Information pump assy, injecti
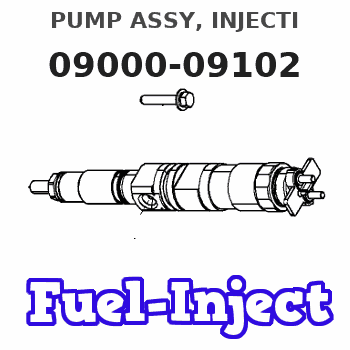
Rating:
Components :
001. | PUMP ASSY, INJECTI | 09000-09102 |
002. | BODY ASSY, INJECTI | 09010-01702 |
003. | COVER, BEARING | 09020-10110 |
004. | TIMER ASSY, AUTOMA | 09180-00431 |
005. | PUMP ASSY, FUEL FE | 09210-01900 |
006. | COUPLING ASSY | 09250-00152 |
Scheme ###:
000. | [01] | 09000-09102 | PUMP ASSY, INJECTI | 22100-1330 |
001. | [01] | 09010-01702 | BODY ASSY, INJECTI | 22110-1440A |
002. | [01] | 09130-00275 | GOVERNOR ASSY, MEC | 22310-2350 |
003. | [01] | 09180-00431 | TIMER ASSY, AUTOMA | 22510-1580A |
004. | [01] | 09210-01900 | PUMP ASSY, FUEL FE | 22570-1330A |
005. | [01] | 09250-00152 | COUPLING ASSY | 22610-1140A |
006. | [02] | 91518-06161 | BOLT, W/WASHER | 22815-1310A |
007. | [02] | 91518-06161 | BOLT, W/WASHER | 22815-1310A |
008. | [04] | 91518-06161 | BOLT, W/WASHER | 22815-1310A |
013. | [01] | 09001-20230 | NUT, TIMER ROUND | 22825-1110A |
014. | [01] | 94901-40070 | WASHER, COUNTERSUN | 22877-1190A |
015. | [01] | 90458-05750 | KEY, WOODRUFF | 22891-1070A |
016. | [01] | 09006-10011 | COVER, PRIMING PUM | 6 053 1552 60 |
017. | [01] | 90801-40280 | O-RING | 22817-1050A |
020. | [01] | 09003-20040 | CAP | 22342-1110A |
021. | [01] | 09002-60050 | SCREW, ADJUSTING | 22396-1140A |
022. | [01] | 94805-30100 | NUT, HEXAGON, W/HO | 22885-3830A |
023. | [02] | 94901-80350 | WASHER, COPPER PLA | 22847-1950A |
024. | [01] | 09001-80152 | COVER, CONTROL RAC | 22372-1100A |
025. | [01] | 94901-80710 | WASHER, COPPER PLA | 22863-1300A |
030. | [01] | 09009-00100 | SWITCH SUB-ASSY, C | 6 051 5627 00 |
031. | [01] | 09009-20031 | BRACKET | 22343-1030A |
032. | [02] | 94904-71360 | BOLT, W/WASHER | 22815-2500A |
033. | [02] | 91518-05121 | BOLT, W/WASHER | 22815-1110A |
034. | [01] | 94935-00460 | CLIP, CORD | 22682-1050 |
035. | [01] | 91510-05081 | BOLT, W/WASHER | 22815-1350A |
Include in #3:
09000-09102
as PUMP ASSY, INJECTI
Cross reference number
Part num | Firm num | Firm | Name |
09000-09102 | 22100-1330 | PUMP ASSY, INJECTI |
Information:
1P3537 BORE GAUGING GROUPWhen reconditioning an engine, the bore size is the determining factor as to the necessity of honing the bores. If bores are worn .006 in. (0.15 mm) more than the standard size, the block should be honed. However, additional service may be obtained without honing if wear does not exceed the maximum wear limit of .0085 in. (0.216 mm)Before honing, inspect the bottom of each cylinder bore adjacent to the main bearing saddle or web. Some of the saddles may overlap the edge of cylinder bores enough to interfere with honing. Where overlap exists, machine a relief in the saddle to provide clearance for the honing tool. The radius of the relief must be concentric with the cylinder bore and .030 .005 in. (0.76 0.13 mm) larger than the bore radius. The relief extends .62 in. (15.7 mm) beyond the bottom of the bore, as shown. This provides adequate clearance for honing.
RELIEF IN SADDLES and CHAMFER AFTER HONINGWhen honing, check bore size at several locations in the length of the bore and around the circumference. Specifically measure at points perpendicular to the crankshaft centerline at locations .25 in. (6.4 mm) from each end and at center of bore. These three specific locations are primary gauge points during and after honing.
PRIMARY GAUGING POINTSWhen honing cylinder blocks, maintain the specific dimensional surface finish and cross hatch tolerances to obtain satisfactory oil control. The tolerances specified are virtually the same as those used for original bore finish at the factory, and can be obtained with an automatic honing machine such as the Sunnen CK-10. This machine has been evaluated and found to give satisfactory results.The Sunnen CK-10 machine is available from Sunnen Products Company, 7910 Manchester Avenue, St. Louis, Missouri, 63143.Due to the cost of suitable honing equipment, it may be more expedient to have the honing done by a shop equipped with a Sunnen CK-10 or equivalent. A list of these shops appears at the back of RECONDITIONING PROCEDURES section of this service manual.Transit Preparation
The following Steps can prevent damage to the block in transit to a shop.1. Completely disassemble, but do not clean block. The residual oil on the surface will prevent rust.2. Enclose the block in an industrial plastic bag and position it with the oil pan surface on a suitable wood pallet or equivalent. Dimension of a suitable wood pallet are shown.
TRANSPORTING PALLET3. Cover the block with 1/2 in. (12.7 mm) thick plywood or equivalent, and band block to the pallet.4. Follow similar instructions when block is returned. To prevent rust, the block should not be cleaned after honing, the film of honing oil provides ample protection from rusting. If blocks are to be stored for any length of time, clean and anti-rust after honing.Cleaning Procedure
After honing is completed, and before assembling the engine, the cylinder block must be cleaned and prepared according to the following instructions.1. If not previously removed, the camshaft bearings must be removed to permit thorough cleaning of