Information fuel-injection pump
BOSCH
9 410 610 227
9410610227
ZEXEL
101060-3290
1010603290
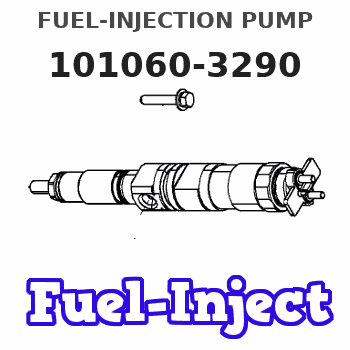
Rating:
Scheme ###:
1. | [1] | 131071-6620 | PUMP HOUSING |
1/30. | [3] | 029040-6220 | STUD |
1/35A. | [1] | 134026-0000 | CAPSULE |
1/40. | [1] | 131423-0900 | ADAPTOR |
1/40A. | [1] | 131423-0900 | ADAPTOR |
2. | [1] | 131028-6020 | COVER |
2/2. | [1] | 131011-0800 | GASKET |
3. | [2] | 131017-1000 | FLAT-HEAD SCREW |
5. | [2] | 029340-6020 | GASKET |
16. | [6] | 131034-1401 | CAPSULE |
20. | [3] | 014110-6440 | LOCKING WASHER D12.2&6.1T1.5 |
21. | [3] | 013030-6040 | UNION NUT |
23. | [1] | 029633-1010 | O-RING |
30. | [6] | 131152-5720 | PLUNGER-AND-BARREL ASSY A191 |
36. | [6] | 131160-2820 | DELIVERY-VALVE ASSEMBLY 11A |
37. | [6] | 131112-4900 | COILED SPRING |
40. | [6] | 131115-1600 | GASKET |
41. | [6] | 131116-7600 | FITTING |
42. | [6] | 131117-2300 | FILLER PIECE |
45. | [3] | 131122-0520 | PLATE |
49. | [6] | 029632-0030 | O-RING |
55. | [6] | 131200-0620 | TAPPET |
55/2. | [6] | 131201-0100 | UNION NUT |
55/3. | [6] | 131202-0100 | HEXAGON SCREW |
55/4. | [6] | 131203-0200 | BEARING PIN |
55/5. | [6] | 131204-1000 | ROLLER |
55/6. | [6] | 131205-0500 | BUSHING |
55/7. | [6] | 131206-0200 | SLIDER |
61. | [6] | 131215-2400 | COMPRESSION SPRING |
62. | [6] | 131216-0100 | SLOTTED WASHER |
63. | [6] | 131217-0100 | SLOTTED WASHER |
67. | [1] | 131256-0000 | CONTROL RACK |
68. | [1] | 131226-0300 | FLAT-HEAD SCREW |
76. | [6] | 131240-0100 | PINION |
77. | [6] | 131241-0100 | CONTROL SLEEVE |
78. | [6] | 131242-0100 | FLAT-HEAD SCREW |
90. | [1] | 131371-0700 | CAMSHAFT |
91A. | [1] | 016640-2030 | BEARING PLATE HR30204J(NSK) |
91B. | [1] | 028202-0020 | BEARING PLATE 4T-30204E1(TOYO) |
91E. | [1] | 016630-2030 | BEARING PLATE HR30203J(NSK) |
91F. | [1] | 028201-7020 | BEARING PLATE 4T-30203E1(TOYO) |
92. | [1] | 131302-0300 | SPACER RING |
92A. | [1] | 131302-1301 | SPACER RING |
93/1. | [0] | 029311-7010 | SHIM D22&17T0.1 |
93/1. | [0] | 029311-7020 | SHIM D22&17T0.12 |
93/1. | [0] | 029311-7030 | SHIM D22&17T0.14 |
93/1. | [0] | 029311-7040 | SHIM D22&17T0.16 |
93/1. | [0] | 029311-7050 | SHIM D22&17T0.18 |
93/1. | [0] | 029311-7060 | SHIM D22&17T0.5 |
93/1. | [0] | 029311-7070 | SHIM D22&17T1.0 |
93/1. | [0] | 029311-7090 | SHIM D22&17T0.3 |
93/1. | [0] | 029311-7210 | SHIM D22&17T0.7 |
93/1. | [0] | 029311-7220 | SHIM D22&17T1.4 |
93/1. | [0] | 139417-0000 | SHIM D22&17T2.4 |
93A/1. | [0] | 029312-0310 | SHIM D24&20T0.10 |
93A/1. | [0] | 029312-0320 | SHIM D24&20T0.12 |
93A/1. | [0] | 029312-0330 | SHIM D24&20T0.14 |
93A/1. | [0] | 029312-0340 | SHIM D24&20T0.16 |
93A/1. | [0] | 029312-0350 | SHIM D24&20T0.18 |
93A/1. | [0] | 029312-0360 | SHIM D24&20T0.3 |
93A/1. | [0] | 029312-0370 | SHIM D24&20T0.5 |
93A/1. | [0] | 029312-0380 | SHIM D24&20T1.0 |
95. | [1] | 131306-0800 | BEARING SHELL |
96. | [2] | 029050-5010 | FLAT-HEAD SCREW |
97. | [2] | 026505-0940 | GASKET |
100A. | [1] | 029622-0190 | PACKING RING |
101A. | [1] | 131316-2000 | COVER |
104A. | [4] | 020006-1440 | BLEEDER SCREW |
106A. | [1] | 029635-0050 | O-RING |
112A. | [1] | 029470-4030 | WOODRUFF KEY |
131. | [1] | 029731-4680 | EYE BOLT |
131A. | [1] | 131424-1520 | OVER FLOW VALVE |
132. | [2] | 026514-1840 | GASKET |
132A. | [2] | 026514-1840 | GASKET |
152. | [1] | 029731-2010 | EYE BOLT |
154. | [2] | 026512-1540 | GASKET |
334. | [1] | 029731-0120 | EYE BOLT |
336. | [2] | 026510-1340 | GASKET |
360A. | [1] | 131496-1000 | POINTER |
361A. | [2] | 029010-6680 | BLEEDER SCREW |
Cross reference number
Zexel num
Bosch num
Firm num
Name
Information:
Adjust - to conform and correspond to specifications. Check - to observe for satisfactory conditions, accuracy, safety or performance. Exchange - to trade a worn or failing component for a remanufactured or rebuilt component. Inspect - to examine closely, in critical appraisal, while testing or evaluating components or systems. Inspect/Rebuild or Exchange - to examine closely; then making the decision on repair option (Rebuild or Exchange). Lubricate - to apply a lubricant (oil, grease, etc.) as specified for reducing friction, heat and wear between solid surfaces. Protective Devices - indicators such as gauges, lights, emergency shutoffs, etc., that alert the pilot that a potential problem may exist. Failure to respond to these indicators in a timely manner could result in serious engine damage. Rebuild - to repair a worn or failing component with new parts, components and/or remanufactured components. Replace - to install something new, remanufactured or rebuilt in place of an existing worn or failing component. Service Hours (Electrical) - records the time (clock hours) the engine is actually running but does not reflect variations in speed, load, etc. The Maintenance Schedules are developed for calendar time, clock hours or fuel consumption. For most users, Service Meter Units and clock hours can be roughly equal. However, Caterpillar recommends that fuel consumption be used as the preferred method of establishing intervals rather than time, SMU's or clock hours.Maintenance Intervals
The Maintenance Schedule requires all previous interval maintenance items to be performed first. For instance, if the Every 250 Hour maintenance is being done, then the Every 50 Hour and Daily maintenance items must be completed BEFORE performing the Every 250 Hour maintenance.Engines may be equipped with various optional components and the charts may recommend maintenance for items not installed on your engine. Simply disregard reference to any extraneous items. If unsure of any item, consult your Caterpillar dealer.Overhaul Interval
The last interval in the chart lists the components inspected, rebuilt, exchanged or replaced at overhaul. OVERHAUL is defined as the interval at which the major wear items in the engine should be replaced. The Overhaul interval represents overhaul of a non-failed engine. In other words, the engine is being rebuilt with certain new parts replacing worn parts such as piston rings, engine rod and main bearings, valves and valve seats., etc.Incidental to the replacement of these relatively few parts is the complete inspection of all other parts that are visible during the overhaul of the engine. The disassembly required to do an overhaul means that disturbed seals and gaskets, etc., will be replaced, and the internal passages of the engine and block be cleaned.* The OVERHAUL interval assumes that regular maintenance recommendations in the rest of the chart have been carefully followed.* Some users may obtain significantly longer or shorter life than the chart recommends between overhauls, but if the recommended intervals are followed, OVERHAULS will occur BEFORE actual FAILURE, and the total COST of operation will be minimized.Although most users will obtain more life between overhauls than
The Maintenance Schedule requires all previous interval maintenance items to be performed first. For instance, if the Every 250 Hour maintenance is being done, then the Every 50 Hour and Daily maintenance items must be completed BEFORE performing the Every 250 Hour maintenance.Engines may be equipped with various optional components and the charts may recommend maintenance for items not installed on your engine. Simply disregard reference to any extraneous items. If unsure of any item, consult your Caterpillar dealer.Overhaul Interval
The last interval in the chart lists the components inspected, rebuilt, exchanged or replaced at overhaul. OVERHAUL is defined as the interval at which the major wear items in the engine should be replaced. The Overhaul interval represents overhaul of a non-failed engine. In other words, the engine is being rebuilt with certain new parts replacing worn parts such as piston rings, engine rod and main bearings, valves and valve seats., etc.Incidental to the replacement of these relatively few parts is the complete inspection of all other parts that are visible during the overhaul of the engine. The disassembly required to do an overhaul means that disturbed seals and gaskets, etc., will be replaced, and the internal passages of the engine and block be cleaned.* The OVERHAUL interval assumes that regular maintenance recommendations in the rest of the chart have been carefully followed.* Some users may obtain significantly longer or shorter life than the chart recommends between overhauls, but if the recommended intervals are followed, OVERHAULS will occur BEFORE actual FAILURE, and the total COST of operation will be minimized.Although most users will obtain more life between overhauls than