Information fuel-injection pump
BOSCH
9 410 611 951
9410611951
ZEXEL
101060-5230
1010605230
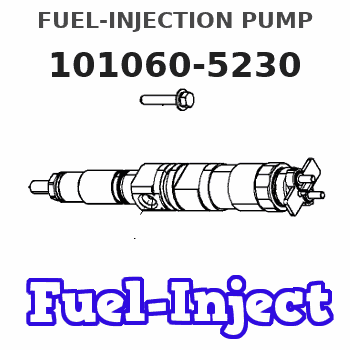
Rating:
Scheme ###:
1. | [1] | 131077-0120 | PUMP HOUSING |
1/22. | [1] | 139916-0100 | CAPSULE |
1/30. | [3] | 029040-6020 | STUD |
1/35. | [1] | 134026-0000 | CAPSULE |
1/40. | [1] | 131002-4700 | ADAPTOR |
1/40A. | [1] | 131002-4800 | ADAPTOR |
1/50A. | [1] | 131311-0100 | SPACER RING |
2. | [1] | 131028-6020 | COVER |
2/2. | [1] | 131011-0800 | GASKET |
3. | [2] | 131017-1000 | FLAT-HEAD SCREW |
5. | [2] | 029340-6020 | GASKET D10&6.5T1.00 |
16. | [6] | 131034-1501 | CAPSULE |
21. | [3] | 139206-0400 | UNION NUT |
23. | [1] | 029633-1010 | O-RING |
30. | [6] | 131153-5720 | PLUNGER-AND-BARREL ASSY |
36. | [6] | 131160-5620 | DELIVERY-VALVE ASSEMBLY |
37. | [6] | 131112-5200 | COILED SPRING |
40. | [6] | 131115-0800 | GASKET |
41. | [6] | 131116-9420 | FITTING |
42. | [6] | 131117-4300 | FILLER PIECE |
45. | [3] | 131122-0320 | PLATE |
49. | [6] | 029632-0070 | O-RING &20W2 |
55. | [6] | 131200-2720 | TAPPET |
55/2. | [1] | 131203-0500 | BEARING PIN |
55/3. | [1] | 131204-1100 | ROLLER |
55/4. | [1] | 131205-0600 | BUSHING |
55/5. | [1] | 131206-0700 | SLIDER |
56/1. | [0] | 029311-0020 | SHIM D19&10T0.30 |
56/1. | [0] | 029311-0030 | SHIM D19&10T0.40 |
56/1. | [0] | 029311-0040 | SHIM D19&10T0.50 |
56/1. | [0] | 029311-0050 | SHIM D19&10T0.6 |
56/1. | [0] | 029311-0060 | SHIM D19&10T0.7 |
56/1. | [0] | 029311-0070 | SHIM D19&10T0.8 |
56/1. | [0] | 029311-0080 | SHIM D19&10T0.9 |
56/1. | [0] | 029311-0090 | SHIM D19&10T1 |
56/1. | [0] | 029311-0110 | SHIM D19&10T1.1 |
56/1. | [0] | 029311-0120 | SHIM D19&10T1.2 |
56/1. | [0] | 029311-0130 | SHIM D19&10T1.3 |
56/1. | [0] | 029311-0140 | SHIM D19&10T1.4 |
56/1. | [0] | 029311-0270 | SHIM D19&10T0.55 |
56/1. | [0] | 029311-0280 | SHIM D19&10T0.65 |
56/1. | [0] | 029311-0290 | SHIM D19&10T0.75 |
56/1. | [0] | 029311-0310 | SHIM D19&10T0.85 |
56/1. | [0] | 029311-0320 | SHIM D19&10T0.95 |
56/1. | [0] | 029311-0330 | SHIM D19&10T1.05 |
56/1. | [0] | 029311-0340 | SHIM D19&10T1.15 |
56/1. | [0] | 029311-0350 | SHIM D19&10T1.25 |
56/1. | [0] | 029311-0490 | SHIM D19&10T1.5 |
56/1. | [0] | 029311-0500 | SHIM D19&10T1.6 |
56/1. | [0] | 029311-0580 | SHIM D19&10T0.2 |
56/1. | [0] | 029311-0590 | SHIM D19&10T0.25 |
56/1. | [0] | 029311-0600 | SHIM D19&10T0.35 |
56/1. | [0] | 029311-0610 | SHIM D19&10T0.45 |
56/1. | [0] | 029311-0620 | SHIM D19&10T1.35 |
56/1. | [0] | 029311-0630 | SHIM D19&10T1.45 |
56/1. | [0] | 029311-0710 | SHIM D19&10T1.55 |
61. | [6] | 131215-2100 | COMPRESSION SPRING |
62. | [6] | 131216-0400 | SLOTTED WASHER |
63. | [6] | 131217-0600 | SLOTTED WASHER |
67. | [1] | 131256-0000 | CONTROL RACK |
68. | [1] | 131226-0300 | FLAT-HEAD SCREW |
76. | [6] | 131240-0100 | PINION |
77. | [6] | 131241-0500 | CONTROL SLEEVE |
78. | [6] | 131242-0100 | FLAT-HEAD SCREW |
90. | [1] | 131375-2000 | CAMSHAFT |
91A. | [1] | 016630-2030 | BEARING PLATE |
91B. | [1] | 028201-7020 | BEARING PLATE |
91E. | [1] | 016640-2030 | BEARING PLATE |
91F. | [1] | 028202-0020 | BEARING PLATE |
92. | [1] | 131302-1000 | SPACER RING |
92A. | [1] | 131302-0400 | SPACER RING |
93/1. | [0] | 029312-0220 | SHIM D27&20T0.1 |
93/1. | [0] | 029312-0230 | SHIM D27&20T0.12 |
93/1. | [0] | 029312-0240 | SHIM D27&20T0.14 |
93/1. | [0] | 029312-0250 | SHIM D27&20T0.16 |
93/1. | [0] | 029312-0260 | SHIM D27&20T0.18 |
93/1. | [0] | 029312-0270 | SHIM D27&20T0.5 |
93/1. | [0] | 029312-0290 | SHIM D27&20T0.3 |
93/1. | [0] | 029312-0300 | SHIM D27&20T1.0 |
93/1. | [0] | 139420-0400 | SHIM D27&20T0.7 |
93A/1. | [0] | 029311-7010 | SHIM D22&17T0.1 |
93A/1. | [0] | 029311-7020 | SHIM D22&17T0.12 |
93A/1. | [0] | 029311-7030 | SHIM D22&17T0.14 |
93A/1. | [0] | 029311-7040 | SHIM D22&17T0.16 |
93A/1. | [0] | 029311-7050 | SHIM D22&17T0.18 |
93A/1. | [0] | 029311-7060 | SHIM D22&17T0.5 |
93A/1. | [0] | 029311-7070 | SHIM D22&17T1.0 |
93A/1. | [0] | 029311-7090 | SHIM D22&17T0.3 |
93A/1. | [0] | 029311-7210 | SHIM D22&17T0.7 |
93A/1. | [0] | 029311-7220 | SHIM D22&17T1.4 |
93A/1. | [0] | 139417-0000 | SHIM D22&17T2.4 |
95. | [3] | 131305-0600 | BEARING SHELL |
96. | [6] | 139105-0200 | FLAT-HEAD SCREW |
97. | [6] | 026505-0940 | GASKET |
100. | [1] | 029622-0190 | PACKING RING |
101. | [1] | 131316-2000 | COVER |
104. | [4] | 020006-1440 | BLEEDER SCREW M6P1L14 |
106. | [1] | 029635-0050 | O-RING |
112. | [1] | 025804-1610 | WOODRUFF KEY |
131. | [1] | 029731-4680 | EYE BOLT |
131A. | [1] | 131424-8320 | OVER FLOW VALVE |
133. | [2] | 139514-0300 | GASKET |
133A. | [2] | 139512-0600 | GASKET |
152. | [1] | 029731-6030 | EYE BOLT |
154. | [2] | 139516-0200 | GASKET |
334. | [1] | 134430-0200 | EYE BOLT |
336. | [2] | 139510-0300 | GASKET |
360. | [1] | 131496-0900 | POINTER |
361. | [2] | 029010-6700 | BLEEDER SCREW |
363/1. | [0] | 139400-0500 | SHIM T0.20 |
363/1. | [0] | 139400-0600 | SHIM T0.30 |
363/1. | [0] | 139400-0700 | SHIM T0.50 |
363/1. | [0] | 139400-0800 | SHIM T1.00 |
Cross reference number
Zexel num
Bosch num
Firm num
Name
Information:
Coolant is essential to control engine operating temperatures and make components last longer. Poorly maintained coolant can actually shorten component life by causing a chain reaction of heat problems. Excessive heat can cause: * Hot spots that crack steel, notably in cylinder heads* Bubble pockets that form on cylinder surfaces and result in liner pitting* Oil to degrade, leading to component damage* Lacquer and shellac build up on precision hydraulic parts* Oil additives to break down and transmission clutches to slipS O S Coolant Analysis is the best way to monitor the condition of your coolant and your cooling system. The two level program, based on samples you submit, shows the condition of coolant and the cooling system.Level I: Basic Coolant Maintenance Check
Checks for correct chemical balance for proper heat and corrosion control. Tests for: * glycol* SCA concentrations* pH* conductivityS O S Coolant Analysis reports results and makes recommendations, usually within 24 hours.The concentration of SCA should be checked regularly for overconcentration or underconcentration. This should be done with test kits, or S O S Coolant Analysis (Level I) at the Every 250 Service Hours interval.Further coolant analysis is recommended at twice a year or after every 1000 service hours.For example, suppose considerable deposits are found in the water jacket areas on the external cooling system, yet coolant additive concentrations were carefully maintained. Chances are that the coolant water had minerals which deposited on the engine over time.One way to verify the water condition, or to be sure of new water at fill time, is to have a coolant analysis conducted. Full water analysis can sometimes be obtained locally by contacting your local water utility company or an agricultural agent. Private laboratories are also available.Caterpillar recommends S O S Level II Coolant Analysis.Level II: Comprehensive Cooling System Analysis
Completely analyzes coolant and coolant effects on the cooling system. Level II Analysis provides: * full Level I analysis* visual properties inspection* metal corrosion and contaminant identification* identification of built up impurities that point to corrosion and scaling problems BEFORE they lead to costly repairs.Level II Analysis provides a simple, clear report of results, and makes recommendations for the lowest cost corrective options.For more information of coolant analysis and how it can help manage your equipment, see your Caterpillar dealer. Consult your Caterpillar dealer for complete information and assistance in establishing an S O S analysis program for your engine(s).
Checks for correct chemical balance for proper heat and corrosion control. Tests for: * glycol* SCA concentrations* pH* conductivityS O S Coolant Analysis reports results and makes recommendations, usually within 24 hours.The concentration of SCA should be checked regularly for overconcentration or underconcentration. This should be done with test kits, or S O S Coolant Analysis (Level I) at the Every 250 Service Hours interval.Further coolant analysis is recommended at twice a year or after every 1000 service hours.For example, suppose considerable deposits are found in the water jacket areas on the external cooling system, yet coolant additive concentrations were carefully maintained. Chances are that the coolant water had minerals which deposited on the engine over time.One way to verify the water condition, or to be sure of new water at fill time, is to have a coolant analysis conducted. Full water analysis can sometimes be obtained locally by contacting your local water utility company or an agricultural agent. Private laboratories are also available.Caterpillar recommends S O S Level II Coolant Analysis.Level II: Comprehensive Cooling System Analysis
Completely analyzes coolant and coolant effects on the cooling system. Level II Analysis provides: * full Level I analysis* visual properties inspection* metal corrosion and contaminant identification* identification of built up impurities that point to corrosion and scaling problems BEFORE they lead to costly repairs.Level II Analysis provides a simple, clear report of results, and makes recommendations for the lowest cost corrective options.For more information of coolant analysis and how it can help manage your equipment, see your Caterpillar dealer. Consult your Caterpillar dealer for complete information and assistance in establishing an S O S analysis program for your engine(s).