Information fuel-injection pump
BOSCH
9 410 612 413
9410612413
ZEXEL
101040-9621
1010409621
HINO
221202261A
221202261a
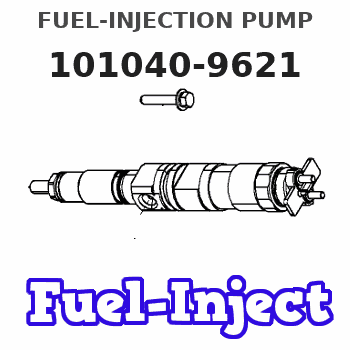
Rating:
Scheme ###:
1. | [1] | 131066-6320 | PUMP HOUSING |
1/30. | [3] | 029040-6020 | STUD |
1/35. | [1] | 134026-0000 | CAPSULE |
1/40. | [1] | 131002-4700 | ADAPTOR |
1/40A. | [1] | 131002-4800 | ADAPTOR |
1/50A. | [1] | 131311-0000 | SPACER RING |
2. | [1] | 131028-6220 | COVER |
2/2. | [1] | 131011-1900 | GASKET |
3. | [2] | 131017-1000 | FLAT-HEAD SCREW |
5. | [2] | 029340-6020 | GASKET |
16. | [4] | 131034-1501 | CAPSULE |
21. | [3] | 139206-0400 | UNION NUT |
23. | [1] | 029633-1010 | O-RING |
30. | [4] | 131153-2920 | PLUNGER-AND-BARREL ASSY A708 |
36. | [4] | 131110-6420 | DELIVERY-VALVE ASSEMBLY A45 |
37. | [4] | 131112-2900 | COILED SPRING |
40. | [4] | 131115-1200 | GASKET |
41. | [4] | 131116-8220 | FITTING |
42. | [4] | 131117-3100 | FILLER PIECE |
45. | [2] | 131122-0520 | PLATE |
49. | [4] | 029632-0070 | O-RING |
55. | [4] | 131200-2720 | TAPPET |
55/2. | [4] | 131203-0500 | BEARING PIN |
55/3. | [4] | 131204-1100 | ROLLER |
55/4. | [4] | 131205-0600 | BUSHING |
55/5. | [4] | 131206-0700 | SLIDER |
56/1. | [0] | 029311-0020 | SHIM D19&10T0.30 |
56/1. | [0] | 029311-0030 | SHIM D19&10T0.40 |
56/1. | [0] | 029311-0040 | SHIM D19&10T0.50 |
56/1. | [0] | 029311-0050 | SHIM D19&10T0.6 |
56/1. | [0] | 029311-0060 | SHIM D19&10T0.7 |
56/1. | [0] | 029311-0070 | SHIM D19&10T0.8 |
56/1. | [0] | 029311-0080 | SHIM D19&10T0.9 |
56/1. | [0] | 029311-0090 | SHIM D19&10T1 |
56/1. | [0] | 029311-0110 | SHIM D19&10T1.1 |
56/1. | [0] | 029311-0120 | SHIM D19&10T1.2 |
56/1. | [0] | 029311-0130 | SHIM D19&10T1.3 |
56/1. | [0] | 029311-0140 | SHIM D19&10T1.4 |
56/1. | [0] | 029311-0270 | SHIM D19&10T0.55 |
56/1. | [0] | 029311-0280 | SHIM D19&10T0.65 |
56/1. | [0] | 029311-0290 | SHIM D19&10T0.75 |
56/1. | [0] | 029311-0310 | SHIM D19&10T0.85 |
56/1. | [0] | 029311-0320 | SHIM D19&10T0.95 |
56/1. | [0] | 029311-0330 | SHIM D19&10T1.05 |
56/1. | [0] | 029311-0340 | SHIM D19&10T1.15 |
56/1. | [0] | 029311-0350 | SHIM D19&10T1.25 |
56/1. | [0] | 029311-0490 | SHIM D19&10T1.5 |
56/1. | [0] | 029311-0500 | SHIM D19&10T1.6 |
56/1. | [0] | 029311-0580 | SHIM D19&10T0.2 |
56/1. | [0] | 029311-0590 | SHIM D19&10T0.25 |
56/1. | [0] | 029311-0600 | SHIM D19&10T0.35 |
56/1. | [0] | 029311-0610 | SHIM D19&10T0.45 |
56/1. | [0] | 029311-0620 | SHIM D19&10T1.35 |
56/1. | [0] | 029311-0630 | SHIM D19&10T1.45 |
56/1. | [0] | 029311-0710 | SHIM D19&10T1.55 |
61. | [4] | 131215-2100 | COMPRESSION SPRING |
62. | [4] | 131216-0400 | SLOTTED WASHER |
63. | [4] | 131217-0600 | SLOTTED WASHER |
67. | [1] | 131254-0000 | CONTROL RACK |
68. | [1] | 131226-0300 | FLAT-HEAD SCREW |
76. | [4] | 131240-0100 | PINION |
77. | [4] | 131241-0500 | CONTROL SLEEVE |
78. | [4] | 131242-0100 | FLAT-HEAD SCREW |
90. | [1] | 131366-0600 | CAMSHAFT |
91A. | [1] | 016640-2030 | BEARING PLATE HR30204J(NSK) |
91B. | [1] | 028202-0020 | BEARING PLATE 4T-30204E1(TOYO) |
91E. | [1] | 016640-2030 | BEARING PLATE HR30204J(NSK) |
91F. | [1] | 028202-0020 | BEARING PLATE 4T-30204E1(TOYO) |
92. | [1] | 131302-1301 | SPACER RING |
92A. | [1] | 131302-1301 | SPACER RING |
93/1. | [0] | 029312-0310 | SHIM D24&20T0.10 |
93/1. | [0] | 029312-0320 | SHIM D24&20T0.12 |
93/1. | [0] | 029312-0330 | SHIM D24&20T0.14 |
93/1. | [0] | 029312-0340 | SHIM D24&20T0.16 |
93/1. | [0] | 029312-0350 | SHIM D24&20T0.18 |
93/1. | [0] | 029312-0360 | SHIM D24&20T0.3 |
93/1. | [0] | 029312-0370 | SHIM D24&20T0.5 |
93/1. | [0] | 029312-0380 | SHIM D24&20T1.0 |
93A/1. | [0] | 029312-0310 | SHIM D24&20T0.10 |
93A/1. | [0] | 029312-0320 | SHIM D24&20T0.12 |
93A/1. | [0] | 029312-0330 | SHIM D24&20T0.14 |
93A/1. | [0] | 029312-0340 | SHIM D24&20T0.16 |
93A/1. | [0] | 029312-0350 | SHIM D24&20T0.18 |
93A/1. | [0] | 029312-0360 | SHIM D24&20T0.3 |
93A/1. | [0] | 029312-0370 | SHIM D24&20T0.5 |
93A/1. | [0] | 029312-0380 | SHIM D24&20T1.0 |
101. | [1] | 131330-1200 | COVER |
104. | [4] | 029010-6810 | BLEEDER SCREW |
106. | [1] | 131321-1600 | GASKET |
112. | [1] | 025804-1310 | WOODRUFF KEY |
131. | [1] | 029731-4680 | EYE BOLT |
131A. | [1] | 131424-6420 | OVER FLOW VALVE |
133. | [2] | 029341-4130 | GASKET |
133A. | [2] | 029341-2140 | GASKET |
191. | [1] | 131459-8722 | BRACKET |
191/1. | [1] | 131459-8702 | BRACKET |
192. | [1] | 029637-5030 | O-RING |
194. | [4] | 014011-0140 | PLAIN WASHER |
195. | [4] | 014111-0440 | LOCKING WASHER |
196. | [4] | 131465-0000 | UNION NUT |
334. | [1] | 134430-0200 | EYE BOLT |
336. | [2] | 139510-0300 | GASKET |
Cross reference number
Zexel num
Bosch num
Firm num
Name
101040-9621
221202261A HINO
FUEL-INJECTION PUMP
Q 14BD FUEL INJECTION PUMP PE4AD PE
Q 14BD FUEL INJECTION PUMP PE4AD PE
Information:
The following topics describe care and maintenance of the electrical system components. These components functioning together produce the energy needed for operating the electrical equipment on the truck and each is dependent upon the other for satisfactory operation. In the event of failure or improper operation, it is essential to check the entire electrical system as a defect in one component can cause damage to another.Many electrical system problems can be traced to loose or corroded connections. Keep connections tight and make sure the wiring insulation is in satisfactory condition. Most of electrical system testing can be performed on the vehicle. (It should be remembered, if a malfunction is found on a vehicle test, the component may need further testing, repair or replacement.) Installations will have electrical components not furnished by Caterpillar. Consult the vehicle manufacturer's manual for maintenance procedures.Check the electrolyte level of each cell and the general condition of the battery. Maintain the electrolyte level to the base of each vent well. The make-up water must be one of the following (in order of preference): 1. Distilled water.2. Odorless, tasteless drinking water.3. Iron free water.4. Any available water.
Never add acid or electrolyte.
CLEANING BATTERY: Mix a weak solution of baking soda and water. Be careful not to get cleaning solution into battery. Apply the solution with a soft bristle brush.
CLEANING BATTERY TERMINALSThoroughly rinse the battery and battery tray with clean water. Apply grease to the battery cable clamps and terminals and to all threads. Testing The Electrolyte Solution: The general condition of a battery can be determined by measuring the specific gravity of the electrolyte solution and adjusting the reading to 80°F (27°C). If the electrolyte level is too low to allow taking a hydrometer reading, add make-up water to the correct level and then charge the battery 2 to 4 hours before taking a reading.
TESTING ELECTROLYTE SOLUTION1. Insert the hydrometer into a cell. Fill the hydrometer barrel while holding it vertically. The float must not drag on the wall of the barrel.2. Read the hydrometer: 1.250 or above - fully charged battery cell1.250-1.225 - full to half charged battery cell1.225-1.150 - half to low charged battery cellBelow 1.150 - dead cell1.000 - water3. Test each cell in the same manner.4. If there is more than .050 (50 gravity points) variation between the highest and lowest reading, the battery may need to be replaced.5. Adjust the readings to 80°F (27°C). a. For every 10F° (5.5C°) the electrolyte temperature is above 80°F (27°C), add .004 (4 gravity points) to the specific gravity readings.b. For every 10F°(5.5C°) the electrolyte temperature is below 80°F (27°C), subtract .004 (4 gravity points) from the specific gravity reading.The corrected reading is of most importance during cold weather when the hydrometer reading is always corrected to a lower specific gravity reading. A low reading signifies the battery has less available power to crank the engine and that booster batteries may be required. Voltage Test (After Load): A load test should be made on a
Never add acid or electrolyte.
CLEANING BATTERY: Mix a weak solution of baking soda and water. Be careful not to get cleaning solution into battery. Apply the solution with a soft bristle brush.
CLEANING BATTERY TERMINALSThoroughly rinse the battery and battery tray with clean water. Apply grease to the battery cable clamps and terminals and to all threads. Testing The Electrolyte Solution: The general condition of a battery can be determined by measuring the specific gravity of the electrolyte solution and adjusting the reading to 80°F (27°C). If the electrolyte level is too low to allow taking a hydrometer reading, add make-up water to the correct level and then charge the battery 2 to 4 hours before taking a reading.
TESTING ELECTROLYTE SOLUTION1. Insert the hydrometer into a cell. Fill the hydrometer barrel while holding it vertically. The float must not drag on the wall of the barrel.2. Read the hydrometer: 1.250 or above - fully charged battery cell1.250-1.225 - full to half charged battery cell1.225-1.150 - half to low charged battery cellBelow 1.150 - dead cell1.000 - water3. Test each cell in the same manner.4. If there is more than .050 (50 gravity points) variation between the highest and lowest reading, the battery may need to be replaced.5. Adjust the readings to 80°F (27°C). a. For every 10F° (5.5C°) the electrolyte temperature is above 80°F (27°C), add .004 (4 gravity points) to the specific gravity readings.b. For every 10F°(5.5C°) the electrolyte temperature is below 80°F (27°C), subtract .004 (4 gravity points) from the specific gravity reading.The corrected reading is of most importance during cold weather when the hydrometer reading is always corrected to a lower specific gravity reading. A low reading signifies the battery has less available power to crank the engine and that booster batteries may be required. Voltage Test (After Load): A load test should be made on a