Information fuel-injection pump
BOSCH
9 410 611 944
9410611944
ZEXEL
101060-3730
1010603730
HINO
221003190A
221003190a
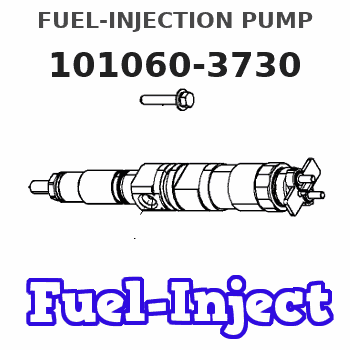
Rating:
Scheme ###:
1. | [1] | 131077-0120 | PUMP HOUSING |
1/30. | [3] | 029040-6020 | STUD |
1/35. | [1] | 134026-0000 | CAPSULE |
1/40. | [1] | 131002-4700 | ADAPTOR |
1/40A. | [1] | 131002-4800 | ADAPTOR |
1/50A. | [1] | 131311-0100 | SPACER RING |
2. | [1] | 131028-6020 | COVER |
2/2. | [1] | 131011-0800 | GASKET |
3. | [2] | 131017-1000 | FLAT-HEAD SCREW |
5. | [2] | 029340-6020 | GASKET D10&6.5T1.00 |
16. | [6] | 131034-1501 | CAPSULE |
21. | [3] | 139206-0400 | UNION NUT |
23. | [1] | 029633-1010 | O-RING |
30. | [6] | 131153-2820 | PLUNGER-AND-BARREL ASSY |
36. | [6] | 131160-4320 | DELIVERY-VALVE ASSEMBLY |
37. | [6] | 131112-4000 | COILED SPRING |
40. | [6] | 131115-1200 | GASKET D16&8T0.5 |
41. | [6] | 131116-8220 | FITTING |
42. | [6] | 131117-3100 | FILLER PIECE |
45. | [3] | 131122-0320 | PLATE |
49. | [6] | 029632-0070 | O-RING &20W2 |
55. | [6] | 131200-2720 | TAPPET |
55/2. | [1] | 131203-0500 | BEARING PIN |
55/3. | [1] | 131204-1100 | ROLLER |
55/4. | [1] | 131205-0600 | BUSHING |
55/5. | [1] | 131206-0700 | SLIDER |
56/1. | [0] | 029311-0020 | SHIM D19&10T0.30 |
56/1. | [0] | 029311-0030 | SHIM D19&10T0.40 |
56/1. | [0] | 029311-0040 | SHIM D19&10T0.50 |
56/1. | [0] | 029311-0050 | SHIM D19&10T0.6 |
56/1. | [0] | 029311-0060 | SHIM D19&10T0.7 |
56/1. | [0] | 029311-0070 | SHIM D19&10T0.8 |
56/1. | [0] | 029311-0080 | SHIM D19&10T0.9 |
56/1. | [0] | 029311-0090 | SHIM D19&10T1 |
56/1. | [0] | 029311-0110 | SHIM D19&10T1.1 |
56/1. | [0] | 029311-0120 | SHIM D19&10T1.2 |
56/1. | [0] | 029311-0130 | SHIM D19&10T1.3 |
56/1. | [0] | 029311-0140 | SHIM D19&10T1.4 |
56/1. | [0] | 029311-0270 | SHIM D19&10T0.55 |
56/1. | [0] | 029311-0280 | SHIM D19&10T0.65 |
56/1. | [0] | 029311-0290 | SHIM D19&10T0.75 |
56/1. | [0] | 029311-0310 | SHIM D19&10T0.85 |
56/1. | [0] | 029311-0320 | SHIM D19&10T0.95 |
56/1. | [0] | 029311-0330 | SHIM D19&10T1.05 |
56/1. | [0] | 029311-0340 | SHIM D19&10T1.15 |
56/1. | [0] | 029311-0350 | SHIM D19&10T1.25 |
56/1. | [0] | 029311-0490 | SHIM D19&10T1.5 |
56/1. | [0] | 029311-0500 | SHIM D19&10T1.6 |
56/1. | [0] | 029311-0580 | SHIM D19&10T0.2 |
56/1. | [0] | 029311-0590 | SHIM D19&10T0.25 |
56/1. | [0] | 029311-0600 | SHIM D19&10T0.35 |
56/1. | [0] | 029311-0610 | SHIM D19&10T0.45 |
56/1. | [0] | 029311-0620 | SHIM D19&10T1.35 |
56/1. | [0] | 029311-0630 | SHIM D19&10T1.45 |
56/1. | [0] | 029311-0710 | SHIM D19&10T1.55 |
61. | [6] | 131215-2100 | COMPRESSION SPRING |
62. | [6] | 131216-0400 | SLOTTED WASHER |
63. | [6] | 131217-0600 | SLOTTED WASHER |
67. | [1] | 131256-0000 | CONTROL RACK |
68. | [1] | 131226-0300 | FLAT-HEAD SCREW |
76. | [6] | 131240-0100 | PINION |
77. | [6] | 131241-0500 | CONTROL SLEEVE |
78. | [6] | 131242-0100 | FLAT-HEAD SCREW |
90. | [1] | 131375-1900 | CAMSHAFT |
91A. | [1] | 016630-2030 | BEARING PLATE |
91B. | [1] | 028201-7020 | BEARING PLATE |
91E. | [1] | 016640-2030 | BEARING PLATE |
91F. | [1] | 028202-0020 | BEARING PLATE |
92. | [1] | 131302-1000 | SPACER RING |
92A. | [1] | 131302-0400 | SPACER RING |
93/1. | [0] | 029312-0220 | SHIM D27&20T0.1 |
93/1. | [0] | 029312-0230 | SHIM D27&20T0.12 |
93/1. | [0] | 029312-0240 | SHIM D27&20T0.14 |
93/1. | [0] | 029312-0250 | SHIM D27&20T0.16 |
93/1. | [0] | 029312-0260 | SHIM D27&20T0.18 |
93/1. | [0] | 029312-0270 | SHIM D27&20T0.5 |
93/1. | [0] | 029312-0290 | SHIM D27&20T0.3 |
93/1. | [0] | 029312-0300 | SHIM D27&20T1.0 |
93/1. | [0] | 139420-0400 | SHIM D27&20T0.7 |
93A/1. | [0] | 029311-7010 | SHIM D22&17T0.1 |
93A/1. | [0] | 029311-7020 | SHIM D22&17T0.12 |
93A/1. | [0] | 029311-7030 | SHIM D22&17T0.14 |
93A/1. | [0] | 029311-7040 | SHIM D22&17T0.16 |
93A/1. | [0] | 029311-7050 | SHIM D22&17T0.18 |
93A/1. | [0] | 029311-7060 | SHIM D22&17T0.5 |
93A/1. | [0] | 029311-7070 | SHIM D22&17T1.0 |
93A/1. | [0] | 029311-7090 | SHIM D22&17T0.3 |
93A/1. | [0] | 029311-7210 | SHIM D22&17T0.7 |
93A/1. | [0] | 029311-7220 | SHIM D22&17T1.4 |
93A/1. | [0] | 139417-0000 | SHIM D22&17T2.4 |
95. | [3] | 131305-0600 | BEARING SHELL |
96. | [6] | 139105-0200 | FLAT-HEAD SCREW |
97. | [6] | 026505-0940 | GASKET |
100. | [1] | 029622-0190 | PACKING RING |
101. | [1] | 131316-2000 | COVER |
104. | [4] | 020006-1440 | BLEEDER SCREW M6P1L14 |
106. | [1] | 029635-0050 | O-RING |
112. | [1] | 025804-1610 | WOODRUFF KEY |
131. | [1] | 029731-4680 | EYE BOLT |
131A. | [1] | 134424-0920 | OVER FLOW VALVE |
133. | [2] | 139514-0300 | GASKET |
133A. | [2] | 139512-0600 | GASKET |
152. | [1] | 029731-6030 | EYE BOLT |
154. | [2] | 139516-0200 | GASKET |
334. | [1] | 134430-0200 | EYE BOLT |
336. | [2] | 139510-0300 | GASKET |
360. | [1] | 131496-0900 | POINTER |
361. | [2] | 029010-6700 | BLEEDER SCREW |
363/1. | [0] | 139400-0500 | SHIM T0.20 |
363/1. | [0] | 139400-0600 | SHIM T0.30 |
363/1. | [0] | 139400-0700 | SHIM T0.50 |
363/1. | [0] | 139400-0800 | SHIM T1.00 |
Cross reference number
Zexel num
Bosch num
Firm num
Name
Information:
Bridge Adjustment
Intake and Exhaust Valve Mechanism
(1) Adjustment locknut, (2) Exhaust bridge, (3) Adjustment locknut, (4) Intake bridgeThe valve bridge should be checked and/or adjusted each time valve clearance is checked and/or adjusted. Valve and valve mechanism components do not always wear evenly which can allow the bridge to be out of adjustment.It is not necessary to remove the rocker arm shaft to adjust the valve bridges, but there must be clearance. Use the procedure that follows to make an adjustment to the bridge. Valves must be fully closed.1. Remove the valve covers from the engine.2. Lubricate the bridge dowel, bridge bore and the top pad of the bridge assembly with engine oil.3. While firmly pressing straight down on the bridge pad with a force of 1 to 10 lb (0.5 to 4.5 kg), turn the adjusting screw clockwise (CW) until contact is made with the valve stem.4. Turn the adjusting screw clockwise (CW) an additional 45° (1/8 turn) to straighten the dowel in the guide and compensate for slack in the threads.5. Hold the adjusting screw in this position and tighten the adjustment locknut to a torque of 18 5 lb ft (25 7 N m).6. Put engine oil at the point where the rocker arms make contact with the bridges.Valve Lash (Clearance) and Unit Injector Preload Adjustment
Valve clearance is measured between the rocker arm and the bridge for the valves.
Measure the valve lash with the engine stopped. To obtain an accurate measurement, allow at least 20 minutes for the valves to cool to engine cylinder head and block temperature.
When the valve lash (clearance) is checked, an adjustment is NOT necessary if the measurement is within the range given in the "Valve Clearance Check" chart shown. If the measurement is outside of the valve clearance check range shown, an adjustment is necessary. See the "Valve Clearance Setting" chart shown and make the setting to the nominal (desired) specifications in this chart. Adjust the valve clearance to within .003 in ( 0.08 mm) of the value given in the chart above.Rotate the engine crankshaft 360° in the normal crankshaft rotation direction before any adjustments are made. Operation of Caterpillar engines with improper valve adjustments will reduce engine efficiency. This reduced efficiency could result in excessive fuel usage and/or shortened engine component life.
Cylinder and Valve LocationTo make an adjustment to the valve clearance, turn the adjustment screw in the rocker arm. Valve clearance adjustments can be made by using the following procedure. The No. 1 piston must be at top center (TC) on the compression stroke. Follow the first three steps to find top center position for piston No. 1.
Locating Top Center for Piston No. 1
(1) Bolts (two - 6V5219), (2) Cover, (3) Flywheel Housing1. Remove two bolts (1) and remove cover (2) from the flywheel housing (3) to open the turning hole.2. Put one of the 6V5219 bolts in the timing hole located approximately 5 to 6 inches (127 to 152 mm) above the turning hole in
Intake and Exhaust Valve Mechanism
(1) Adjustment locknut, (2) Exhaust bridge, (3) Adjustment locknut, (4) Intake bridgeThe valve bridge should be checked and/or adjusted each time valve clearance is checked and/or adjusted. Valve and valve mechanism components do not always wear evenly which can allow the bridge to be out of adjustment.It is not necessary to remove the rocker arm shaft to adjust the valve bridges, but there must be clearance. Use the procedure that follows to make an adjustment to the bridge. Valves must be fully closed.1. Remove the valve covers from the engine.2. Lubricate the bridge dowel, bridge bore and the top pad of the bridge assembly with engine oil.3. While firmly pressing straight down on the bridge pad with a force of 1 to 10 lb (0.5 to 4.5 kg), turn the adjusting screw clockwise (CW) until contact is made with the valve stem.4. Turn the adjusting screw clockwise (CW) an additional 45° (1/8 turn) to straighten the dowel in the guide and compensate for slack in the threads.5. Hold the adjusting screw in this position and tighten the adjustment locknut to a torque of 18 5 lb ft (25 7 N m).6. Put engine oil at the point where the rocker arms make contact with the bridges.Valve Lash (Clearance) and Unit Injector Preload Adjustment
Valve clearance is measured between the rocker arm and the bridge for the valves.
Measure the valve lash with the engine stopped. To obtain an accurate measurement, allow at least 20 minutes for the valves to cool to engine cylinder head and block temperature.
When the valve lash (clearance) is checked, an adjustment is NOT necessary if the measurement is within the range given in the "Valve Clearance Check" chart shown. If the measurement is outside of the valve clearance check range shown, an adjustment is necessary. See the "Valve Clearance Setting" chart shown and make the setting to the nominal (desired) specifications in this chart. Adjust the valve clearance to within .003 in ( 0.08 mm) of the value given in the chart above.Rotate the engine crankshaft 360° in the normal crankshaft rotation direction before any adjustments are made. Operation of Caterpillar engines with improper valve adjustments will reduce engine efficiency. This reduced efficiency could result in excessive fuel usage and/or shortened engine component life.
Cylinder and Valve LocationTo make an adjustment to the valve clearance, turn the adjustment screw in the rocker arm. Valve clearance adjustments can be made by using the following procedure. The No. 1 piston must be at top center (TC) on the compression stroke. Follow the first three steps to find top center position for piston No. 1.
Locating Top Center for Piston No. 1
(1) Bolts (two - 6V5219), (2) Cover, (3) Flywheel Housing1. Remove two bolts (1) and remove cover (2) from the flywheel housing (3) to open the turning hole.2. Put one of the 6V5219 bolts in the timing hole located approximately 5 to 6 inches (127 to 152 mm) above the turning hole in