Information cover, feed pump
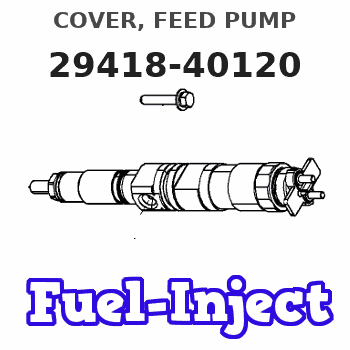
Rating:
Include in #3:
Cross reference number
Part num | Firm num | Firm | Name |
29418-40120 | SM | COVER, FEED PUMP | |
SM | NISSAN MOTOR | COVER, FEED PUMP | |
SM | TOYOTA | COVER, FEED PUMP |
Information:
Defining Contamination
Contamination is defined as the presence of unwanted foreign substances in fluid systems or fluid wetted parts. Contamination alters the properties of fluids, causes damage of fluid systems, and prevents systems and components from attaining the desired reliability and durability. Contamination is the primary cause of fluid system failures.Contaminants include a wide variety of unwanted substances including but not limited to the following:
Foreign and abrasive substances such as wear particles, fibers, dirt, and dust
Chemical substances such as products of combustion that are suspended in the fluids
Cross contamination of water, coolant, oil, and fuel
Biological micro-organisms such as algae or fungi
Physical/chemical contaminants such as products of oxidation and heatSome contaminants are generated within the fluid system due to the normal operation of the system. Contaminants may be drawn into the system from the outside environment or contaminated fill fluids or improper maintenance and repair practices.Particle contaminants are visible to the naked eye if the particles are approximately 40 µm (microns) and larger while smaller particles are not visible. Particle contaminants can cause damage even if the particles are not visible to the naked eye. The critical particle size for wear particles in a modern diesel engine fuel system is 4 µm.Contaminants of all types can be controlled by following contamination control practices and using appropriate filtration. Refer to your Operation and Maintenance Manual and to your local Cat dealer for recommendations.Controlling contamination is especially important for current machine systems. Current machine systems such as hydraulic systems and fuel injection systems are designed with close tolerances and operate at high pressures for enhanced performance. These design improvements emphasize the importance of higher performing fluids, enhanced fluid filtration, and greatly improved fluid cleanliness levels.Measuring Cleanliness
Fluid cleanliness can be measured by taking fluid samples from various machine compartments. Your Cat dealer can analyze the samples. Particle contaminants are typically measured by particle counters. Chemical contaminants can be measured by specific analysis techniques such as oxidation, water, or soot tests. Some chemical contaminants, such as water in fuel, can interfere with the particle counters and can be counted as particles. Refer to your Cat S O S lab or to your Cat dealer for more information.The number of particles in fluids is expressed in "ISO (International Organization for Standardization)" ratings. "ISO 4406" Standard classifies fluid cleanliness by the number and size of particles in 1 milliliter of fluid. "ISO 4406" Standard measures particle size in µm (microns) and reports the resulting count in three code ranges X, Y & Z. The three code range defines the size and distribution of particles in 1 milliliter of fluid:
The first code range, X represents the number of particles equal to or larger than 4 µm per milliliter of fluid.
The second code range, Y represents the number of particles equal to or larger than 6 µm per milliliter of fluid.
The third code range, Z represents the number of particles equal to or larger than 14 µm per milliliter of fluid.An example of an "ISO 4406" particle count
Contamination is defined as the presence of unwanted foreign substances in fluid systems or fluid wetted parts. Contamination alters the properties of fluids, causes damage of fluid systems, and prevents systems and components from attaining the desired reliability and durability. Contamination is the primary cause of fluid system failures.Contaminants include a wide variety of unwanted substances including but not limited to the following:
Foreign and abrasive substances such as wear particles, fibers, dirt, and dust
Chemical substances such as products of combustion that are suspended in the fluids
Cross contamination of water, coolant, oil, and fuel
Biological micro-organisms such as algae or fungi
Physical/chemical contaminants such as products of oxidation and heatSome contaminants are generated within the fluid system due to the normal operation of the system. Contaminants may be drawn into the system from the outside environment or contaminated fill fluids or improper maintenance and repair practices.Particle contaminants are visible to the naked eye if the particles are approximately 40 µm (microns) and larger while smaller particles are not visible. Particle contaminants can cause damage even if the particles are not visible to the naked eye. The critical particle size for wear particles in a modern diesel engine fuel system is 4 µm.Contaminants of all types can be controlled by following contamination control practices and using appropriate filtration. Refer to your Operation and Maintenance Manual and to your local Cat dealer for recommendations.Controlling contamination is especially important for current machine systems. Current machine systems such as hydraulic systems and fuel injection systems are designed with close tolerances and operate at high pressures for enhanced performance. These design improvements emphasize the importance of higher performing fluids, enhanced fluid filtration, and greatly improved fluid cleanliness levels.Measuring Cleanliness
Fluid cleanliness can be measured by taking fluid samples from various machine compartments. Your Cat dealer can analyze the samples. Particle contaminants are typically measured by particle counters. Chemical contaminants can be measured by specific analysis techniques such as oxidation, water, or soot tests. Some chemical contaminants, such as water in fuel, can interfere with the particle counters and can be counted as particles. Refer to your Cat S O S lab or to your Cat dealer for more information.The number of particles in fluids is expressed in "ISO (International Organization for Standardization)" ratings. "ISO 4406" Standard classifies fluid cleanliness by the number and size of particles in 1 milliliter of fluid. "ISO 4406" Standard measures particle size in µm (microns) and reports the resulting count in three code ranges X, Y & Z. The three code range defines the size and distribution of particles in 1 milliliter of fluid:
The first code range, X represents the number of particles equal to or larger than 4 µm per milliliter of fluid.
The second code range, Y represents the number of particles equal to or larger than 6 µm per milliliter of fluid.
The third code range, Z represents the number of particles equal to or larger than 14 µm per milliliter of fluid.An example of an "ISO 4406" particle count