Information autom. advance mechanism
BOSCH
9 420 615 328
9420615328
ZEXEL
105672-0520
1056720520
HINO
225003660A
225003660a
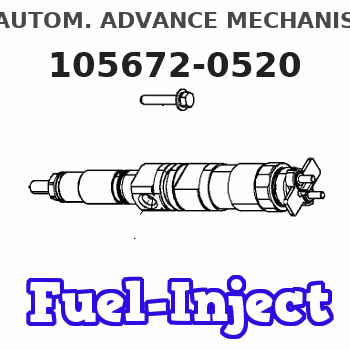
Rating:
Scheme ###:
1. | [1] | 156720-1420 | TIMING-DEVICE HOUSING |
2. | [1] | 156721-2500 | FLANGE BUSHING |
3. | [2] | 156723-0300 | ECCENTRIC DISC |
3. | [2] | 156723-0300 | ECCENTRIC DISC |
4. | [2] | 156723-0400 | ECCENTRIC DISC |
4. | [2] | 156723-0400 | ECCENTRIC DISC |
5. | [1] | 156731-2620 | FLYWEIGHT ASSEMBLY |
5/1. | [2] | 156722-3020 | FLYWEIGHT |
5/1. | [2] | 156722-3020 | FLYWEIGHT |
5/2. | [4] | 156727-1000 | SPRING SEAT |
5/2. | [4] | 156727-1000 | SPRING SEAT |
5/3. | [4] | 156727-1000 | SPRING SEAT |
5/3. | [4] | 156727-1000 | SPRING SEAT |
5/4. | [4] | 156756-8000 | COMPRESSION SPRING |
5/4. | [4] | 156756-8000 | COMPRESSION SPRING |
5/6. | [4] | 156809-0300 | LOCKING WASHER |
5/6. | [4] | 156809-0300 | LOCKING WASHER |
5/7. | [2] | 156726-1000 | PIN |
5/8/1. | [0] | 156728-0800 | SHIM D19&15T0.1 |
5/8/1. | [0] | 156728-0800 | SHIM D19&15T0.1 |
5/8/1. | [0] | 156728-0900 | SHIM D19&15T0.3 |
5/8/1. | [0] | 156728-1000 | SHIM D19&15T0.5 |
5/8/1. | [0] | 156728-1100 | SHIM D19&15T1.0 |
5/8/1. | [0] | 156728-2000 | SHIM D19&15T0.4 |
5/8/1. | [0] | 156728-2100 | SHIM D19&15T0.7 |
5/10. | [4] | 156808-0800 | SPACER BUSHING |
13. | [1] | 156729-1820 | COVER |
13/2. | [1] | 139635-0100 | PACKING RING |
13/3. | [1] | 156117-0100 | O-RING |
30. | [1] | 156729-1400 | LOCKING WASHER |
31. | [1] | 131325-1800 | UNION NUT |
33. | [1] | 029331-0190 | GASKET D14&10.2T1 |
34. | [1] | 156316-0000 | CAPSULE |
35. | [1] | 156729-1500 | CAP |
36. | [1] | 156419-0300 | GASKET |
Include in #1:
101603-2270
as AUTOM. ADVANCE MECHANIS
Cross reference number
Zexel num
Bosch num
Firm num
Name
Information:
Engine Runs Smoothly
Too Much Black Or Gray Exhaust Smoke 1. Poor Quality FuelIf poor or low quality fuel is suspected, use a source of known good quality fuel, and prime and start the engine. If the problem is resolved, drain the complete fuel system, replace the fuel filter, and add fuel recommended by Caterpillar.2. Fuel Injection Timing Out Of CalibrationCheck the fuel injection timing calibration and make necessary adjustments. See the topics, Engine Test Procedure Number P-402, [Checking Electronic Injection Timing With The Timing Adapter Tool Group And The ECAP (Electronic Control Analyzer and Programmer)], and Engine Test Procedure Number P-403, [Calibrating Electronic Injection Timing With The Timing Adapter Tool Group And The ECAP (Electronic Control Analyzer and Programmer)], in Electronic Troubleshooting, 3176 Diesel Truck Engine, Form No. SENR3913.3. Air Inlet Piping Damage Or RestrictionVisually inspect the air inlet system for damage or restriction. If leaks are found, repair or replace parts as required.If the air cleaner has an Air Cleaner Service Indicator, check the indicator for the position of the red piston. If the indicator shows red at any time, install a clean or new air cleaner element.Air inlet restriction can be checked with a water manometer or a vacuum gauge [measuring mm (inches) of water]. Make a connection to the piping between the air cleaner and the inlet to the turbocharger. The maximum restriction allowed, with the engine at full load rpm, is 635 mm (25 in) of water. If a water manometer or vacuum gauge is not available, visually check the air filter for dirt. Clean or replace as required.4. Exhaust System RestrictionVisually inspect the exhaust system for damage or restriction. If leaks are found, repair or replace parts as required.Exhaust system back pressure (pressure differential between the turbocharger exhaust outlet and atmosphere) should not exceed 1016 mm (40 in) of water. An alternative check would be to remove the exhaust piping, load the engine on a chassis dynamometer to determine if the problem is corrected. If this solves the problem, the restriction is in the muffler or truck piping.5. Valve Adjustment Not CorrectCheck and make any necessary adjustments. See the topic, Valve Clearance Setting, in 3176 Diesel Truck Engine Systems Operation And Testing and Adjusting, Form No. SENR3909. Intake valve clearance is 0.38 mm (.015 in), and exhaust valve clearance is 0.64 mm (.025 in).6. Defective Unit InjectorsA defective unit injector can be found, by running the engine at the rpm where the problem exists, with the use of the Electronic Control Analyzer and Programmer (ECAP) service tool Interactive Diagnostics feature (single cylinder cutout) to stop the fuel supply to each cylinder in turn. If a cylinder is found where the cutout makes no difference on the engine performance, that injector should be removed and tested. Drain the fuel supply manifold and remove the injector(s) (see 3176 Diesel Truck Engine Disassembly and Assembly, Form No. SENR3914).Testing of the injectors must be done off of the engine. Use the 1U6661 Pop (Injector) Tester Group with
Too Much Black Or Gray Exhaust Smoke 1. Poor Quality FuelIf poor or low quality fuel is suspected, use a source of known good quality fuel, and prime and start the engine. If the problem is resolved, drain the complete fuel system, replace the fuel filter, and add fuel recommended by Caterpillar.2. Fuel Injection Timing Out Of CalibrationCheck the fuel injection timing calibration and make necessary adjustments. See the topics, Engine Test Procedure Number P-402, [Checking Electronic Injection Timing With The Timing Adapter Tool Group And The ECAP (Electronic Control Analyzer and Programmer)], and Engine Test Procedure Number P-403, [Calibrating Electronic Injection Timing With The Timing Adapter Tool Group And The ECAP (Electronic Control Analyzer and Programmer)], in Electronic Troubleshooting, 3176 Diesel Truck Engine, Form No. SENR3913.3. Air Inlet Piping Damage Or RestrictionVisually inspect the air inlet system for damage or restriction. If leaks are found, repair or replace parts as required.If the air cleaner has an Air Cleaner Service Indicator, check the indicator for the position of the red piston. If the indicator shows red at any time, install a clean or new air cleaner element.Air inlet restriction can be checked with a water manometer or a vacuum gauge [measuring mm (inches) of water]. Make a connection to the piping between the air cleaner and the inlet to the turbocharger. The maximum restriction allowed, with the engine at full load rpm, is 635 mm (25 in) of water. If a water manometer or vacuum gauge is not available, visually check the air filter for dirt. Clean or replace as required.4. Exhaust System RestrictionVisually inspect the exhaust system for damage or restriction. If leaks are found, repair or replace parts as required.Exhaust system back pressure (pressure differential between the turbocharger exhaust outlet and atmosphere) should not exceed 1016 mm (40 in) of water. An alternative check would be to remove the exhaust piping, load the engine on a chassis dynamometer to determine if the problem is corrected. If this solves the problem, the restriction is in the muffler or truck piping.5. Valve Adjustment Not CorrectCheck and make any necessary adjustments. See the topic, Valve Clearance Setting, in 3176 Diesel Truck Engine Systems Operation And Testing and Adjusting, Form No. SENR3909. Intake valve clearance is 0.38 mm (.015 in), and exhaust valve clearance is 0.64 mm (.025 in).6. Defective Unit InjectorsA defective unit injector can be found, by running the engine at the rpm where the problem exists, with the use of the Electronic Control Analyzer and Programmer (ECAP) service tool Interactive Diagnostics feature (single cylinder cutout) to stop the fuel supply to each cylinder in turn. If a cylinder is found where the cutout makes no difference on the engine performance, that injector should be removed and tested. Drain the fuel supply manifold and remove the injector(s) (see 3176 Diesel Truck Engine Disassembly and Assembly, Form No. SENR3914).Testing of the injectors must be done off of the engine. Use the 1U6661 Pop (Injector) Tester Group with