Information fuel-injection pump
BOSCH
9 410 611 255
9410611255
ZEXEL
101060-4900
1010604900
MITSUBISHI
ME727157
me727157
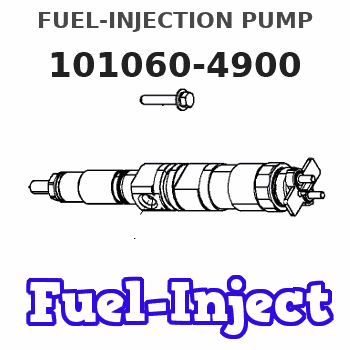
Rating:
Scheme ###:
1. | [1] | 131075-4620 | PUMP HOUSING |
1/22. | [1] | 139916-0100 | CAPSULE |
1/30. | [3] | 029040-6020 | STUD |
1/35A. | [1] | 131400-0100 | ADAPTOR |
1/40. | [1] | 131002-5000 | ADAPTOR |
1/50. | [1] | 131311-0000 | SPACER RING |
2. | [1] | 131028-6020 | COVER |
2/2. | [1] | 131011-0800 | GASKET |
3. | [2] | 131017-1000 | FLAT-HEAD SCREW |
5. | [2] | 029340-6020 | GASKET D10&6.5T1.00 |
16. | [6] | 131034-1501 | CAPSULE |
21. | [3] | 139206-0400 | UNION NUT |
23. | [1] | 029633-1010 | O-RING |
30. | [6] | 131153-0320 | PLUNGER-AND-BARREL ASSY |
36. | [6] | 131110-8820 | DELIVERY-VALVE ASSEMBLY |
37. | [6] | 131112-2600 | COILED SPRING |
40. | [6] | 131115-1200 | GASKET D16&8T0.5 |
41. | [6] | 131116-4900 | FITTING |
42. | [6] | 131117-2100 | FILLER PIECE |
45. | [3] | 131122-0520 | PLATE |
49. | [6] | 029632-0070 | O-RING &20W2 |
55. | [6] | 131200-2720 | TAPPET |
55/2. | [1] | 131203-0500 | BEARING PIN |
55/3. | [1] | 131204-1100 | ROLLER |
55/4. | [1] | 131205-0600 | BUSHING |
55/5. | [1] | 131206-0700 | SLIDER |
56/1. | [0] | 029311-0020 | SHIM D19&10T0.30 |
56/1. | [0] | 029311-0030 | SHIM D19&10T0.40 |
56/1. | [0] | 029311-0040 | SHIM D19&10T0.50 |
56/1. | [0] | 029311-0050 | SHIM D19&10T0.6 |
56/1. | [0] | 029311-0060 | SHIM D19&10T0.7 |
56/1. | [0] | 029311-0070 | SHIM D19&10T0.8 |
56/1. | [0] | 029311-0080 | SHIM D19&10T0.9 |
56/1. | [0] | 029311-0090 | SHIM D19&10T1 |
56/1. | [0] | 029311-0110 | SHIM D19&10T1.1 |
56/1. | [0] | 029311-0120 | SHIM D19&10T1.2 |
56/1. | [0] | 029311-0130 | SHIM D19&10T1.3 |
56/1. | [0] | 029311-0140 | SHIM D19&10T1.4 |
56/1. | [0] | 029311-0270 | SHIM D19&10T0.55 |
56/1. | [0] | 029311-0280 | SHIM D19&10T0.65 |
56/1. | [0] | 029311-0290 | SHIM D19&10T0.75 |
56/1. | [0] | 029311-0310 | SHIM D19&10T0.85 |
56/1. | [0] | 029311-0320 | SHIM D19&10T0.95 |
56/1. | [0] | 029311-0330 | SHIM D19&10T1.05 |
56/1. | [0] | 029311-0340 | SHIM D19&10T1.15 |
56/1. | [0] | 029311-0350 | SHIM D19&10T1.25 |
56/1. | [0] | 029311-0490 | SHIM D19&10T1.5 |
56/1. | [0] | 029311-0500 | SHIM D19&10T1.6 |
56/1. | [0] | 029311-0580 | SHIM D19&10T0.2 |
56/1. | [0] | 029311-0590 | SHIM D19&10T0.25 |
56/1. | [0] | 029311-0600 | SHIM D19&10T0.35 |
56/1. | [0] | 029311-0610 | SHIM D19&10T0.45 |
56/1. | [0] | 029311-0620 | SHIM D19&10T1.35 |
56/1. | [0] | 029311-0630 | SHIM D19&10T1.45 |
56/1. | [0] | 029311-0710 | SHIM D19&10T1.55 |
61. | [6] | 131215-2100 | COMPRESSION SPRING |
62. | [6] | 131216-0400 | SLOTTED WASHER |
63. | [6] | 131217-0600 | SLOTTED WASHER |
67. | [1] | 131256-0000 | CONTROL RACK |
68. | [1] | 131226-0300 | FLAT-HEAD SCREW |
76. | [6] | 131240-0100 | PINION |
77. | [6] | 131241-0500 | CONTROL SLEEVE |
78. | [6] | 131242-0100 | FLAT-HEAD SCREW |
90. | [1] | 131376-0100 | CAMSHAFT |
91A. | [1] | 016640-2030 | BEARING PLATE |
91E. | [1] | 016640-2030 | BEARING PLATE HR30204J(NSK) |
92. | [1] | 131302-1000 | SPACER RING |
92A. | [1] | 131302-1000 | SPACER RING |
93/1. | [0] | 029312-0220 | SHIM D27&20T0.1 |
93/1. | [0] | 029312-0230 | SHIM D27&20T0.12 |
93/1. | [0] | 029312-0240 | SHIM D27&20T0.14 |
93/1. | [0] | 029312-0250 | SHIM D27&20T0.16 |
93/1. | [0] | 029312-0260 | SHIM D27&20T0.18 |
93/1. | [0] | 029312-0270 | SHIM D27&20T0.5 |
93/1. | [0] | 029312-0290 | SHIM D27&20T0.3 |
93/1. | [0] | 029312-0300 | SHIM D27&20T1.0 |
93/1. | [0] | 139420-0400 | SHIM D27&20T0.7 |
93A/1. | [0] | 029312-0220 | SHIM D27&20T0.1 |
93A/1. | [0] | 029312-0230 | SHIM D27&20T0.12 |
93A/1. | [0] | 029312-0240 | SHIM D27&20T0.14 |
93A/1. | [0] | 029312-0250 | SHIM D27&20T0.16 |
93A/1. | [0] | 029312-0260 | SHIM D27&20T0.18 |
93A/1. | [0] | 029312-0270 | SHIM D27&20T0.5 |
93A/1. | [0] | 029312-0290 | SHIM D27&20T0.3 |
93A/1. | [0] | 029312-0300 | SHIM D27&20T1.0 |
93A/1. | [0] | 139420-0400 | SHIM D27&20T0.7 |
95. | [1] | 131305-0700 | BEARING SHELL |
96. | [2] | 139105-0200 | FLAT-HEAD SCREW |
97. | [2] | 026505-0940 | GASKET |
100A. | [1] | 029622-0190 | PACKING RING |
101A. | [1] | 131316-2000 | COVER |
104A. | [4] | 020006-1440 | BLEEDER SCREW M6P1L14 |
106A. | [1] | 029635-0050 | O-RING |
107A. | [1] | 156635-1700 | COUPLING PLATE |
110A. | [1] | 131325-0400 | UNION NUT |
111A. | [1] | 029321-4010 | LOCKING WASHER |
112A. | [1] | 025804-1610 | WOODRUFF KEY |
117A. | [1] | 029731-4570 | EYE BOLT |
118A. | [2] | 029341-4130 | GASKET D20&13.8T2* |
131. | [1] | 131424-4620 | OVER FLOW VALVE |
133. | [2] | 029341-4130 | GASKET D20&13.8T2* |
152. | [1] | 131456-4300 | EYE BOLT |
154. | [2] | 026512-1540 | GASKET D15.4&12.2T1.50 |
334. | [1] | 029731-0180 | EYE BOLT |
336. | [2] | 026510-1340 | GASKET D13.4&10.2T1 |
Cross reference number
Zexel num
Bosch num
Firm num
Name
101060-4900
ME727157 MITSUBISHI
FUEL-INJECTION PUMP
Q 14BF FUEL INJECTION PUMP PE6AD PE
Q 14BF FUEL INJECTION PUMP PE6AD PE
Information:
Fuel System Information
Use only fuel as recommended in this section.
Fill the fuel tank at the end of each day of operation to drive out moist air and to prevent condensation. Do not fill the tank to the top. Fuel expands as it gets warm and may overflow. Do not fill the fuel filters with fuel before installing them. Contaminated fuel will cause accelerated wear to the fuel system parts.
Fuel Tanks
Drain the water and sediment from any fuel storage tank weekly, at the oil change period, and before it is refilled. This will help prevent water and/or sediment from being pumped from the fuel storage tank into the engine fuel tank.Fuel tanks should contain some provision for draining water and sediment from the bottom of the fuel tanks. Some fuel tanks use supply pipes that allow water and sediment to settle below the end of the fuel supply pipe. This water and sediment should be drained at each oil change. Do not use fuel tanks with supply lines that take fuel directly from the bottom of the tank.Fuel Lines
The fuel return line should deposit fuel at the top of the tank opposite the supply connection. This allows the engine to get warm (not hot) fuel from the tank. It also allows air to escape from the return fuel without being pulled back into the engine. If hot fuel must return to the tank, a fuel cooler is required.Avoid sharp angles and use as few fittings and connections as possible. Moisture in the fuel will tend to collect and freeze at low points in the fuel lines. Fuel lines should travel the most direct route to the engine compartment.Do not use galvanized fittings in the fuel lines. Size fuel lines so they do not exceed maximum fuel transfer pump inlet restriction and fuel return line restriction specifications.Fuel Filters
A primary fuel filter and/or water separator is recommended and should be installed between the fuel tank and the engine fuel inlet.After changing the fuel filter(s), always prime the fuel system (if equipped with a priming pump) to remove air bubbles from the system.Fuel Recommendations
Caterpillar Diesel Engines are capable of burning a wide range of distillate fuels. The use of clean, stable blends of distillate fuel which meet the following requirements will provide quality engine service life. The fuels recommended for use in Caterpillar engines are normally No.2-D diesel fuel and No.2 fuel oil, although No. 1 grades are acceptable. The following fuel specifications are some of the worldwide fuels which also meet the requirements. The following fuel characteristics should be considered when procuring fuel for use in Caterpillar diesel engines.Cetane Number
The minimum cetane number required for average starting conditions for the direct injection engine is 40. A higher cetane value may be required for high altitude operation or cold weather starting.Filterability
Clean fuels should have no more than 0.1% of sediment and water. Storage of fuel for extended periods of time can cause fuel oxidation with solids forming, causing filtering problems.Pour Point
The pour
Use only fuel as recommended in this section.
Fill the fuel tank at the end of each day of operation to drive out moist air and to prevent condensation. Do not fill the tank to the top. Fuel expands as it gets warm and may overflow. Do not fill the fuel filters with fuel before installing them. Contaminated fuel will cause accelerated wear to the fuel system parts.
Fuel Tanks
Drain the water and sediment from any fuel storage tank weekly, at the oil change period, and before it is refilled. This will help prevent water and/or sediment from being pumped from the fuel storage tank into the engine fuel tank.Fuel tanks should contain some provision for draining water and sediment from the bottom of the fuel tanks. Some fuel tanks use supply pipes that allow water and sediment to settle below the end of the fuel supply pipe. This water and sediment should be drained at each oil change. Do not use fuel tanks with supply lines that take fuel directly from the bottom of the tank.Fuel Lines
The fuel return line should deposit fuel at the top of the tank opposite the supply connection. This allows the engine to get warm (not hot) fuel from the tank. It also allows air to escape from the return fuel without being pulled back into the engine. If hot fuel must return to the tank, a fuel cooler is required.Avoid sharp angles and use as few fittings and connections as possible. Moisture in the fuel will tend to collect and freeze at low points in the fuel lines. Fuel lines should travel the most direct route to the engine compartment.Do not use galvanized fittings in the fuel lines. Size fuel lines so they do not exceed maximum fuel transfer pump inlet restriction and fuel return line restriction specifications.Fuel Filters
A primary fuel filter and/or water separator is recommended and should be installed between the fuel tank and the engine fuel inlet.After changing the fuel filter(s), always prime the fuel system (if equipped with a priming pump) to remove air bubbles from the system.Fuel Recommendations
Caterpillar Diesel Engines are capable of burning a wide range of distillate fuels. The use of clean, stable blends of distillate fuel which meet the following requirements will provide quality engine service life. The fuels recommended for use in Caterpillar engines are normally No.2-D diesel fuel and No.2 fuel oil, although No. 1 grades are acceptable. The following fuel specifications are some of the worldwide fuels which also meet the requirements. The following fuel characteristics should be considered when procuring fuel for use in Caterpillar diesel engines.Cetane Number
The minimum cetane number required for average starting conditions for the direct injection engine is 40. A higher cetane value may be required for high altitude operation or cold weather starting.Filterability
Clean fuels should have no more than 0.1% of sediment and water. Storage of fuel for extended periods of time can cause fuel oxidation with solids forming, causing filtering problems.Pour Point
The pour