION SPRING |
62. | [6] | 131216-0400 | SLOTTED WASHER |
63. | [6] | 131217-0600 | SLOTTED WASHER |
67. | [1] | 131256-0000 | CONTROL RACK |
68. | [1] | 131226-0300 | FLAT-HEAD SCREW |
76. | [6] | 131240-0100 | PINION |
77. | [6] | 131241-0500 | CONTROL SLEEVE |
78. | [6] | 131242-0100 | FLAT-HEAD SCREW |
90. | [1] | 131375-1800 | CAMSHAFT |
91A. | [1] | 016630-2030 | BEARING PLATE |
91B. | [1] | 028201-7020 | BEARING PLATE |
91E. | [1] | 016640-2030 | BEARING PLATE |
91F. | [1] | 028202-0020 | BEARING PLATE |
92. | [1] | 131302-1000 | SPACER RING |
92A. | [1] | 131302-0400 | SPACER RING |
93/1. | [0] | 029312-0220 | SHIM D27&20T0.1 |
93/1. | [0] | 029312-0230 | SHIM D27&20T0.12 |
93/1. | [0] | 029312-0240 | SHIM D27&20T0.14 |
93/1. | [0] | 029312-0250 | SHIM D27&20T0.16 |
93/1. | [0] | 029312-0260 | SHIM D27&20T0.18 |
93/1. | [0] | 029312-0270 | SHIM D27&20T0.5 |
93/1. | [0] | 029312-0290 | SHIM D27&20T0.3 |
93/1. | [0] | 029312-0300 | SHIM D27&20T1.0 |
93/1. | [0] | 139420-0400 | SHIM D27&20T0.7 |
93A/1. | [0] | 029311-7010 | SHIM D22&17T0.1 |
93A/1. | [0] | 029311-7020 | SHIM D22&17T0.12 |
93A/1. | [0] | 029311-7030 | SHIM D22&17T0.14 |
93A/1. | [0] | 029311-7040 | SHIM D22&17T0.16 |
93A/1. | [0] | 029311-7050 | SHIM D22&17T0.18 |
93A/1. | [0] | 029311-7060 | SHIM D22&17T0.5 |
93A/1. | [0] | 029311-7070 | SHIM D22&17T1.0 |
93A/1. | [0] | 029311-7090 | SHIM D22&17T0.3 |
93A/1. | [0] | 029311-7210 | SHIM D22&17T0.7 |
93A/1. | [0] | 029311-7220 | SHIM D22&17T1.4 |
93A/1. | [0] | 139417-0000 | SHIM D22&17T2.4 |
95. | [1] | 131305-0600 | BEARING SHELL |
96. | [2] | 139105-0200 | FLAT-HEAD SCREW |
97. | [2] | 026505-0940 | GASKET |
100. | [1] | 029622-0190 | PACKING RING |
101. | [1] | 131316-2000 | COVER |
104. | [4] | 020006-1440 | BLEEDER SCREW M6P1L14 |
106. | [1] | 029635-0050 | O-RING |
112. | [1] | 029470-4030 | WOODRUFF KEY |
131. | [1] | 029731-4680 | EYE BOLT |
131A. | [1] | 134424-1520 | OVER FLOW VALVE |
152. | [1] | 029731-4680 | EYE BOLT |
334. | [1] | 029731-0120 | EYE BOLT |
360. | [1] | 131496-0700 | POINTER |
361. | [2] | 029010-6700 | BLEEDER SCREW |
363/1. | [0] | 139400-0500 | SHIM T0.20 |
363/1. | [0] | 139400-0600 | SHIM T0.30 |
363/1. | [0] | 139400-0700 | SHIM T0.50 |
363/1. | [0] | 139400-0800 | SHIM T1.00 |
Cross reference number
Zexel num
Bosch num
Firm num
Name
Information:
You must read and understand the warnings and instructions contained in the Safety section of this manual before performing any operation or maintenance procedures.Before proceeding with this maintenance, perform all previous maintenance interval requirements.Cooling System (Extended Life Coolant Only)
Do not perform this maintenance until you read and understand the material in the Safety and Cooling System Specifications sections of this publication.
Drain/Flush/Replace Coolant
Caterpillar Extended Life Coolant should be replaced every 6,000 Service Hours or 4 Years, whichever comes first. Only clean water is needed to clean and flush the cooling system when ELC is drained and replaced.Drain
1. Stop the engine and allow the engine to cool. Loosen the coolant filler cap slowly to relieve any pressure, and remove the cap.2. Remove the cooling system drain plug(s) or open the drain valve. Remove the drain plug from the bottom of the water pump housing (if equipped) and/or radiator. Allow the coolant to drain.
Dispose of used engine coolant properly or recycle. Various methods have been proposed to reclaim used coolant for reuse in engine cooling systems. The full distillation procedure is the only method acceptable by Caterpillar to reclaim the used coolant. Contact your Caterpillar dealer for information regarding disposal and recycling of used coolant.
Contact Caterpillar Service Technology Group:Outside Illinois: 1-800-542-TOOLInside Illinois: 1-800-541-TOOLCanada: 1-800-523-TOOLFlush
4. Flush the cooling system with clean water to remove any debris.5. Clean and install all drain plugs and/or close the drain valve(s).6. Fill the cooling system with clean water. Install the filler cap. Operate the engine until warm 49 to 66°C (150 to 120°F).7. Stop the engine and allow the engine to cool. Loosen the coolant filler cap slowly to relieve any pressure, and remove the cap. Remove the cooling system drain plug(s) or open the drain valve. Allow the water to drain. Flush the cooling system with clean water.8. Repeat steps 6 and 7.Fill
9. Fill the cooling system with ELC. Refer to the refill capacities chart in this manual for the amount of ELC needed to refill your system.10. Start and run the engine with the filler cap removed. Allow the ELC to warm, the thermostat to open, and the coolant level to stabilize. Add ELC if necessary to bring the coolant to the proper level.11. Check the condition of the filler cap gasket. If the gasket is damaged, discard the old filler cap and install a new filler cap. If the gasket is not damaged, use a 9S8140 Service Tool (available from your Caterpillar dealer) to pressure test the filler cap. The correct filler cap pressure is stamped on the face of the filler cap. If the filler cap does not hold the correct pressure, install a new filler cap.12. Start the engine and inspect for coolant leaks and proper operating temperature. Stop the engine.
Do not perform this maintenance until you read and understand the material in the Safety and Cooling System Specifications sections of this publication.
Drain/Flush/Replace Coolant
Caterpillar Extended Life Coolant should be replaced every 6,000 Service Hours or 4 Years, whichever comes first. Only clean water is needed to clean and flush the cooling system when ELC is drained and replaced.Drain
1. Stop the engine and allow the engine to cool. Loosen the coolant filler cap slowly to relieve any pressure, and remove the cap.2. Remove the cooling system drain plug(s) or open the drain valve. Remove the drain plug from the bottom of the water pump housing (if equipped) and/or radiator. Allow the coolant to drain.
Dispose of used engine coolant properly or recycle. Various methods have been proposed to reclaim used coolant for reuse in engine cooling systems. The full distillation procedure is the only method acceptable by Caterpillar to reclaim the used coolant. Contact your Caterpillar dealer for information regarding disposal and recycling of used coolant.
Contact Caterpillar Service Technology Group:Outside Illinois: 1-800-542-TOOLInside Illinois: 1-800-541-TOOLCanada: 1-800-523-TOOLFlush
4. Flush the cooling system with clean water to remove any debris.5. Clean and install all drain plugs and/or close the drain valve(s).6. Fill the cooling system with clean water. Install the filler cap. Operate the engine until warm 49 to 66°C (150 to 120°F).7. Stop the engine and allow the engine to cool. Loosen the coolant filler cap slowly to relieve any pressure, and remove the cap. Remove the cooling system drain plug(s) or open the drain valve. Allow the water to drain. Flush the cooling system with clean water.8. Repeat steps 6 and 7.Fill
9. Fill the cooling system with ELC. Refer to the refill capacities chart in this manual for the amount of ELC needed to refill your system.10. Start and run the engine with the filler cap removed. Allow the ELC to warm, the thermostat to open, and the coolant level to stabilize. Add ELC if necessary to bring the coolant to the proper level.11. Check the condition of the filler cap gasket. If the gasket is damaged, discard the old filler cap and install a new filler cap. If the gasket is not damaged, use a 9S8140 Service Tool (available from your Caterpillar dealer) to pressure test the filler cap. The correct filler cap pressure is stamped on the face of the filler cap. If the filler cap does not hold the correct pressure, install a new filler cap.12. Start the engine and inspect for coolant leaks and proper operating temperature. Stop the engine.