Information fuel-injection pump
BOSCH
9 410 611 946
9410611946
ZEXEL
101060-5000
1010605000
HINO
221003410A
221003410a
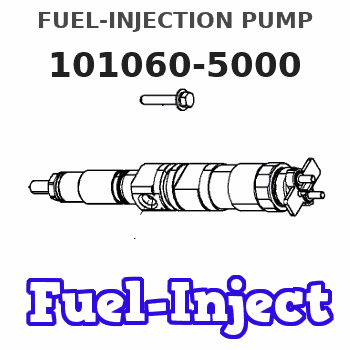
Rating:
Scheme ###:
1. | [1] | 131077-0120 | PUMP HOUSING |
1/22. | [1] | 139916-0100 | CAPSULE |
1/30. | [3] | 029040-6020 | STUD |
1/35. | [1] | 134026-0000 | CAPSULE |
1/40. | [1] | 131002-4700 | ADAPTOR |
1/40A. | [1] | 131002-4800 | ADAPTOR |
1/50A. | [1] | 131311-0100 | SPACER RING |
2. | [1] | 131028-6020 | COVER |
2/2. | [1] | 131011-0800 | GASKET |
3. | [2] | 131017-1000 | FLAT-HEAD SCREW |
5. | [2] | 029340-6020 | GASKET D10&6.5T1.00 |
16. | [6] | 131034-1501 | CAPSULE |
21. | [3] | 139206-0400 | UNION NUT |
23. | [1] | 029633-1010 | O-RING |
30. | [6] | 131153-5720 | PLUNGER-AND-BARREL ASSY |
36. | [6] | 131160-5620 | DELIVERY-VALVE ASSEMBLY |
37. | [6] | 131112-5200 | COILED SPRING |
40. | [6] | 131115-0800 | GASKET |
41. | [6] | 131116-9420 | FITTING |
42. | [6] | 131117-4300 | FILLER PIECE |
45. | [3] | 131122-0320 | PLATE |
49. | [6] | 029632-0070 | O-RING &20W2 |
55. | [6] | 131200-2720 | TAPPET |
55/2. | [1] | 131203-0500 | BEARING PIN |
55/3. | [1] | 131204-1100 | ROLLER |
55/4. | [1] | 131205-0600 | BUSHING |
55/5. | [1] | 131206-0700 | SLIDER |
56/1. | [0] | 029311-0020 | SHIM D19&10T0.30 |
56/1. | [0] | 029311-0030 | SHIM D19&10T0.40 |
56/1. | [0] | 029311-0040 | SHIM D19&10T0.50 |
56/1. | [0] | 029311-0050 | SHIM D19&10T0.6 |
56/1. | [0] | 029311-0060 | SHIM D19&10T0.7 |
56/1. | [0] | 029311-0070 | SHIM D19&10T0.8 |
56/1. | [0] | 029311-0080 | SHIM D19&10T0.9 |
56/1. | [0] | 029311-0090 | SHIM D19&10T1 |
56/1. | [0] | 029311-0110 | SHIM D19&10T1.1 |
56/1. | [0] | 029311-0120 | SHIM D19&10T1.2 |
56/1. | [0] | 029311-0130 | SHIM D19&10T1.3 |
56/1. | [0] | 029311-0140 | SHIM D19&10T1.4 |
56/1. | [0] | 029311-0270 | SHIM D19&10T0.55 |
56/1. | [0] | 029311-0280 | SHIM D19&10T0.65 |
56/1. | [0] | 029311-0290 | SHIM D19&10T0.75 |
56/1. | [0] | 029311-0310 | SHIM D19&10T0.85 |
56/1. | [0] | 029311-0320 | SHIM D19&10T0.95 |
56/1. | [0] | 029311-0330 | SHIM D19&10T1.05 |
56/1. | [0] | 029311-0340 | SHIM D19&10T1.15 |
56/1. | [0] | 029311-0350 | SHIM D19&10T1.25 |
56/1. | [0] | 029311-0490 | SHIM D19&10T1.5 |
56/1. | [0] | 029311-0500 | SHIM D19&10T1.6 |
56/1. | [0] | 029311-0580 | SHIM D19&10T0.2 |
56/1. | [0] | 029311-0590 | SHIM D19&10T0.25 |
56/1. | [0] | 029311-0600 | SHIM D19&10T0.35 |
56/1. | [0] | 029311-0610 | SHIM D19&10T0.45 |
56/1. | [0] | 029311-0620 | SHIM D19&10T1.35 |
56/1. | [0] | 029311-0630 | SHIM D19&10T1.45 |
56/1. | [0] | 029311-0710 | SHIM D19&10T1.55 |
61. | [6] | 131215-2100 | COMPRESSION SPRING |
62. | [6] | 131216-0400 | SLOTTED WASHER |
63. | [6] | 131217-0600 | SLOTTED WASHER |
67. | [1] | 131256-0000 | CONTROL RACK |
68. | [1] | 131226-0300 | FLAT-HEAD SCREW |
76. | [6] | 131240-0100 | PINION |
77. | [6] | 131241-0500 | CONTROL SLEEVE |
78. | [6] | 131242-0100 | FLAT-HEAD SCREW |
90. | [1] | 131375-2000 | CAMSHAFT |
91A. | [1] | 016630-2030 | BEARING PLATE |
91B. | [1] | 028201-7020 | BEARING PLATE |
91E. | [1] | 016640-2030 | BEARING PLATE |
91F. | [1] | 028202-0020 | BEARING PLATE |
92. | [1] | 131302-1000 | SPACER RING |
92A. | [1] | 131302-0400 | SPACER RING |
93/1. | [0] | 029312-0220 | SHIM D27&20T0.1 |
93/1. | [0] | 029312-0230 | SHIM D27&20T0.12 |
93/1. | [0] | 029312-0240 | SHIM D27&20T0.14 |
93/1. | [0] | 029312-0250 | SHIM D27&20T0.16 |
93/1. | [0] | 029312-0260 | SHIM D27&20T0.18 |
93/1. | [0] | 029312-0270 | SHIM D27&20T0.5 |
93/1. | [0] | 029312-0290 | SHIM D27&20T0.3 |
93/1. | [0] | 029312-0300 | SHIM D27&20T1.0 |
93/1. | [0] | 139420-0400 | SHIM D27&20T0.7 |
93A/1. | [0] | 029311-7010 | SHIM D22&17T0.1 |
93A/1. | [0] | 029311-7020 | SHIM D22&17T0.12 |
93A/1. | [0] | 029311-7030 | SHIM D22&17T0.14 |
93A/1. | [0] | 029311-7040 | SHIM D22&17T0.16 |
93A/1. | [0] | 029311-7050 | SHIM D22&17T0.18 |
93A/1. | [0] | 029311-7060 | SHIM D22&17T0.5 |
93A/1. | [0] | 029311-7070 | SHIM D22&17T1.0 |
93A/1. | [0] | 029311-7090 | SHIM D22&17T0.3 |
93A/1. | [0] | 029311-7210 | SHIM D22&17T0.7 |
93A/1. | [0] | 029311-7220 | SHIM D22&17T1.4 |
93A/1. | [0] | 139417-0000 | SHIM D22&17T2.4 |
95. | [3] | 131305-0600 | BEARING SHELL |
96. | [6] | 139105-0200 | FLAT-HEAD SCREW |
97. | [6] | 026505-0940 | GASKET |
100. | [1] | 029622-0190 | PACKING RING |
101. | [1] | 131316-2000 | COVER |
104. | [4] | 020006-1440 | BLEEDER SCREW M6P1L14 |
106. | [1] | 029635-0050 | O-RING |
112. | [1] | 025804-1610 | WOODRUFF KEY |
131. | [1] | 029731-4680 | EYE BOLT |
131A. | [1] | 134424-0920 | OVER FLOW VALVE |
133. | [2] | 139514-0300 | GASKET |
133A. | [2] | 139512-0600 | GASKET |
152. | [1] | 029731-6030 | EYE BOLT |
154. | [2] | 139516-0200 | GASKET |
334. | [1] | 134430-0200 | EYE BOLT |
336. | [2] | 139510-0300 | GASKET |
360. | [1] | 131496-2800 | POINTER |
361. | [2] | 029010-6700 | BLEEDER SCREW |
363/1. | [0] | 139400-0500 | SHIM T0.20 |
363/1. | [0] | 139400-0600 | SHIM T0.30 |
363/1. | [0] | 139400-0700 | SHIM T0.50 |
363/1. | [0] | 139400-0800 | SHIM T1.00 |
Cross reference number
Zexel num
Bosch num
Firm num
Name
101060-5000
9 410 611 946
221003410A HINO
FUEL-INJECTION PUMP
* Q
* Q
Information:
If you operate the engine until the turbocharger fails, you could cause severe damage to the turbocharger's compressor wheel and/or your engine. For example: severe damage to the turbocharger compressor wheel could cause parts from the compressor wheel to enter the engine cylinder and cause additional damage to the piston, valve and cylinder head.Maintenance Options
Repair Kits - These useful kits can be obtained from your Caterpillar dealer. These kits include all the necessary parts and instructions to repair your turbocharger in either your own maintenance shop or at your servicing dealer's facility. Repair kits simplify parts ordering, help speed repairs and reduce parts costs. Remanufactured - This process uses manufacturing techniques and procedures to restore your turbocharger to "like-new" performance capability. This process always involves an end product which conforms to the manufacturer's original functional specification. New - Replace with a new turbocharger.Before deciding which method is best, you should make sure you have considered all of the options and costs associated with repair. Some considerations are: * The costs associated with using separate parts from inventory versus the cost of a repair kit.* Downtime costs while the product is being rebuilt or repaired.* Total parts and labor costs for repairs versus the actual Remanufactured cost.* Remanufactured components from Caterpillar are covered by a national factory warranty.Caterpillar Recommendation
To minimize downtime, Caterpillar recommends the use of a Remanufactured turbocharger.There are two levels of pricing for Remanufactured turbochargers.* The first level is primarily based on damage to the turbocharger before failure.* The second level is primarily based on damage to the turbocharger after failure.If you choose to operate your engine until the turbocharger fails, your repair cost could be as much as ten times the repair before failure cost due to additional turbocharger and engine damage that could have been prevented.Refer to the Service Manual for your engine to remove and install the turbocharger.Valve Lash
Check/Adjust
Be sure the engine cannot be started while this maintenance is being performed. To prevent possible injury, do not use the starting motor to turn the flywheel. Hot engine components can cause burns. Allow additional time for the engine to cool before measuring valve clearance.The PEEC uses high voltage to the unit injectors. Disconnect injector enable circuit connector to prevent personal injury. Do not come in contact with the injector terminals while the engine is running.
Measure the valve lash with the engine stopped. To obtain an accurate measurement, allow at least 20 minutes for the valves to cool to engine cylinder head and block temperature.
Adjust the valve clearance to within 0.08 mm (.003 in) of the valve clearance setting given in the Valve Clearance Setting chart above. Rotate the engine crankshaft 360° in the normal crankshaft rotation direction before any adjustments are made.Bridge Adjustment
The valve bridge should be checked and/or adjusted each time valve clearance is chcked and/or adjusted. Valve and valve mechanism components do not always wear evenly which can allow the bridge to be out of adjustment.It is not necessary to remove the rocker
Repair Kits - These useful kits can be obtained from your Caterpillar dealer. These kits include all the necessary parts and instructions to repair your turbocharger in either your own maintenance shop or at your servicing dealer's facility. Repair kits simplify parts ordering, help speed repairs and reduce parts costs. Remanufactured - This process uses manufacturing techniques and procedures to restore your turbocharger to "like-new" performance capability. This process always involves an end product which conforms to the manufacturer's original functional specification. New - Replace with a new turbocharger.Before deciding which method is best, you should make sure you have considered all of the options and costs associated with repair. Some considerations are: * The costs associated with using separate parts from inventory versus the cost of a repair kit.* Downtime costs while the product is being rebuilt or repaired.* Total parts and labor costs for repairs versus the actual Remanufactured cost.* Remanufactured components from Caterpillar are covered by a national factory warranty.Caterpillar Recommendation
To minimize downtime, Caterpillar recommends the use of a Remanufactured turbocharger.There are two levels of pricing for Remanufactured turbochargers.* The first level is primarily based on damage to the turbocharger before failure.* The second level is primarily based on damage to the turbocharger after failure.If you choose to operate your engine until the turbocharger fails, your repair cost could be as much as ten times the repair before failure cost due to additional turbocharger and engine damage that could have been prevented.Refer to the Service Manual for your engine to remove and install the turbocharger.Valve Lash
Check/Adjust
Be sure the engine cannot be started while this maintenance is being performed. To prevent possible injury, do not use the starting motor to turn the flywheel. Hot engine components can cause burns. Allow additional time for the engine to cool before measuring valve clearance.The PEEC uses high voltage to the unit injectors. Disconnect injector enable circuit connector to prevent personal injury. Do not come in contact with the injector terminals while the engine is running.
Measure the valve lash with the engine stopped. To obtain an accurate measurement, allow at least 20 minutes for the valves to cool to engine cylinder head and block temperature.
Adjust the valve clearance to within 0.08 mm (.003 in) of the valve clearance setting given in the Valve Clearance Setting chart above. Rotate the engine crankshaft 360° in the normal crankshaft rotation direction before any adjustments are made.Bridge Adjustment
The valve bridge should be checked and/or adjusted each time valve clearance is chcked and/or adjusted. Valve and valve mechanism components do not always wear evenly which can allow the bridge to be out of adjustment.It is not necessary to remove the rocker
Have questions with 101060-5000?
Group cross 101060-5000 ZEXEL
Hino
101060-5000
9 410 611 946
221003410A
FUEL-INJECTION PUMP