Information bleeder screw
BOSCH
9 442 610 515
9442610515
ZEXEL
020106-2540
0201062540
ISUZU
1157292420
1157292420
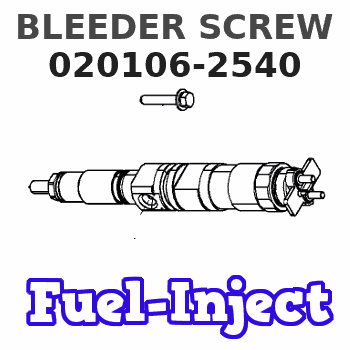
Rating:
Include in #1:
108621-1063
as _
Include in ###:
Number on scheme 236
1047480320
as BLEEDER SCREW
1047491740
as BLEEDER SCREW
M6P1L25
1054010222
as BLEEDER SCREW
1054010241
as BLEEDER SCREW
M6P1L25
1054010282
as BLEEDER SCREW
1054010331
as BLEEDER SCREW
M6P1L25
1054010522
as BLEEDER SCREW
1054010530
as BLEEDER SCREW
M6P1L25
1054010821
as BLEEDER SCREW
1054010831
as BLEEDER SCREW
M6P1L25
1054010962
as BLEEDER SCREW
1054010980
as BLEEDER SCREW
M6P1L25
Cross reference number
Zexel num
Bosch num
Firm num
Name
020106-2540
9 442 610 515
1157292420 ISUZU
BLEEDER SCREW
D 90HY BOLT Standard parts Others
D 90HY BOLT Standard parts Others
020106-2540
9 442 610 515
228114140A HINO
BLEEDER SCREW
D 90HY BOLT Standard parts Others
D 90HY BOLT Standard parts Others
020106-2540
9 442 610 515
ME705322 MITSUBISHI
BLEEDER SCREW
D 90HY BOLT Standard parts Others
D 90HY BOLT Standard parts Others
020106-2540
9 442 610 515
836062514 NISSAN
BLEEDER SCREW
D 90HY BOLT Standard parts Others
D 90HY BOLT Standard parts Others
020106-2540
9 442 610 515
1929189TA0 NISSAN
BLEEDER SCREW
A D 90HY BOLT Standard parts Others
A D 90HY BOLT Standard parts Others
020106-2540
9 442 610 515
1938299105 NISSAN-DIESEL
BLEEDER SCREW
D 90HY BOLT Standard parts Others
D 90HY BOLT Standard parts Others
020106-2540
9 442 610 515
907972625 MAZDA
BLEEDER SCREW
D 90HY BOLT Standard parts Others
D 90HY BOLT Standard parts Others
020106-2540
9 442 610 515
SL0124483 MAZDA
BLEEDER SCREW
A D 90HY BOLT Standard parts Others
A D 90HY BOLT Standard parts Others
Information:
Cleaning the DPF
Because the sections of the DPF are replaceable, a small stock of filter sections can be maintained. Filter sections from a small on-hand stock can be used to replace filters in service at the next scheduled cleaning. The removed filters can be cleaned and returned for installation in the next vehicle. This process of maintaining a stock of filter sections can significantly reduce the amount of down time that will occur.Note: Check State and Local air pollution regulations pertaining to record keeping of serviced filters. Some governmental entities may require filter tracking. Note: Perform a back pressure test prior to cleaning the DPF and record the results. After cleaning the DPF, run the engine at high idle for 5 to 15 minutes to bring the engine and exhaust system to operating temperature. Perform another back pressure test and record the results on the DPF cleaning records form.
Weigh and record the filter unit prior to baking.
By baking the filter under a controlled procedure, the remaining soot on the DPF will burn off and leave a smaller quantity of ash. Failure to observe this procedure can result to damage or cracking to the DPF substrate. A commercial programmable oven is required for this procedure. Careful adherence to this procedure is imperative. Deviation from this procedure may lead to thermal shock and cracking of the DPF substrate or melting at high temperatures.
Place filter into a programmable commercial oven designed for this purpose. Center the filter as much as possible on a rack with 2 inches of spacing below and above for best results.
Program the oven as follows:
Ramp oven temperature to 200° C (392° F)
Hold oven temperature at 200° C (392° F)
Ramp oven temperature to 450° C (842° F)
Hold oven temperature at 450° C (842° F)
Cool down to ambient temperature at natural rate within the oven with the doors closed. Do not use fans.
Place filter in cleaning machine and clean as per machine instructions.
Replace the filter in the oven. Ramp to 650° C (1202° F) in 60 minutes.
Hold oven temperature at 650° C (1202° F) for 240 minutes.
Cool to ambient temperature at a natural rate. Do not use fans.Note: Allow the filter to cool in the oven with the door closed until the filter can be handled with bare hands.Cleaning Procedure
Ash and soot should be removed from the DPF utilizing the Cat 319-2189 Diesel Particulate Filter Cleaner Gp. Using the cleaner without following baking procedure, results in lower efficiency cleaning and will reduce the life of the HEPA filters in the machine. The tool uses pulsed air to flush the ash and soot.Note: Other cleaning methods can release significant quantities of airborne ash and soot. Airborne ash and soot should not be inhaled and may be regulated as a hazardous substance by local regulations.Cleaned Filter Specification
The following steps determine if the DPF was properly cleaned:Note: This specification applies to filters that were cleaned of ash only. This specification is only valid subsequent to the recommend
Because the sections of the DPF are replaceable, a small stock of filter sections can be maintained. Filter sections from a small on-hand stock can be used to replace filters in service at the next scheduled cleaning. The removed filters can be cleaned and returned for installation in the next vehicle. This process of maintaining a stock of filter sections can significantly reduce the amount of down time that will occur.Note: Check State and Local air pollution regulations pertaining to record keeping of serviced filters. Some governmental entities may require filter tracking. Note: Perform a back pressure test prior to cleaning the DPF and record the results. After cleaning the DPF, run the engine at high idle for 5 to 15 minutes to bring the engine and exhaust system to operating temperature. Perform another back pressure test and record the results on the DPF cleaning records form.
Weigh and record the filter unit prior to baking.
By baking the filter under a controlled procedure, the remaining soot on the DPF will burn off and leave a smaller quantity of ash. Failure to observe this procedure can result to damage or cracking to the DPF substrate. A commercial programmable oven is required for this procedure. Careful adherence to this procedure is imperative. Deviation from this procedure may lead to thermal shock and cracking of the DPF substrate or melting at high temperatures.
Place filter into a programmable commercial oven designed for this purpose. Center the filter as much as possible on a rack with 2 inches of spacing below and above for best results.
Program the oven as follows:
Ramp oven temperature to 200° C (392° F)
Hold oven temperature at 200° C (392° F)
Ramp oven temperature to 450° C (842° F)
Hold oven temperature at 450° C (842° F)
Cool down to ambient temperature at natural rate within the oven with the doors closed. Do not use fans.
Place filter in cleaning machine and clean as per machine instructions.
Replace the filter in the oven. Ramp to 650° C (1202° F) in 60 minutes.
Hold oven temperature at 650° C (1202° F) for 240 minutes.
Cool to ambient temperature at a natural rate. Do not use fans.Note: Allow the filter to cool in the oven with the door closed until the filter can be handled with bare hands.Cleaning Procedure
Ash and soot should be removed from the DPF utilizing the Cat 319-2189 Diesel Particulate Filter Cleaner Gp. Using the cleaner without following baking procedure, results in lower efficiency cleaning and will reduce the life of the HEPA filters in the machine. The tool uses pulsed air to flush the ash and soot.Note: Other cleaning methods can release significant quantities of airborne ash and soot. Airborne ash and soot should not be inhaled and may be regulated as a hazardous substance by local regulations.Cleaned Filter Specification
The following steps determine if the DPF was properly cleaned:Note: This specification applies to filters that were cleaned of ash only. This specification is only valid subsequent to the recommend
Have questions with 020106-2540?
Group cross 020106-2540 ZEXEL
Isuzu
020106-2540
9 442 610 515
1157292420
BLEEDER SCREW
Hino
020106-2540
9 442 610 515
228114140A
BLEEDER SCREW
Mitsubishi
020106-2540
9 442 610 515
ME705322
BLEEDER SCREW
Nissan
020106-2540
9 442 610 515
836062514
BLEEDER SCREW
020106-2540
9 442 610 515
1929189TA0
BLEEDER SCREW
Nissan-Diesel
020106-2540
9 442 610 515
1938299105
BLEEDER SCREW
Mazda
020106-2540
9 442 610 515
907972625
BLEEDER SCREW
020106-2540
9 442 610 515
SL0124483
BLEEDER SCREW